Understanding Cut Off Wheels: Selection, Use, and Maintenance
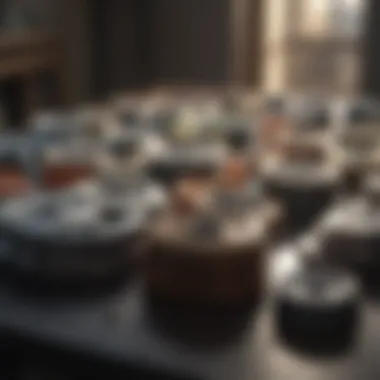
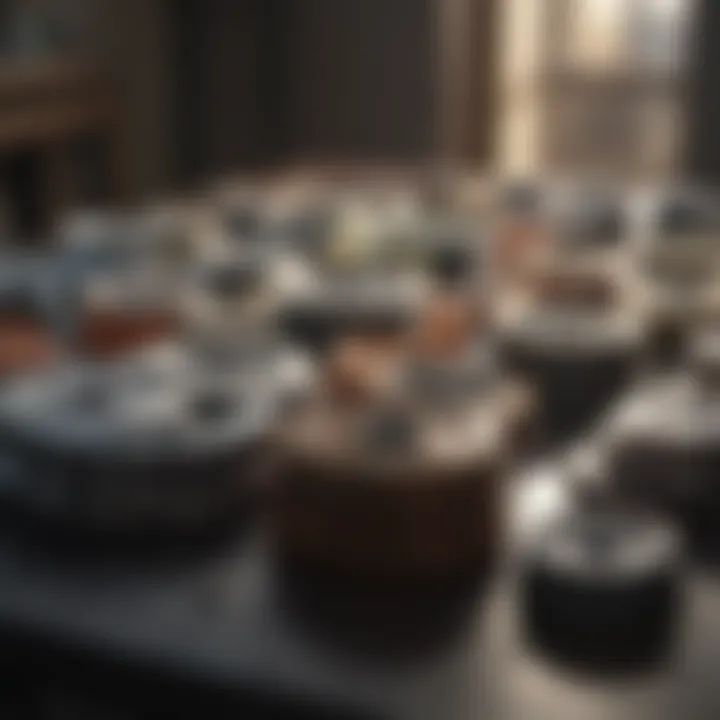
Overview of Topic
Cut off wheels are specialized tools commonly used in the home improvement industry. They are versatile and effective for a variety of tasks, such as cutting metal, masonry, and other materials. Understanding their specifications is crucial for achieving desired outcomes and ensuring safety during use.
The importance of this topic cannot be overstated. Proper knowledge enables users to select the right cut off wheel for each specific application, enhancing both efficiency and safety. Failing to understand the nuances involved can lead to mistakes that may result in poor job performance or injury.
Common Challenges and Solutions
Many homeowners encounter challenges when using cut off wheels. One common issue is selecting the wrong type of wheel for a specific material. For example, using a metal cut off wheel on a masonry surface can yield poor results and increase the risk of accidents.
To overcome this, here are some practical tips:
- Choose the right material: Select wheels made from abrasive materials that are suitable for your task.
- Check compatibility: Ensure that the wheel's size and diameter fit your tool properly.
- Test the equipment: Small test cuts before actual work can help check if chosen equipment works effectively.
Product Recommendations
In the market, there are several reputable brands offering high-quality cut off wheels. Some of the noteworthy product options include:
DEWALT DW8011B5
- Made for metal cutting
- Long durability due to superior materials
- Designed to minimize vibrations
Bosch
- Versatile use for multiple materials
- Reliable and consistent performance
- Engineered for precision
These products stand out for their dependable build quality and effectiveness in performance. Whether cutting through sheet metal or bricks, investing in these tools is advisable.
Step-by-Step Guides
Using a cut off wheel properly involves several steps:
- Select the Cut Off Wheel: Choose based on the material you will be working with and ensure it fits your tool.
- Prepare Your Workspace: Maintain a clean and organized area. Wear proper safety gear like goggles and gloves.
- Mark Your Cut: Utilize a marker to indicate where you plan to cut. Accurate markings lead to cleaner cuts.
- Attach the Wheel: Securely fit the cut off wheel onto the spindle of your tool. Make explcit sure it’s tightly in place to avoid accidents.
- Make the Cut: Position the tool carefully, applying even pressure. Allow the cut off wheel to do the work without forcing the tool.
- Finish the Job: After you finish cutting, inspect the area to ensure there are no sharp edges and clean the work area.
Following these outlined procedures will greatly improve your experiences with cut off wheels. This reduces risks while enhancing both the quality of results and efficiency in your tasks.
Intro to Cut Off Wheels
Understanding cut off wheels is essential for any user aiming to optimize their cutting tasks, whether in renovation projects at home or professional applications. The effectiveness of cut off wheels stems from their design and usage; knowing these aspects can lead to improved results and safety during operation.
In this section, we explore the fundamental aspects that define cut off wheels, underlining their importance in daily tasks. With the right knowledge, users can select the appropriate tools for their projects, whether they involve cutting metal, masonry, or other materials. This foundation ensures decisions are made based on informed choices, enhancing productivity and ensuring safety.
Definition and Purpose
Cut off wheels are specialized rotary discs made for cutting a variety of materials. The purpose of these wheels is to provide a fast, efficient, and precise method of cutting through dense surfaces. Typically attached to power tools like angle grinders, these wheels can slice through materials such as metals, concrete, and ceramics.
Understanding their definition is not just about knowing what they are; it is about acknowledging their role in improving cutting efficiency. Each wheel is formulated according to the material it aims to cut. Their functionality ensures high performance and reduces the wear on the tools they are used with.
Common Applications
The versatility of cut off wheels makes them a common choice across different sectors. Common applications include:
- Metal Fabrication: Cut off wheels efficiently shearing through steel and aluminum.
- Masonry Work: Effective for cutting bricks, tiles, and concrete blocks, aiding in home renovation projects.
- Glass and Ceramics: Specialized wheels designed for precisely cutting glass products without cracking.
Many hobbyists and professionals utilize these wheels for both large and small projects, where precision and performance are paramount. Better selection and understanding directly affect the outcome of the work to be done, highlighting the importance of this introduction.
Types of Cut Off Wheels
Understanding the types of cut off wheels is vital for making informed decisions when selecting the right tools for specific tasks. Each type is designed with particular materials and purposes in focus. Recognizing the distinctions among these categories can lead to improved efficiency, better results in applications, and increased safety during use. Engaging in this detailed exploration of cut off wheel types ensures the reader is well-equipped to choose correctly based on their needs.
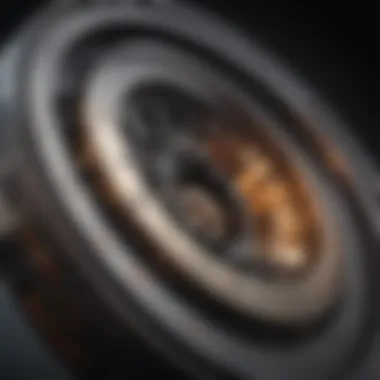
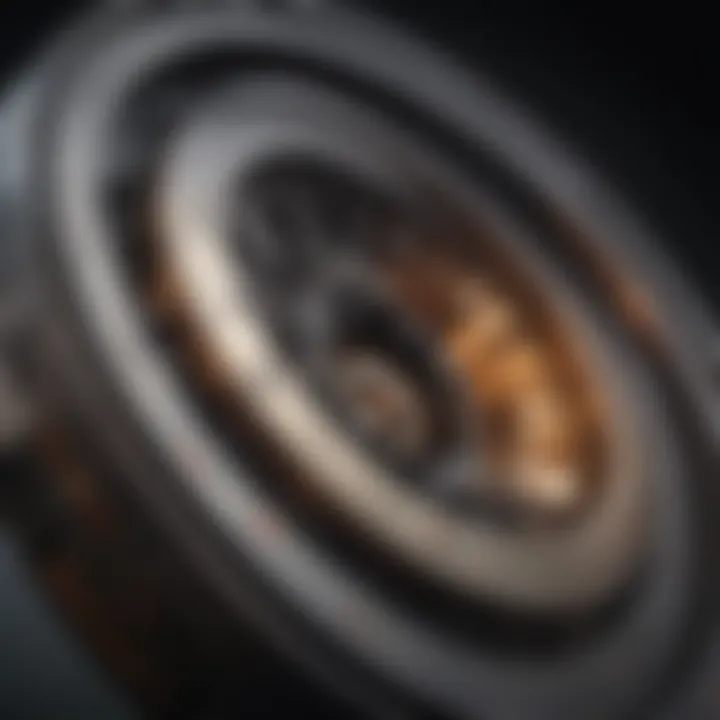
Metal Cutting Wheels
Metal cutting wheels are among the most common types utilized across various industries. They are engineered specifically for cutting ferrous and non-ferrous metals. Typical applications include steel, aluminum, and cast iron. The composition of these wheels usually includes abrasive materials like aluminum oxide, silicon carbide, or zirconia.
Benefits: Metal cutting wheels boast a high removal rate and generate less heat, helping to prolong the life of the blades. Their structure is designed to optimize cutting speed and precision while minimizing material deformation or melting—their importance to manufacturers cannot be overstated.
Consider the bore size and thickness in relation to the specific cuts needed. For example, a thinner wheel is ideal for making precision cuts, while thicker wheels provide greater durability when doing heavy-duty cutting. Careful selection in these aspects can transform the outcomes significantly and positively influence the durability of the cutting equipment.
Stone and Masonry Wheels
When it comes to stone and masonry, specialized cut off wheels are crucial. This category includes blades crafted explicitly for cutting rigid materials like concrete, bricks, and stones. The rough nature of these materials requires wheels that can resist abrasion and withstand greater forces.
These wheels often include diamond segments. The application of diamonds in the abrasives ensures enhanced longevity and cutting capability compared to traditional materials. They significantly improve the cutting efficiency in rugged substrates like granite or concrete.
Considerations: Pay attention to the size and grain structure of the diamond segments. A wheel with larger segments may provide aggressive cutting, but it might not achieve finer finishes needed in maintenance tasks. This understanding helps adapt the cutting approach whether working on building blocks or intricate stone surfaces.
Ceramic and Glass Cutting Wheels
Lastly, ceramic and glass cutting wheels serve a niche but significant purpose in specific professions. These wheels are designed to handle delicate materials that require precision Suction during the cutting process. Their applications extend from crafting tiles to intricate glass cutting.
Typically, these wheels utilize very fine abrasives that prevent chipping or damaging the intricate glass and ceramic surfaces. The reduction in breaks and shards enhances not only the quality of the work but also the safety of the operator.
Consider specifics such as wet versus dry cutting requirements. Some wheels operate better with coolant, significantly reducing friction during the cut. Understanding these needs can optimize results and maintain a safe working environment.
Important: Each type of wheel serves a distinct function in metal, cement, stone, and glass cutting. Choosing the correct type is critical in satisfying operational demands and achieving desired results.
Specifications of Cut Off Wheels
Understanding the specifications of cut off wheels is essential for achieving precision and effectiveness in various projects. Knowing details such as diameter, thickness, bore size, and material composition allows one to select the appropriate wheel for specific tasks. This knowledge not only enhances safety but also improves the overall performance and lifespan of the tools used. Therefore, a focus on specifications is vital when engaging with cut off wheels.
Diameter and Thickness
The diameter and thickness of cut off wheels are significant elements that directly impact their performance in cutting various materials. The diameter typically ranges from 4 to 14 inches, with different applications requiring different sizes. A larger diameter often equates to a deeper cut and may be more suitable for heavy-duty machinery, whereas smaller diameters tend to be better for precise cuts in intricate work.
Thickness affects the scope of the cut as well. A thicker wheel is usually more durable but tends to produce a wider cut, which may not be suitable for work demanding finesse. On the contrary, thinner wheels allow for smoother and less abrasive cuts but may wear down faster. Therefore, understanding the task at hand is crucial when selecting the right diameter and thickness to avoid compromising on quality.
Bore Size and Arbor Hole
Bore size and arbor hole are crucial to ensuring compatibility between the cut off wheel and the power tools being utilized. The arbor hole, which can commonly be found in various sizes like 1 inch or 5/8 inch, allows the wheel to fit securely onto the motor of a grinder or cutting machine. If the bore size does not match the specifications of the equipment, usage can become not only ineffective but also dangerous.
It is imperative to refer to manufacturer's guidelines to find the correct bore size before purchasing a wheel. Also, proper installation is key—it must be mounted securely to prevent vibrations and potential accidents. Ensuring that the bore size aligns with the power tool specifications ultimately leads to safer and more efficient outcomes.
Material Composition
The material composition of cut off wheels significantly dictates their performance, longevity, and suitability for specific tasks. Most cut off wheels are composed of abrasive materials such as aluminum oxide, zirconia, or silicon carbide.
- Aluminum oxide is often used for cutting steel and iron due to its durability.
- Zirconia is better for tougher materials, as it can withstand higher temperatures and offers longer life.
- Silicon carbide works well with materials like glass and ceramic, providing high cutting speeds without much force.
Choosing the correct material composition permits not only a higher efficiency in cutting but also reduces the chances of damage to both the material being cut and the wheel itself. It is advisable to evaluate the material types being cut in relation to the wheel’s abrasive quality to maximize effectiveness.
Knowledge of the specifications offers better selection, enabling enhanced performance and ultimately catering to project needs effectively.
Selecting the Right Cut Off Wheel
Selecting the appropriate cut off wheel plays a crucial role in achieving the desired results in various projects. Given the diverse range of cut off wheels available, understanding the selection criteria helps users make informed decisions. Each wheel type is designed for specific tasks and materials, directly impacting performance and safety. Selecting the incorrect wheel can lead to inefficient cutting, increased wear on the wheel, and even hazardous situations. Thus, it becomes imperative for users to meticulously evaluate their needs, equipment compatibility, and additional factors.
Factors to Consider
When selecting a cut off wheel, several key factors should be considered:
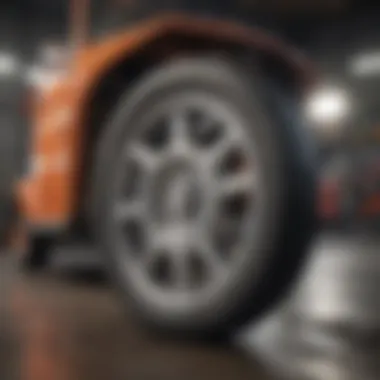
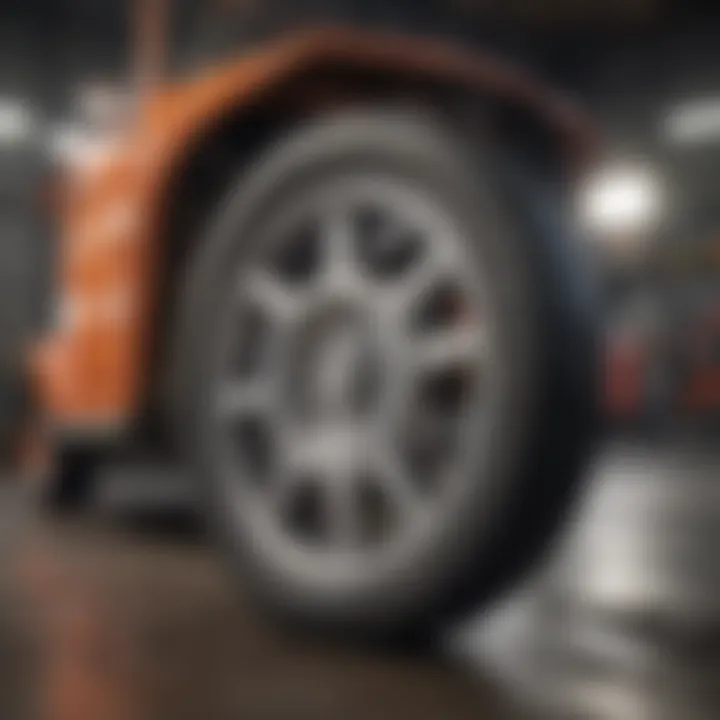
- Material Composition: Different materials require different wheels. For example, metal cutting may require aluminum oxide textures while masonry jobs may need diamond cutting discs.
- Diameter and Thickness: These specifications influence the strength and cutting capacity of the wheel. A thicker wheel can provide more durability albeit may be slower.
- Operator Experience: Knowledge of proper handling can influence wheel life. Beginners should choose simpler wheel types while more experienced users might venture into specialized options.
- Cooling Properties: Selecting wheels that minimize excess heat during operation can result in a cleaner cut and prolong the life of the wheel.
- Safety Ratings: Always check for compliance with safety standards and the reputation of notable brands. High-quality wheels lessen risks during operation.
These elements guide the user in making the most suitable choice, ensuring efficacy and safety during operations.
Compatibility with Equipment
It’s vital to ensure that the cut off wheel competes with your equipment. The arbor hole must match the spindle size of the tool being used. Disparities will cause improper fitting and may lead to unsafe usage.
- Tool Types: Determine whether the cut off wheel is designated for handheld, bench grinders, or floor saws. Each application has its specially designed wheels.
- Speed Ratings: Different tools operate at varied speeds. Adhering to the optimal maximum RPM rating on the wheel will aid performance align with the equipment strength.
- Mounting Features: Certain wheels come with additional features for enhanced grip or security. Consider whether the mounting nature of the wheel fits the selected tool.
Ensuring compatibility fosters better results and enhances safety during the cutting process. By taking into account these factors, users can derive the best out of their cut off wheels.
Safety Considerations
Safety is an essential element when working with cut off wheels. To protect oneself during projects, understanding and following safety guidelines cannot be overstated. Engaging in tasks involving cutting instruments presents risks, including injuries from flying debris and exposure to harmful particles. Therefore, taking safety seriously is crucial.
Personal Protective Equipment
The first line of defense against accidents when using cut off wheels is personal protective equipment, or PPE. PPE includes various gear specifically designed to protect the user. Here are some important items:
- Safety glasses or goggles: Protect the eyes from flying particles.
- Hearing protection: Reduce the risk of hearing damage.
- Respirator masks: Guard against inhaling dust and toxic fumes.
- Cut-resistant gloves: Provide protection for the hands from sharp edges.
- Dust mask: Prevent inhalation of harmful particles from materials being cut.
Wearing PPE is not just recommended; it is necessary. For those not accustomed to such tasks, donning appropriate gear may feel unnecessary at first. However, one lapse in safety might change everything, resulting in significant injuries or accidents.
Operating Procedures
Establishing proper operating procedures represents another vital component of safety when using cut off wheels. Following standard protocols maximizes safety and efficiency. Here are some best practices to consider:
- Examine the equipment before use: Check for damages to the cut off wheel and machine itself.
- Ensure a stable working area: A clutter-free environment helps prevent accidents.
- Use the right cutting speed: Proper speeds are essential for effective results and safety. Refer to instructions from the wheel manufacturer's guidelines.
- Maintain a firm grip and stance: Stand firmly and hold the tool properly to minimize risks.
- Follow the blade's design: Make sure the cut off wheel aligns with the material being processed. Avoid applying lateral or excessive force.
Following these operating procedures does not guarantee accidents will not occur, but they greatly reduce the chance of incidents. Consistent attention to both PPE and established procedures will enhance the overall safety of using cut off wheels, thereby ensuring that projects proceed smoothly and safely.
Following safety precautions when using cut off wheels not only protects lives and limbs but also ensures projects have a better chance of success and efficiency without disruptions.
Best Practices in Using Cut Off Wheels
Understanding the best practices in using cut off wheels is crucial for both safety and efficiency. These practices help maximize the performance of the wheels and prolong their life. Adhering to specific techniques and managing heat can significantly influence the satisfied results in cutting. Moreover, these elements ensure a safer environment, benefiting not just the user but also the quality of work produced. Multiple factors shape one's experience with cut off wheels—hence considerations about proper usage shouldn't be marginalized.
Proper Techniques
Mastering cutting techniques stands as the foundation for better results. Here are important techniques to grasp:
- Aligning with the Workpiece: Always make sure the cut off wheel aligns with the cutting line. Misalignment may cause unnecessary strain on the wheel, reducing its effectiveness and lifespan.
- Controlled Force Application: Apply gentle, controlled pressure when cutting. Overzealous force can warp the wheel or cause it to break, resulting in both damage and hazards.
- Cutting Speed: Use moderate speed. Going too fast may increase friction and reduce cutting effectiveness. Likewise, very low-speed doesn’t provide proper cutting action. Balancing speed is key.
- Blade Angle: Maintain a consistent angle. A proper angle aids in effective cutting and avoids additional wear. Typically, a 90-degree angle serves for straight cuts, enabling optimal engagement with the material.
Employing these techniques makes handling cut off wheels safer and more productive.
Heat Management
Heat management directly relates to the durability of cut off wheels. Excessive heat can lead to wear and degrade performance. Monitoring temperature is integral. Consider the following steps:
- Coolant Use: Apply engagement with coolant when cutting. Coolants like water or lubricants minimize heat generated and mitigate friction. Tools shaped for downtime can optimize cooldown time.
- Monitoring Duration: Avoid prolonged cutting to curb heat buildup. Breaks between cutting allow end-user and tool resilience.
- Material Selection: The choice of the material influences heat generation. For example, selecting a diamond-blade wheel for stone might reduce overheating due to compressive strengths.
These heat management strategies help in lowering the risk of cracking or burning and assist to prolong the life of the cut off wheels.
Leveraging proper techniques along with keen heat management prepares users for success and ensures the longevity of tools.
Implementing these practices should greatly enhance one’s experience with cut off wheels, leading to better results and ensuring sustained quality in projects.
Maintenance of Cut Off Wheels
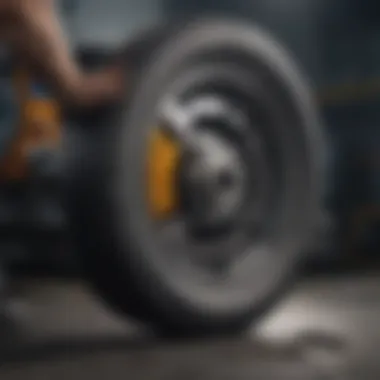

Maintenance of cut off wheels is crucial for ensuring their effectiveness and longevity. Proper maintenance practices not only enhance performance but also promote safety, minimizing the risk of accidents caused by equipment failure or wheel breakage. Maintaining cut off wheels involves multiple aspects, including storage, regular inspections, and adhering to best practices during use.
The benefits of diligent maintenance are significant. Regularly checking wheels for wear and damage ensures tools remain in optimal working condition. By following the guidelines outlined below, users can protect their investment and improve the overall quality of their work.
Storage Guidelines
Storing cut off wheels correctly reduces the chance of damage and preserves their quality. Here are some recommendations:
- Keep Wheels In Original Packaging: The original packaging offers appropriate protection against environmental factors. It helps avoid moisture and dust exposure, preventing wheel coma, warping, or deformation.
- Store Vertically: If the wheels are stacked, they should be placed vertically to prevent excessive pressure on the edges. Stacking them horizontally can lead to cracking and other structural damage.
- Maintain a Controlled Environment: Store in a cool, dry place to prevent deterioration caused by humidity or extreme temperature changes. High temperatures can affect the integrity of certain materials used in wheels.
By following these simple storage guidelines, users can significantly enhance the lifespan of their cut-off wheels.
Inspection for Wear and Damage
Regular inspections are essential for identifying any sign of wear or damage. Ignoring these inspections can lead to serious problems during usage. Here are key factors to consider during your inspection:
- Look for Visible Cracks: After each use, inspect the wheel surfaces for stress cracks or chips. Such damage can lead to wheel breakdown while cutting, posing a major risk.
- Check for Uneven Wear: Observe the exterior of the wheel for signs of uneven wear. If certain areas appear more worn out, this may indicate improper use or angle during cutting. Inconsistent wear may also compromise the integrity of the wheel.
- Evaluate Arbor Hole: Ensure the arbor hole is intact. It should fit snugly on the equipment's spindle without excessive wobbling.
Environmental Considerations
Environmental considerations play a crucial role in the usage of cut off wheels, as they directly impact the sustainability of practices within various industries. In a time where environmental awareness is rising, it is imperative for both house owners and professionals to recognize the implications of their tools and materials on our ecosystem. Understanding how cut off wheels affect the environment can lead to more responsible choices and ultimately, a more sustainable approach to cutting tasks.
Sustainability of Materials Used
The sustainability of materials used in cut off wheels needs careful evaluation. Most wheels are designed from various materials which have different environmental footprints. Investing in cut off wheels made from eco-friendly materials, such as diamond and ceramic, can present better longevity and efficiency. These materials not only cut effectively but also tend to reduce the need for replacements, resulting in less waste produced.
Additionally, some manufacturers focus on employing recyclable materials in their products. When materials are selected with sustainability in mind, the overall impact they have during their life span is notably mitigated, providing a dual advantage of performance as well as reducing waste. Calibrating the blend of performance and environmental impact can guide consumers toward making more informed decisions regarding the cut off wheels they choose.
Waste Management of Used Wheels
Proper waste management of used cut off wheels is vital in minimizing their negative environmental effects. Disposing of these wheels inappropriately can lead to increased pollution and resource wastage. It is essential to establish clear protocols for handling used wheels once they reach the end of their service life.
Here are some steps to follow for effective waste management:
- Recycling Programs: Seek manufacturers or local facilities that have recycling programs for used wheels. Engaging with a recycling initiative can transform waste into valuable secondary materials.
- Community Workshops: Encourage participation in community or workshop-based events, where used cut off wheels can be collected and repurposed safely.
- Proper Disposal: If recycling is unfeasible, make sure to follow local regulations on hazardous waste disposal to keep the environment safe.
Emerging Technologies in Cut Off Wheels
Emerging Technologies in cut off wheels represent a pivotal aspect of advancements in the cutting tools sector. As industries evolve, the demands for high-efficiency, safety, and sustainability grow. Innovations in this field not only refine the cutting process but also enhance user experience significantly.
The significance of these technologies stems from several key elements:
- Material Enhancements: New materials improve cutting speed and longevity.
- Efficiency Gains: Designs that minimize energy use and maximize performance.
- User-Centric Features: Innovations cater to safety and ease of use, making products more accessible, especially for house owners and DIY enthusiasts.
Integrating these advancements is vital for optimizing performance, reducing operational costs, and maintaining safety standards. This pursuit for continuous improvement benefits all users in the cut off wheel market.
Advancements in Material Science
Recent developments in material science have revolutionized cut off wheels. Various exotic materials primarily dominate improvements. For example, diamond and ceramic composite materials have emerged as key components in modern wheels. These materials enhance durability significantly, allowing users to cut through harder materials with greater ease.
The primary benefits include:
- Durability: Longer lifespan compared to traditional steel wheels.
- Precision: Improved cutting accuracy minimizes wastage.
- Versatility: Effective in various applications, from metal to masonry.
One notable example can be seen in diamond-blade cutting wheels. Their ability to handle tough materials like concrete and stone is noteworthy and continues to gain traction across different user bases.
Future Trends in Cut Off Wheel Design
As industries grow, so must cut off wheel designs. Future trends promise convenience and efficiency. A notable aspect includes ergonomic designs tailored for easier manipulation and reduced fatigue during use.
Moreover, smart technologies integrated within those wheels create possibilities for:
- Real-time Monitoring: Sensors can indicate wear levels, ensuring safety and efficiency.
- Customizable Fittings: Easy adaptation for different machines enhances operational flexibility.
- Sustainable Practices: Innovations aim at using eco-friendly materials and processes, aligning with global sustainability goals.
These advances points clearly towards a future where functionality aligns with user needs and environmentally friendly practices. The fusion of material science and innovative designs holds potential for better ergonomic options.