A Comprehensive Guide to Industrial Enamel: Unveiling Its Uses and Benefits
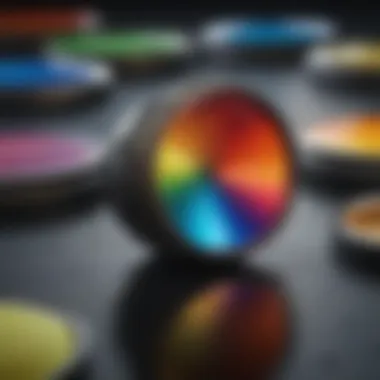
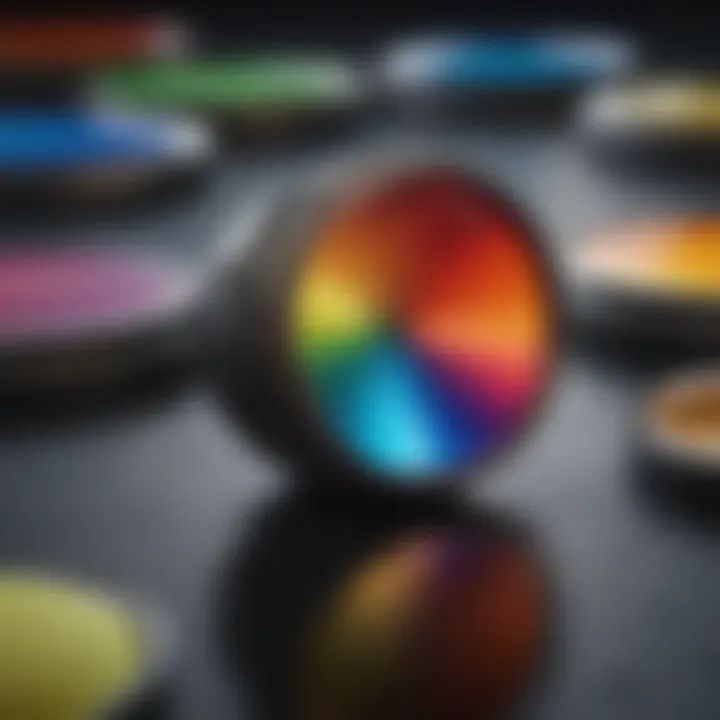
Overview of Industrial Enamel in Home Improvement
Industrial enamel plays a crucial role in the home improvement industry as a versatile coating material that offers durability and enhances aesthetics. It is widely used for various applications, such as protecting surfaces from corrosion, providing a smooth finish, and adding vibrant color to surfaces. The importance of industrial enamel lies in its ability to prolong the lifespan of different materials while giving them a polished look, making it a popular choice for homeowners seeking long-lasting solutions for their surfaces.
Common Challenges and Solutions
Homeowners often face common issues related to industrial enamel, such as improper application leading to streaks or bubbling, chipping over time, or difficulty in color matching for touch-ups. To overcome these challenges, it is essential to ensure proper surface preparation before applying enamel, use high-quality brushes or sprayers for even application, opt for enamel with added durability features, and store leftover enamel properly to prevent deterioration. Additionally, consulting with professionals or following manufacturer's guidelines can provide further insights into solving these common challenges effectively.
Product Recommendations
When considering industrial enamel products for home improvement projects, it is essential to choose quality brands like Rust-Oleum, Behr, and Sherwin-Williams known for their durability, color options, and ease of application. Rust-Oleum's Professional High-Performance Enamel offers excellent adhesion and resistance to wear and tear, making it ideal for high-traffic areas. Behr's Premium Direct-To-Metal Paint provides superior rust protection and a wide range of finishes to suit different aesthetic preferences. Sherwin-Williams Pro Industrial Enamel is renowned for its durability and quick drying time, perfect for efficient home improvement projects.
Step-by-Step Application Guide
For a successful industrial enamel application in home improvement, follow these steps meticulously:
- Surface Preparation: Clean the surface thoroughly, ensuring it is free from dirt, rust, and debris to promote proper adhesion.
- Priming: Apply a primer compatible with the chosen enamel to enhance durability and adhesion to the surface.
- Application Technique: Brush, roll, or spray the enamel in thin, even coats, following the manufacturer's recommended drying times between layers.
- Drying and Curing: Allow the enamel to dry and cure per the instructions provided, ensuring proper ventilation for optimal results.
- Finishing Touches: Inspect the surface for any imperfections or touch-up areas as needed, ensuring a flawless finish.
By adhering to these meticulous instructions and choosing top-quality enamel products, homeowners can achieve professional results in their home improvement projects, elevating the aesthetics and durability of various surfaces with industrial enamel.
Introduction to Industrial Enamel
Industrial enamel serves as a crucial component in various industries, playing a significant role in enhancing durability, aesthetics, and protection of surfaces. This article aims to provide a detailed exploration of industrial enamel, shedding light on its composition, application techniques, benefits, and applications across different sectors. Understanding the fundamentals of Industrial Enamel is essential for both professionals and enthusiasts seeking to delve deeper into the world of protective coatings.
Defining Industrial Enamel
When it comes to defining Industrial Enamel, it is essential to examine its components, types, and distinguish it from traditional paint. Industrial Enamel is characterized by its resilience, color retention, and ability to withstand environmental factors, making it a preferred choice for various applications.
Components of Industrial Enamel
Industrial Enamel typically consists of resins, pigments, solvents, and additives. These components work together to provide adhesion, color, durability, and chemical resistance to the coating. The unique blend of these materials ensures that Industrial Enamel offers long-lasting protection against corrosion and wear, making it an indispensable solution for surfaces exposed to harsh conditions.
Types of Industrial Enamel
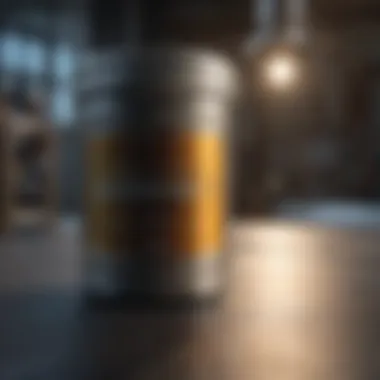
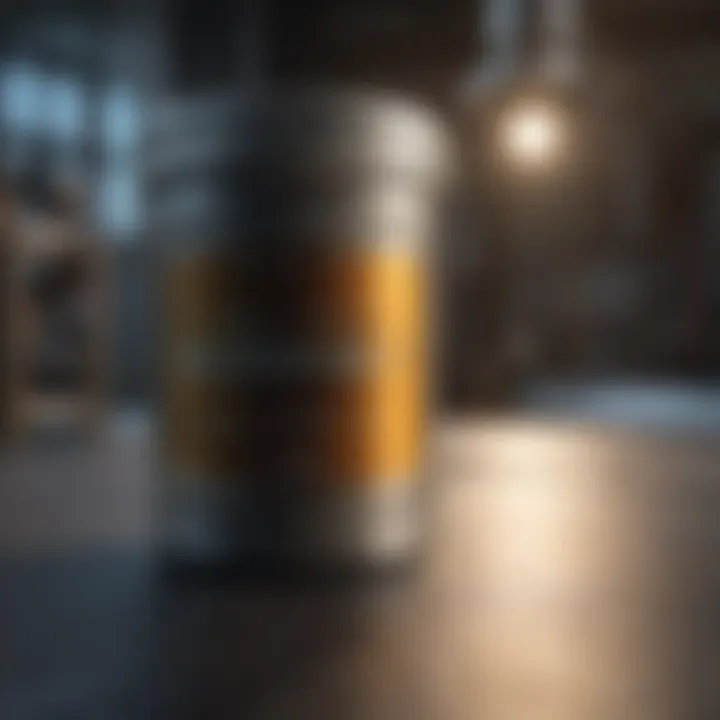
There are different types of Industrial Enamel, such as acrylic, alkyd, and polyurethane enamels, each with its distinct characteristics and applications. Acrylic enamels are known for their fast drying time and UV resistance, making them ideal for outdoor use. Alkyd enamels offer excellent adhesion and durability, while polyurethane enamels provide superior chemical and abrasion resistance. Understanding the various types of Industrial Enamel allows users to select the most suitable option based on their specific needs.
Industrial Enamel vs. Traditional Paint
Industrial Enamel stands out from traditional paint due to its higher durability, chemical resistance, and longevity. While traditional paint may offer aesthetic appeal, Industrial Enamel goes beyond surface-level enhancements, providing robust protection against corrosion, impact, and harsh environments. The distinct formulation of Industrial Enamel makes it a preferred choice for industries that require high-performance coatings.
Historical Evolution of Industrial Enamel
The historical evolution of Industrial Enamel showcases its journey from early applications to modern technological advancements, highlighting the continuous innovation in coating technology.
Origins and Early Applications
Industrial Enamel traces its origins back to ancient civilizations where protective coatings were applied to metal surfaces for corrosion prevention and decorative purposes. Over time, the adoption of Industrial Enamel expanded to various industries, including automotive, aerospace, and construction, showcasing its versatility and reliability. The early applications of Industrial Enamel set the foundation for its widespread usage in contemporary settings.
Technological Advancements in Industrial Enamel
Advancements in technology have greatly influenced the development of Industrial Enamel, leading to improved formulations, application methods, and performance attributes. Modern Industrial Enamel formulations now offer enhanced durability, faster curing times, and increased customization options, catering to the diverse needs of industries worldwide. The integration of nanotechnology and advanced coatings research continues to propel the evolution of Industrial Enamel, ensuring its relevance in a constantly evolving industrial landscape.
Properties of Industrial Enamel
Industrial enamel possesses a myriad of properties that make it a highly sought-after coating material in various industries. Understanding the properties of industrial enamel is crucial in appreciating its utility and versatility. In this article, we will delve deep into the essential characteristics that define industrial enamel, shedding light on its durability, aesthetic appeal, and protective qualities. By exploring the properties of industrial enamel, readers will gain a comprehensive understanding of why it is the preferred choice for numerous applications.
Durability and Longevity
Resistance to Corrosion
Resistance to corrosion is a key aspect of industrial enamel that sets it apart from traditional paint. Industrial enamel is specially formulated to withstand harsh environmental conditions, moisture, and corrosive substances, making it an ideal choice for surfaces exposed to the elements. The unique composition of industrial enamel creates a protective barrier that prevents the onset of corrosion, ensuring the longevity of coated surfaces. Its ability to resist rust and deterioration makes it a popular choice for outdoor equipment, machinery, and automotive components.
Impact of Environmental Factors
The impact of environmental factors on industrial enamel's performance is paramount in assessing its overall effectiveness. Industrial enamel is designed to withstand UV exposure, extreme temperatures, humidity, and chemical exposure without deteriorating. This resilience to environmental stresses ensures that surfaces coated with industrial enamel remain durable and attractive for an extended period. By considering the impact of environmental factors, users can confidently select industrial enamel for applications that require long-lasting protection and aesthetics.
Aesthetic Appeal
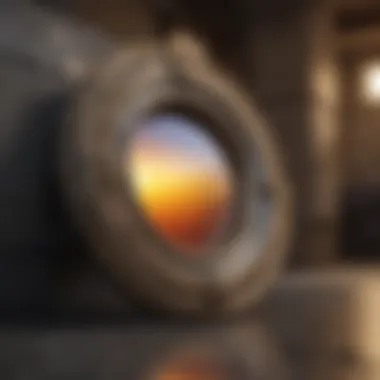
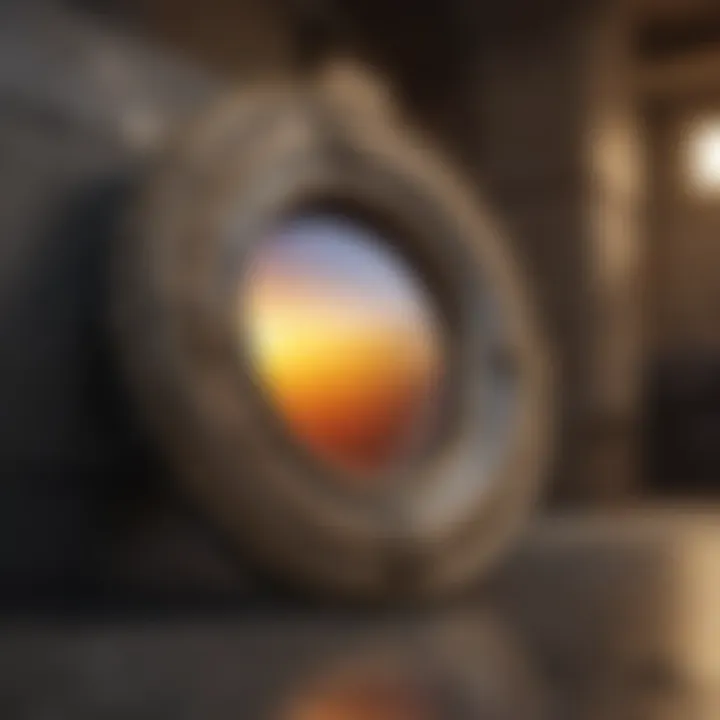
Color Retention
One of the standout features of industrial enamel is its superior color retention properties. Unlike traditional paint, industrial enamel maintains its vibrant colors without fading or yellowing over time. The advanced formulations of industrial enamel ensure that the colors stay true and vibrant even in challenging conditions, adding a layer of visual appeal to coated surfaces. Whether used for decorative purposes or brand recognition, the color retention capabilities of industrial enamel make it a top choice for enhancing aesthetics.
Finish Options
Industrial enamel offers a wide range of finish options, allowing users to achieve the desired look and texture for their surfaces. From glossy finishes to matte textures, industrial enamel can be customized to suit different styles and preferences. The versatility of finish options provided by industrial enamel gives users the flexibility to create visually stunning coatings that enhance the overall appearance of objects and structures. By exploring the diverse finish options available, users can select the perfect industrial enamel finish to elevate the visual appeal of their projects.
Applications of Industrial Enamel
In this comprehensive guide, the section on Applications of Industrial Enamel plays a pivotal role in highlighting the practical usage and significance of this coating material. Industrial enamel finds extensive application across various industries due to its exceptional properties that enhance durability, aesthetics, and protection. Understanding the diverse applications of industrial enamel provides insights into its versatility and adaptability in different contexts.
Automotive Industry
Vehicle Coatings
Vehicle Coatings form a crucial aspect of industrial enamel application in the automotive industry. The key characteristic of Vehicle Coatings lies in their ability to provide a durable and visually appealing finish to vehicles. Industrial enamel is a preferred choice for Vehicle Coatings due to its excellent adhesion, corrosion resistance, and color retention properties, ensuring long-lasting protection for automotive surfaces. The unique feature of Vehicle Coatings is their ability to withstand harsh environmental conditions and frequent wear, making them a popular choice for vehicle manufacturers and refurbishment services. While Vehicle Coatings offer impeccable protection and aesthetic enhancement, they may require specialized application techniques for optimal results.
Protective Finishes
Protective Finishes play a vital role in safeguarding automotive surfaces from external elements and ensuring longevity. The key characteristic of Protective Finishes is their ability to create a protective barrier against corrosion, impacts, and abrasions, extending the lifespan of automotive components. Industrial enamel serves as an ideal option for Protective Finishes due to its high durability, chemical resistance, and customizable finish options. The unique feature of Protective Finishes is their capacity to maintain the structural integrity of vehicles while enhancing their visual appeal. While Protective Finishes provide comprehensive protection, careful consideration of environmental factors and application methods is essential to maximize their effectiveness.
Industrial Equipment
Machinery Coatings
Machinery Coatings constitute a critical aspect of industrial enamel usage in industrial equipment applications. The key characteristic of Machinery Coatings lies in their ability to withstand heavy use, extreme conditions, and chemical exposure, ensuring the longevity and performance of machinery components. Industrial enamel is a preferred choice for Machinery Coatings due to its exceptional adhesion, impact resistance, and ease of maintenance, enhancing the durability and functionality of industrial equipment. The unique feature of Machinery Coatings is their capability to prevent corrosion, reduce friction, and enhance operational efficiency, making them a valuable investment for industries requiring robust machinery protection. While Machinery Coatings offer significant benefits, proper surface preparation and application techniques are crucial for achieving optimal results.
Workshop Applications
Workshop Applications play a significant role in preserving the workspace environment and improving the aesthetics of industrial settings. The key characteristic of Workshop Applications is their ability to provide a clean, protective, and visually appealing coating on various surfaces within workshops. Industrial enamel is favored for Workshop Applications due to its versatility, quick drying time, and resistance to chemicals and oils, enhancing the longevity and hygiene of workspace areas. The unique feature of Workshop Applications is their capacity to transform bland workshop surfaces into vibrant, corrosion-resistant spaces that promote safety and efficiency. While Workshop Applications offer aesthetic and protective advantages, proper ventilation, thorough cleaning, and precise application methods are essential considerations for successful implementation.
Application Techniques
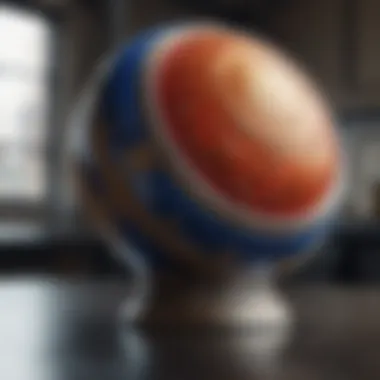
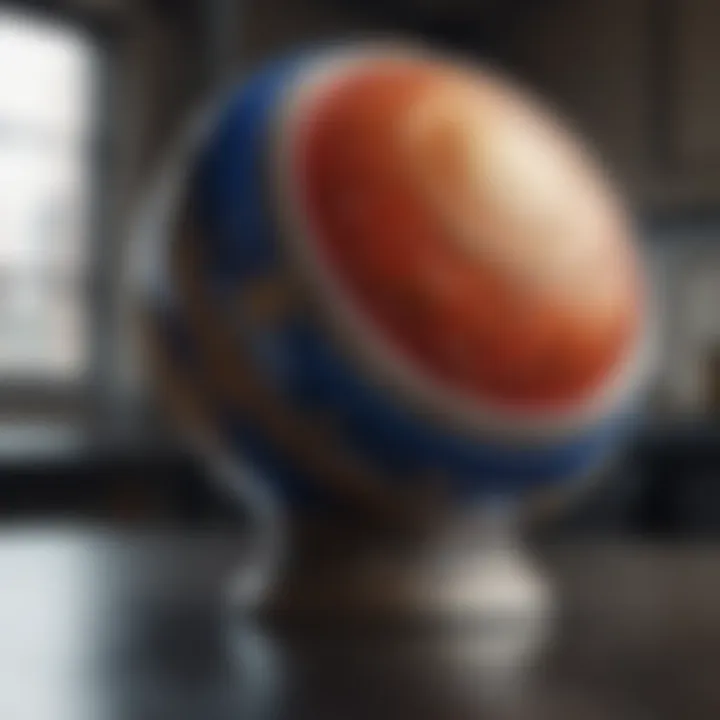
Industrial enamel application techniques play a pivotal role in ensuring a successful coating outcome. Understanding the intricacies of these techniques is crucial for achieving optimal results in various industries. By delving into the specifics of application methods, it enables a deeper comprehension of how industrial enamel can be effectively utilized.
Spray Application
Spray application is a predominant method used for applying industrial enamel due to its efficiency and flawless finish. The equipment requirements for spray application are essential for achieving a consistent and uniform coating on surfaces. The choice of equipment impacts the overall quality and durability of the enamel application.
- Equipment Requirements: The equipment needed for spray application includes spray guns, compressors, and ventilation systems. These components contribute significantly to the precision and even distribution of the enamel on surfaces. The choice of equipment directly affects the efficiency and effectiveness of the application process, leading to enhanced results.
- Best Practices: Optimal practices for spray application involve ensuring proper ventilation, correct nozzle adjustments, and consistent pressure settings. These practices guarantee a smooth and uniform coating, reducing the risk of dripping or uneven application. Following best practices is key to achieving a professional finish and maximizing the benefits of spray application.
Brush and Roller Application
Brush and roller application techniques offer versatility in applying industrial enamel, especially in scenarios where precision and control are paramount. Understanding the techniques involved in brush and roller application is essential for achieving desired outcomes with industrial enamel coatings.
- Techniques for Even Coating: Achieving an even coating with brush and roller application involves proper loading of enamel, controlled pressure during application, and consistent strokes. These techniques ensure uniform coverage and enhance the aesthetic appeal of the final finish. The proficiency in applying even coatings is crucial for maximizing the protective properties of industrial enamel.
- Surface Preparation: Adequate surface preparation is vital for brush and roller application to ensure adhesion and durability. Proper cleaning, priming, and smoothing of surfaces before applying enamel contribute to the longevity and effectiveness of the coating. Surface preparation techniques determine the overall quality and resilience of the enamel coating, making it a critical aspect of the application process.
Benefits of Industrial Enamel
Industrial enamel offers a plethora of benefits that make it a crucial choice for various applications. From enhancing protection to providing cost-efficiency, the advantages of industrial enamel are multifaceted and impactful. This section delves deep into the specific elements that highlight the importance and practicality of utilizing industrial enamel coatings.
Enhanced Protection
Industrial enamel excels in providing enhanced protection for surfaces, making it a highly sought-after coating material. Within this realm, two key aspects stand out: prevention of corrosion and impact resistance.
Prevention of Corrosion
The prevention of corrosion is a critical feature of industrial enamel that significantly contributes to its overall efficacy. Industrial enamel coatings form a robust barrier against corrosive agents, shielding underlying surfaces from degradation and deterioration. The unique rust-resistant properties of industrial enamel make it a popular choice for applications requiring long-term protection against environmental factors. Despite its undeniable advantages, the main drawback of this protection is the need for proper application and periodic inspections to maintain its integrity.
Impact Resistance
Another essential characteristic of industrial enamel is its remarkable impact resistance. This quality ensures that coated surfaces can withstand physical damage and stressful conditions without compromising the underlying structure. Industrial enamel's ability to absorb and disperse impact energy makes it an ideal solution for applications where durability is paramount. While offering unparalleled protection, the downside of impact resistance lies in the potential for chip or scratch formation under severe mechanical stress.
Cost-Efficiency
In addition to enhanced protection, industrial enamel also boasts significant cost-efficiency benefits that contribute to its widespread use across different industries.
Long-Term Savings
One of the primary cost-saving aspects of industrial enamel is its capacity for providing long-term savings. By offering durable protection against corrosion and wear, industrial enamel coatings reduce the frequency of recoating and repair, resulting in extended product lifespan. The longevity and resilience of industrial enamel make it a valuable investment that pays off in terms of reduced maintenance and replacement costs. However, the initial cost of high-quality industrial enamel coatings may pose a barrier for some budget-conscious consumers.
Reduced Maintenance Costs
Furthermore, industrial enamel plays a pivotal role in reducing maintenance costs due to its low-maintenance nature and long-lasting performance. The easy-clean properties of industrial enamel surfaces simplify upkeep, requiring minimal effort and resources for maintaining a pristine appearance. By minimizing the need for frequent touch-ups and repairs, industrial enamel helps homeowners and facility managers cut down on maintenance expenses over time. Despite these advantages, occasional specialized maintenance may be necessary to address specific issues and ensure optimal coating performance.