Selecting the Best Grease for Electrical Connections
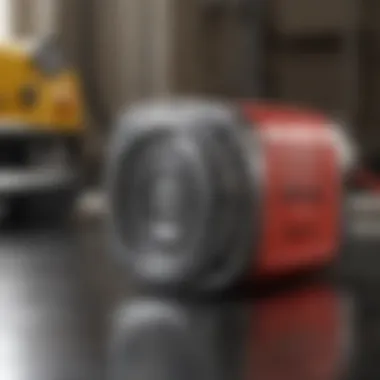

Intro
In the realm of home improvement, a small but significant component often goes unnoticed: the grease used for electrical connections. While most homeowners might not give it a second thought, choosing the right grease can make all the difference between a well-functioning circuit and unexpected issues down the line. Proper electrical contact is essential not only for efficiency but also for safety, and that’s where grease steps into the spotlight.
Using grease with suitable properties can help to enhance conductivity, fend off corrosion, and manage heat effectively. In simple terms, this means it aids in maintaining optimal performance in your electrical systems. A good quality grease acts as a protective barrier and improves the longevity of electrical connections, making it a must-consider in your home maintenance toolkit.
Importance of the Topic
Neglecting the significance of the right grease can lead to several problems, like reduced connection quality, frequent maintenance needs, and potential safety hazards. When electrical connections become oxidized or corroded, it can cause failure or inefficient operation of appliances or systems. With the right grease at hand, homeowners can minimize these risks, thus enjoying a more reliable and long-lasting electrical system.
Understanding the intricacies of electrical grease can empower homeowners to make informed decisions, ultimately resulting in healthier electrical installations. This guide aims to provide the necessary insights, navigating through various product choices and their applications, helping you to ensure your connections stand the test of time.
Understanding Electrical Connections
Electrical connections serve as the backbone of virtually all electrical systems. Their reliability can make or break the performance of devices ranging from household appliances to complex industrial machinery. Understanding these connections reveals the necessity for careful maintenance and enhancement techniques, particularly focusing on the type of grease applied to them. Grease is not just a mere accessory; it plays an instrumental role in ensuring optimal functionality and longevity of electrical systems. Without proper application of the right grease, the integrity of connections can be compromised, leading to failures that may have costly repercussions.
The Role of Grease in Electrical Systems
Grease has multiple functions within electrical systems. Firstly, it facilitates electrical conductivity while preventing corrosion, two factors that are often at odds with one another. Applying the right type of grease ensures that power flows freely, while also protecting components from oxidative damage. Moreover, grease acts as a barrier against moisture, which is notorious for creating short circuits and other failures. It's like putting on a good pair of gloves before stepping out into the cold; a small yet crucial step towards preventing bigger problems.
Common Issues in Electrical Connections
Common issues that arise in electrical connections can be categorized into three main types: Corrosion, Arcing, and Oxygen Exposure.
Corrosion
Corrosion is a tale as old as time in the world of electrical connections. It's that slow, insidious process where metal reacts with moisture and oxygen, leading to degradation. The key characteristic of corrosion is its ability to form non-conductive barriers between electrical contacts. This can lead to increased resistance and eventual failures in connection. Not to mention, corrosion can accumulate over time, making it a sneaky enemy that goes largely unnoticed until it’s too late. Understanding corrosion is vital because choosing the right type of grease can either exacerbate or minimize its effects.
Proper grease can significantly limit corrosion and extend the life of electrical connections.
Arcing
Arcing occurs when electricity jumps between two points. This can create sparks, leading to potential damage to electrical components. The key characteristic of arcing is its unpredictable nature; it can occur suddenly and often without warning. In the context of this article, understanding arcing is important because the right grease can help to provide a cushioning effect that minimizes its occurrence. Essentially, by applying grease, you are insulating the connection against the rapid discharge that typically leads to arcing. However, if the wrong type of grease is applied, it can actually enhance the situation, creating a direct pathway for electricity to escape.
Oxygen Exposure
Oxygen exposure in electrical connections is a double-edged sword. On one hand, oxygen is necessary for life; on the other hand, it's a primary contributor to oxidation in metals. The key characteristic of oxygen exposure is that it accelerates corrosion processes. Additionally, its ubiquitous presence makes it nearly impossible to avoid. In the scope of this article, recognizing how oxygen interacts with electrical connections helps in selecting the appropriate grease. The right grease acts as a shield, effectively limiting the amount of oxygen that can react with exposed metal surfaces. This armors electrical connections against the ravages of time and environment, ensuring that they maintain their effectiveness and longevity.
Types of Grease Suitable for Electrical Connections
When it comes to ensuring optimal performance in electrical connections, the type of grease used plays a crucial role. Choosing the right grease can significantly enhance conductivity, mitigate corrosion, and maintain the integrity of connections over time. Hence, understanding the diversity of greases available can help in making well-informed decisions that lead to better maintenance and fewer issues.
Conductive Grease
Characteristics and Composition
Conductive grease is formulated specifically to improve the flow of electricity across connections. Its primary ingredient is typically silver or graphite, giving it high electrical conductivity. This makes it a favored choice in applications where electrical current needs to flow smoothly.
One standout trait is its viscosity. Conductive greases retain a sticky yet spreadable quality, allowing them to stay in place during operation. This characteristic is advantageous because it ensures that the conductive material remains effective over time, reducing wear and tear on electrical components. However, a downside to consider is that it can be more expensive than conventional greases, which may put a damper on budget-conscious projects.
Applications and Limitations
In practical terms, conductive grease finds its sweet spot in high-performance environments, such as automotive and industrial applications. It is invaluable for connectors that require reliable conductivity under high-stress conditions. An example includes high-amperage electrical connections found in hybrid vehicles.
Yet, there are limitations. Its effectiveness can diminish in extreme temperatures, as excessive heat may cause the grease to break down. Additionally, while conductive grease enhances conductivity, it may not shield against moisture and dirt, necessitating further protective measures in humid environments.
Dielectric Grease
Properties and Benefits
Dielectric grease is a non-conductive compound made mostly of silicone. The primary appeal of dielectric grease lies in its ability to protect electrical connections from moisture and contaminants, safeguarding against corrosion. This grease is particularly beneficial in environments where exposure to water is a concern, such as outdoor settings or marine applications.
One key benefit is its thick consistency, which allows it to form a protective barrier that keeps moisture away. Its durability is another plus; dielectric grease can withstand a range of temperatures and remains effective without breaking down easily over time. However, it should be noted that while it offers moisture protection, it does not improve the conductivity of electrical connections, making it less suited for situations where enhanced conductivity is essential.
Appropriate Uses
Dielectric grease shines in situations like spark plug boots, electrical connectors, and terminals where moisture exposure is high. Its insulating properties make it popular for applications in automotive and outdoor electrical setups.
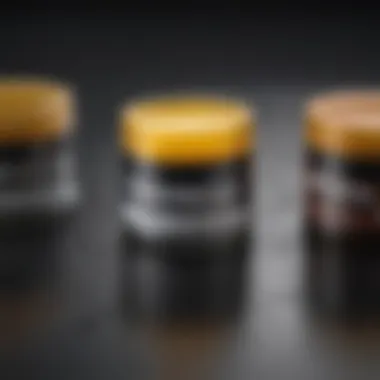
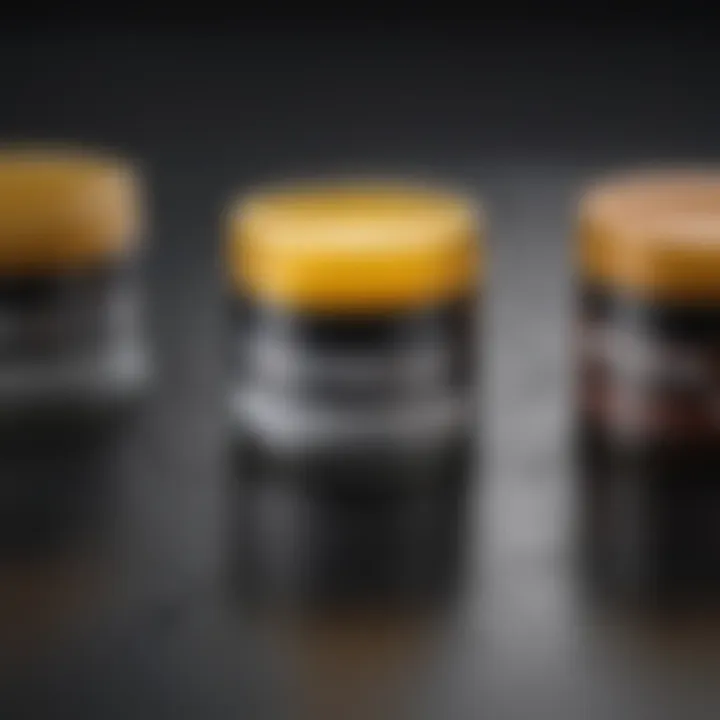
That said, the non-conductive nature is also a drawback. It should never be used on connections where electrical flow is critical, as it may hinder the required conductivity needed for optimal performance. So while it provides excellent moisture protection, one must weigh the specific application needs carefully before opting for dielectric grease.
Silicone-Based Grease
Advantages and Disadvantages
Silicone-based grease is heralded for its versatility. It offers a unique blend of lubrication and protection, making it a staple in various maintenance and electrical applications. Its wide service temperature range is a significant advantage, allowing it to perform in both low and high temperatures without breaking down.
However, this grease comes with its own set of considerations. While it is excellent for preventing corrosion and is chemically inert, it does not conduct electricity as some other greases do. Therefore, in scenarios requiring high conductivity, silicone grease may not be the optimal choice.
Situations for Use
Silicone grease is perfect for situations where lubrication is essential along with moisture resistance. One common application is in electronic contacts, where it can protect components while allowing for easy disassembly and maintenance.
Nonetheless, it lacks the conductivity that more specialized greases offer. Thus, while it serves well in maintaining communication in wiring or when using connectors, it is not advised for high-current applications.
In summary, selecting the right grease for electrical connections hinges upon understanding the various options available and the specific needs of the application. Each type brings its own benefits and limitations, which is why taking the time to analyze usage scenarios can go a long way in ensuring lasting performance.
Key Properties of Electrical Grease
To ensure efficient and reliable performance of electrical connections, the properties of grease used hold significant importance. Electrical grease does not merely serve the role of lubrication; rather, it acts as a protective barrier against issues such as corrosion, moisture ingress, and thermal fluctuations. By recognizing the key properties of electrical grease, individuals can better appreciate how these factors contribute to the longevity and functionality of electrical systems.
Thermal Stability
Importance in High-Temperature Environments
In high-temperature settings, the grease needs to maintain its integrity and not break down under stress. Thermal stability is crucial because excessive heat can alter the grease's physical and chemical properties, leading to diminished effectiveness. Maintaining the grease's viscoelastic characteristics ensures that it continues to lubricate and protect electrical connections without becoming brittle. For example, a grease designed for automotive applications must withstand temperatures that can soar in engine compartments, ensuring that it continues to function effectively over prolonged periods.
The unique feature here is that reliable thermal stability not only aids in performance but also reduces maintenance needs over time, making it a popular choice for various electrical applications.
Measuring Thermal Properties
Understanding thermal properties allows for improved selection processes regarding grease. The measurement typically includes thermal conductivity, which assesses how well heat passes through the material. This characteristic is vital since it highlights how efficiently a grease can dissipate heat from critical electrical connections.
Measuring instruments like differential scanning calorimetry can help provide insights. The advantage here is that you can make an informed choice based on empirical data instead of intuition or guesswork. Observing these properties can dictate whether a grease is suitable for applications subject to frequent temperature changes, ensuring ongoing performance reliability.
Moisture Resistance
Impact of Humidity on Electrical Connections
Humidity can wreak havoc on electrical systems, leading to increased resistance and possible failure of components. The impact of moisture involves corrosion and the formation of unwanted conductive paths which can cause short circuits or malfunctions. Greases with moisture-resistant properties can combat this by providing a seal that repels water and maintains integrity, ultimately prolonging the life of electrical connections.
The key characteristic to note is the ability to withstand moisture without losing its protective functions. With the right grease, even in damp environments, the risk of corrosion is significantly reduced, making it a beneficial solution in many electrical conduits.
How Grease Provides Protection
Ultimately, grease acts as a barrier to moisture infiltration through its chemical makeup. Certain greases contain hydrophobic agents that prevent water from breaching electrical connections. This unique feature enhances reliability in environments with fluctuating humidity levels, proving advantageous in both outdoor and indoor applications.
Moreover, selecting a product with strong moisture resistance contributes to minimizing long-term failures. By understanding how grease protects against humidity, users can feel confident in their choice even in adverse weather conditions.
Chemical Resistance
Interaction with Various Chemicals
Electrical environments can be plagued with exposure to chemical substances, whether from the products used during installation or natural elements around them. Understanding how grease interacts with these chemicals is essential in maintaining its protective capabilities. Certain chemical compounds can break down or alter the formulation of the grease, compromising its effectiveness.
Knowing the ingredient compatibility ensures that the longevity of both grease and electrical components is maintained without unexpected failures. Greases formulated specifically to resist chemical interaction not only give you peace of mind but also enhance overall safety in installation.
Selecting for Specific Environments
When you know where a product will be applied, you can select grease meant to endure those specific challenges. Some environments, like coastal areas, may require grease that’s saltwater resistant, while others near industrial chemicals might need specialized formulations. This selective approach makes the choice to use chemical-resistant grease a key factor in ensuring the durability of connected systems. By assessing the specific environmental conditions, you greatly reduce the risk of premature failures and costs related to replacements or repairs.
Understanding and appreciating the role of these properties in electrical grease assists in making informed decisions that ensure reliable and long-lasting electrical connections. Their importance cannot be overstated, as they form the backbone of effective maintenance strategies in electrical applications.
Application Techniques for Electrical Grease
Applying grease to electrical connections isn’t just a matter of slapping some product on and calling it a day. It’s a delicate dance that requires careful planning and execution. Proper techniques significantly impact the performance and longevity of electrical connections, ensuring that they remain functional and safe over time. Understanding the nuances of application can mean the difference between a reliable circuit and one fraught with issues. Let’s dive into the finer details of this crucial process.
Surface Preparation
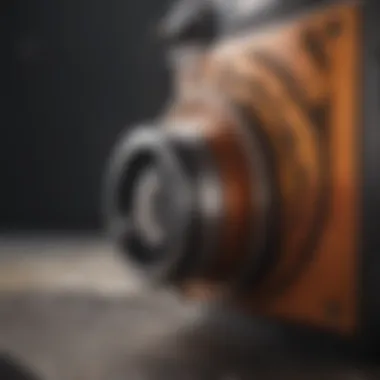
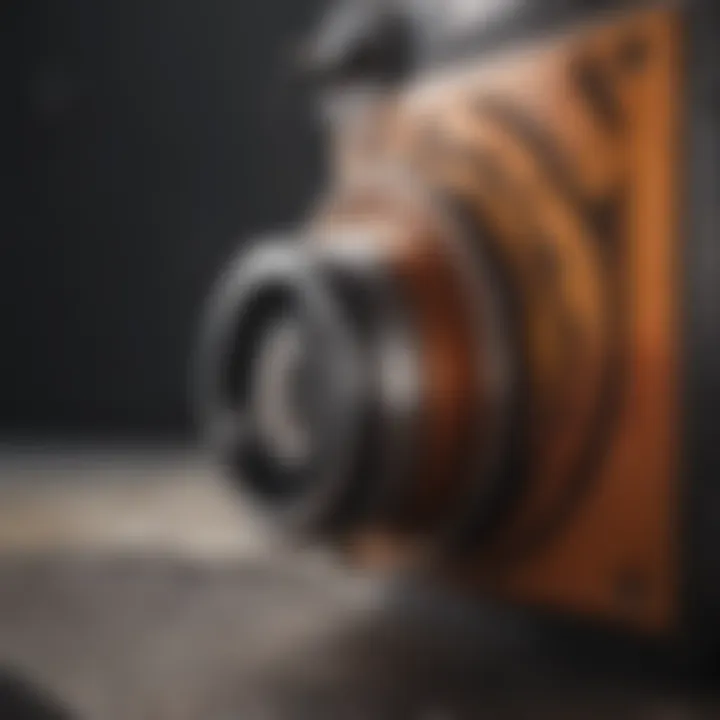
Cleaning Techniques
Before grease meets the metal, the surfaces need a proper cleaning. Dust, grime, and oxidation can wreak havoc on electrical connections. Cleaning techniques may involve using isopropyl alcohol or a specialized electrical contact cleaner to ensure a pristine surface. This meticulous approach is beneficial because it eliminates potential roadblocks to effective conductivity. Moreover, using lint-free cloths or brushes minimizes the risk of leaving behind possible contaminants.
A unique feature of these cleaning methods is their ability to interact with residue, facilitating a better bond with the grease. That’s why choosing the right cleaner is crucial. A disadvantage, however, could be the need for meticulous application, as careless cleaning might lead to scratches that can compromise future conductivity.
Ensuring Optimal Contact
Now that the surface is squeaky clean, ensuring optimal contact takes center stage. This means aligning and pressing the electrical components properly, reducing gaps that might inhibit performance. A well-aligned connection allows the grease to distribute evenly, enhancing electrical flow.
The key characteristic here is mechanical integrity. Optimal contact ensures that the grease forms a thin, even layer rather than clumping, which can obstruct electrical pathways. On the downside, achieving perfect contact sometimes requires a touch of finesse and additional tools, which might intimidate novices in the DIY community.
Application Methods
Choosing the Right Tools
Selecting the right tools for grease application plays a pivotal role in the process. Brushes, applicators, or even syringes can facilitate precisely controlled application to each connection point. For instance, a syringe allows for accuracy while minimizing mess.
The unique advantage of precision tools is that they help maintain the right amount of grease, avoiding excess that can attract dirt or moisture later on. However, the downside is the need for additional investment in various tools, which may deter some individuals from proceeding with their projects.
Techniques for Even Distribution
Once grease is on the scene, applying it evenly across the surface is essential. Techniques may vary—a gentle circular motion can often do the trick. The objective here is to create a consistent layer that doesn’t lead to buildups or gaps.
A vital characteristic of even distribution is its role in ensuring lifespan and effectiveness. An even layer minimizes the risk of corrosion and electrical arcing, leading to improved connection performance. One drawback is that it can be time-consuming, especially if there are multiple points to cover, but it’s a worthy investment in the long run.
Post-Application Inspection
Verifying Proper Coverage
After the grease has been applied, the next step involves verifying that every part has been adequately covered. This inspection is crucial, as any missed spots can become corrosion hotspots or failure points in the future. Users can perform a simple visual assessment or utilize diagnostic tools to check conductivity in key areas.
The standout feature of verifying coverage is that it can save significant headaches down the line. A thorough inspection helps identify issues before they escalate, ensuring longevity and safety in operations. The trade-off? This takes additional time and effort, but it’s about doing it right.
Identifying Application Errors
Even the best efforts can lead to mistakes. Finding application errors—like applying too little or too much grease—can drastically alter performance in undesirable ways. Common signs of application issues include reduced conductivity or increased heating during operation.
The integral aspect of identifying errors is that it paves the way for solutions. Early detection can lead to corrective action before problems arise. Although it can be a hassle to rectify mistakes after application, knowing how to identify them strengthens future application techniques.
Assessing Grease Performance
Evaluating the performance of grease used in electrical connections can feel a bit like trying to find a needle in a haystack—it's crucial but often overlooked. When it comes to making sure that electrical parts are functioning seamlessly, grease performance is right up there in importance. Grease not only facilitates smooth operation but also contributes to the longevity of connections, thereby minimizing potential maintenance costs. In this section, we explore various testing methods that help gauge grease effectiveness in terms of conductivity, resistance to corrosion, and durability under various conditions.
Conductivity Tests
Conductivity is paramount in the world of electrical connections. Testing grease for conductivity ensures that electric current can flow efficiently through the links without significant energy loss. A poor-performing grease here can lead to increased resistance, generating heat and potentially causing failure in the circuit.
There are different methods to assess conductivity. One popular method involves using a conductivity meter to measure the grease's ability to conduct electric current. By evaluating the resistance encountered as current passes through the grease, one can determine if the chosen product meets the required standards for application.
Furthermore, a grease that showcases high conductivity becomes the front runner for high-load or high-frequency environments, making the selection process that much clearer.
Corrosion Resistance Testing
Corrosion is the slow, unsuspecting enemy of electrical connections. An effective grease should have robust resistance against corrosion, especially when faced with moisture or salty environments that typically accelerate the degradation process. Conducting corrosion resistance tests involves subjecting grease samples to environments where corrosive agents are present, and then evaluating how well the grease protects the metal surfaces.
One common approach is the salt spray test, which simulates coastal or high-humidity conditions. Greases that excel in these tests exhibit remarkable longevity and reliability as they ward off rust and other types of degradation, making them suitable for both indoor and outdoor applications.
Long-Term Durability Studies
Long-term durability studies focus on how grease performs under extended exposure to various environmental conditions and mechanical stress. This is critical because it reflects the real-world use of electrical systems.
Factors Influencing Longevity
When discussing factors that contribute to longevity, one must consider thermal stability as a key characteristic. Grease that performs well under high temperatures prevents it from breaking down, ensuring continuous protection. Moreover, resistance to moisture and chemical exposure plays a vital role. A grease that maintains its properties after being subjected to these stressors is undoubtedly a beneficial choice.
Interestingly, some greases include additives to enhance durability. These additives can shield against oxidation or provide additional lubrication, which is an added bonus when it comes to extending the life of electrical components.
Case Studies
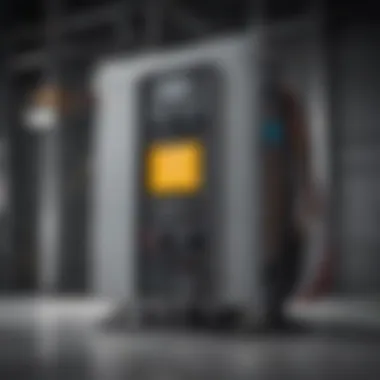
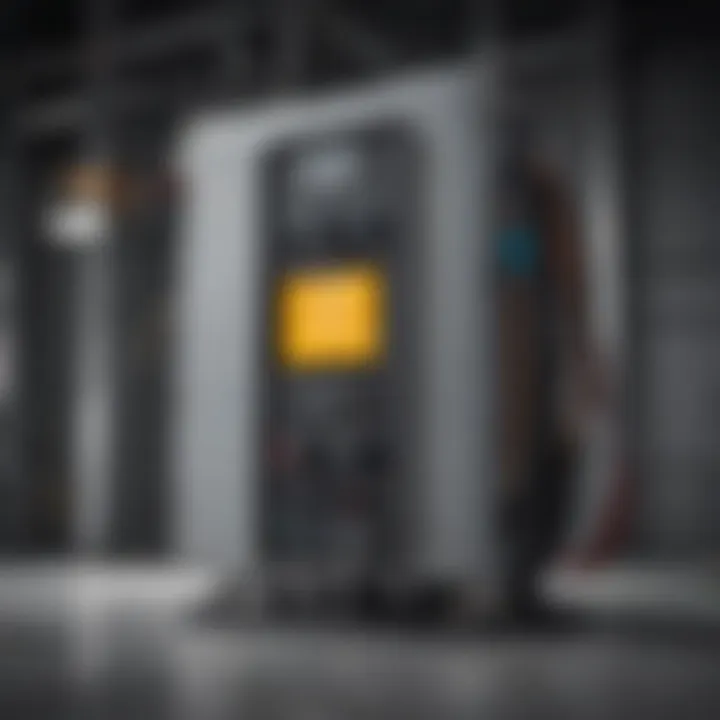
Case studies provide practical insights into how grease performs in the field over time. They often reveal real-world scenarios where specific greases were applied and the resulting operational outcomes. For instance, certain marine applications have documented significant improvements in connection reliability when using specially formulated greases designed for salty conditions.
The unique feature of these case studies lies in their ability to showcase how environmental factors distinctly affect grease performance. Continuous evaluation through such studies allows manufacturers to innovate and improve the formulation of electrical greases, thus ensuring higher standards of reliability.
"Investing time in assessing grease performance can lead to safer, more efficient electrical systems, ultimately avoiding costly repairs."
Environmental Considerations
In today’s world, concern for the environment has become essential, even in fields that may seem distant from environmental impacts, like electrical systems. Electrical connections, due to their crucial nature, often require maintenance with various grease types. However, the choice of grease can significantly affect our surroundings. Understanding environmental considerations helps not only in reducing harm but also in promoting sustainability within electrical practices.
Eco-Friendly Alternatives
Impact on Sustainability
When we talk about sustainability in the context of electrical grease, we refer to methods, products, and processes that minimize environmental harm. Eco-friendly grease, which may be biodegradable or derived from renewable sources, contributes positively by significantly reducing the risk of pollution. This is especially beneficial for homeowners and electricians who perform regular maintenance.
One key characteristic of sustainable grease options is their ability to degrade naturally over time, unlike traditional petrochemical products that can linger in the environment for years. This not only helps in preserving soil and water quality but also mitigates adverse effects on local flora and fauna.
Eco-friendly alternatives often come without harmful VOCs (volatile organic compounds), boasting health advantages for users who might otherwise come into contact with hazardous materials. Nevertheless, potential drawbacks include possible costs that could be higher than conventional greases; however, the long-term environmental benefits tend to outweigh the upfront expenses.
Market Options
The market is evolving, with an increasing number of retailers offering eco-friendly greases. Brands like Permatex, with their Bio-Based Dielectric Grease, provide effective conductivity while being kind to the environment. This option exemplifies a beneficial balance between performance and ecological responsibility, making it a popular choice among consumers.
A unique feature of modern market options is their growing formulation based on vegetable oils or other natural ingredients. Such formulations not only enable effective lubrication but also cater to a burgeoning awareness among consumers regarding sustainable practices.
As the landscape of electrical grease continues to change, it’s crucial to evaluate these options carefully and discern which ones align with environmental goals while still meeting electrical performance needs.
Disposal Guidelines
Proper disposal of electrical grease is vital to prevent environmental harm. Many household products fall under waste categories that require specific handling to avoid contaminating landfills or waterways. Understanding disposal guidelines ensures that we do our part in maintaining a cleaner planet.
Best Practices
Employing best practices involves knowing how to dispose of used greases correctly. For many eco-friendly alternatives, they may often be biodegradable, which allows for fewer restrictions in disposal. However, it’s important to always check product labels for instructions.
A key characteristic is the emphasis on recycling or repurposing containers whenever possible. This not only reduces waste but also conserves resources needed to produce new containers. Furthermore, disposal should be done in compliance with local laws, often requiring grease to be taken to specified waste management facilities to minimize harm.
Local Regulations
Local regulations regarding disposal often vary widely. They set the framework for how hazardous materials, including certain types of grease, should be managed. These regulations help in creating uniform guidelines that all citizens can follow, promoting community health.
The strength of local regulations lies in their ability to keep hazardous waste out of landfills and waterways, thus protecting sensitive environments. It's important for individuals, especially housewives and homeowners, to familiarize themselves with these applicable laws to ensure compliance, as penalties for improper disposal might be stricter than one would expect.
Following these guidelines, adapting eco-friendly practices, and staying informed are paramount in fostering a sustainable future, one electrical connection at a time.
The End
The conclusion of this article underscores the vital role that choosing the correct grease for electrical connections plays in ensuring safety and efficiency. By synthesizing everything discussed earlier, we aim to leave readers with a clear understanding of what to prioritize when selecting their grease. This selection isn't merely about performance; it directly impacts the longevity of your electrical systems. In this guide, we've explored different types of grease —focusing on their distinct properties, applications, and performance assessments.
Summarizing Key Takeaways
One cannot overstate the significance of the right grease choice. Here are the key takeaways to remember:
- Understand the Purpose: Grease serves not just as a lubricant but protects against corrosion and improves conductivity.
- Types Matter: Conductive, dielectric, and silicone-based greases each have unique properties and specific applications. Understand which one suits your needs.
- Application Techniques: Preparation and application methods are just as important as the grease type. A clean surface ensures better adhesion and performance.
- Regular Assessments: Routine checks on grease performance can alert you to potential issues long before they become significant problems.
In summary, being well-informed will allow one to choose wisely, ensuring that your electrical connections remain in top shape.
Future Trends in Electrical Greases
As we look ahead, it’s crucial to keep an eye on how advancements can affect the selection of greases in electrical settings. Two trends are emerging that might reshape the landscape significantly.
Emerging Technologies
Emerging technologies are changing how materials work together in electrical systems, especially regarding grease. New formulations combine advanced materials that enhance properties like conductivity and temperature resistance. A key characteristic of these innovations is their ability to adapt to various conditions without compromising performance. For instance, some greases now include nano-particles that can further improve their thermal and electrical behavior.
Such technologies are becoming increasingly popular due to their longevity and effectiveness in diverse environments, allowing electrical connections to perform better under stress. While many of these products are still making their way into the market, their potential advantages are already evident, enticing users who want reliable performance in their electrical systems.
Shifts in Industry Standards
Another noteworthy trend is the shift in industry standards, reflecting a growing awareness of environmental issues and the safety of end-users. Regulatory bodies are tightening requirements around chemical compositions and safety arrangements. A key aspect of this shift is a more significant emphasis on using materials that are non-toxic and environmentally friendly. These evolving standards mean that manufacturers must innovate constantly, often leading to safer and more efficient products entering the market.
This shift is beneficial as it promotes more informed choices among consumers. Meanwhile, the unique features of these greases help in reducing hazards associated with electrical failures while enhancing performance. However, with these new standards, one must also keep an eye on the cost implications and availability, as some newer products may be pricier than traditional options.
In closing, understanding these trends can empower house owners and maintenance professionals to make better decisions that enhance both performance and sustainability in their electrical systems.