Mastering Workshop Compressor Performance: A Complete Guide for Efficiency
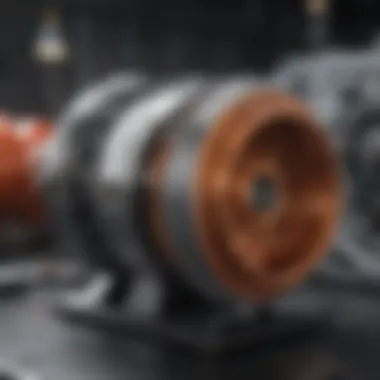
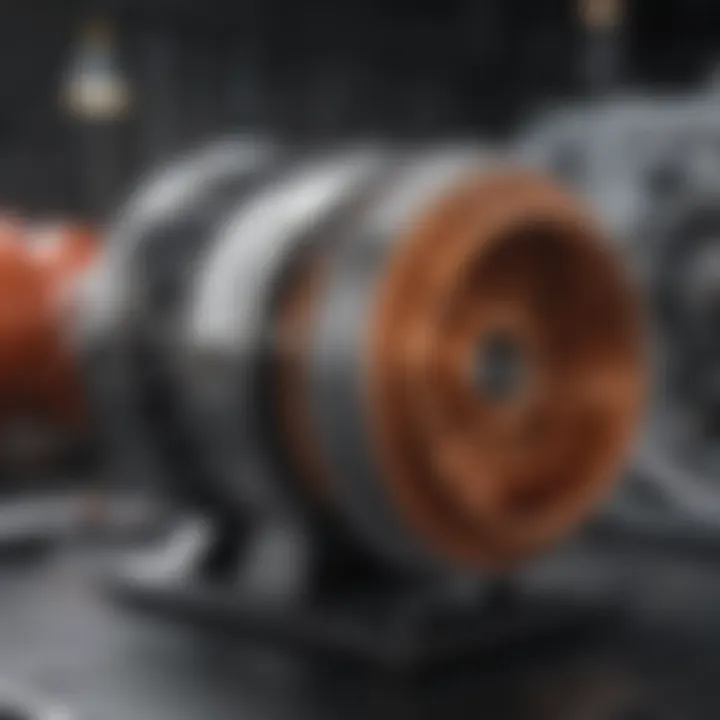
Overview of Workshop Compressor Performance
When delving into the realm of workshop compressors, one must first grasp the intricacies of these vital tools in the home improvement industry. Workshop compressors play a pivotal role in powering numerous pneumatic tools that aid in various tasks, such as painting, nailing, and inflating tires. Understanding the nuances of workshop compressors is crucial for efficient performance and optimal results.
It is imperative to note the significance of workshop compressor performance in enhancing productivity and precision in household tasks. A well-functioning compressor ensures seamless operation of pneumatic tools, leading to smoother and more efficient home improvement projects.
Common Challenges and Solutions
Homeowners often encounter common challenges when dealing with workshop compressors. Issues such as air leaks, insufficient pressure, and compressor overheating can hinder performance. However, solutions exist to mitigate these challenges and optimize compressor functionality.
To combat air leaks, homeowners can inspect and replace worn-out components such as seals and gaskets. Maintaining proper lubrication and cleaning air filters regularly can prevent overheating and ensure consistent pressure levels. Implementing a routine maintenance schedule is key to addressing these issues effectively and prolonging the lifespan of the compressor.
Product Recommendations
When seeking top-notch workshop compressors, considering renowned industry brands like [Industry Brand] is paramount. These brands offer a wide range of products known for their durability, efficiency, and advanced features that cater to diverse homeowner needs.
Top [Industry Brand] compressors boast innovative technologies such as auto startstop function, oil-free pumps, and portable designs for added convenience. These products excel in delivering high performance, low noise levels, and long-term reliability, making them ideal choices for optimizing workshop compressor performance.
Step-by-Step Guides
Enhancing workshop compressor performance requires a systematic approach to ensure seamless operation and longevity. Follow these practical steps to elevate your compressor efficiency:
- Regular Inspection: Check for air leaks, worn-out parts, and clean air filters periodically.
- Proper Lubrication: Lubricate moving parts as recommended by the manufacturer to prevent friction and overheating.
- Pressure Regulation: Monitor pressure levels using a gauge and adjust as needed for optimal tool performance.
- Maintenance Schedule: Establish a routine maintenance plan including oil changes, filter replacements, and overall system checks.
By adhering to these detailed instructions and implementing proactive measures, homeowners can enjoy the benefits of a well-optimized workshop compressor that facilitates seamless operation and enhances productivity in various home improvement tasks.
Introduction
In the realm of workshop functionality, one cannot underestimate the pivotal role that compressors play. These mechanical devices are the unsung heroes that power a plethora of tools and machinery in a workshop setting. From pneumatic drills to painting guns, compressors serve as the lifeblood, providing the necessary compressed air to make these tools operational. Understanding the nuances of workshop compressors is crucial for ensuring optimal performance and productivity in any workshop environment. This section will delve into the intricacies of workshop compressors, shedding light on their types and the significance they hold within workshop settings.
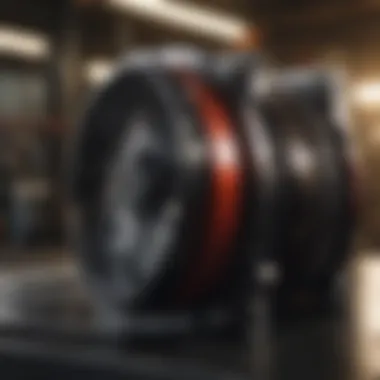
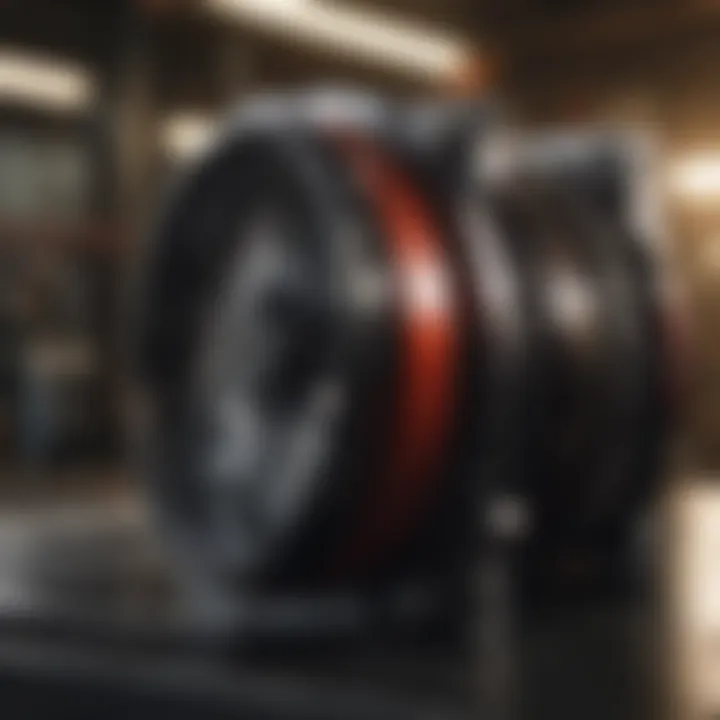
Understanding Workshop Compressors
Types of Workshop Compressors
When it comes to workshop compressors, there is a diverse range of options available, each tailored to specific needs and applications. Reciprocating, rotary screw, and centrifugal compressors are among the common types found in workshops, each with its unique characteristics and benefits. Reciprocating compressors, known for their simplicity and cost-effectiveness, are ideal for small to medium-sized workshops where intermittent use is prevalent. Rotary screw compressors, on the other hand, are more suitable for continuous operation, offering higher efficiency and smoother operation. Meanwhile, centrifugal compressors excel in large industrial setups where high volumes of compressed air are required. Understanding the strengths and limitations of each compressor type is essential for selecting the most suitable option for a workshop's specific requirements.
Importance of Compressors in Workshops
The importance of compressors in workshops cannot be overstated, as they serve as the heart of pneumatics-driven operations. Compressors enable the efficient powering of air tools, pneumatic machinery, and spray equipment, enhancing the speed and accuracy of various workshop tasks. With the ability to adjust pressure levels based on the tool being used, compressors offer versatility and precision in operation. Additionally, compressors contribute to a cleaner and safer working environment by eliminating the need for bulky and noisy electric motors commonly found in non-air-powered tools. Recognizing the pivotal role that compressors play in workshops underscores the need for proper maintenance and optimization to ensure seamless functionality and prolonged lifespan.
Essential Components:
Workshop compressors are intricate machines comprising various essential components that work together to ensure optimal performance. Understanding these components is crucial for maximizing the efficiency and durability of the compressor. Each part plays a vital role in the overall functionality and productivity of the workshop compressor system. From the air tank to the pressure switch, motor, and regulator, each component must be well-maintained and utilized effectively to achieve peak performance.
Key Parts of a Workshop Compressor:
Air Tank:
The air tank is a fundamental component of a workshop compressor, responsible for storing compressed air and maintaining a steady supply during operation. Its primary function is to store pressurized air, providing a reserve that allows the compressor to work efficiently without constant cycling. The air tank's size and material construction impact the compressor's performance, with larger tanks typically offering more significant air storage capacity and reducing cycle frequency. Additionally, the quality of the tank's construction influences its longevity and resistance to pressure variations, ensuring reliable operation over time. The air tank's insulation properties also affect its performance in different environmental conditions. Proper insulation helps prevent moisture buildup and corrosion within the tank, enhancing overall durability. However, inadequate insulation can lead to condensation issues and reduce the efficiency of the compressor system.
Pressure Switch:
The pressure switch is a critical component that regulates the compressor's operation by monitoring and controlling air pressure levels within the system. It acts as an automatic control device that turns the compressor on and off based on preset pressure settings, ensuring optimal performance and safety. The pressure switch plays a vital role in preventing excessive pressure build-up, which can lead to system malfunctions or damage. Its ability to maintain consistent pressure levels contributes to energy efficiency and prolongs the compressor's lifespan. The pressure switch's sensitivity and accuracy in detecting pressure variations are essential for maintaining a stable air supply. Adjustable pressure settings allow users to customize the compressor's operating range according to specific requirements, optimizing performance for varying workshop tasks.
Motor:
The motor is the powerhouse of the workshop compressor, driving the compression process to generate and deliver compressed air for various applications. Motors contribute significantly to the compressor's efficiency and performance, with different motor types offering varying power capacities and energy consumption levels. Electric motors are commonly used in workshop compressors for their reliability, consistent power output, and relatively low maintenance requirements. The motor's horsepower rating determines its capability to deliver compressed air at the specified pressure and flow rates. High-horsepower motors are suitable for powering heavy-duty compressors used in demanding workshop environments, providing the necessary strength to handle continuous operation and varied air tool requirements. Efficient motor operation is essential for achieving optimal compressor performance and meeting production targets.
Regulator:
The regulator is a crucial component that controls the air pressure exiting the compressor, ensuring consistency and precision in air delivery to connected tools and equipment. It regulates the output pressure based on the user-defined settings, enabling fine-tuning of air supply for different tasks. The regulator's ability to maintain a constant pressure level enhances tool performance, accuracy, and overall efficiency in workshop operations. Regulators come in various types, including basic single-stage regulators and advanced precision regulators with adjustable pressure ranges. Choosing the right regulator for the workshop compressor depends on the application requirements and desired air pressure control precision. Well-calibrated regulators help prevent air pressure fluctuations, leaks, and tool damage, maintaining a controlled working environment and improving overall productivity.
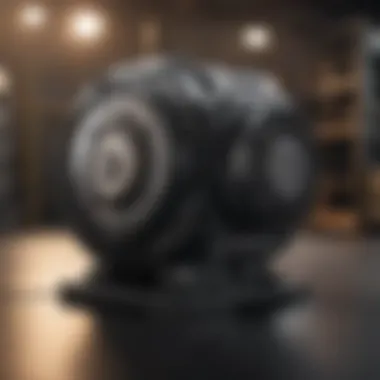
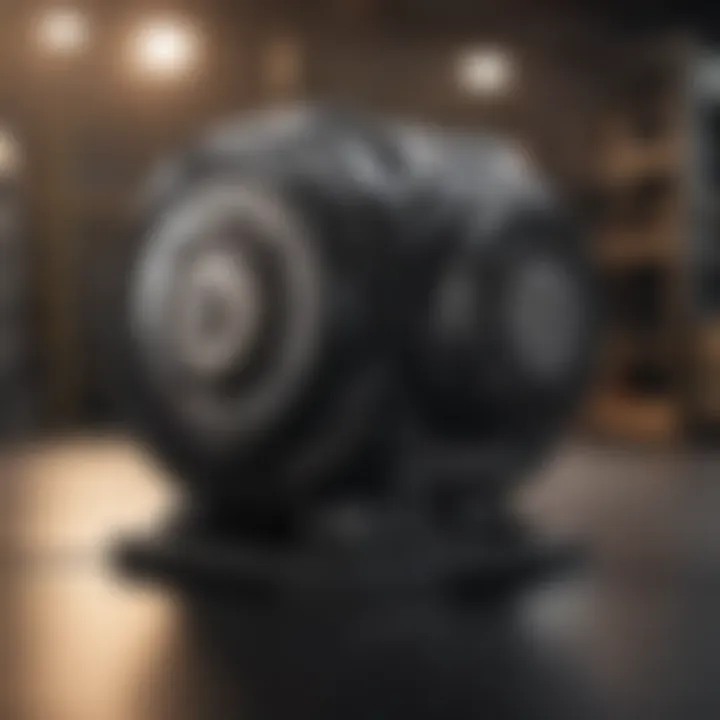
Maintenance Practices
In this article focused on optimizing workshop compressor performance, maintenance practices play a crucial role in ensuring the longevity and efficiency of the equipment. Regular maintenance not only extends the lifespan of the compressor but also enhances its performance capabilities. By prioritizing maintenance practices, workshop owners can prevent potential breakdowns, reduce operational costs, and maintain a safe working environment. By following a structured maintenance routine, workshop compressors can operate at peak efficiency, contributing to increased productivity and overall success.
Regular Inspections
Checking for Leaks
Checking for leaks is a critical aspect of compressor maintenance as it helps identify potential issues that can affect the equipment's efficiency. A thorough inspection of air lines, fittings, and connections can reveal hidden leaks that may lead to energy wastage and reduced performance. By detecting and rectifying leaks promptly, workshop owners can optimize the compressor's efficiency, prevent unnecessary wear and tear, and reduce energy consumption. Implementing a proactive approach to checking for leaks can result in significant cost savings and improved overall compressor performance.
Inspecting Filters
Inspecting filters is another essential maintenance task that contributes to the overall functionality of the compressor. Filters play a vital role in ensuring the quality of compressed air by trapping contaminants and debris. Regular inspection of filters helps prevent clogging, which can obstruct airflow and diminish the compressor's efficiency. By monitoring and replacing filters as needed, workshop owners can maintain optimal air quality, protect the compressor from damage, and prolong its operational life. Prioritizing filter maintenance is integral to ensuring consistent and reliable performance from the workshop compressor.
Cleaning Air Intake
Cleaning the air intake area is a key maintenance practice that promotes efficient compressor operation. The air intake system is responsible for drawing in clean air for compression, and any obstruction or contamination in this area can compromise performance. Regularly cleaning the air intake filters and ensuring the surrounding area is free from dust and debris can prevent overheating, reduce strain on the motor, and improve overall air quality. By incorporating air intake cleaning into the regular maintenance routine, workshop owners can optimize airflow, minimize the risk of equipment damage, and enhance the compressor's operational efficiency.
Optimization Techniques
In the realm of workshop compressors, optimization techniques play a pivotal role in ensuring seamless operation and enhanced performance. This section delves into various strategies and practices that can elevate the efficiency and functionality of workshop compressors to new heights. By implementing optimization techniques, users can not only improve the overall output of their compressors but also prolong their lifespan and reduce maintenance costs significantly.
Improving Efficiency
Proper Sizing of Tools
Proper sizing of tools is a critical aspect of optimizing workshop compressor performance. Ensuring that tools are adequately matched to the compressor's capacity is essential for maximizing efficiency and preventing undue strain on the system. By selecting tools that align with the compressor's output capability, users can avoid overworking the machine and achieve optimal results consistently. Proper sizing of tools also contributes to enhanced productivity and reduces the risk of breakdowns, making it a popular choice among workshop owners looking to optimize their compressor setup.
Optimal Pressure Settings
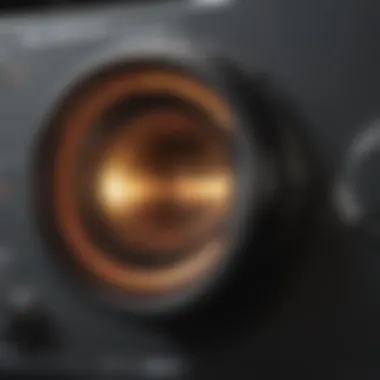
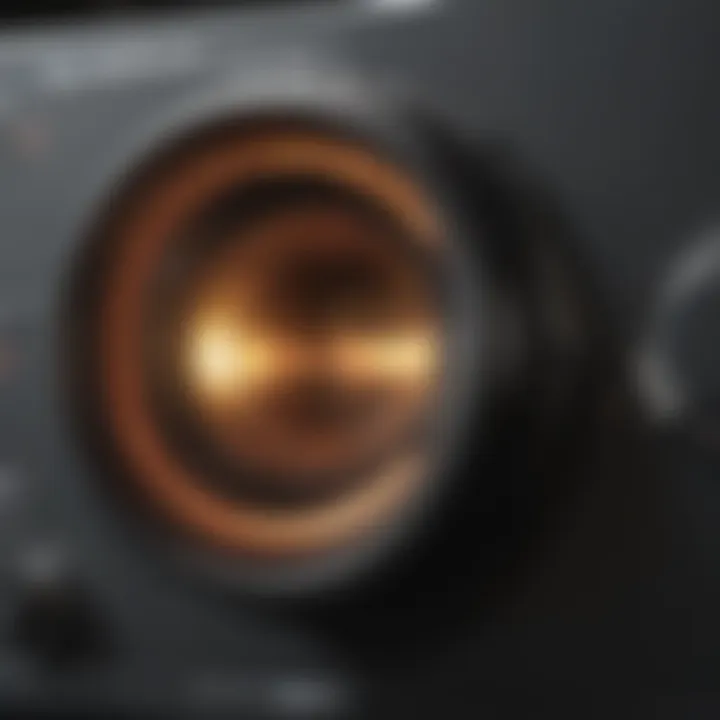
Setting the right pressure levels is paramount in ensuring the efficient operation of a workshop compressor. Optimal pressure settings not only promote better tool performance but also help conserve energy and extend the compressor's lifespan. By maintaining pressure within the recommended range, users can prevent unnecessary wear and tear on components, leading to improved longevity and reduced maintenance costs. Additionally, optimal pressure settings minimize the risk of leaks and pressure fluctuations, ensuring a steady and reliable air supply for various applications.
Regular Drainage of Moisture
Regular drainage of moisture is a crucial practice for preserving the integrity of a workshop compressor. Accumulated moisture within the system can lead to corrosion, air quality issues, and reduced efficiency. By implementing a routine drainage schedule, users can prevent moisture buildup, thereby safeguarding the compressor's components and maintaining optimal performance. Regular drainage not only improves durability but also enhances air quality and prolongs the life of tools connected to the compressor, making it a fundamental aspect of compressor optimization.
Enhancing Durability
Proper Lubrication
Proper lubrication is essential for enhancing the durability and performance of a workshop compressor. Adequate lubrication reduces friction between moving parts, minimizing wear and extending the lifespan of critical components. By using the right lubricants in the correct amounts, users can ensure smooth operation, reduce heat generation, and prevent premature equipment failure. Proper lubrication also helps maintain efficiency and reliability, making it a prudent choice for workshop owners seeking to optimize their compressor's longevity and overall performance.
Storage Practices
Effective storage practices are key to preserving the condition and functionality of a workshop compressor. Proper storage minimizes exposure to damaging elements, such as moisture and dust, which can compromise performance and durability over time. By storing the compressor in a clean, dry environment and following manufacturer recommendations, users can mitigate potential damage and maintain optimal operational efficiency. Good storage practices not only protect the compressor from external harm but also contribute to prolonged lifespan and consistent performance, highlighting their significance in enhancing the overall durability of workshop compressors.
Troubleshooting
In the realm of workshop compressors, troubleshooting plays a pivotal role in ensuring optimal performance. Constant vigilance and prompt problem-solving are essential to maintain the efficiency and longevity of these crucial tools. By addressing issues proactively, users can prevent more significant problems down the line, thereby saving time and money in the long run.
Common Issues and Solutions
Air Leakage
Air leakage is a common issue that can significantly impact the functionality of a workshop compressor. The key characteristic of air leakage is the gradual loss of compressed air due to leaks in the system. This can lead to inefficiencies in operation, increased energy consumption, and reduced overall performance. Addressing air leakage promptly is vital to maintain the effectiveness of the compressor. While air leakage can be a persistent challenge, regular maintenance and inspection can help identify and repair leaks before they escalate.
Overheating
Overheating is another prevalent issue encountered with workshop compressors. The primary characteristic of overheating is the excessive rise in temperature during compressor operation. This can be caused by factors such as inadequate ventilation, overuse, or malfunctioning components. Overheating not only hampers the performance of the compressor but also poses a safety risk. It is crucial to address overheating promptly by allowing the compressor to cool down, ensuring proper ventilation, and conducting regular maintenance to prevent overheating issues from recurring.
Irregular Pressure
Irregular pressure in workshop compressors can pose significant challenges to their functionality. The key characteristic of irregular pressure is fluctuations in the output pressure, leading to inconsistencies in air supply. This can impact the operation of pneumatic tools and equipment, affecting work quality and efficiency. To address irregular pressure, users need to calibrate the pressure settings accurately, inspect the regulator for any issues, and ensure proper maintenance of the compressor system. By maintaining consistent pressure levels, users can optimize the performance of their workshop compressors and enhance overall productivity.
Conclusion
Workshop compressors play a crucial role in enhancing the efficiency and productivity of a workshop environment. In this comprehensive guide on 'Optimizing Workshop Compressor Performance,' we have delved deep into the intricacies of workshop compressors to equip our readers with essential knowledge and techniques to maximize the functionality of these vital tools. Throughout this guide, we have explored key components, maintenance practices, optimization techniques, and troubleshooting solutions to ensure that workshop compressors operate at peak performance levels. By understanding the types and importance of workshop compressors, identifying key components like the air tank, pressure switch, motor, and regulator, implementing regular maintenance practices such as inspections and cleaning, and optimizing efficiency through proper sizing of tools, optimal pressure settings, and drainage of moisture, readers can significantly enhance the durability and functionality of their compressors. Moreover, the troubleshooting section provides insights into common issues like air leakage, overheating, and irregular pressure, offering practical solutions to rectify these problems efficiently. By paying attention to these details and implementing the strategies outlined in this guide, workshop owners and users can enjoy maximized compressor efficiency, reduced downtime, and enhanced overall workshop productivity.