Exploring the Intricacies of Forney Cut Off Wheels for Optimal Performance
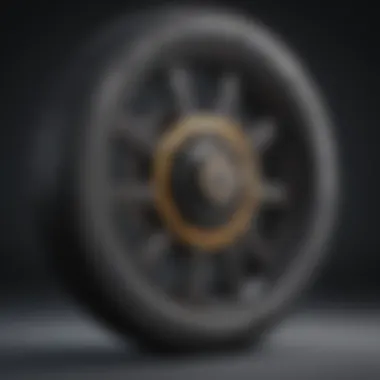

Overview of Topic
In the realm of the home improvement industry, Forney cut off wheels stand out as essential tools for various cutting tasks. These specialized wheels are crafted from high-quality materials, designed to deliver precise and efficient cutting results. The importance of utilizing the right cut off wheels cannot be overstated, as they play a critical role in shaping and refining materials for countless projects.
Common Challenges and Solutions
When it comes to using Forney cut off wheels, homeowners may encounter common challenges such as blade wear, inadequate performance on certain materials, and safety concerns. To address these issues, it is vital to follow proper usage guidelines, regularly inspect the condition of the wheels, and ensure they are compatible with the materials being cut. By investing in quality wheels and adopting appropriate safety measures, these challenges can be effectively mitigated.
Product Recommendations
For those seeking top-notch cut off wheels within the industry, Forney offers a range of premium products known for their durability and cutting precision. These wheels are designed to withstand the rigors of various cutting applications, providing smooth and accurate results. The benefits of Forney cut off wheels include long-lasting performance, exceptional cutting speed, and compatibility with a wide range of materials, making them a reliable choice for homeowners and professionals alike.
Step-by-Step Guides
To optimize the use of Forney cut off wheels, it is essential to follow a systematic approach. Begin by selecting the appropriate wheel for the material being cut, ensuring it is securely attached to the tool. Adjust the cutting speed and pressure according to the task at hand, allowing the wheel to work efficiently without overheating. Additionally, proper storage and maintenance of the wheels after use are crucial to prolong their lifespan and maintain cutting performance.
With a keen focus on precision and efficiency, Forney cut off wheels offer homeowners the versatility and reliability needed to accomplish a wide range of cutting tasks with ease. By understanding the nuances of these cutting tools and implementing best practices in their usage, homeowners can elevate their DIY projects to a new level of excellence.
Introduction
Forney cut off wheels are a crucial component in various industries, offering precise cutting capabilities and versatility. This article delves into the intricacies of Forney cut off wheels, providing a detailed exploration of their composition, applications, key features, and maintenance guidelines. By understanding the nuances of these cutting tools, housewives and homeowners can enhance their efficiency and optimize their performance for a wide range of tasks.
Overview of Forney Cut Off Wheels
Composition of Forney Cut Off Wheels
The composition of Forney cut off wheels plays a crucial role in their performance and durability. These wheels are typically crafted from high-quality abrasive materials, such as aluminum oxide or silicon carbide, blended with a bonding agent to enhance their strength and cutting precision. This composition ensures that Forney cut off wheels can withstand the rigors of heavy-duty cutting tasks while maintaining sharpness and efficiency throughout their lifespan.
Importance of Selecting the Right Wheel for the Task
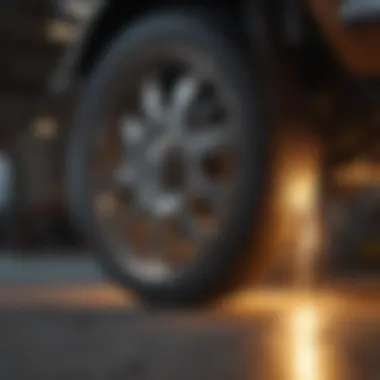

Choosing the correct type of Forney cut off wheel for a specific task is essential for achieving optimal results. Different wheels are designed for varying materials and applications, such as metalworking, masonry, or automotive repair. Selecting the right wheel based on factors like wheel diameter, thickness, and abrasive material ensures efficient cutting, minimal wear, and increased safety during operation.
Key Features of Forney Cut Off Wheels
Forney cut off wheels boast several key features that set them apart in the realm of cutting tools. These wheels are known for their exceptional durability, precise cutting performance, and compatibility with a wide range of materials. Additionally, they are designed to reduce heat build-up during operation, prolonging the wheel's lifespan and enhancing cutting efficiency.
Applications of Forney Cut Off Wheels
Metalworking Applications
Forney cut off wheels excel in metalworking applications, offering precise cutting of various metals with minimal heat generation. Whether cutting steel, aluminum, or other metals, these wheels provide clean cuts and high precision, making them indispensable tools in metal fabrication and welding processes.
Masonry and Concrete Cutting
In masonry and concrete cutting tasks, Forney cut off wheels showcase their versatility and efficiency. These wheels can effortlessly slice through concrete, brick, and stone, delivering smooth cuts and precise shapes for construction and renovation projects. Their durable composition and sharp cutting edges make them ideal for heavy-duty masonry applications.
Automotive Repair Tasks
For automotive repair tasks, Forney cut off wheels prove to be invaluable assets, enabling precision cutting of metal components, exhaust pipes, and body panels. Whether working on engine repairs, exhaust system modifications, or bodywork, these wheels offer superior cutting performance and accuracy, enhancing the efficiency of automotive maintenance tasks.
Significance of Cut Off Wheels in Various Industries
Manufacturing Sector
In the manufacturing sector, Forney cut off wheels play a vital role in enhancing productivity and precision in metal fabrication processes. These wheels enable manufacturers to achieve intricate cuts, shaping, and finishing of metal components with ease, thereby contributing to the overall efficiency and quality of production.
Construction Industry
Within the construction industry, Forney cut off wheels are indispensable tools for cutting and shaping materials like concrete, tiles, and bricks. Contractors and construction professionals rely on these wheels for their durability, precision, and versatility, allowing them to complete tasks such as tile installation, brick cutting, and concrete shaping with accuracy and efficiency.
Automotive Maintenance
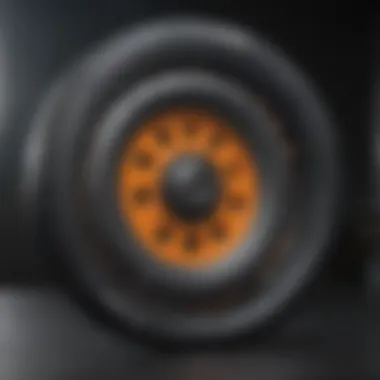

For automotive maintenance purposes, Forney cut off wheels offer unparalleled cutting precision and efficiency for repairing and modifying vehicle components. From cutting through metal parts to reshaping exhaust systems, these wheels provide mechanics and auto enthusiasts with the tools needed to perform detailed and accurate work on vehicles with ease.
Factors Influencing Performance
Factors influencing performance play a crucial role in optimizing the efficiency and effectiveness of Forney cut off wheels. Understanding these factors is essential for achieving superior results in various cutting tasks. By delving into the material composition, wheel diameter and thickness, operating speed, and pressure, users can make informed decisions to enhance cutting performance.
Material Composition and Density
Impact on cutting speed and precision
The material composition and density of Forney cut off wheels significantly impact cutting speed and precision. The quality and type of abrasive materials used in the wheels determine their ability to cut through different materials with varying levels of hardness and density. For instance, wheels with high-density abrasive materials are known for their exceptional cutting precision and speed, making them a popular choice for intricate cutting tasks. However, wheels with lower densities may excel in different applications due to their unique characteristics.
Distinguishing between abrasive materials
Distinguishing between abrasive materials is pivotal in maximizing the performance of Forney cut off wheels. Different abrasive materials offer distinct advantages and disadvantages based on their hardness, cutting efficiency, and durability. Understanding the specific properties of each abrasive material helps users select the most suitable option for a particular cutting task. It allows for precise control over the cutting process, resulting in clean and accurate cuts across various materials.
Wheel Diameter and Thickness
Effects on maneuverability and cutting depth
The wheel diameter and thickness directly impact maneuverability and cutting depth when using Forney cut off wheels. Larger diameter wheels provide enhanced maneuverability, allowing users to navigate through complex cuts with ease. Additionally, thicker wheels offer increased cutting depth, enabling users to work on thicker materials or achieve deeper cuts efficiently. Choosing the right combination of diameter and thickness is essential for optimizing cutting performance based on the specific requirements of each task.
Choosing the optimal specifications
Selecting the optimal specifications for wheel diameter and thickness is a critical aspect of maximizing the benefits of Forney cut off wheels. Users must consider the material being cut, the depth of the cut required, and the maneuverability needed to accomplish the task efficiently. By choosing the right specifications, users can ensure smooth cutting operation, precise results, and extended wheel longevity.
Operating Speed and Pressure
Ideal RPM for different materials
Determining the ideal revolutions per minute (RPM) for different materials is paramount for achieving optimal cutting results with Forney wheels. The RPM setting affects the wheel's cutting efficiency, heat generation, and overall performance. By matching the RPM to the material being cut, users can prevent overheating, reduce wear on the wheel, and ensure consistent cutting accuracy across various applications.
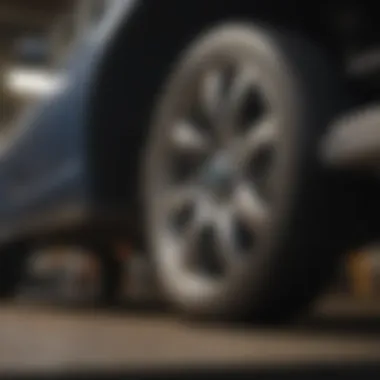

Maintaining consistent pressure for efficiency
Maintaining consistent pressure while operating Forney cut off wheels is essential for maximizing cutting efficiency. By applying uniform pressure during cutting tasks, users can prevent wheel wear, minimize tool vibration, and enhance cutting precision. Consistent pressure also promotes safety and prolongs the life of the cutting wheel by ensuring even distribution of force during operation.
Maintenance and Safety Guidelines
In this detailed examination of Forney Cut Off Wheels, the section on Maintenance and Safety Guidelines plays a crucial role in ensuring optimal performance and safety standards. Addressing this topic provides readers with essential insights into preserving the longevity of their tools and safeguarding against potential risks.
Proper Handling and Storage
Storage conditions to prevent damage
Exploring the specific aspect of Storage conditions to prevent damage sheds light on the significance of proper tool storage. This includes factors such as humidity levels, temperature control, and protection from external elements. Emphasizing the ideal storage conditions enhances the durability and functionality of Forney Cut Off Wheels. By storing the wheels in a dry and cool environment, users can prevent corrosion and maintain cutting precision. The unique feature of specialized containers or racks for storage ensures easy access and minimizes the risk of damage during handling.
Guidelines for safe transportation
Guidelines for safe transportation are essential to maintain the integrity of the cut off wheels during transit. This aspect outlines best practices for packaging and moving the wheels without compromising their structural integrity. Highlighting features such as secure packaging, shock absorption materials, and proper handling techniques, these guidelines promote safe and damage-free transportation. Providing clear instructions on securing the wheels in transit containers or boxes reduces the likelihood of breakage or deformation. The advantages of following these guidelines include minimizing potential accidents and ensuring the wheels arrive at their destination in optimal condition.
Regular Inspection and Cleaning
Checking for wear and tear
Regularly inspecting Forney Cut Off Wheels for wear and tear is a critical maintenance task to uphold their performance standards. This involves assessing factors like abrasive wear, uneven surfaces, or any signs of damage that may affect cutting efficiency. By checking for wear and tear, users can identify when the wheels need replacement, ensuring continuous precision in cutting operations. The unique feature of monitoring wear patterns and deviations enables timely action to prevent operational disruptions and maintain consistent cutting quality.
Removing debris for optimal performance
Removing debris from Forney Cut Off Wheels is essential for ensuring optimal performance and longevity. Accumulated debris can hinder cutting efficiency and compromise the wheel's structural integrity. By cleaning the wheels regularly, users can prevent clogging, overheating, and premature wear. The unique feature of specialized cleaning tools or techniques facilitates thorough debris removal without causing damage to the wheel surface. This proactive approach enhances cutting accuracy and prolongs the lifespan of the wheels.
Safety Precautions during Operation
Wearing appropriate protective gear
One of the paramount safety precautions during operation is wearing suitable protective gear to prevent injuries. This includes items such as safety goggles, gloves, and face shields to shield against flying debris and potential hazards. The key characteristic of prioritizing protective gear underscores the importance of personal safety in high-speed cutting tasks. By wearing appropriate gear, operators minimize the risk of eye injuries, skin abrasions, and other safety hazards. The unique feature of adjustable and ergonomic protective gear ensures comfort and compliance with safety regulations.
Following best practices for injury prevention
Following best practices for injury prevention is a proactive measure to maintain a safe working environment when using Forney Cut Off Wheels. This approach involves adhering to operational guidelines, maintaining focus during tasks, and avoiding risky behaviors that could lead to accidents. Highlighting the importance of following best practices empowers users to mitigate potential risks and handle the tools responsibly. By adopting these practices, individuals contribute to creating a secure cutting environment and safeguarding against unforeseen accidents. The advantages of consistent injury prevention practices include reducing downtime due to injuries and promoting a culture of safety consciousness among users.