A Comprehensive Guide to Choosing the Best Screws for Hardwood Projects
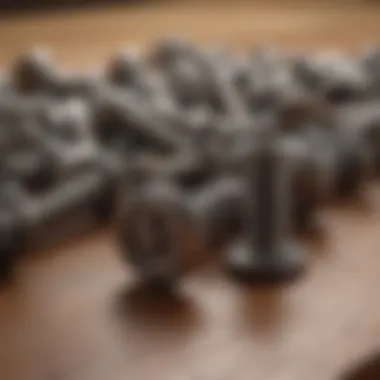
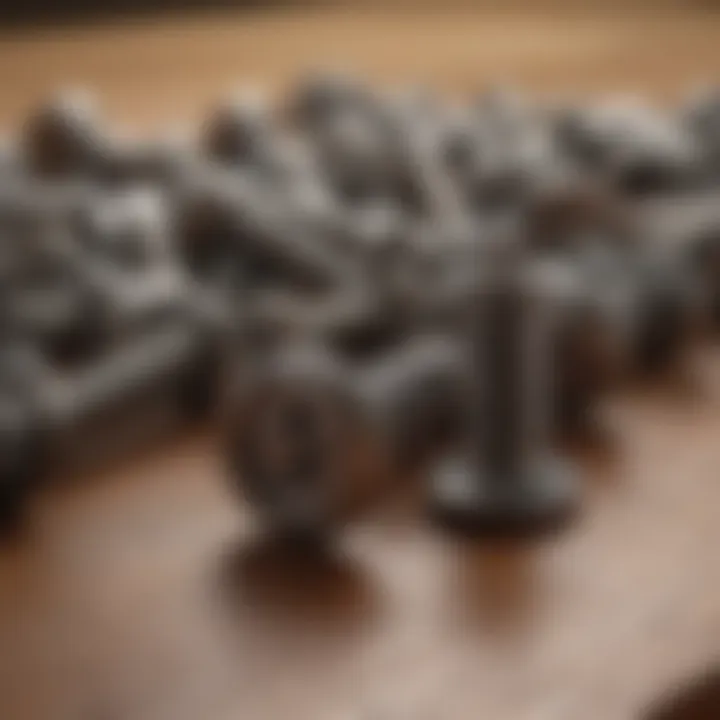
Overview of Topic
In the intricate realm of the home improvement industry, selecting the ideal screws for hardwood stands as a crucial element in ensuring the durability and precision of woodworking projects. When delving into the intricacies of woodworking, the choice of screws plays a pivotal role in determining the structural integrity and aesthetic appeal of the final product. Understanding the composition and characteristics of hardwood is essential in comprehending the significance of choosing the right screws for optimal results.
Common Challenges and Solutions
Homeowners often encounter a myriad of challenges when it comes to fastening hardwood, ranging from splitting to inadequate holding power. To combat these issues, it is imperative to pre-drill pilot holes to prevent splitting and utilize screws with sharp threads for enhanced grip. Additionally, opting for screws specifically designed for hardwood can mitigate issues related to stripping or snapping during installation.
Product Recommendations
When it comes to top-notch products in the home improvement industry, [Industry Brand] stands out for its quality and reliability. Their range of hardwood screws offers a perfect blend of strength and versatility, ensuring secure fastening without compromising the wood fibers. The benefits of [Industry Brand] screws include corrosion resistance, high tensile strength, and various sizes to cater to different woodworking needs.
Step-by-Step Guides
- Start Planning: Begin by assessing the woodworking project and determining the type of hardwood being used. Understand the load-bearing requirements and aesthetic preferences to select the appropriate screw type, size, and material.
- Choosing the Right Screws: Once the project specifications are established, choose screws designed specifically for hardwood applications. Consider factors such as length, diameter, head type, and drive style to ensure optimal performance.
- Preparation and Pre-Drilling: Prior to screw installation, prepare the hardwood surface by pre-drilling pilot holes to prevent splitting. Use a countersink bit to create a recess for the screw head, allowing for a flush finish.
- Fastening the Screws: Carefully drive the screws into the pre-drilled holes using a screwdriver or power drill. Maintain consistent pressure to avoid over-tightening, which can lead to wood damage or thread stripping.
- Final Inspection and Enjoying the Result: Once all screws are securely fastened, inspect the project for any loose joints or misalignments. With the final product complete, revel in the satisfaction of a well-crafted woodworking endeavor.
Understanding Hardwood
In the realm of woodworking, understanding hardwood is paramount to ensure the success and longevity of any project. Hardwood, known for its durability and natural beauty, presents unique challenges and opportunities for craftsmen and DIY enthusiasts alike. By delving into the properties of hardwood, individuals gain a deeper insight into how different species of wood behave under various conditions, allowing for more informed decision-making throughout the woodworking process.
Properties of Hardwood
Density
Density serves as a critical factor when considering hardwood for projects. The density of hardwood directly impacts its strength and resilience, making it an ideal choice for structural components that require longevity and stability. Hardwoods with higher density levels, such as oak or maple, are sought after for their durability in withstanding heavy loads and wear and tear, ensuring the longevity of the final piece.
Grain Pattern
The unique grain patterns found in hardwoods contribute to their aesthetic appeal and individuality. The distinct swirls, knots, and lines in the grain pattern of hardwood not only add visual interest but also influence the wood's strength and stability in different directions. Understanding the grain pattern of specific hardwood species allows woodworkers to make informed decisions on how to cut and shape the wood to enhance both the structural integrity and visual appeal of their projects.
Durability
One of the most notable attributes of hardwood is its exceptional durability. Hardwoods are renowned for their ability to withstand the test of time, making them a popular choice for high-traffic areas or furniture pieces that require longevity. Their natural resistance to wear, rot, and decay ensures that hardwood projects retain their beauty and functionality for years to come, making them a valuable investment in any woodworking endeavor.
Challenges of Working with Hardwood
Splitting
The propensity of hardwood to split during construction poses a common challenge for woodworkers. Due to the density and hardness of hardwood, improper drilling or fastening techniques can lead to unsightly splits in the wood, compromising the structural integrity of the project. Implementing proper pilot holes and utilizing the correct tools and techniques can mitigate the risk of splitting, ensuring a seamless woodworking experience.
Piloting Holes
Piloting holes in hardwood is crucial to prevent cracking and ensure a secure fastening. By creating pilot holes that accommodate the screw size and thread count, woodworkers can alleviate the stress on the wood, reducing the likelihood of splits or damage during assembly. Careful consideration of the pilot hole diameter and depth is essential in guaranteeing a smooth and successful fastening process for hardwood projects.
Strength Requirements
Hardwoods demand a higher level of strength and precision in fastening due to their dense composition. Meeting the strength requirements of hardwood projects necessitates selecting screws that can withstand heavy loads and resist withdrawal forces. Understanding the structural demands of the project and selecting screws with appropriate tensile strength and thread design is crucial in ensuring the longevity and stability of the final piece, minimizing the risk of failures or structural issues over time.
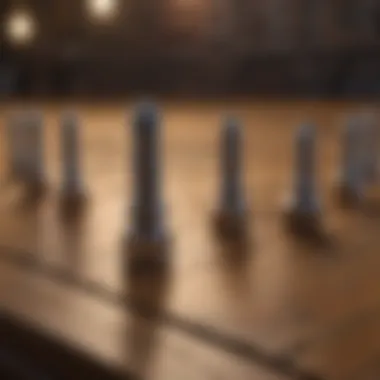
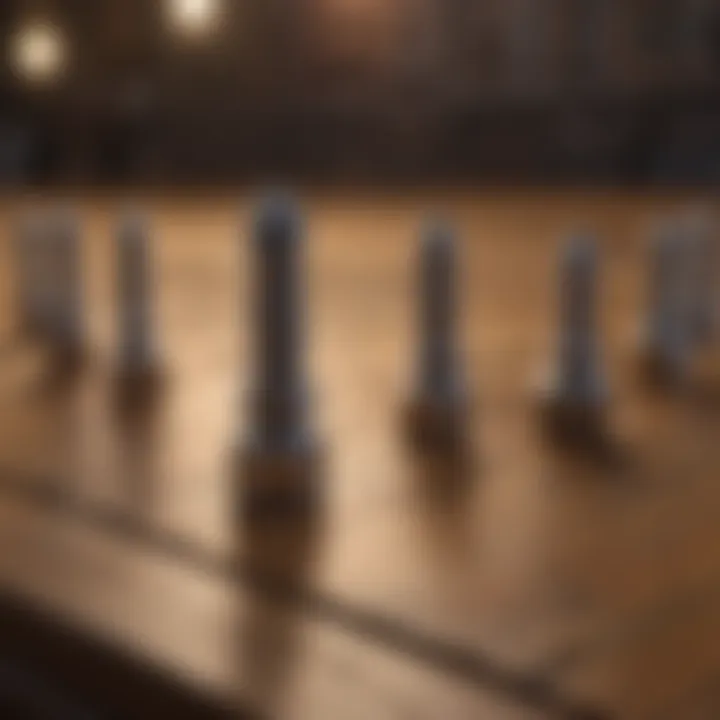
Factors Influencing Screw Selection
When delving into the world of hardwood screws, it is crucial to understand the pivotal role that factors influencing screw selection play in determining the success and durability of your woodworking projects. The choice of screws for hardwood goes beyond mere aesthetics; it directly impacts the structural integrity and longevity of your creations. Factors such as screw types, sizes, and materials all need to be carefully considered to ensure optimal performance and functionality in various woodworking applications.
Screw Types for Hardwood
Wood Screws
Wood screws, with their sharp threads and tapered ends, are specifically designed for hardwood applications. Their coarse threads provide excellent holding power in dense wood, ensuring a secure attachment. One key characteristic of wood screws is their self-drilling ability, which reduces the need for pre-drilling pilot holes in many cases. This feature makes wood screws a popular choice for their ease of use and efficiency in woodworking projects. While wood screws offer quick installation and strong holding power, it is essential to note that their coarse threads may cause splitting in certain hardwoods, requiring careful consideration during use.
Deck Screws
Deck screws are specially manufactured to withstand outdoor conditions, making them ideal for hardwood decks and outdoor furniture. Their corrosion-resistant properties, often with coatings like zinc or ceramic, ensure longevity and durability in exterior applications. The key characteristic of deck screws lies in their ability to resist rust and corrosion even in harsh environments, providing a reliable fastening solution for hardwood projects exposed to the elements. However, one potential disadvantage of deck screws is their higher cost compared to standard wood screws.
Cabinet Screws
Cabinet screws, with their thin shanks and large heads, are designed for cabinet installations in hardwood. Their sharp points and smooth shanks make them ideal for securely fastening cabinets without damaging the delicate wood fibers. The key characteristic of cabinet screws is their ability to sink flush into the wood surface, creating a seamless finish in cabinetry projects. While cabinet screws offer excellent holding power and a clean appearance, their higher cost relative to traditional wood screws may be a consideration for budget-conscious woodworkers.
Screw Sizes and Lengths
Gauge
The gauge of a screw refers to its diameter, with lower gauge numbers indicating thicker screws. In hardwood applications, choosing the correct gauge is crucial to ensure the screw provides adequate structural support without causing splits or damage to the wood. The key characteristic of gauge selection is to match the thickness of the wood being joined, allowing for optimal holding power and stability in the finished project.
Length
The length of a screw is determined by measuring from the head to the tip of the fastener. Selecting the appropriate screw length is essential for ensuring that the screw penetrates deep enough into the receiving surface to create a secure bond. The key characteristic of screw length is to consider the thickness of the materials being joined, allowing for ample penetration while avoiding protrusion that could cause splintering or aesthetic issues in hardwood projects.
Thread Count
Thread count refers to the number of threads per inch on a screw's shaft, influencing how quickly the screw drives into the wood and its overall holding strength. Higher thread counts provide greater holding power and faster installation but may also increase the risk of splitting in dense hardwoods. The key is to balance thread count with the wood's density and hardness to achieve optimal grip without compromising structural integrity.
Materials for Screws
Stainless Steel
Stainless steel screws offer excellent corrosion resistance, making them ideal for outdoor and marine applications where exposure to moisture is a concern. The key characteristic of stainless steel screws is their durability and strength, ensuring long-term performance in environments prone to rust and degradation. While stainless steel screws are slightly more expensive than traditional materials, their longevity and resistance to weathering make them a valuable investment in high-quality hardwood projects.
Brass
Brass screws are known for their aesthetic appeal and resistance to corrosion, particularly in decorative woodworking projects and antique restorations. The key characteristic of brass screws is their ability to blend seamlessly with hardwood surfaces, creating a visually pleasing finish that complements the natural beauty of the wood. However, brass screws are softer than steel counterparts, requiring careful installation to prevent stripping or damage to the screw heads.
Bronze
Bronze screws offer a combination of strength and corrosion resistance, making them suitable for both indoor and outdoor hardwood applications. The key characteristic of bronze screws is their versatility in various woodworking projects, from furniture assembly to architectural detailing. While bronze screws are a durable and reliable option, their higher cost compared to standard steel alternatives may be a consideration for budget-sensitive projects.
Best Practices for Screwing into Hardwood
When it comes to working with hardwood, following the best practices for screwing is paramount for achieving sturdy and durable connections in woodworking projects. Emphasizing key elements like pre-drilling holes, driving screws correctly, and adding finishing touches ensures the longevity and quality of your woodworking endeavors. Understanding the nuances of hardwood and the intricate nature of screw materials and sizes contributes significantly to the success of any project.
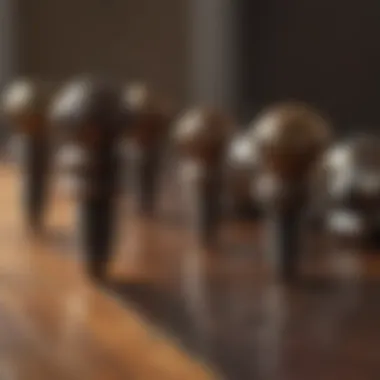
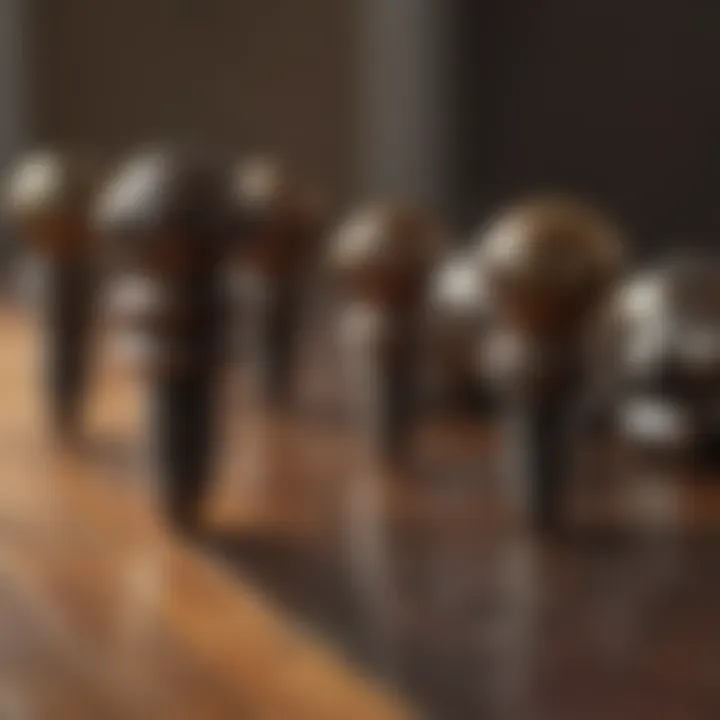
Pre-Drilling Holes
Importance of Pilot Holes
In woodworking, the importance of pilot holes cannot be overstated. Pilot holes serve as guides for screws, preventing hardwood from splitting and ensuring a snug fit. By creating pilot holes, you enhance precision, reduce the risk of damaging wood fibers, and facilitate smooth screw insertion, particularly crucial in dense hardwood varieties. Additionally, pilot holes aid in maintaining control over depth and angle, optimizing the overall integrity of your project.
Proper Drill Bit Selection
Selecting the appropriate drill bit for hardwood is essential for achieving precise pilot holes that accommodate screws seamlessly. The right drill bit ensures compatibility with screw sizes, mitigates the chances of wandering or skidding during drilling, and promotes clean and accurate hole formation in hardwood. By choosing a high-quality, sharp drill bit suited to the hardness of the wood, you enhance the efficiency and accuracy of your drilling process.
Depth Considerations
Considering the depth of pilot holes is critical for secure screw placement and stability. Judiciously determining the depth based on screw length and thickness of the material prevents over or under penetration, maintaining structural integrity and aesthetics. Careful planning and attention to detail in determining the depth of pilot holes contribute significantly to the overall success and reliability of your woodworking projects.
Driving Screws Correctly
Manual vs. Power Tools
Deciding between manual and power tools for driving screws depends on the project's scale, complexity, and personal preference. Manual tools offer control and precision, ideal for intricate work requiring finesse. In contrast, power tools expedite larger tasks, boosting efficiency and reducing manual effort. Understanding the benefits and limitations of each tool type is essential for selecting the appropriate method to ensure accurate and secure screw driving results.
Torque Adjustment
Optimal torque adjustment plays a crucial role in preventing damage to hardwood while driving screws. Adjusting the torque settings on power tools ensures consistent and controlled screw insertion, preventing over-tightening, stripping, or damaging the wood fibers. By calibrating torque levels according to the wood density and screw type, you safeguard the integrity of the material and optimize the effectiveness of the fastening process.
Avoiding Over-Tightening
The temptation to over-tighten screws can compromise the structural integrity of your woodworking project and mar its aesthetic appeal. Over-tightening may cause wood splitting, weakening of joints, or damage to the screw head and surrounding wood surface. Practicing restraint and employing precision when tightening screws prevent over-stressing the material, preserving its strength and enhancing the longevity of the project.
Finishing Touches
Counter-Sinking Screws
Counter-sinking screws involves creating recessed holes for screw heads, allowing them to sit flush with the wood surface. This technique enhances the visual appeal of your woodworking project by concealing screw heads, reducing snag risks, and enabling seamless finishes. Properly executed counter-sinking promotes a professional appearance, minimizes surface disruptions, and elevates the overall aesthetic quality of your craftsmanship.
Filling Holes
Filling holes post-screw installation is crucial for maintaining the wood's integrity and visual continuity. Fillers come in various formulations to match different wood types and finishes, enabling seamless integration with hardwood grain and color. By diligently filling holes with suitable fillers, you eradicate gaps, enhance structural stability, and ensure a flawless appearance, elevating the professional finish of your woodworking creation.
Sanding and Sealing
Sanding surfaces post-screw installation smoothens wood imperfections, eliminates blemishes, and prepares the surface for sealing. Proper sanding techniques refine wood texture to a polished state, promoting an even finish and enhancing the wood's natural beauty. Sealing the wood surface afterward protects it from moisture, stains, and wear, extending its lifespan and preserving the aesthetic appeal of your woodworking project.
Common Mistakes to Avoid
When working with hardwood, it's crucial to be aware of common mistakes to avoid to ensure the success of your woodworking projects. Understanding and sidestepping these pitfalls can save time, effort, and materials in the long run. Choosing the right screws is essential, but equally important is ensuring you do not fall prey to these common errors that can detract from the quality and durability of your work. Some of the key mistakes to steer clear of include using incorrect screw types, poor installation techniques, underestimating length, and more.
Using Incorrect Screw Types
Avoiding Soft Woods Screws:
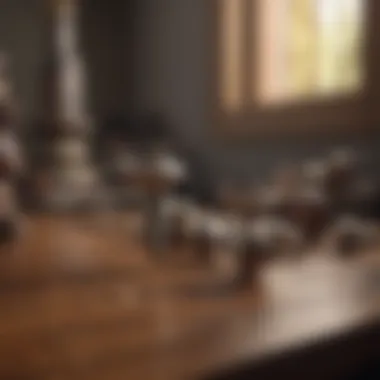
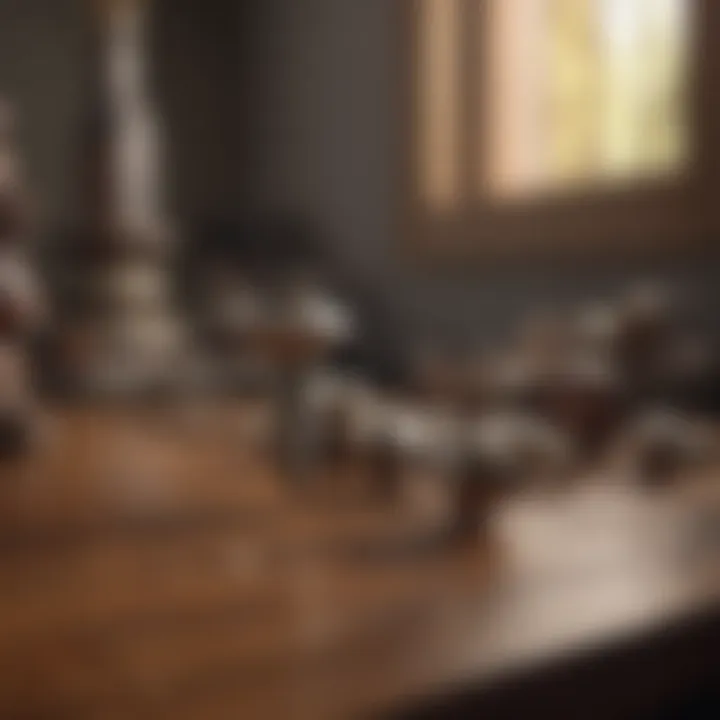
One of the critical aspects in screw selection is avoiding soft woods screws when working with hardwood. Soft woods screws are not designed to withstand the density and hardness of hardwood, leading to potential issues like stripping and weak fastening. Opting for screws specifically engineered for dense hardwoods ensures proper grip and longevity, enhancing the overall structural integrity of your woodworking projects. Their superior strength and durability make them a popular choice among professionals and DIY enthusiasts seeking reliability and precision in their work.
Skipping Pre-Drilling:
Skipping pre-drilling before inserting screws into hardwood can result in splitting, cracking, or even breaking of the wood fibers. Pre-drilling pilot holes allows for smooth and secure screw placement, reducing the risk of damaging the wood and ensuring a strong bond between the screw and the hardwood. This step is crucial in preventing structural weaknesses and maintaining the aesthetics of your finished piece. While it may seem like an extra task, the benefits far outweigh the time invested.
Underestimating Length:
Underestimating the length of screws needed for a woodworking project is a common mistake that can lead to subpar results. Using screws that are too short may not provide adequate anchorage, compromising the stability and structural integrity of the piece. It is essential to choose screws of sufficient length to penetrate the hardwood and secure the joints firmly. A thorough understanding of the depth requirements based on the thickness of the wood is key to avoiding this oversight and ensuring a professional finish.
Poor Installation Techniques
Incorrect Angle:
Maintaining the correct angle when driving screws into hardwood is vital for proper fastening and aesthetics. An incorrect angle can cause the screws to twist, strip the wood, or weaken the connection. Ensuring that the screws are driven in straight and at the appropriate angle guarantees a strong and visually appealing result. Attention to detail in this aspect enhances the overall quality of your woodworking projects and minimizes the risk of structural flaws.
Uneven Pressure:
Applying uneven pressure while driving screws can lead to uneven fastening and potential warping of the wood. Consistent and controlled pressure is essential to achieving a secure and uniform bond between the screw and the hardwood. By distributing pressure evenly throughout the driving process, you can prevent inconsistencies in the final assembly and ensure stability and balance in your woodworking creations.
Lack of Depth Control:
Failing to control the depth when driving screws can result in over-tightening, under-tightening, or surface damage to the wood. Maintaining precise depth control ensures that the screws are inserted to the correct depth, achieving a flush finish without damaging the wood surface. This attention to detail contributes to the professional look and structural durability of your woodworking projects, showcasing a mastery of installation techniques and a commitment to craftsmanship.
Conclusion
In this comprehensive guide on choosing the best screws for hardwood, the conclusion plays a pivotal role in summarizing key takeaways and emphasizing the significance of proper screw selection and installation. The conclusion encapsulates the critical aspects discussed throughout the article, providing a clear roadmap for readers to follow when embarking on woodworking projects involving hardwood. By highlighting the importance of selecting the right screws, understanding proper installation techniques, and implementing maintenance tips, the conclusion serves as a valuable tool for professionals and DIY enthusiasts seeking to enhance the durability and aesthetic appeal of their woodworking creations.
Summary of Key Points
Choosing the Right Screw
Selecting the appropriate screw type is paramount in ensuring the structural integrity and longevity of woodworking projects involving hardwood. Factors such as thread count, length, and gauge play a crucial role in determining the right screw for the job. By choosing the right screw, woodworkers can prevent issues such as splitting and ensure a secure and stable joinery, enhancing the overall quality of their craftsmanship.
Proper Installation Steps
Executing proper installation steps is essential in maximizing the effectiveness of chosen screws. Pre-drilling pilot holes, adjusting torque settings, and avoiding over-tightening are key elements in achieving a professional finish and avoiding damage to the hardwood. By following meticulous installation procedures, woodworkers can enhance the structural strength and visual appeal of their projects, elevating the overall woodworking experience.
Maintenance Tips
Maintenance tips are vital in preserving the integrity of woodworking projects over time. Implementing practices such as counter-sinking screws, filling holes seamlessly, and sanding and sealing surfaces contribute to the longevity and aesthetic quality of the finished piece. By incorporating these maintenance tips into their routine, woodworkers can ensure that their hardwood projects remain durable and visually appealing for years to come.
Enhancing Woodworking Projects
Efficiency in Screw Selection
Efficiency in screw selection is crucial for optimizing the woodworking process. By carefully choosing screws that match the hardness and density of the hardwood, woodworkers can streamline their projects and minimize the risk of damage or structural failure. Efficient screw selection not only saves time and resources but also results in a more precise and professional finish.
Optimizing Screw Performance
Optimizing screw performance involves utilizing screws that are specifically designed for hardwood applications. By understanding the characteristics of different screw materials and types, woodworkers can select screws that offer superior holding power and corrosion resistance. Optimized screw performance enhances the overall strength and durability of woodworking projects, ensuring long-lasting and reliable joinery.
Project Durability
Project durability is a fundamental consideration in woodworking, especially when working with hardwood. By prioritizing durability in the selection of screws and installation methods, woodworkers can create projects that withstand the test of time and environmental factors. Durable woodworking projects not only showcase craftsmanship and attention to detail but also provide long-term satisfaction and pride for creators and homeowners alike.