Top Drill Bits for Effortless Screw Extraction: A Comprehensive Guide
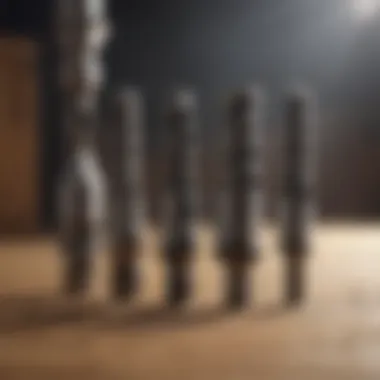
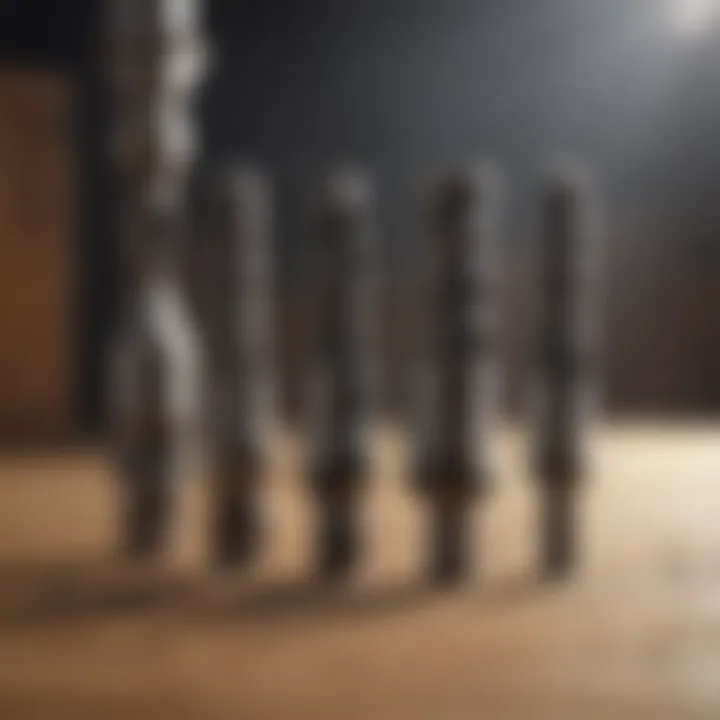
Overview of Topic
In the realm of home improvement, the specific topic we are delving into is the intricate process of effectively removing screws using the best drill bits available. This task may seem simple on the surface, but it requires the right tools and techniques to ensure success. The importance of this topic lies in the fact that screws can be stubborn to remove, especially in renovation or repair projects, and having the right drill bit can make a significant difference in the outcome.
Common Challenges and Solutions
Homeowners often face common challenges when it comes to extracting screws. One of the main issues is stripped or stuck screws that refuse to budge, causing frustration and hampering the progress of a project. To overcome these challenges, it is crucial to use high-quality drill bits specifically designed for screw extraction. Additionally, employing techniques such as pre-drilling pilot holes, applying lubricants, and using the correct drilling speed can greatly assist in overcoming these obstacles.
Product Recommendations
When it comes to selecting the best drill bits for drilling out screws, [Industry Brand] offers a range of top-quality products that cater to this specific need. These drill bits are specially engineered to provide optimal performance when removing screws, ensuring efficiency and precision. Some of the key benefits of these recommended products include durable materials, sharp cutting points, and compatibility with various screw types. By investing in these drill bits, homeowners can experience smoother screw extraction operations with minimal effort.
Step-by-Step Guides
To effectively drill out screws, follow these step-by-step guides for seamless implementation:
- Begin by selecting the appropriate drill bit size that matches the screw you intend to remove.
- Securely attach the drill bit to the drill chuck, ensuring a tight fit to prevent slippage.
- Mark the center of the screw to guide the drilling process accurately.
- Initiate drilling at a slow speed to avoid overheating and damaging the screw or surrounding material.
- Apply steady pressure while drilling in a straight line until the screw is completely extracted.
- Finish by cleaning any debris and ensuring the area is clear of residues for future use.
By following these detailed instructions and guidelines, homeowners can successfully navigate the process of drilling out screws with precision and efficiency.
Introduction
As we navigate through the labyrinth of screw extraction, understanding the importance of choosing the correct drill bit cannot be overstated. Not all drill bits are created equal, and when it comes to tackling different screw types embedded in various materials, precision and efficiency are paramount. The world of drill bits is vast, with a myriad of options tailored for specific applications. This guide aims to demystify the selection process and equip readers with the essential knowledge needed to undertake screw extraction with confidence and ease.
Advancing further, we will unravel the intricate details of different drill bit types, materials, and features crucial in the realm of screw extraction. By exploring the subtle distinctions between twist drill bits, left-hand drill bits, and screw extractor bits, readers will gain a comprehensive understanding of the nuances that influence their performance. Materials such as High-Speed Steel (HSS), Cobalt Steel, and Titanium Coated variations will be dissected, shedding light on how material composition directly impacts drilling efficiency.
Moreover, this article will delve into the specific considerations required when dealing with different screw types like wood screws, metal screws, and hex screws. Each screw type poses its own set of challenges, demanding a tailored approach in terms of drill bit selection and usage. By honing in on these nuances, readers will be empowered to make informed decisions when faced with a spectrum of screw extraction scenarios.
In essence, the crux of successful screw extraction lies not just in brute force but in the intricacies of drill bit features. Factors such as flute design, shaft strength, and coating options play a pivotal role in determining the effectiveness of a drill bit in removing stubborn screws. A deep dive into these features will arm readers with the knowledge needed to approach screw extraction methodically, enhancing both efficiency and results.
Understanding Screw Extraction
When it comes to effectively removing screws, having a comprehensive understanding of screw extraction is vital. In this article, we delve deep into the intricacies of screw extraction, focusing on specific elements, benefits, and considerations that can enhance the extraction process. By shedding light on the various facets of screw extraction, readers will be equipped with the knowledge needed to tackle screw removal with confidence and precision.
Types of Drill Bits
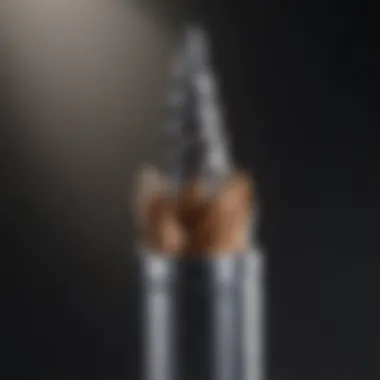
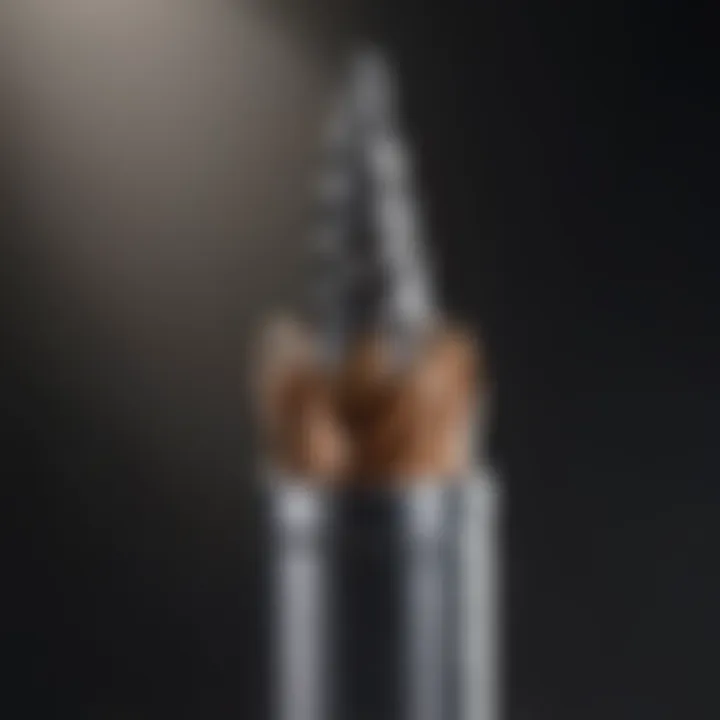
Twist Drill Bits
Twist drill bits are renowned for their versatility and precision in drilling various materials. Their helical flute design allows for efficient chip removal, resulting in cleaner and more accurate holes. A key characteristic of twist drill bits is their ability to work well with both handheld and stationary drilling equipment, making them a popular choice for general drilling tasks. While twist drill bits excel in drilling softer materials like wood and plastic, they may encounter challenges with tougher metals.
Left-Hand Drill Bits
Left-hand drill bits offer a unique advantage for screw extraction due to their counterclockwise rotation. This reverse rotation can grip onto screws and broken fasteners, facilitating easier removal without causing further damage. A key characteristic of left-hand drill bits is their ability to extract stuck or stripped screws effectively, providing a valuable solution for challenging extraction scenarios. However, using left-hand drill bits requires a degree of caution to prevent unintended consequences.
Screw Extractor Bits
Screw extractor bits are specially designed to tackle the toughest extraction tasks by gripping onto screws firmly and enabling their removal. Their unique spiral flutes and drilling ends provide optimal torque and grip on stubborn screws, ensuring successful extraction with minimal effort. A key characteristic of screw extractor bits is their ability to extract screws of various sizes and materials, offering versatility and reliability in extraction operations. While highly effective, screw extractor bits require precise handling to avoid damaging the workpiece.
Materials Matter
High-Speed Steel (HSS)
High-speed steel (HSS) drill bits are valued for their durability and heat resistance, making them ideal for drilling into tough materials like metal and hardwood. A key characteristic of HSS drill bits is their exceptional hardness and longevity, allowing for prolonged use without significant wear. The unique feature of HSS drill bits lies in their ability to maintain sharp cutting edges even under high-temperature conditions, ensuring consistent drilling performance. However, HSS drill bits may be prone to brittle fractures when subjected to excessive force.
Cobalt Steel
Cobalt steel drill bits are renowned for their strength and heat resistance, making them suitable for drilling hard metals like stainless steel and cast iron. A key characteristic of cobalt steel drill bits is their high cobalt content, which enhances their hardness and heat dissipation capabilities, resulting in superior drilling performance. The unique feature of cobalt steel drill bits is their ability to withstand extreme drilling conditions without losing their cutting edge, making them a reliable choice for demanding applications. However, cobalt steel drill bits may come at a higher price point compared to other types.
Titanium Coated
Titanium-coated drill bits combine the strength of high-speed steel with the durability of titanium nitride coating, offering improved wear resistance and extended tool life. A key characteristic of titanium-coated drill bits is their enhanced surface hardness and lubricity, reducing friction during drilling and preventing overheating. The unique feature of titanium-coated drill bits is their ability to drill efficiently through various materials while maintaining sharpness for extended periods, resulting in cost-effective and reliable performance. However, titanium-coated drill bits may require careful handling to prevent excessive heat buildup.
Consideration of Screw Types
Wood Screws
Wood screws are designed with coarse threads and sharp points, making them ideal for fastening wood and other soft materials. A key characteristic of wood screws is their ability to create strong connections in wooden surfaces by gripping the fibers securely, ensuring structural integrity. The unique feature of wood screws lies in their self-tapping design, which eliminates the need for pre-drilling in many applications, saving time and effort. However, using wood screws in hardwoods may require pilot holes to prevent splitting.
Metal Screws
Metal screws are engineered with fine threads and a pointed tip to securely fasten metal components and thin materials. A key characteristic of metal screws is their excellent tensile strength and corrosion resistance, ensuring long-lasting connections in metal assemblies. The unique feature of metal screws is their ability to provide a secure hold in metal substrates without loosening over time, making them essential for structural applications. However, using metal screws in dissimilar metals may lead to galvanic corrosion.
Hex Screws
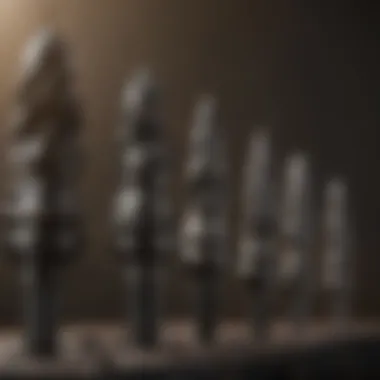
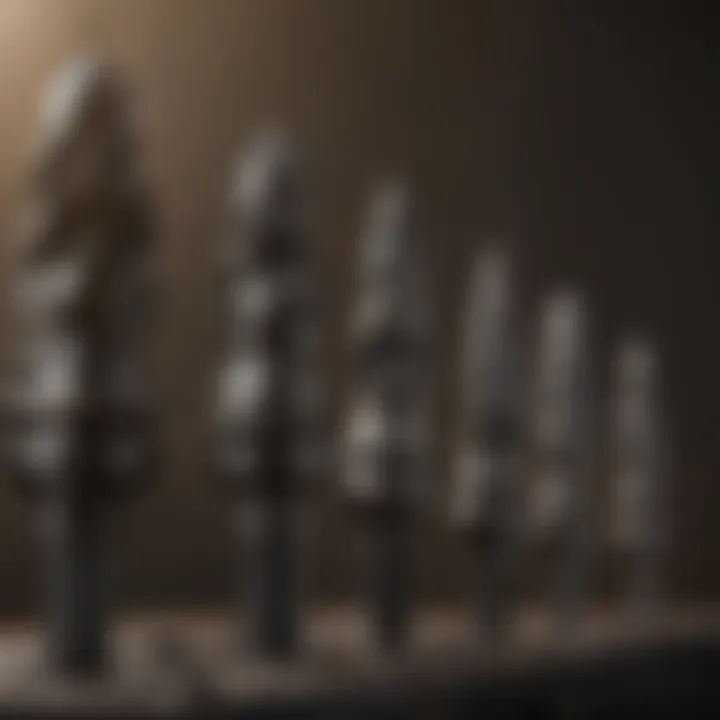
Hex screws, also known as hex bolts or hex cap screws, feature a hexagonal head for easy installation and removal with a wrench or socket. A key characteristic of hex screws is their high tensile strength and precise fit, allowing for secure fastening in mechanical and structural applications. The unique feature of hex screws lies in their resistance to loosening due to vibrations, making them a reliable choice for machinery and equipment assembly. However, over-tightening hex screws may lead to thread stripping or head deformation.
Drill Bit Features
Flute Design
The flute design of a drill bit plays a crucial role in chip evacuation and hole accuracy during drilling operations. Optimal flute geometry enables efficient chip removal and enhances drilling speed, resulting in cleaner and smoother holes. A key characteristic of flute design is its ability to prevent clogging and heat buildup in the drilled hole, ensuring consistent performance in various materials. The unique feature of flute design lies in its versatility across different drill bit types, offering tailored solutions for specific drilling applications. However, improper flute design may result in chip packing and reduced drilling efficiency.
Shaft Strength
The shaft strength of a drill bit determines its resilience against bending and breaking during high-torque drilling tasks. High shaft strength is essential for maintaining drilling stability and precision, especially in challenging materials or deep drilling applications. A key characteristic of shaft strength is its impact resistance and rigidity, ensuring effective power transmission from the drill to the cutting tip. The unique feature of shaft strength lies in its ability to withstand torsional stress and axial loads, providing reliability and durability in demanding drilling conditions. However, excessive force or lateral pressure may compromise the shaft integrity and lead to premature wear.
Coating Options
Coating options for drill bits, such as titanium nitride (TiN) or black oxide, enhance the surface hardness and lubricity of the cutting edges, resulting in improved wear resistance and reduced friction during drilling. A key characteristic of coating options is their ability to extend tool life by protecting against heat and wear, ensuring consistent cutting performance over multiple drilling operations. The unique feature of coating options lies in their compatibility with specific materials and applications, offering tailored solutions for various drilling needs. However, improper coating application or excessive wear may diminish the coating's effectiveness and impact drilling performance.
Choosing the Right Drill Bit
When it comes to successfully drilling out screws, selecting the right drill bit is paramount. The choice of drill bit can significantly impact the efficiency and effectiveness of the screw extraction process. In this section, we will delve into the crucial elements, benefits, and considerations of choosing the right drill bit for optimum results.
Size Does Matter
Matching Screw Size
Matching screw size is a fundamental aspect to consider when choosing a drill bit for extracting screws. Ensuring that the drill bit matches the size of the screw enhances precision and minimizes the risk of damaging the screw head or the surrounding material. The key characteristic of matching screw size lies in its ability to provide a snug fit, allowing for better control and accuracy during the drilling process. This precise fit not only facilitates smooth screw extraction but also reduces the likelihood of slippage or misalignment. While matching screw size offers excellent compatibility and accuracy, it may limit versatility when working with screws of varying sizes.
Pilot Hole Consideration
Pilot hole consideration is another essential factor in selecting the right drill bit for screw extraction. Creating a pilot hole before drilling out the screw can prevent the wood or metal from splitting or cracking, especially when dealing with hard materials. Pilot holes serve as guides for the drill bit, ensuring a straight path for accurate screw removal. The key characteristic of pilot hole consideration lies in its ability to improve the overall stability and precision of the drilling process. By reducing the risk of material damage and providing a clear pathway for the drill bit, pilot holes contribute to efficient and effective screw extraction. However, the additional step of creating pilot holes may slightly prolong the extraction process, particularly when working on multiple screws.
Compatibility with Drilling Equipment
Corded Drills
In the realm of drilling out screws, corded drills offer a reliable and consistent power source for tackling various screw extraction tasks. The key characteristic of corded drills lies in their steady power delivery, which ensures consistent drilling performance without the need for battery changes or recharges. This feature makes corded drills ideal for prolonged use and heavy-duty applications, providing uninterrupted power to drive through stubborn screws. While corded drills provide continuous operation, their reliance on a power outlet may restrict mobility, making them more suitable for stationary or workshop settings.
Cordless Drills
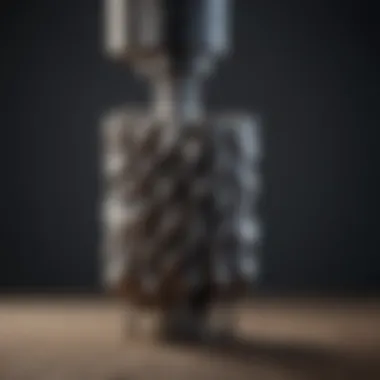
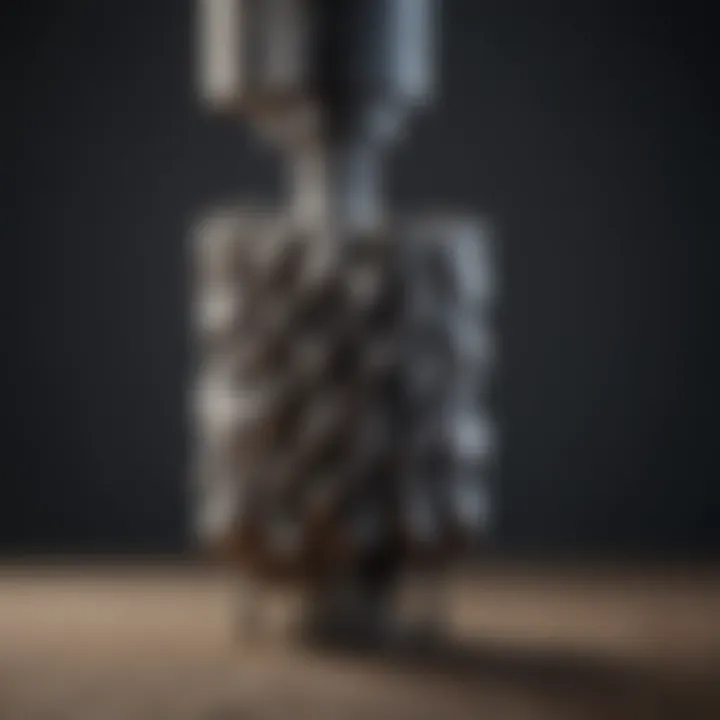
Contrasting corded drills, cordless drills offer enhanced portability and flexibility when extracting screws. The key characteristic of cordless drills lies in their battery-powered operation, allowing users to maneuver easily in various work environments without being tethered to a power source. This mobility grants users the freedom to extract screws in tight or hard-to-reach spaces where corded drills may have limitations. Cordless drills excel in versatility and convenience, enabling users to perform screw extraction tasks with ease and efficiency on the go. However, the need for battery recharges or replacements may interrupt continuous operation, necessitating spare batteries for extended usage.
Impact Drivers
When efficiency and power are paramount in screw extraction, impact drivers stand out as formidable tools. The key characteristic of impact drivers lies in their high torque output and rapid rotational force, allowing for swift and robust screw removal. Impact drivers excel in driving screws effortlessly and extracting stubborn or rusted screws with ease, thanks to their impact mechanism that delivers forceful rotational energy. This unique feature of impact drivers makes them indispensable for demanding screw extraction tasks that require precision and strength. However, the high torque levels and rotational force of impact drivers may lead to overtightening or overdriving screws if not handled with care, potentially causing damage to the screw threads or the material being worked on.
Performance Metrics
Speed and Precision
The combination of speed and precision is vital for successful screw extraction with a drill bit. Speed determines the efficiency and rate at which the drill bit can remove screws, while precision ensures accurate screw removal without causing damage to the surrounding material. The key characteristic of speed and precision lies in their synergistic effect, where fast drilling speeds are complemented by precise control, resulting in swift and accurate screw extraction. This balanced approach enhances productivity and minimizes errors, allowing users to remove screws quickly and efficiently. However, maintaining a balance between speed and precision is crucial to prevent overheating of the drill bit or the material, which can adversely affect the extraction process and compromise the longevity of the drill bit.
Heat Resistance
Heat resistance plays a critical role in the performance of a drill bit during screw extraction. The key characteristic of heat resistance lies in the drill bit's ability to withstand high temperatures generated during drilling without compromising its structural integrity or sharpness. High heat resistance ensures prolonged durability and performance of the drill bit, even when working on demanding materials or continuously extracting screws. This feature is particularly beneficial when tackling stubborn screws that require extended drilling periods, as it prevents overheating and maintains the drill bit's efficiency. While heat-resistant drill bits offer enhanced durability, prolonged exposure to high temperatures can still affect their longevity and cutting performance, necessitating periodic cooling or rotation of drill bits for optimal results.
This meticulously crafted section provides in-depth insights into the critical aspects of choosing the right drill bit for screw extraction, focusing on size considerations, compatibility with drilling equipment, and essential performance metrics. By understanding these key elements, readers can make informed decisions when selecting drill bits for efficient and effective screw removal.
Tips for Effective Screw Extraction
In this comprehensive guide focusing on the best drill bits for effectively drilling out screws, the section on tips for effective screw extraction plays a crucial role in ensuring successful screw removal. By delving into specific elements and considerations, readers can gain valuable insights into optimizing the extraction process. Understanding the importance of preparation and technique is key to achieving desired results efficiently. Effective screw extraction not only saves time but also prevents damage to surrounding materials and enhances overall project outcomes.
Preparation Steps
- Appropriate Safety Gear: When it comes to screw extraction, safety should always be a top priority. Appropriate safety gear such as safety goggles, gloves, and ear protection are essential for safeguarding against potential hazards during the extraction process. These safety measures not only protect the individual performing the task but also ensure a secure working environment conducive to successful screw removal. The use of quality safety gear is a popular choice within this article due to its proven effectiveness in minimizing risks and promoting a safe working environment.
- Securing the Workpiece: Another critical aspect of effective screw extraction is securing the workpiece before commencing the removal process. Properly securing the workpiece with clamps or vices prevents any movement or slippage that could lead to inaccuracies or accidents during extraction. The key characteristic of securely holding the workpiece in place is its ability to provide stability and precision, allowing for controlled and efficient screw removal. While securing the workpiece may add an extra step to the process, its advantages in terms of safety and accuracy make it a valuable practice within this article.
Techniques for Screw Removal
- Reverse Drilling Method: The reverse drilling method is a technique that involves drilling in the opposite direction of the screw's insertion to loosen it for easier removal. This method is beneficial in situations where screws are stubbornly stuck or stripped, making traditional extraction challenging. The unique feature of the reverse drilling method lies in its ability to create opposing forces that help release the screw grip, facilitating smoother extraction. Although this technique requires attentiveness to avoid potential damage, its advantages in dislodging stubborn screws make it a preferred choice within this article.
- Using Extractor Bits: Extractor bits are specialized tools designed to grip and extract screws with damaged or stripped heads. These bits feature reverse threading that bites into the screw head, allowing for effective removal without causing further damage to the surrounding material. The key characteristic of extractor bits is their ability to grip and extract screws securely, providing a practical solution for challenging screw removal tasks. While using extractor bits requires precision and care to avoid breakage, their advantages in safely extracting damaged screws make them a valuable addition to this article.
Maintenance and Care
- Cleaning and Storage: Proper cleaning and storage of drill bits are essential practices to prolong their lifespan and maintain their efficiency. Regularly cleaning drill bits after use helps prevent debris buildup that can affect performance, ensuring consistent drilling results. Additionally, storing drill bits in a dry and secure location protects them from corrosion and damage, preserving their sharpness and functionality. The key characteristic of cleaning and storage lies in its ability to extend the longevity of drill bits, making it a beneficial practice for maintaining optimal performance within this article.
- Regular Inspection: Conducting regular inspections of drill bits is vital for identifying signs of wear, damage, or dullness that may impact performance. By inspecting drill bits before and after use, individuals can address any issues promptly and prevent potential setbacks during drilling tasks. The key characteristic of regular inspection is its proactive approach to maintaining drill bit quality and functionality, enabling users to ensure peak performance and efficiency. Although regular inspections require time and attention to detail, their advantages in proactive maintenance make them a valuable recommendation within this article.
Conclusion
One of the primary takeaways from this article is the significance of selecting the appropriate size drill bit that matches the screw being extracted. This ensures a secure fit and optimal performance during the drilling process. Additionally, considering pilot hole requirements before drilling enhances precision and prevents damage to the workpiece or the screw itself.
Moreover, compatibility with drilling equipment is essential for achieving desired results. Different types of drills, such as corded drills, cordless drills, and impact drivers, offer varying levels of power and torque, affecting the extraction process. Understanding the performance metrics of speed, precision, and heat resistance can further elevate the efficiency of screw extraction tasks.
For effective screw extraction, proper preparation steps are vital. This includes wearing appropriate safety gear to prevent injuries and securing the workpiece to maintain stability during drilling. Employing techniques like the reverse drilling method and utilizing extractor bits can facilitate smooth screw removal without causing additional damage.
Lastly, maintenance and care of drill bits are imperative for prolonged usability and performance. Regularly cleaning and storing the drill bits properly can prevent corrosion and maintain sharpness, ensuring optimal functionality when needed. Conducting routine inspections of the drill bits can help identify any wear or damage early, allowing for timely repairs or replacements.