Exploring the Intricacies of Advanced Specialized Drill Bits
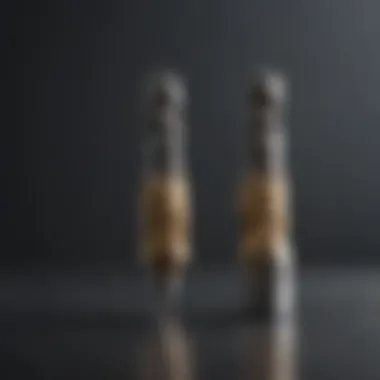
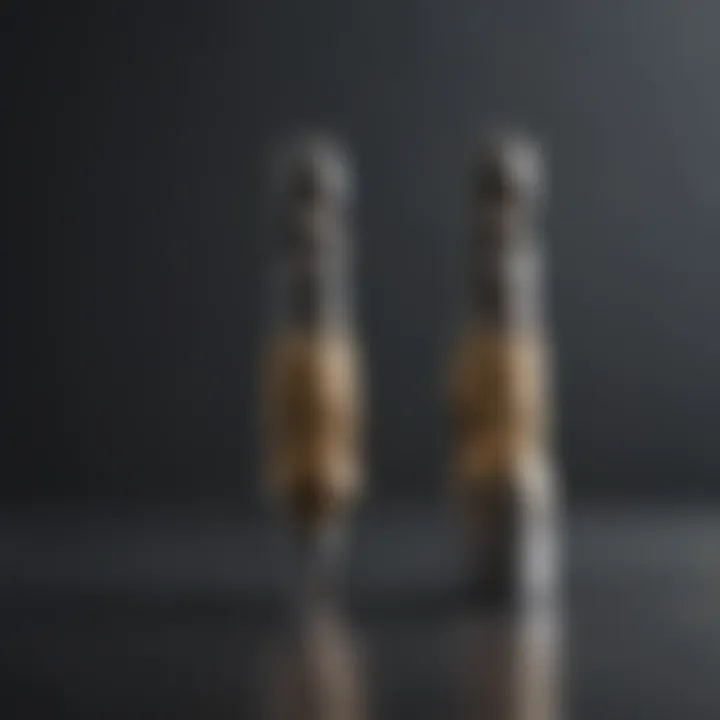
Overview of Specialized Drill Bits in the Home Improvement Industry
The world of specialized drill bits in the home improvement industry is a fascinating and essential aspect for anyone looking to enhance their drilling experiences. These advanced tools offer a wide range of applications and benefits that can significantly optimize performance and precision.
Common Challenges Faced by Homeowners and Solutions
Homeowners often encounter challenges when it comes to selecting the right drill bits for specific applications. Issues such as durability, precision, and compatibility with different materials can pose hurdles. However, with the right knowledge and insight, these challenges can be easily overcome. Tips such as proper bit selection based on the material being drilled, maintaining sharpness through sharpening, and using the correct drilling techniques can help homeowners tackle these challenges effectively.
Product Recommendations from Industry Brands
Top industry brands offer a wide selection of specialized drill bits that cater to various needs and preferences. Brands like [Industry Brand] provide drill bits known for their durability, precision, and versatility. These products come with a range of features such as advanced coatings for enhanced durability, innovative designs for improved performance, and compatibility with different drilling machines. By investing in high-quality drill bits from reputable brands, homeowners can ensure smooth drilling experiences and reliable results.
Step-by-Step Guides for Optimal Drilling Results
Implementing improvements in drilling requires precision and attention to detail. By following practical step-by-step guides, homeowners can enhance their drilling skills and achieve optimal results. From selecting the right bit for the job to maintaining and sharpening drill bits for prolonged use, each step plays a crucial role in ensuring efficient and accurate drilling. Detailed instructions on drilling techniques, safety measures, and maintenance practices can empower homeowners to successfully carry out drilling projects with confidence and precision.
Introduction
In the realm of construction, woodworking, and automotive industries, the utilization of specialized drill bits plays a pivotal role in achieving precise and efficient drilling operations. With advancements in technology and material science, specialized drill bits have evolved to cater to specific drilling needs, offering a myriad of benefits over traditional drill bits. This section serves as a gateway to understanding the significance and nuances of specialized drill bits, setting the stage for a detailed exploration of their types, applications, and future innovations.
Defining Specialized Drill Bits
Understanding the Purpose
Specialized drill bits are meticulously engineered tools designed to excel in drilling through various materials with precision and effectiveness. The key aspect of understanding the purpose of specialized drill bits lies in their targeted functionality and specialized features tailored to specific applications. For instance, drill bits used for metal fabrication differ significantly from those used in woodworking due to the distinct requirements of each material. Understanding the purpose of specialized drill bits empowers professionals to choose the right tool for the job, enhancing efficiency and achieving superior results. The unique feature of specialized drill bits is their capacity to optimize drilling processes, resulting in cleaner cuts, reduced material waste, and enhanced productivity.
Key Characteristics
The key characteristics of specialized drill bits encompass aspects such as material composition, tip geometry, and specialized coatings tailored to enhance durability and cutting performance. By leveraging high-quality materials such as carbide and cobalt steel, specialized drill bits offer superior hardness and heat resistance compared to standard drill bits, ensuring prolonged tool life and consistent performance. Additionally, the unique flute designs and tip configurations of specialized drill bits enable efficient chip evacuation, reducing heat buildup and preventing material distortion during the drilling process. These characteristics translate into enhanced drilling precision, improved surface finish, and reduced drilling times, making specialized drill bits a valuable investment for professionals seeking optimal drilling outcomes.
Historical Evolution
Origins
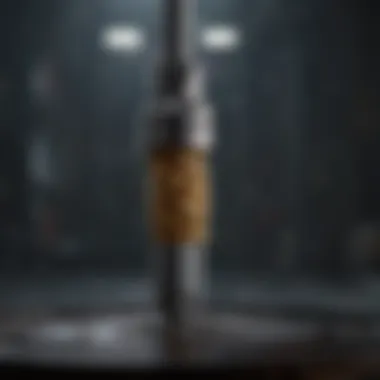
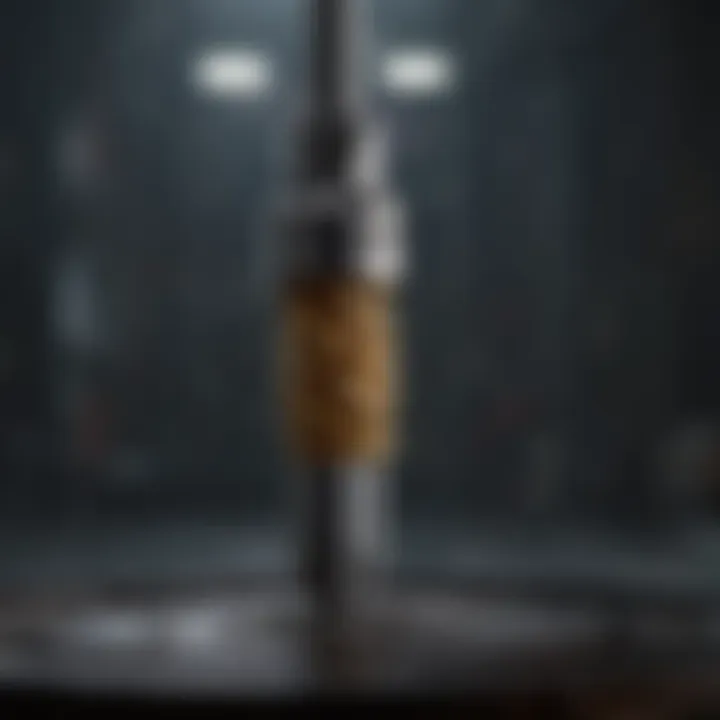
The origins of specialized drill bits can be traced back to ancient civilizations where rudimentary drilling tools were crafted from materials like stone and bone. Over time, the evolution of drill bits saw the emergence of metal drill bits during the industrial revolution, revolutionizing drilling capabilities across various industries. The key characteristic of origins lies in the gradual refinement of drill bit designs and materials, fueled by innovations in metallurgy and manufacturing processes. This evolutionary journey from primitive hand tools to sophisticated metal drill bits underscores the continuous quest for precision and efficiency in drilling operations. The unique feature of drill bit origins is the interplay of craftsmanship and technological advancements that have shaped modern drill bit designs, unlocking new possibilities for precision drilling across diverse materials and applications.
Technological Advancements
The continual pursuit of technological advancements has been instrumental in enhancing the performance and versatility of specialized drill bits. Innovations in materials science, such as the development of tungsten carbide tips and diamond coatings, have revolutionized the cutting capabilities of drill bits, enabling them to drill through hardened materials with ease. The key characteristic of technological advancements is the integration of cutting-edge manufacturing processes like CNC machining and laser etching, which have elevated the precision and consistency of drill bit production. This convergence of technology and engineering has propelled specialized drill bits to new heights of performance and reliability, enabling users to tackle complex drilling tasks with unprecedented ease and efficiency.
Types of Specialized Drill Bits
Specialized drill bits play a crucial role in various industries and applications, offering specific design features and material compositions tailored to different drilling needs. Understanding the intricacies of drill bit types is essential for optimizing performance and achieving precise results. In this article, we delve deep into the realm of specialized drill bits, highlighting the importance of selecting the right type for each drilling task.
Twist Drill Bits
Twist drill bits are among the most commonly used types of drill bits, known for their versatility and effectiveness in various materials. In this section, we explore three significant variations of twist drill bits, each designed to excel in specific applications.
High-Speed Steel (HSS)
High-Speed Steel (HSS) drill bits are revered for their durability and resistance to heat, making them ideal for high-speed drilling operations. These bits feature exceptional sharpness and longevity, ensuring consistent performance in demanding projects. The key characteristic of HSS drill bits lies in their ability to maintain sharp cutting edges, resulting in precise and efficient drilling. Despite their advantages, HSS bits may be prone to quicker wear under intense usage, requiring proper maintenance for prolonged use.
Cobalt Steel
Cobalt steel drill bits are renowned for their superior hardness and heat-resistance properties, offering enhanced performance in challenging drilling conditions. The key characteristic of cobalt steel lies in its ability to withstand high temperatures without compromising on cutting efficiency. These bits are a popular choice for drilling hard materials such as stainless steel and cast iron, thanks to their extended lifespan and robust construction. However, cobalt steel bits can be more expensive than other options and may require specialized sharpening techniques for optimal longevity.
Carbide-Tipped
Carbide-tipped drill bits are characterized by their exceptional hardness and cutting precision, making them well-suited for abrasive materials like concrete and masonry. The key advantage of carbide-tipped bits is their longevity and resistance to wear, ensuring consistent drilling performance over extended periods. These bits feature a unique carbide tip that offers superior cutting strength and durability, enhancing efficiency in tough drilling tasks. Despite their impressive qualities, carbide-tipped bits can be brittle and may chip if not used with proper care, requiring careful handling to maintain their integrity.
Applications of Specialized Drill Bits
In this section, we delve into the vital role that specialized drill bits play in various industries and sectors, providing a gateway to innovation and efficiency. The applications of specialized drill bits are diverse and essential, revolutionizing the way tasks are approached and accomplished. Professionals and enthusiasts alike benefit from the precision and effectiveness that these drill bits offer, enhancing their projects and delivering superior results.
Construction Industry
Concrete Drilling
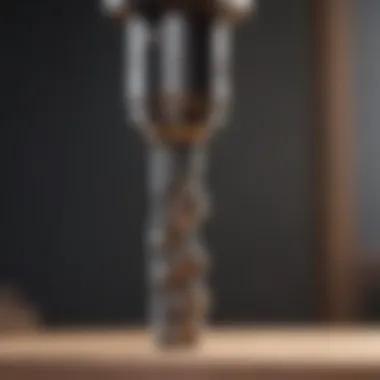
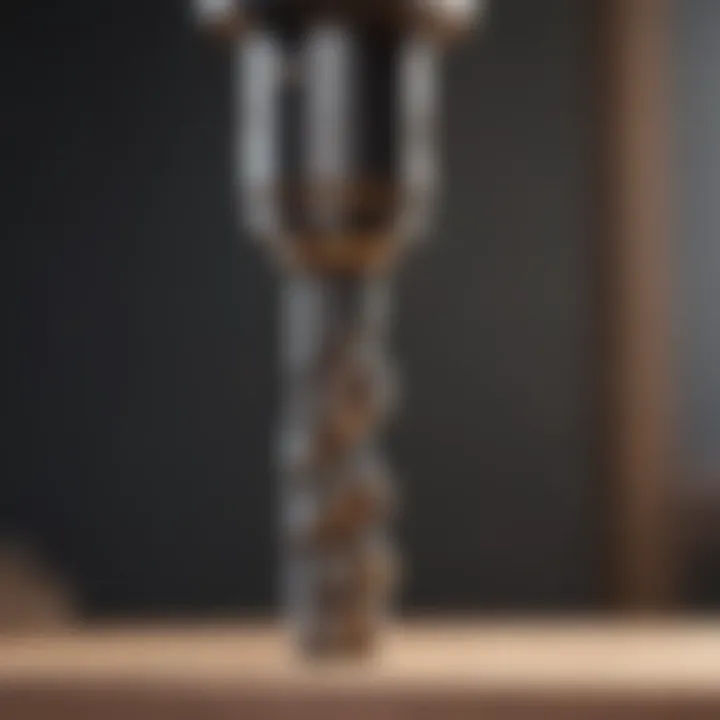
Concrete drilling stands out as a cornerstone application in the construction industry, facilitating the creation of openings in concrete surfaces with unparalleled accuracy and speed. The key characteristic of concrete drilling lies in its ability to penetrate tough materials while maintaining structural integrity. This makes it a popular choice for construction projects that require precise and reliable drilling. Concrete drilling's unique feature is its adaptability to various concrete compositions, offering versatility and efficiency. However, frequent use may lead to quicker drill bit wear, requiring periodic replacements to maintain optimal performance.
Metal Fabrication
Metal fabrication showcases another integral application of specialized drill bits in the construction sector, enabling the drilling of holes and shaping of metal components with utmost precision. The key characteristic of metal fabrication drilling is its ability to withstand high temperatures and pressures, essential for working with different metal alloys. This makes it a preferred choice for metalworking tasks that demand accuracy and consistency. One unique feature of metal fabrication drilling is its compatibility with a wide range of metals, ensuring versatility and adaptability. However, prolonged drilling may result in reduced drill bit sharpness, necessitating frequent re-sharpening for continued efficiency.
Woodworking Sector
Cabinet Making
Within the woodworking sector, drill bits play a fundamental role in cabinet making, allowing for the precise drilling of holes for hinges, handles, and assembly. Cabinet making drill bits are characterized by their fine cutting edges and chip removal abilities, making them ideal for intricate woodworking projects. The unique feature of cabinet making drill bits lies in their ability to create clean and precise holes without splintering or damaging the wood grain. This makes them a favored choice for craftsmen seeking impeccable finishes. However, care must be taken to avoid overheating during prolonged use, as this can affect the drill bit's overall performance.
Furniture Construction
In furniture construction, specialized drill bits contribute significantly to the assembly and customization of wooden components, enhancing the efficiency and quality of the production process. The key characteristic of drill bits used in furniture construction is their precision in creating holes for dowels, screws, and connectors, ensuring seamless joinery and structural integrity. This precision makes them a popular choice for furniture makers aiming for immaculate craftsmanship. A unique feature of furniture construction drill bits is their optimized design for working with various wood densities, offering reliability and consistency. However, frequent drilling in dense hardwoods may lead to quicker dulling of the drill bit, necessitating periodic sharpening to maintain peak performance.
Automotive Field
Drilling in Automobile Manufacturing
Drilling plays a crucial role in automobile manufacturing by enabling precise hole creation for component assembly, fabrication, and customization. The key characteristic of drilling in automobile manufacturing lies in the requirement for high precision, as even minor deviations can impact vehicle performance and safety. This preciseness makes specialized drill bits a preferred choice in automotive settings where accuracy is paramount. A unique feature of drilling in automobile manufacturing is the incorporation of advanced coatings and materials to enhance heat dissipation and wear resistance, ensuring prolonged durability and efficiency. However, the high intensity of drilling in automotive applications may accelerate wear on drill bits, necessitating regular maintenance and replacements to uphold operational excellence.
Optimizing Drill Bit Performance
In the realm of specialized drill bits, optimizing performance is crucial to ensure efficient and effective drilling operations. By focusing on improving performance factors, professionals and enthusiasts can achieve precise and accurate results. This section delves into various elements that contribute to enhancing drill bit performance, offering insights that can elevate drilling experiences to new heights.
Proper Maintenance
Cleaning
Cleaning plays a vital role in maintaining the effectiveness and longevity of drill bits. By removing debris, residues, and built-up material from the bits, cleaning helps prevent wear and tear, ensuring optimal cutting performance. The key characteristic of cleaning is its ability to extend the lifespan of drill bits by keeping them free from contaminants. This maintenance practice is a popular choice among professionals as it enhances the durability and sharpness of the bits, ultimately improving drilling precision. Despite its advantages, cleaning requires meticulous attention to detail to ensure thorough removal of any materials that could hinder the drilling process.
Sharpening Techniques
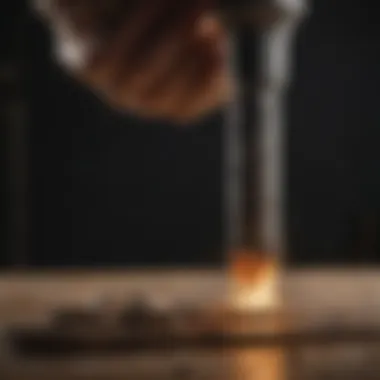
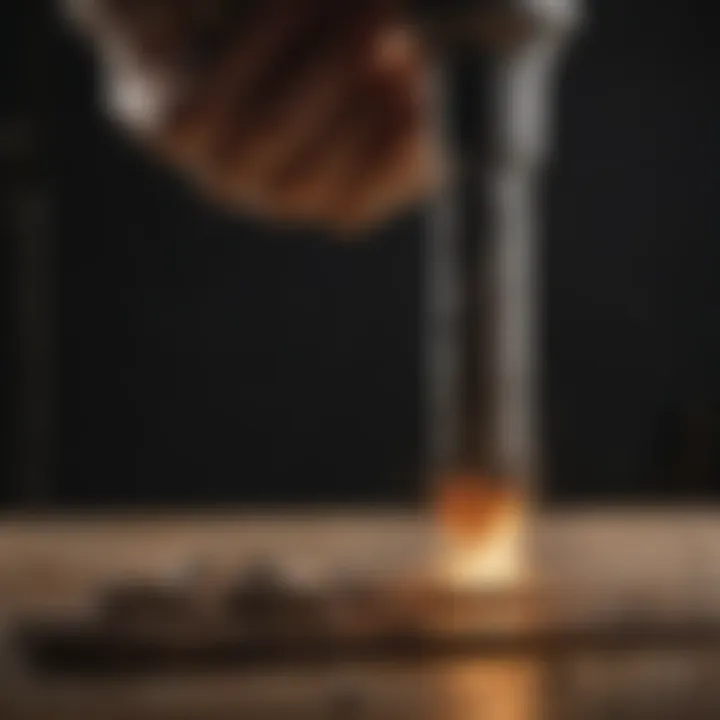
Sharpening techniques are instrumental in revitalizing dull or worn-out drill bits, enhancing their cutting efficacy. By restoring sharp edges, these techniques enable drill bits to maintain their precision and effectiveness during drilling tasks. The key characteristic of sharpening techniques lies in their ability to restore the original sharpness of the bits, facilitating smooth and accurate drilling operations. These techniques are a beneficial choice for professionals looking to extend the lifespan of their drill bits and maximize performance. However, improper sharpening can lead to irregular cutting edges, affecting drilling quality. It is essential to employ proper sharpening methods to avoid compromising the efficiency of the drill bits.
Usage Tips
Speed and Feed Rates
Optimal speed and feed rates are essential considerations for achieving efficient drilling outcomes. By matching the right speed and feed rates to the material being drilled, users can prevent overheating, reduce tool wear, and maintain precision during operations. The key characteristic of speed and feed rates is their influence on the chip formation process, which directly impacts the quality of the drilled hole. Proper adjustment of these parameters is a popular choice among professionals seeking to enhance productivity and maximize tool lifespan. However, incorrect speed and feed rate settings can result in poor chip evacuation and premature tool failure, underscoring the importance of adhering to recommended guidelines for each drilling application.
Coolant Application
Coolant application is integral to controlling heat buildup and extending the lifespan of drill bits during high-speed drilling operations. By dissipating heat and lubricating the cutting edges, coolant helps prevent thermal damage and reduces friction, enhancing cutting efficiency. The key characteristic of coolant application is its capacity to enhance tool life by minimizing heat-related wear and increasing chip evacuation. This application is a beneficial choice for professionals aiming to improve cutting performance and maintain drilling precision. However, excessive coolant usage can lead to environmental concerns and health hazards, emphasizing the need for proper coolant management practices to balance performance benefits with safety considerations.
Future Innovations in Drill Bit Technology
In the realm of specialized drill bits, staying at the forefront of technological advancements is paramount to enhance efficiency and precision. The section on Future Innovations in Drill Bit Technology within this article delves into the cutting-edge developments reshaping the drilling landscape. By exploring the integration of nanotechnology and the emergence of smart drill bits, professionals and enthusiasts can anticipate groundbreaking changes that are set to revolutionize their drilling experiences.
Nanotechnology Integration
Nanotechnology integration stands as a pinnacle in the evolution of drill bits, heralding a new era of durability and precision. It encompasses two key aspects: Enhanced Durability and Precision Engineering.
Enhanced Durability
Enhanced Durability is a game-changer in drill bit performance, offering unparalleled resilience and longevity. The nanotechnology-infused materials used in Enhanced Durability ensure that drill bits can withstand rigorous drilling conditions without compromising precision or efficiency. The unique feature of Enhanced Durability lies in its ability to resist wear and tear, extending the lifespan of drill bits significantly. While the advantages are evident in prolonged usability and reduced replacement costs, some may find that the initial investment in these advanced drill bits is higher. However, the benefits far outweigh the costs, making Enhanced Durability a popular choice for professionals seeking reliability and longevity in their drilling tools.
Precision Engineering
Precision Engineering, another facet of nanotechnology integration, focuses on enhancing the accuracy and consistency of drill bits. The key characteristic of Precision Engineering lies in its ability to craft drill bits with unparalleled precision, ensuring uniformity in borehole sizes and depths. By leveraging nanoscale engineering techniques, drill bits can achieve micron-level accuracy, ideal for intricate drilling tasks that demand utmost precision. The unique feature of Precision Engineering resides in its capability to optimize drilling operations, resulting in flawless outcomes and minimal errors. While Precision Engineering offers superior accuracy, some may find that the intricate manufacturing processes could lead to higher production costs. However, the precision and quality delivered by these drill bits justify the investment, making Precision Engineering a preferred choice for professionals prioritizing exactness and perfection in their drilling endeavors.
Smart Drill Bits
The emergence of smart drill bits brings connectivity and real-time monitoring to the forefront of drilling technology, ushering in a new era of efficiency and data-driven insights.
Io
T Connectivity
IoT Connectivity transforms traditional drill bits into intelligent tools that communicate and interact seamlessly with other devices and systems. By harnessing IoT technology, drill bits can provide real-time data on drilling progress, tool condition, and performance metrics. The key characteristic of IoT Connectivity is its ability to streamline drilling operations by optimizing parameters based on real-time feedback. This adaptability ensures that drill bits operate at peak efficiency, reducing downtime and enhancing productivity. The unique feature of IoT Connectivity is its capacity to facilitate remote monitoring and control, allowing users to oversee drilling processes from anywhere with an internet connection. While the advantages include improved operational efficiency and data-driven decision-making, some may express concerns about data security and connectivity issues. However, the benefits of IoT Connectivity in enhancing drill bit performance and productivity outweigh these considerations, making it a valuable asset for professionals engaging in complex drilling tasks.
Real-Time Monitoring
Real-Time Monitoring offers a proactive approach to drill bit management, enabling users to track and analyze drilling activity instantaneously. By providing instant feedback on drill bit performance and conditions, Real-Time Monitoring empowers users to make real-time adjustments and optimizations. The key characteristic of Real-Time Monitoring is its ability to detect potential issues early and prevent costly downtime or tool damage. This proactive approach ensures that drill bits operate at peak performance levels, prolonging their lifespan and maximizing efficiency. The unique feature of Real-Time Monitoring lies in its real-time alerts and notifications, alerting users to any anomalies or deviations during drilling operations. While the advantages of Real-Time Monitoring are evident in optimized performance and proactive maintenance, some users may find the continuous monitoring system intrusive or overwhelming. Nevertheless, the benefits of real-time insights and preventative maintenance offered by Real-Time Monitoring position it as a vital tool for professionals seeking to enhance their drilling operations.