Understanding Wire Cable Tighteners: Types and Best Practices
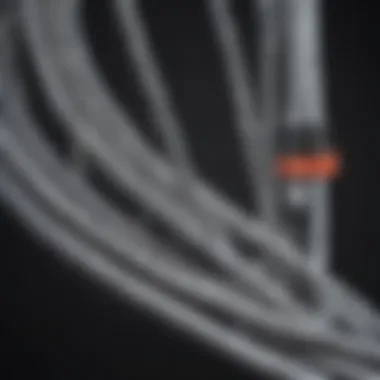
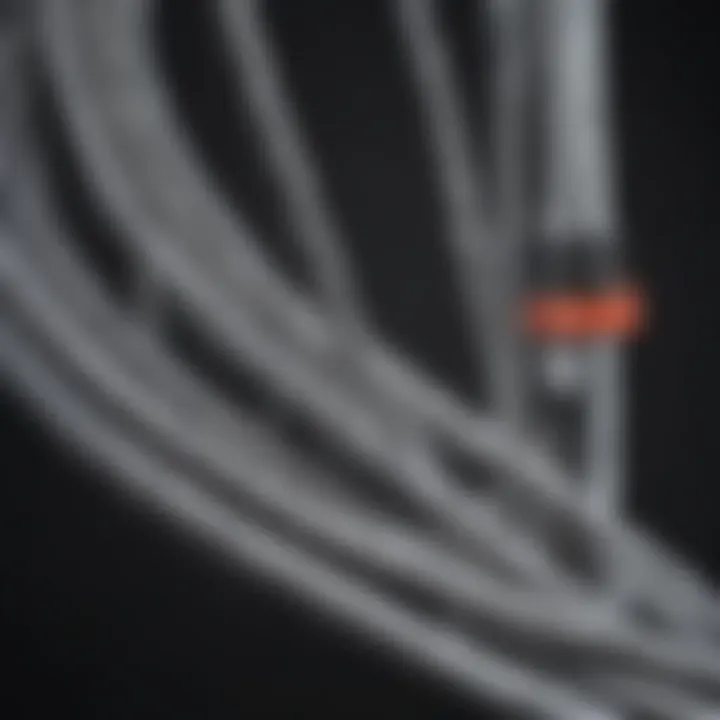
Overview of Topic
Wire cable tighteners serve a vital role in various applications such as construction, electrical work, and even in residential settings. They function to secure and stabilize wires and cables, minimizing potential hazards from loose or sagging installations. Families relying on functional outdoor lighting or safe garage wiring should appreciate the significance of having proper tension maintained within these systems.
Understanding their mechanisms and installation techniques is essential not only for achieving effective performance but also for ensuring safety in all related tasks. Many homeowners may find the idea of wire cable tighteners unfamiliar, yet they offer an elegant solution for matters of cable management. By having this knowledge, individuals can avoid pitfalls that stem from improper set-up.
Common Challenges and Solutions
One significant difficulty homeowners encounter with wire cable tighteners revolves around ineffectively securing wire machinery or systems, resulting in sagging cables or damaged wires over time. Or they may face trouble in choosing the appropriate hardware for their unique context. Not solving these problems can lead to malfunction or possibly create safety hazards.
To mitigate these challenges, several actionable solutions provide direct answers:
- Proper Selection: Research various available materials. Selecting the incompatible type can lead to frequent adjustments.
- Determine Load Requirements: Be sure to assess the weight and pressure each wire will sustain.
- Regular Maintenance Checks: Inspect cable tighteners routinely, which can prevent premature failure or misalignment.
“Safety should always be the priority. Regular checks on your installation safeguard against future problems.”
By approaching these common issues with active strategies, homeowners can position themselves for success and enhance the functionality of their systems.
Product Recommendations
When it comes to product recommendations, several brands showcase efficient wire cable tighteners in their portfolios. Here is a closer look into two notable contenders:
- Dstg: Known for its durable aluminum appliances, the brand offers ease of installation and reasonable prices. Each device efficiently manages cable tension, allowing for seamless adjustments.
- Klein Tools: Known for tackling tough jobs, their tighteners exhibit solid performance metrics due to innovative designs meant for industrial applications, extending durability and strength.
Utilizing these products can provide safety and reliability while elevating the performance of any installation. The ease of use and prolonged effectiveness are aspects that especially appeal to homeowners.
Step-by-Step Guides
For homeowners eager to tackle their own wire and cable situations, working with wire cable tighteners can become a formidable task if approached properly. Here’s a condensed overview of action-oriented steps one might undertake:
- Assess Requirements: Identify the spacing and tension required for your wires.
- Select Tighteners Appropriately: Ensure you choose a type compatible with the specifics of your project.
- Installation Process: Begin fittings by following these instructions closely:
- Test Reliability: After installation, apply more pressure to assess if the functions meet expectations.
- Iterate Maintenance!: Consider end of season checks lasting over time.
- Component Layout: Arrange detailed settings visually prior to mounting.
- Tension Implementation: Tightly fasten without striping to keep everything secure.
- Integrate Safety Mechanisms: Incorporating extra joint elements helps to further reinforce stability.
By converging on these key parts, one ensures that surrounding installations are reliable and viable for varied uses over time.
Prelude to Wire Cable Tighteners
Wire cable tighteners serve a pivotal role in system integrity across various applications, particularly in construction and electrical projects. Understanding the fundamental aspects of wire cable tighteners enhances clarity about their purpose, functionality, and significance in these operations. This introduction sets the stage for an informed approach toward selecting and using these tools effectively.
Definition and Functionality
A wire cable tightener is a device designed to apply tension to cables or wires. Its functionality resides in achieving the appropriate tension necessary for maintaining cable positioning and reducing vibrations. This is done while ensuring operational efficiency and safety. Tighteners can either adjust the tension gradually or lock it in place, depending on their design. Different types exist, each suitable for diverse applications and operational settings. By integrating these tools into cable systems, one can promote reliability and enhance overall effectiveness.
Importance in Various Industries
Wire cable tighteners are essential in multiple industries, from construction to marine applications. Their role extends further into telecommunications and energy sectors as well. To narrow down, here’s a brief outline of their importance:
- Construction: Ensuring safety and structural integrity in building projects is crucial. Tighteners help manage cable systems within frameworks, contributing to stability.
- Electrical: In electrical fields, maintaining tension prevents accidental disconnection, which safeguards both professionals and the public.
- Transportation: In shipping and logistics, wire tighteners secure cargo, addressing safety and logistical concerns.
Utilizing wire cable tighteners not only fosters safety but also standardizes workspace protocols, leading to an overall enhancement in project outcomes.
Types of Wire Cable Tighteners
Understanding the types of wire cable tighteners is vital for anyone engaged in projects where the strength and durability of cables play a critical role. Different environments and loads call for specific types of tighteners, and the right selection can significantly enhance efficiency and safety. Each type has unique characteristics that cater to different applications. Addressing these variations ensures optimal usage and longevity of the tightening mechanisms.
Mechanical Tighteners
Mechanical tighteners are straightforward devices that utilize physical principles to create tension. They often take the form of a screw mechanism or a lever system. These tighteners are favored for their durability and simplicity. They can withstand substantial loads and are less likely to fail compared to more complex systems, thus providing reliability in essential applications.
Benefits of Mechanical Tighteners
- Ease of Use: These tighteners do not require advanced knowledge to be applied effectively, and thus they can be used by individuals with varying skill levels.
- Cost-Effective: Being less complicated, mechanical tighteners typically cost less to produce and replace than hydraulic or automatic systems.
- Low Maintenance: They can operate efficiently with minimal mechanical parts needing regular adjustments, translating to lower maintenance needs.
Despite these benefits, mechanical tighteners may lack the fine control offered in hydraulic systems, which might be necessary for highly specific applications.
Hydraulic Tighteners
Hydraulic tighteners take advantage of fluid mechanics to generate tension. These devices use pressurized fluid to create tension and they can apply more force than mechanical models. As a result, they are commonly used in heavy-duty applications, such as construction and maintenance of industrial equipment.
Advantages of Hydraulic Tighteners

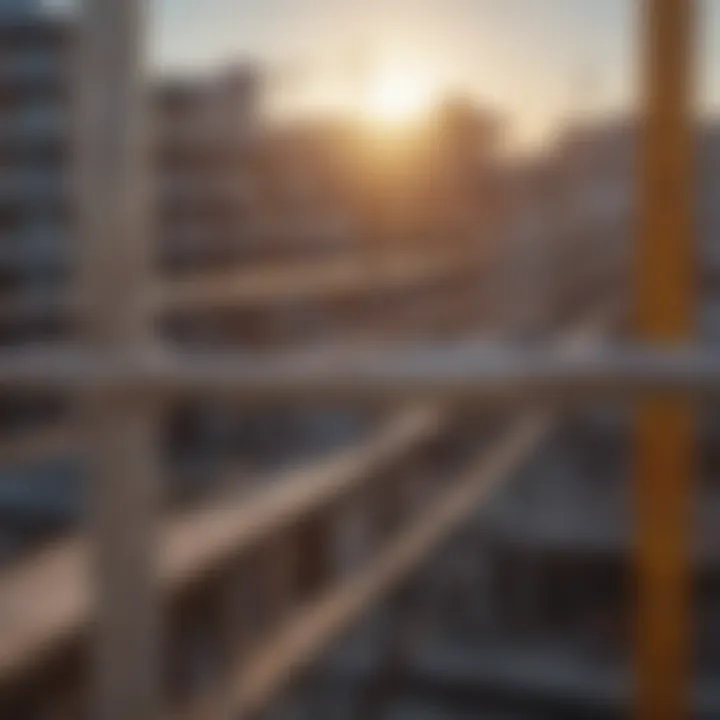
- High Load Capacity: These tighteners handle substantially heavier loads than their mechanical counterparts, making them suitable for demanding environments.
- Greater Control: Users can achieve precision in tensioning features, minimizing the risk of cable slippage.
- Fast Operation: Hydraulic systems can tighten cables quickly, which is advantageous during projects that run against time constraints.
However, they do require specific skill set for operation, as improper handling may lead to malfunctions.
Automatic Tighteners
Automatic tighteners represent the next stage in wire cable fastening technology. Designed to operate without manual intervention, these systems often involve electronic components and advanced technologies. They are typically used in environments where consistency and reliability are crucial over manual adjustment.
Benefits of Automatic Tighteners
- Consistency: The precision of automatic systems guarantees a uniform tension across all cables, an important factor in maintaining structural integrity.
- Independence: Operators can focus on other tasks as these systems manage the tightening autonomously. This feature increases efficiency on job sites.
- Integration with Technology: Modern automatic tighteners can often connect to monitoring systems to give real-time feedback on cable status.
Nonetheless, the reliance on electronic components may make these systems more susceptible to damage under adverse conditions, such as exposure to moisture or extreme temperatures.
Selecting the Right Wire Cable Tightener
Selecting an appropriate wire cable tightener is crucial in ensuring the efficiency and safety of any project. A well-chosen tightener can provide optimal performance and avoid unforeseen failures. Many parameters play a role in making this decision. Factors such as load capacity, environmental conditions, and compatibility with different cable types deserve careful consideration.
Load Capacity Considerations
When selecting a wire cable tightener, load capacity must be examined. It defines how much weight the tightener can effectively manage. If the load exceeds this capacity, the risk for failure enhances greatly, leading to project setbacks or potential hazards. Each tightener comes with specific load ratings, generally stated by the manufacturer. Failures commonly stem from underestimating or ignoring these limits. As a thumb rule, always assess the total weight and distribute loads evenly. When in doubt, consult the guidelines provided by the tool manufacturers.
- Before purchase, check:
- Manufacturer specifications
- Weight distribution
- Safety factors
By doing this, one can avoid selecting a tightener that is inadequate for task demands. Always err on the side of caution when dealing with heavy loads, prioritizing safety above all.
Environmental Conditions
Environmental factors heavily influence the efficiency and durability of wire cable tighteners. The exposure to weather elements, such as moisture, temperature variations, or chemical substances, can expedite wear and tear. Some tighteners are designed specifically for harsh environments, while others suit standard conditions well.
Consideration of these factors can inform choices:
- Humidity levels
- Temperature extremes
- Presence of corrosive agents (like salt or solvents)
Using a tightener unsuitable for the expected conditions leads to issues ranging from poor performance to sudden failures. Additionally, proper protective coatings and materials should feature in your selection choice, aiding in prolonging the lifespan of the tool.
Always align your selection with the expected environmental challenges, ensuring your tighteners remain capable and reliable.
Compatibility with Cable Types
Different cable types require specific tighteners for effective performance. Simple selections often lead to inefficient securing or even cable damage. Each tightener has variations best suited for particular materials and thicknesses. Factors to consider include:
- Type of wire: Metal, plastic, or composite wires may need distinct tighteners.
- Diameter: Ensure the appropriate grip for the cable’s size to avoid unnecessary slippage or damage.
- Cable tension needs: Some applications may necessitate higher tension while others do not require much stress at all.
Select a tightener designed explicitly for the chosen cable type yields better operational results. In situations where belligerent cords or hoses find use, ensuring compatibility ensures less issue with performance and increases safety over time.
Choosing wisely by keeping in mind these elements are paramount. Over time, careful and informed decisions creates longevity within your projects, bringing better outcomes for intended assembly.
Installation Techniques for Wire Cable Tighteners
Installation techniques are crucial for the effective use of wire cable tighteners. Proper installation ensures that cables are tensioned correctly, leading to enhanced stability and safety in various applications. This section delves into the essential steps involved in preparing cables, mounting tightening systems, and ensuring proper tensioning mechanisms are in place. Each technique plays a role in extending the lifespan of the installation and optimizing performance, making it essential knowledge for homeowners.
Preparation of Cables
Prepare the cables adequately before using wire cable tighteners. Begin by inspecting the cables for any damages or defects. Damaged cables may lead to failures during tensioning, jeopardizing both safety and effectiveness. Make sure to clean the cables to remove dirt or grease, which can interfere with the tightening mechanism.
It is also important to cut the cables to the necessary length based on the specific project needs. Having cables cut precisely helps enhance performance once they are tightened. If you need multiple cuts, be sure each piece matches your required specifications. Marking the cables beforehand can be quite helpful, ensuring accurate cuts and installation.
Mounting Procedures
Once the cables are prepared, the next step involves the correct mounting of the wire cable tightener system. Accurate mounting goes hand-in-hand with achieving the right tension. Begin by determining the points where the tightener will be installed. Generally, tighteners should be positioned where tension changes occur, commonly where cables cross or loop.
After establishing the mounting points, use appropriate mounting tools to secure the tightener in place. Ensure to tighten the screws and bolts properly but be aware of over-tightening as it may lead to damages. Depending on the project scale, it may also be useful to consult manufacturer specifications for correct installation processes specific to the products used.
When available, use templates or mounting guides to aid in efficient placement. These tools can simplify the alignment process, ensuring the correct angel and fit needed to maximize the effect of the tensioning process.
Ensuring Proper Tensioning
Ensuring proper tensioning is the final stage in the installation technique of wire cable tighteners. Too much tension can cause wear, while too little can result in slippage, making it crucial to find a balance. To assess tension post-installation, an initial inspection of the cable's tension is essential by employing tension meters or other measuring tools suited for the load involved.
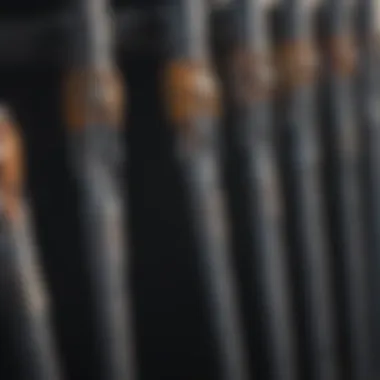
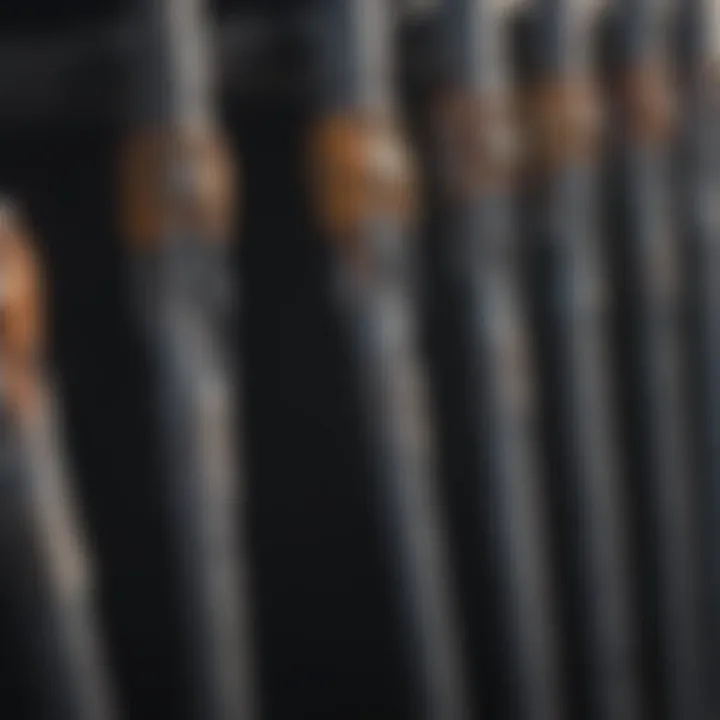
Monitor adjustments on the tightener gradually. After achieving desired tension, perform thorough checks to guarantee everything is stable. Continuous monitoring during the usage phase will help stabilize the setup as environmental changes may cause shifts in tension.
In summary, the steps involve accurately preparing cables, securely mounting them, and diligently ensuring proper tensioning. Each step builds upon the previous one, reinforcing the effectiveness of wire cable tighteners. Correctly applying these installation techniques not only maintains integrity and safety in applications but also enhances the overall reliability of projects.
A careful approach during the installation phase is as important as the chosen type of wire cable tightener; overlooking any step can lead to significant implications down the road.
Maintenance of Wire Cable Tighteners
Maintaining wire cable tighteners is a critical aspect of ensuring their longevity and functionality. Routine maintenance prevents expensive repairs or replacements and guarantees safety during operations. Components of these systems can wear down over time, affecting their performance and requiring attention.
Routine Inspections
Conducting regular inspections is essential. These inspections should focus on:
- Visual checks: Look for any signs of damage, rust, or wear. It's especially important to check connectors and clamps for any visible issues. If any irregularities are noticed, it is best to address them promptly.
- Functional checks: Verify that the tighteners are operating as intended. Apply and release tension periodically to ensure response is smooth and consistent. Inconsistent action might indicate internal issues needing repair.
Inspections should be done more often if the environment is harsh or if the equipment is in constant use. Proper inspection schedules can influence the operational lifespan positively.
“Regular inspections can extend the life of your wire cable tightener and ensure its effectiveness during use.”
Cleaning Procedures
Cleaning keeps the wire cable tighteners in good shape. Debris, dirt, and grit can build up and negatively affect functionality. Proper cleaning steps include:
- Use a soft brush: Clean surfaces gently to avoid scratches and damage. Recommended materials include:** Cloth or brush that won't cause scratches** to avoid further wear.
- Mild detergents: Only mild cleaning agents should be used. Avoid aggressive chemicals, as these can damage critical components.
- Thorough rinse: Ensure all residues from cleaning solutions are completely washed away. Leftover products may interact with the materials, causing degradation over time.
Keeping tighteners clean reduces risks of component failure and improves the overall operational appearance.
Lubrication and Wear Monitoring
Effective lubrication plays a significant role in the maintenance of wire cable tighteners. It need to be a routine part of their upkeep. Key points to remember include:
- Choose appropriate lubricants: Using and applying correct lubricants is vital. Not every lubricant is ideal, as some can lead to excessive buildup or harmful residue.
- When to lubricate: Frequent checks for lubrication are needed. If moving parts feel
Safety Considerations
Safety is paramount in any task that involves wire cable tighteners. Whether one is in a construction site or working on electrical installations, adhering to safety protocols can prevent accidents and save lives. Wire cable tighteners are essential tools, but improper usage can yield significant risks. Melded with both operational efficiency and worker safety, understanding specific safety elements linked to wire cable tighteners grants not only optimal performance but also peace of mind.
Personal Protective Equipment
Using the appropriate personal protective equipment (PPE) is critical when operating wire cable tighteners. Key items include:
- Safety glasses - To shield eyes from flying debris or potential cable snapping stories due to inappropriate tensioning.
- Gloves - Heavily padded gloves can protect hands, offering grip while reducing the risk of cuts.
- Hard hats - In a construction site, wearing hard hats can prevent head injuries from falling objects.
- Steel-toed boots - Essential for foot protection against heavy machinery or loads that may fall.
Training staff on the correct use of PPE not only safeguards physical health but instills a culture of safety in the workplace. Accidents can stem from lack of preparation or carelessness, which proper equipment can alleviate vastly.
Load Limit Awareness
Understanding and respecting load limits for wire cable tighteners is indispensable. Exceeding the designated load can lead to equipment failure or, worse, tragic accidents. Familiarizing oneself with specifications set by manufacturers enables proper usage. Some considerations include:
- Read vendor guidelines - Consult the datasheets and know the rated capacities of the specific tightener in use.
- Balance loads - Ensure that loads are uniformly distributed whenever applicable to maintain stability.
- Regularly monitor wear and kryptonite - Actively check that the applied load does not increase as cables settle over time.
Promoting awareness of load limitations among employees enhances the likelihood of minimizing workplace injuries and maintaining operational integrity. A clear understanding not only contributes to better safety but also prolongs the life of the equipment.
Risks of Improper Installation
Many accidents involving wire cable tighteners stem from improper installation. Even seasoned professionals may overlook nuances during the installation phase. Critical risks of inadequate installation include:
- Cable slippage - This can occur from misaligned or improperly secured tighteners, leading to loose cables affecting overall stability.
- Structural failure - Poorly anchored cable tighteners can result in component failures, leading to catastrophic incidents.
- Injury - Workers positioned nearby may face danger from equipment that dislodges due to incorrect tension.
To mitigate these issues, it’s crucial to adhere to installation protocols. Following recommended guidelines significantly decreases the aforementioned risks while maximizing efficiency in operational capacities.
Safety must be the priority; taking shortcuts can have serious long-term consequences.
Common Issues with Wire Cable Tighteners
Wire cable tighteners are pivotal in maintaining the integrity of various cable infrastructures. However, they are not without problems. If these issues are neglected, the results can compromise both safety and performance. Here we explore some common challenges, such as slippage, wear and tear, and improper installation, which highlight the need for diligence and care in usage and maintenance.
Slippage Problems
Slippage occurs when cables do not maintain the necessary tension during their operation. Several factors contribute to this issue. One prominent factor is insufficient load or incorrect tensioning. When the tension on wire cables is too low, they can shift from their designated positions.
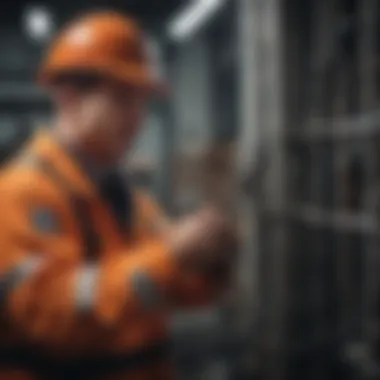
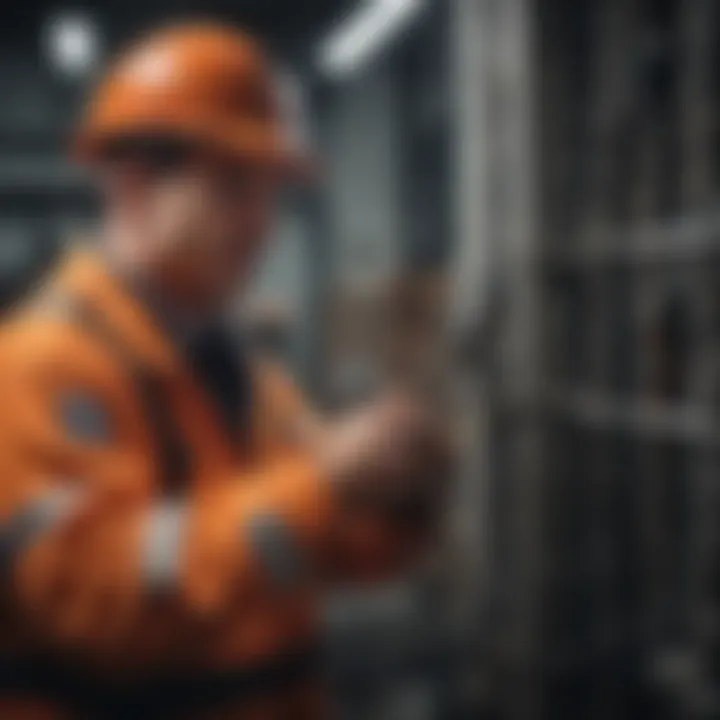
In addition, variations in environmental conditions can affect tighteners ability to hold securing tension. Temperature changes might expand or contract materials, leading to unexpected shifts. For instance, if a bolt or clamp holding a cable is not secured properly, the cable could easily start slipping. To prevent slippage, it is essential to monitor the setup actively and perform regular checks.
"Proper tensioning is crucial for ensuring that cables do not slip. Regular maintenance blocks many such issues."
Wear and Tear
Over time, wear and tear contribute significantly to failure in wire cable tighteners. Cables continuously bear weight and resist dynamic forces. However, overextending demands on tighteners or using low-quality components can result in premature degradation. Metal parts are especially prone to rust or corrosion when exposed to moisture without proper protection.
Signs of wear can manifest as fraying cables, weakened clamps, or degraded materials overall. Operators should assess any tightener setups for such deteriorations frequently. Scheduled inspections are key to catching wear before it becomes a dangerous problem.
Regular cleaning and appropriate lubrication will prolong the life of these tighteners. They can effectively minimize the effects of wear if done frequently.
Installation Errors
Installation mistakes must be strictly avoided to ensure the effectiveness of wire cable tighteners. Errors in alignment or imprecise mounting can lead to asymmetric tensions.
If a tightener is not installed according to the manufacturer’s guidelines, or if it experiences irregular stress due to poor cable placement, it can worsen performance. Operators must follow installation instructions with precision.
Thorough training or familiarization with best practices can reduce the likelihood of making installation errors. Using useful tools and checking twice before final tightening are practical measures.
Holistic training aids in understanding not only how to install but also how each component interacts within a larger system. By giving attention to common pitfalls, users can greatly mitigate potential failures related to wire cable tighteners.
Innovations in Wire Cable Tightening Technology
Innovations in wire cable tightening technology are reshaping how we approach cable installations and maintenance. These advancements offer not just convenience, but significant improvements in safety, efficiency, and performance across different industries. As projects grow more complex, having sophisticated tools that enhance cable management becomes increasingly paramount. Innovators in wire cable tighteners prioritize developing systems and materials that address specific challenges faced in various applications.
Smart Tightening Systems
The rise of smart tightening systems represents a major shift in tensioning technology. These systems leverage sensors and digital feedback to monitor the tightness of cables in real-time. By implementing smart technology, users can significantly reduce the risk of under-tightening or over-tightening. This feature is pivotal in ensuring that installations meet specific load requirements and comply with safety standards.
Benefits of smart tightening systems include:
- Real-time Monitoring: Continuous feedback allows for immediate adjustments if tension exceeds the set limits, reducing failure risks.
- User-Friendly Interfaces: Modern systems typically come with intuitive controls, making it easy for workers to monitor cable tension with minimal training.
- Data Collection: Many smart systems document tightening history, which helps with audits and future installations.
When understanding the long-term benefits, these innovations save time and resources. They mitigate risks associated with human error, allowing teams to focus on other critical aspects of their projects.
Material Advancements
The choice of materials in wire cable tightening technologies ranks as a fundamental aspect of innovation. New materials are being developed regularly, impacting performance and longevity which translates directly to better user experience and reduced operational costs.
Some notable advancements in materials include:
- High-Strength Alloys: These materials provide enhanced durability and weight-to-strength ratios, suitable for demanding environments.
- Corrosion-Resistant Coatings: Many tightening systems now feature coatings that resist wear and tear due to harsh environmental conditions. This is particularly beneficial for outdoor applications where exposure to moisture and other elements is common.
- Lightweight Composites: Reduction in weight can ease installation processes and lessen shipping costs. Using composites offers flexibility that is often not achievable with traditional metals.
"Adopting best practices from industry advancements can lead to a much safer and efficient work environment, benefiting both workers and projects alike."
Case Studies: Successful Applications
Understanding the practical applications of wire cable tighteners through case studies enriches the reader's knowledge. Case studies highlight how these tools perform in real-life scenarios. They showcase the functionality of wire cable tighteners in various environments. Additionally, they offer insights into best practices that can be applied across different industries.
Industry-Specific Examples
When considering cake studies, examining industry-specific examples serves as terrific for unvailing how wire cable tighteners adapt to various settings. Here are few examples:
- Construction Projects: In recent residential developments, wire cable tighteners worked as integral part of the structural integrity of essential installations, such as tension support systems. Safety issues associated with slippage were mitigated through the use of these precise tools.
- Telecommunications: In telecommunications, tighteners enhance cable stability during wind and other environmental factors. A specific scenario involved a utility provider replacing old infrastructure. They installed new support systems to securely hold high voltage cables, ensuring uninterrupted service across regions.
- Maritime Applications: On ships, wire tighteners secure rigging and lifelines effectively. A cruise ship faced extensive chassis fatigue due to heavy wind. The deployment of hydraulic tighteners prevented structural damage maximal stress areas, reinforcing overall safety and dependability.
These examples support a deeper grasp of not only the types of tighteners available but also the consequences of aligning with their advanced features in real-world operations.
Lessons Learned from Projects
Extracted lessons from these case studies are crucial for practical applications. Important insights include:
- Importance of Pre-planning: Each project emphasizes the necessity of initial site assessments and planning. Understanding load requirements and environmental factors can drastically say what type of tightener to use.
- Maintenance Protocol Lessons: Consistent upkeep not only prolongs the lifespan of tighteners but also prevents unforeseen issues from arise during operations. This finding proves cost-effective in long term.
- Training and Familiarity with Equipment: Knowledge distributed among teams played a few key roles in seamless operations. Team members trained with specific wire cable tighteners exhibited better results than those unfamiliar with their use.
Continuous improvement of understanding applied in various industries emphasizes the fact that the success stories serve as the basis for strategy and future project execution.
Reflecting on successful applications of wire cable tighteners informs decision-making strategies. Each case study enriches the understanding of importance these tools present across diverse fields.
Ending
Recap of Key Points
In summarizing the insights from this discussion, several core elements about wire cable tighteners become clear. They are crucial for maintaining tension in cables across various applications, ensuring both safety and effectiveness. Wire cable tighteners come in different types, such as mechanical, hydraulic, and automatic, each serving specific situational needs. Regular maintenance through inspections and proper installation techniques is necessary for their longevity. Selected based on load capacity and environmental considerations, ideal tighteners can significantly reduce the risks associated with misuse.
Future Outlook for Wire Cable Tighteners
As industries continually evolve, the future for wire cable tighteners appears promising and dynamic. Emerging technologies aiming at smarter and more efficient tightening mechanisms are developed. Intelligent systems that predict and adjust tension in real-time could be game-changers. Also, sustainable materials may enhance performance while considering environmental impact. The growing necessity for safety and efficiency will drive ongoing innovations in the design and application of wire cable tighteners, making them even more indispensable tools in both construction and other practical fields.