Understanding Pipe Burring Reamers: A Comprehensive Exploration
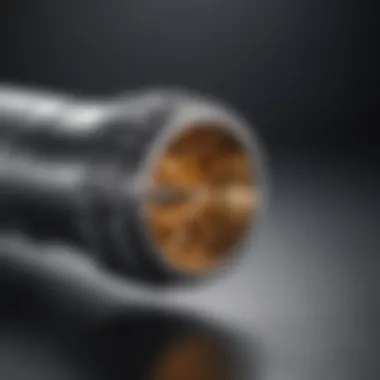
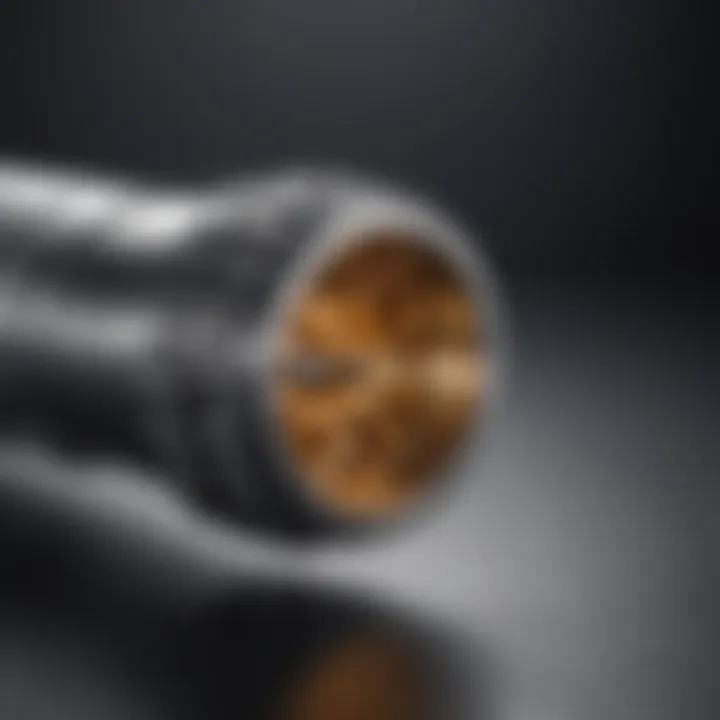
Intro
Pipe burring reamers are tools often overlooked in the home improvement industry. They serve a specific yet crucial purpose in the preparation of pipe edges. This section provides an initial understanding of what pipe burring reamers are, how they work, and why they are significant in both minor home repairs and major industrial applications.
Overview of Topic
In the world of home improvement, precision is key. Pipe burring reamers are designed to create smooth, deburred edges on pipes. This action helps to prevent damage and allows for better fitment when connecting various plumbing components.
Understanding this tool is essential for any homeowner or DIY enthusiast working on plumbing or related projects. Not only does it facilitate improved installation, but it also enhances the overall durability of the pipe systems in use.
Given the rising popularity of DIY home improvement projects, it is important to recognize the role of such specialized tools in fostering better outcomes.
Importance of the Topic
The importance of understanding pipe burring reamers extends beyond personal use. In industrial scenarios, the quality of tools directly influences the effectiveness of work undertaken. For instance, in precision engineering and manufacturing, utilizing an effective reamer can reduce the possibility of leaks and malfunctions in piping systems.
Furthermore, proper knowledge of the tool helps in selecting the right one for the job, maintaining it correctly, and ultimately ensuring safety and functionality in the long run.
"The right tool can make or break a project; pipe burring reamers are no exception."
Next, we will delve into common challenges associated with using burring reamers, along with practical solutions.
Preface to Pipe Burring Reamers
Pipe burring reamers are specialized tools that play a crucial role in various industries. Their primary function is to smoothen and refine the edges of pipes after cutting, ensuring an optimal fit for connections. This process is important because it prevents damage to both the pipe and the fittings, thus enhancing the overall integrity of the plumbing or mechanical system.
In this article, we will explore the intricate details that define pipe burring reamers, delving into their history, construction, and operational principles. Understanding these elements is vital for both professionals and enthusiasts looking to harness the full potential of these tools.
The section will cover their working mechanisms, the types available, and how they select between different materials based on the application. Each of these details contributes to a comprehensive understanding of pipe burring reamers, making it easier to appreciate their significance in improved work quality and time efficiency in tasks.
Defining Pipe Burring Reamers
Pipe burring reamers are designed specifically to remove burrs from the inner and outer edges of a pipe. The term "burring" refers to the creation of raised edges or rough surfaces that can occur when a pipe is cut. These reamers help to remove those imperfections, resulting in smooth surfaces that ensure proper sealing when fittings are applied.
Typically, these reamers come in various shapes and designs, each tailored to specific types of pipes. For instance, some are suited for metal tubing, while others accommodate plastic pipes. It is noteworthy that the operation involves rotating the tool against the pipe edge, where the cutting edges of the reamer engage the material, removing any burrs effectively.
History and Evolution of Reaming Tools
The origins of reaming tools can be traced back centuries. Initially, reaming was done manually using basic hand tools. With advancements in technology, these tools evolved into the more precise and efficient designs we see today. Traditional reamers were simple, while modern pipe burring reamers feature complex geometries that improve cutting performance.
As industries expanded, the demand for high precision tools grew. Innovations in materials also influenced the evolution of burring reamers. Early tools were often forged from softer metals, making them prone to wear. Today, many reamers are made from high-speed steel or carbide, offering greater durability and cutting efficiency.
In essence, the evolution of pipe burring reamers reflects broader technological advancements in manufacturing and engineering. Their design has continuously improved to meet the changing demands of various applications.
Key Components of Pipe Burring Reamers
Understanding the key components of pipe burring reamers is essential for anyone involved in plumbing, HVAC repairs, or manufacturing. These components play a vital role in how effectively and efficiently the reamer performs its function. Every aspect, from the material used to the design of the cutting edges, contributes to the overall precision and usability of the tool. By focusing on these elements, users can make informed decisions when selecting a pipe burring reamer, ensuring they choose a tool that best fits their specific needs.
Cutting Edges and Geometry
The cutting edges of pipe burring reamers are critical to their functionality. They determine not just how much material can be removed, but also the quality of the finish on the pipe edges. Generally, a sharper edge can cut through materials with less resistance. Though some may overlook the significance of geometry, it is essential. The angle and shape of the cutting edges influence the amount of friction generated during operation. An optimal cutting edge geometry enhances the cutting efficiency, which translates to reduced wear on the tool. Furthermore, a well-designed edge can help prevent common issues like chattering, which may lead to poor results and wear.
Key Takeaways:
- Cutting edges dictate the effectiveness of the reamer.
- Optimal geometry increases efficiency and reduces tool wear.
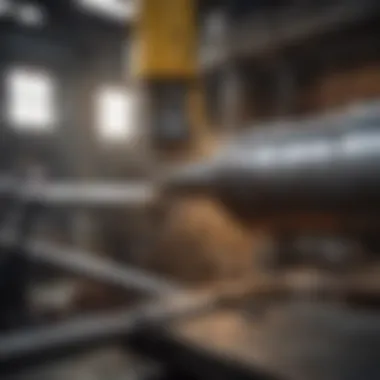
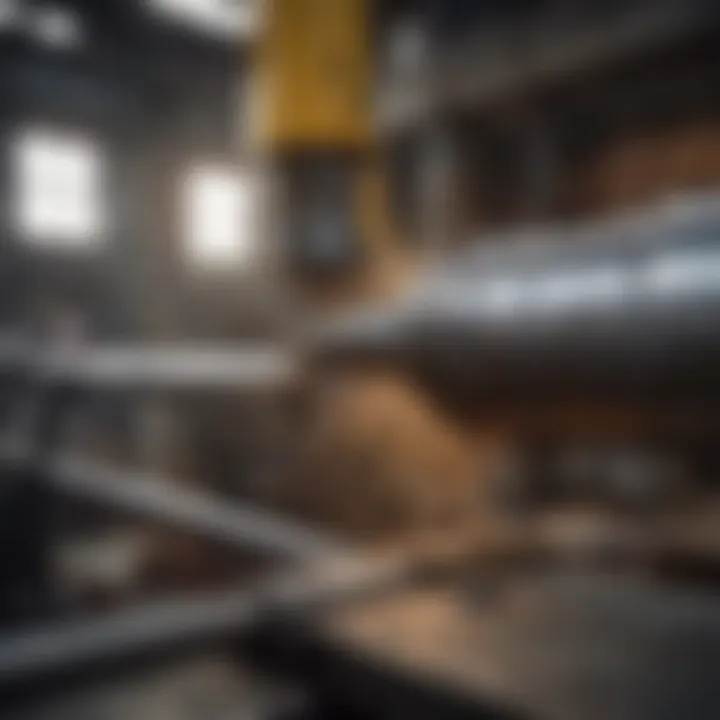
In addition, reamers may feature different types of cutting edges tailored for specific materials. For instance, tools designed for soft metals might have rounded edges, while those intended for harder materials could possess sharper, more aggressive angles. This adaptability helps users select the right tool for their particular tasks, resulting in better performance overall.
Shank Types and Their Importance
The shank is another significant component of pipe burring reamers. It connects the reamer to the drilling or reaming machine, creating stability during operation. Different shank types can affect the reamer's usage and compatibility with various machines. Common shank types include straight, tapered, and threaded versions. A straight shank is suitable for most standard machines, providing easy attachment and stability. However, tapered shanks offer better grip within the machine, making them ideal for heavy-duty applications. Threaded shanks provide versatility, allowing users to interchange with different extensions and adapt to various tasks as needed.
Selecting the right shank type ensures the tool operates smoothly. An inappropriate shank can lead to chattering or ineffective burring, causing undesirable results. Optimal shank selection therefore contributes to improved performance and efficiency, which is vital for high-quality workmanship in both home projects and industrial settings.
In summary, the cutting edges and the shank types of pipe burring reamers are foundational to their effectiveness and applicability. Understanding these components allows users to select tools that better meet their specific requirements, thereby enhancing their overall experience and efficiency during use.
Operational Principles of Pipe Burring Reamers
The operational principles of pipe burring reamers are central to understanding their functionality and the benefits they offer in various applications. At their core, these tools are designed to refine the edges of pipes, contributing to both aesthetics and safety. The significance of a proper operation cannot be overstated. It directly influences the effectiveness of the reaming process, the longevity of the tools, and the quality of the finished product.
Mechanics of Burring
Burring is the process where the edges of metal or other materials are smoothed out to prevent sharp edges that could cause injury or damage. When a pipe undergoes cutting, it typically leaves behind burrs—jagged edges formed during the process. Pipe burring reamers utilize sharp cutting edges to eliminate these burrs effectively.
The mechanisms behind burring involve a rotating tool that engages the internal or external surface of the pipe. This engagement creates a shearing action that removes excess material. - The design of the cutting edges is crucial; they must be sharp and positioned at the correct angles to optimize the cutting efficiency. The geometry of the reamer influences how smoothly it moves through the pipe, affecting both the quality of the burring and the amount of force needed.
Effect of Speed and Feed Rates
Speed and feed rates are essential parameters in the operation of pipe burring reamers. Speed refers to the rotational velocity of the reamer, while feed rate denotes how quickly the tool moves through the pipe.
- Rotational Speed: Higher speeds can increase efficiency but may lead to overheating or rapid tool wear if not monitored properly. Monitoring is essential to maximize both performance and tool life.
- Feed Rate: This involves how fast the tool is advanced into the material. A slower feed rate allows for more controlled machining, which can produce a finer finish but may also take longer. Conversely, a rapid feed rate might increase productivity but could compromise the finish quality.
Achieving the right balance between these variables is key. It impacts the burr quality, the extent of finishing needed afterwards, and the durability of the burring reamer itself. Adjusting both speed and feed requires careful consideration based on the material being worked on and the desired outcome.
"The efficiency of pipe burring largely relies on the precise adjustment of both speed and feed rates, promoting optimal tool performance."
Combining the knowledge of mechanics of burring with the understanding of speed and feed rates results in a profound appreciation of how pipe burring reamers operate. This knowledge not only empowers contractors and DIY enthusiasts alike but also emphasizes the importance of precision in achieving the desired results.
Types of Pipe Burring Reamers
Understanding the types of pipe burring reamers is essential for anyone looking to enhance their tool collection or improve their precision in various tasks. These tools are not just about drilling holes; they play a significant role in the overall quality of the work. Key considerations in the types of burring reamers include the specific applications, the precision they offer, and their ease of use in various environments. Choosing the right type can greatly impact the effectiveness and efficiency of plumbing or manufacturing processes.
Standard versus Adjustable Reamers
Standard reamers provide a fixed cutting diameter, making them ideal for repetitive tasks where consistency is crucial. For example, in plumbing installations, using a standard reamer ensures that all connections are uniform, which can prevent leaks. These tools are often easier to use since they do not require adjusting.
On the other hand, adjustable reamers offer versatility, as they allow the user to modify the cutting diameter to suit different pipe sizes. This adaptability can be beneficial in situations where multiple sized pipes are handled, providing a tailored approach. However, the use of adjustable reamers does demand a higher skill level, as improper adjustments may lead to uneven cuts, affecting the integrity of the installation.
Usage of Carbide versus High-Speed Steel Reamers
When selecting between carbide and high-speed steel reamers, the material choice hinges on the intended application. Carbide reamers are known for their hardness and durability. They are well-suited for harder materials, ensuring a longer service life and superior performance in rigorous tasks. Their rigidity allows for high precision and minimal wear, making them ideal for industrial applications where durability is paramount.
High-speed steel reamers, while less durable than their carbide counterparts, offer greater flexibility and ease of sharpening. They are typically favored in situations where materials are softer or when cost is a concern. This type of reamer provides a great balance between performance and affordability, making them suitable for light to moderate usage scenarios.
In summary, selecting the appropriate type of pipe burring reamer is crucial. Depending on the task, whether installing plumbing fixtures or performing industrial fabrications, understanding both standard versus adjustable and carbide versus high-speed steel options can provide users with the right tools to achieve optimal performance.
Applications of Pipe Burring Reamers
Pipe burring reamers serve vital functions across various industries. Understanding the applications can highlight their significance and benefits. This section explores their use in plumbing, HVAC, manufacturing, and fabrication sectors. The precision and efficiency of these tools contribute greatly to the quality of work in each field.
Applications in Plumbing and HVAC
In plumbing and HVAC installations, the use of pipe burring reamers is critical. These tools help ensure clean edges on pipes, which is essential for proper fitting and sealing. When edges are burring-free, the connection between pipes becomes more effective. This reduces the risk of leaks and improves overall system efficiency. For example, when installing copper pipes, using a burring reamer smoothens the edges after cutting. This prevents debris from obstructing the flow of water or gas.
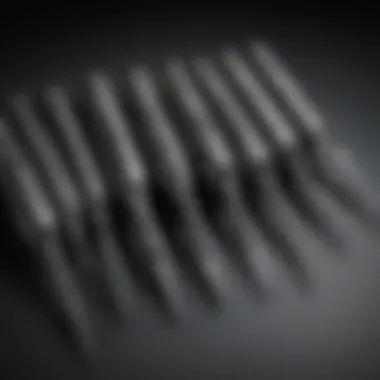
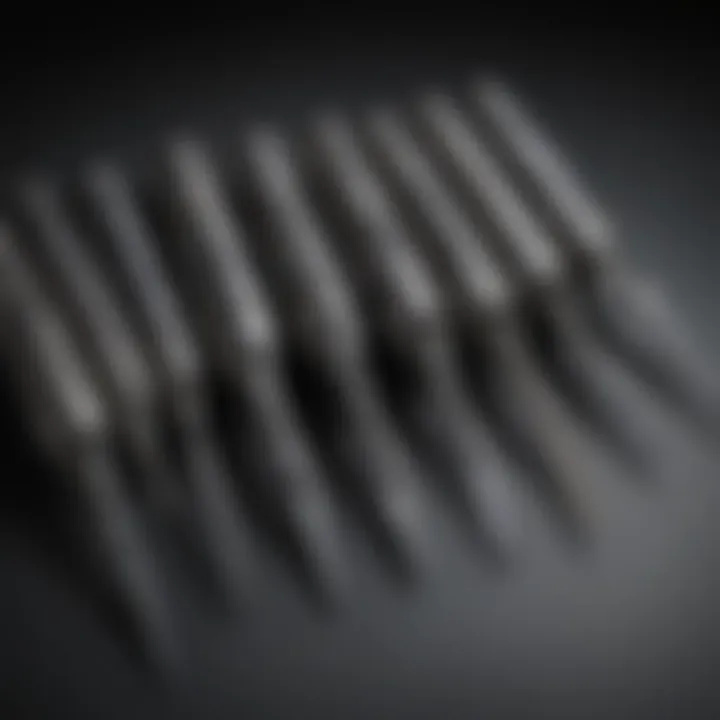
Furthermore, well-reamed pipes are easier to install and often require less force during the joining process. As a result, both novice and experienced plumbers benefit from using these tools. It's not just about performance; safety plays a role as well. A sharp pipe edge can cause injuries. Smooth edges created with a burring reamer contribute to a safer work environment.
Use in Manufacturing and Fabrication
In manufacturing and fabrication, pipe burring reamers are essential during the production process. They allow for precise finishing of components, which is crucial in fields such as automotive and aerospace. Without proper finishing, components may fail during use, leading to costly errors and potential safety hazards. By removing metal burrs, manufacturers can enhance the integrity of the final product.
Moreover, these reamers enable better alignment. When assembling sections of a machine or structure, the ability to align parts accurately is paramount. The reaming process ensures that all pieces fit together seamlessly, which can significantly reduce assembly time. This is crucial in fast-paced production lines where efficiency is key.
Some considerations for using burring reamers include selecting the right material for the job. For instance, carbide reamers are often preferred in industrial applications due to their hardness and durability. High-speed steel reamers serve well in less demanding tasks. Each material has its own application realm, and understanding these can lead to optimal performance.
"Precision tools like pipe burring reamers are the unsung heroes in ensuring the integrity of piping systems across various industries."
In summary, the applications of pipe burring reamers are wide-ranging and impactful. From plumbing and HVAC to manufacturing and fabrication, these tools not only enhance performance but also promote safety and achieve efficiency in operations.
Material Selection for Pipe Burring Reamers
Material selection is a fundamental aspect of crafting pipe burring reamers. The choice of material directly affects the performance, durability, and efficiency of the tool. Proper materials can handle the stresses during operation and ensure precision in tasks. Selecting the right material can significantly enhance the effectiveness of reaming processes across different applications.
Factors Influencing Material Choice
There are several factors to consider when choosing materials for pipe burring reamers:
- Cutting Performance: The material must possess suitable hardness and wear resistance. Harder materials maintain sharp edges for a longer time, which is critical for effective burring.
- Thermal Stability: During operation, friction generates heat. Selected materials should retain their properties under high temperatures to avoid deformation or failure.
- Corrosion Resistance: In environments where reamers come into contact with corrosive substances, it's important to choose materials that do not easily corrode.
- Cost-Effectiveness: Material choice should balance performance with cost. High-performance materials may be more expensive but could offer longer service life, leading to overall cost savings.
Comparative Overview of Reamer Materials
The two most common materials used for reamers are High-Speed Steel (HSS) and carbide. Each has distinct characteristics:
- High-Speed Steel (HSS):
HSS offers good toughness and is easier to sharpen. This material is suitable for general-purpose reaming. It can withstand high operation speeds and delivers decent performance in various conditions. However, it might wear faster under extreme conditions. - Carbide:
Carbide offers superior hardness and wear resistance. It is well-suited for heavy-duty applications and maintains sharp edges longer than HSS. The downside, though, is its brittleness; carbide can fracture under impact if not handled properly.
Maintenance of Pipe Burring Reamers
Proper maintenance of pipe burring reamers is crucial to ensure their longevity and efficiency. These tools are not only investments but essential equipment in various industries. Regular attention to maintenance practices can enhance the performance of the reamer, minimize downtime, and reduce operational costs. This section will delve into key aspects of maintenance, specifically cleaning and storage practices as well as sharpening techniques and tools.
Cleaning and Storage Practices
Cleaning is a fundamental aspect of maintenance for pipe burring reamers. After use, reamers can accumulate debris, metal shavings, and other contaminants. These remnants can affect the cutting edges and overall functionality of the tool. Ensuring the reamer is clean after every use helps maintain its precision and efficiency.
Some recommended cleaning steps include:
- Immediate Cleaning: After each use, clean the reamer with a soft brush or cloth to remove any debris. This prevents buildup that can cause wear.
- Use of Solvents: For tougher residues, solvents like mineral spirits can be applied. Make sure to rinse adequately afterwards.
- Storage Considerations: Store the reamer in a dry environment to prevent rust. Using a protective case or sheath can also help protect the cutting edges from damage.
It is advised to avoid stacking reamers without protection, as this can lead to nicks and dulling of the blades. In addition to cleaning, check for any signs of wear before storing them for an extended period. This proactive approach can avert costly repairs or replacements later.
Sharpening Techniques and Tools
Sharpening reamers is another important maintenance step that can greatly impact performance. Dull cutting edges can lead to inefficient burring and possible damage to the pipe itself. Proper sharpening techniques are necessary to restore the functionality of the tool.
There are several methods and tools specific to sharpening pipe burring reamers:
- Bench Grinder: This is a common tool used for sharpening. Set the reamer at the correct angle while grinding to ensure the cutting edges remain sharp.
- Honing Tools: For finishing touches, honing tools can be useful. They provide a smoother edge without removing too much material.
- Professional Sharpening Services: If unsure about sharpening techniques, seeking help from a professional could be the best route. They have the expertise and equipment to preserve the reamer’s integrity.
Regular inspection and sharpening will vastly extend the life of your burring reamers, ensuring they remain effective and reliable for future projects. Maintaining your tools is not just about keeping them functional; it is about preserving the quality of your work.
"Consistent maintenance of pipe burring reamers is essential for achieving precision and efficiency in pipework. Investing time in care will pay dividends in performance."
Industry Standards Affecting Pipe Burring Reamers
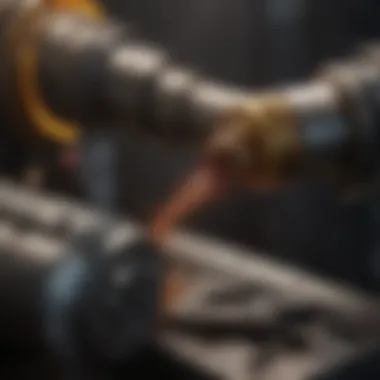
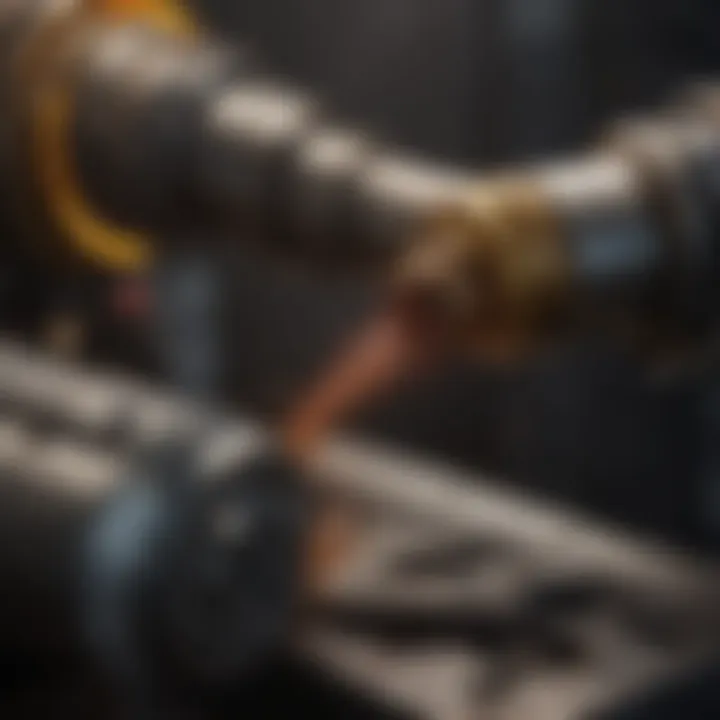
In the world of machining and tooling, industry standards serve as a foundation for quality, performance, and safety. For pipe burring reamers, adhering to these standards is not just a regulatory requirement; it is essential for ensuring that tools operate effectively and reliably in various applications. Understanding the importance of industry standards can help both manufacturers and users make informed decisions about the tools they choose.
Overview of ANSI and ISO Standards
ANSI, which stands for the American National Standards Institute, provides norms for tools such as pipe burring reamers, facilitating consistency and safety in manufacturing processes. This organization creates standards that cover the dimensions, tolerances, and materials used in tool production. On the other hand, the International Organization for Standardization (ISO) offers globally recognized benchmarks that many international manufacturers strive to meet.
Both ANSI and ISO standards influence several aspects of pipe burring reamers. Key points include:
- Dimension Specifications: Proper sizes ensure compatibility with different pipes.
- Material Characteristics: Standards define which materials are suitable for making durable reamers.
- Quality Measurement: These standards set expectations for performance and safety, contributing to effective quality assurance practices.
- Interoperability: Tools made to these standards can be used interchangeably, enhancing flexibility in procurement.
This adherence to industry standards not only improves product quality but also builds trust between manufacturers and users. For those looking to select pipe burring reamers, being aware of these benchmarks is crucial.
Compliance and Quality Assurance
Compliance with ANSI and ISO standards is integral to maintaining the reliability of pipe burring reamers. It ensures that all products are manufactured to consistent specifications, which diminishes the risk of failure during operation. Rigorous quality assurance processes, aligned with these standards, result in tools that can perform consistently over time.
Benefits of compliance include:
- Increased Safety: Standardized tools reduce the chance of accidents caused by tool failure.
- Enhanced Performance: Tools that meet industry standards are typically more efficient and effective in various applications.
- Market Trust: Products that are compliant are often regarded as higher quality, which can influence purchasing decisions.
Trends and Innovations in Pipe Burring Reamers
In the ever-evolving landscape of manufacturing and construction, trends and innovations in pipe burring reamers play a significant role. These advances not only enhance the performance of these tools but also contribute to greater efficiency and sustainability in various applications. It is essential to understand these trends as they reflect broader shifts in technology, material science, and production processes.
Emerging Technologies in Cutting Tools
The rise of smart technology is reshaping cutting tools, and pipe burring reamers are no exception. Innovations such as sensor integration allow for real-time monitoring of tool performance. This automation can alert users to potential issues before they escalate, leading to improved reliability and reduced downtimes. Furthermore, the implementation of computer numerical control (CNC) systems facilitates precise adjustments to tool specifications.
Another noteworthy advancement is the development of coating technologies that improve tool lifespan. For example, coatings such as titanium nitride provide enhanced durability and reduce friction. By minimizing wear, these coatings enhance the cutting capacity of reamers and deliver smoother finishes on pipes.
Next, the introduction of multi-functional tools is a trend gaining traction. These tools are endowed with capabilities to not only burr but also perform various reaming tasks. Such versatility is particularly beneficial in tighter workspaces where multiple tools may not be feasible.
Sustainable Practices in Manufacturing
Sustainability has become a central theme in manufacturing processes. Pipe burring reamer production is transitioning towards more environmentally responsible practices. One significant change involves the sourcing of materials. Manufacturers are increasingly opting for recycled or sustainably sourced metals. This effort reduces the ecological footprint associated with mining new resources.
Additionally, advancements in energy-efficient manufacturing techniques are gaining attention. Processes that minimize energy consumption during production not only lower operational costs but also contribute to a reduction in greenhouse gas emissions. Such practices align with global initiatives aimed at combating climate change.
Moreover, waste management practices have improved remarkably. By adopting a closed-loop system, manufacturers can recycle scrap materials generated during the production of burring reamers. This not only conserves raw materials but also reduces waste sent to landfills.
"Innovation in tool production processes is essential for meeting modern industry standards while focusing on sustainability."
In summary, the trends and innovations impacting pipe burring reamers highlight the industry's commitment to enhancing functionality while embracing sustainable practices. By staying informed about these changes, professionals can leverage cutting-edge tools that offer improved performance, reliability, and environmental stewardship.
Future Outlook for Pipe Burring Reamers
The future of pipe burring reamers is influenced by various factors, including technological advancements, market demands, and the evolving needs of industries. Understanding these elements is crucial. As industries seek to enhance productivity and precision, the role of burring reamers becomes more significant.
With continuous developments in material science and manufacturing processes, we can expect pipe burring reamers to incorporate more durable and efficient materials. These enhancements can lead to increased performance, reduced wear, and longer tool life. Moreover, as companies commit to sustainability, we may see innovations aimed at minimizing waste and improving energy efficiency in the production of these tools.
Anticipated Market Developments
In the upcoming years, the market for pipe burring reamers is predicted to experience notable changes. Trends indicate that demand will grow, driven by several sectors including plumbing, HVAC, and manufacturing.
- Technical Advancements: New materials and design methodologies will likely result in reamers that not only perform better but also meet the stricter regulations in place across different regions.
- Customization: There is a rising tendency toward customized reaming solutions. Industries may look for specific designs to optimize their operations according to unique requirements.
- Automation and Digital Integration: The future may involve more automated processes for using burring reamers. Digital tools for measuring and controlling the reaming process can enhance precision.
Continued Importance in Various Industries
Pipe burring reamers will continue to hold relevance in diverse industries. Their importance stems from the essential role they play in ensuring quality and precision in various applications. Some key areas where they remain critical include:
- Plumbing: In plumbing, the proper reaming of piping ensures smooth connections, reducing leak risks and promoting long-lasting installations.
- HVAC Systems: Heating, ventilation, and air conditioning systems also rely on effective burring to prepare pipes for assembly and ensure efficient airflow.
- Shipbuilding and Aerospace: High standards in shipbuilding and aerospace applications make the use of pipe burring reamers indispensable in creating secure and reliable fittings.
The adaptability of pipe burring reamers underscores their enduring significance as industries evolve and new challenges arise.