Enhancing Drilling Efficiency: The Role of Pumps
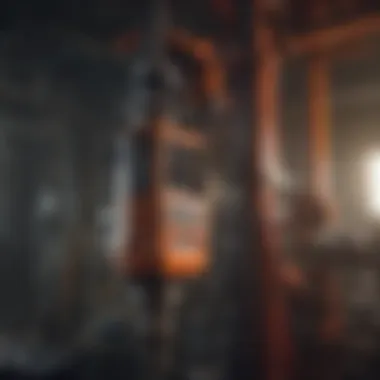
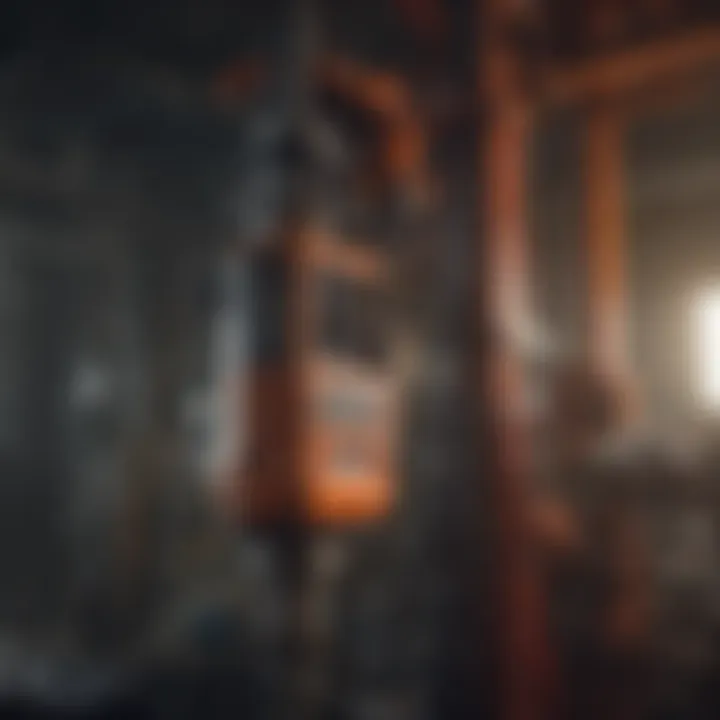
Intro
Overview of Topic
Pumps in drilling systems play a critical role in the operational efficiency of drilling projects. These devices transport fluids, such as water or drilling mud, to various parts of the drilling rig. Integrating the right pump into a drilling system can enhance performance, reduce downtime, and increase overall productivity.
The importance of this topic extends beyond mere functionality. Effective pumping solutions lead to optimized drilling processes. They aid in maintaining the pressure required for various drilling techniques and ensure the smooth flow of fluids necessary for effective job completion.
Common Challenges and Solutions
Homeowners and contractors alike encounter specific challenges when integrating pumps into drilling systems. Some of the most common issues include:
- Inadequate fluid flow: Often, the selected pump fails to provide sufficient pressure, leading to inefficient drilling.
- Maintenance difficulties: Pumps can suffer from wear and tear, leading to unexpected failures.
- Compatibility problems: A pump may not work well with existing drilling equipment, causing compatibility issues.
Solutions and Tips
To overcome these challenges, homeowners should consider several approaches:
- Evaluate pump capacities: Ensure the selected pump meets the required specifications for your drilling project.
- Regular maintenance checks: Set aside time for routine maintenance to prevent small issues from escalating.
- Consult experts: Seek advice from professionals who can recommend products that enhance compatibility with existing systems.
Product Recommendations
In examining pumps suitable for drilling applications, specific brands stand out for their efficiency and reliability. Notably, the Centrifugal Pump by Grundfos offers a robust solution for high flow and pressure capacity. The PosiFlow Pump from Flowserve is also notable, famed for its adaptability across diverse drilling environments. Both products exhibit durability and involve minimal maintenance.
The benefits of these products include:
- High operational efficiency: Both pumps ensure effective fluid transferring.
- Ease of maintenance: Simplified maintenance routines reduce operational downtime.
- Compatibility: Modes of integration with various drilling frameworks are easy to troubleshoot.
Step-by-Step Guides
When implementing a pump in a drilling system, following precise steps can lead to successful integration:
- Identify correct pump type: Analyze your drilling requirements and choose a corresponding pump type.
- Prepare the drilling rig: Ensure that you have suitable fitments and mounting equipment ready for installation.
- Install the pump: Follow the manufacturer’s guidelines closely, making sure the pump is positioned correctly.
- Test the system: After setup, run several tests to verify that all components function as intended.
- Utilize maintenance practices: Develop a schedule or checklist to ensure regular assessments of pump performance and condition.
Regular maintenance practices will increasingly enhance the lifespan of pumps.
Integrating pumps effectively will provide substantial value to the drilling processes. Endeavoring to choose the right pump and maintaining it actively serves the ultimate goal of efficiency and capability in drilling operations.
Preamble to Drilling Pumps
Drilling pumps are integral components in various drilling systems. They are mainly used to deliver fluids under high pressure, necessary for the hydraulic actions of drilling operations. Understanding their role is crucial for optimizing performance, ensuring equipment longevity, and minimizing costs associated with drilling activities.
Definition and Purpose
Drilling pumps are defined as devices that move liquids, often under high pressure. Their primary functions include circulating drilling fluid to cool, lubricate, and remove cuttings from the drill bit. They achieve a balance in the system's pressure, ensuring stability and safety during the drilling process. Furthermore, they allow for adjustments in fluid flow, which can influence the efficiency of drilling operations.
The purpose of these pumps extends to improving the overall speed of drilling. Fast fluid circulation can drastically reduce the time needed for drilling, skyrocketing production rates, and thereby impacting overall project costs favorably. Additionally, certain pumps can be adaptable for various fluid types, which adds to their utility in different environments.
Historical Development
The historical development of drilling pumps traces back to the early advancements in drilling technology. Initially, drilling operations relied on more manual methods, requiring significantly more labor. Early pumps were rudimentary, and lacked the precision and efficiency observed today.
As technology progresses, featuring innovations during the industrial revolution, the design and functionality of drilling pumps evolved immensely. By the mid-20th century, widespread use of centrifugal pumps emerged as energy demands surged. This era saw pumps that were more efficient and streamlined, providing the necessary outputs required by modern drilling systems.
Today, precision in the design of pumps is vital. It is a market driven by technology and the necessity for enhanced dynamic performance. Manufacturers have harnested data analytics, leading to pumps that save fuel and minimize environmental impact while ensuring sustained drilling output. Understanding this progression not only highlights the importance of pumps but also their adaptive nature in different drilling scenarios.
Types of Pumps for Drilling Applications
Pumps play a crucial role in the effectiveness of drilling operations. Understanding the various types of pumps is essential for optimizing drilling outcomes and ensuring efficient performance. Each pump type presents specific benefits, operational traits, and use-cases within drilling systems. Choosing the correct pump is no merely a technical decision, but a strategic one that can strongly influence overall project costs and timelines. Accurate selection contributes to water management, cuttings removal, and maintaining pressure in the wellbore.
Centrifugal Pumps
Centrifugal pumps are among the most widely used types in drilling applications. They operate using a rotating impeller to create a flow of liquid. The design is straightforward, leading to reliability under high operational demands. Key advantages of centrifugal pumps include:
- High flow rates: Suitable for large-scale operations requiring quick flow.
- Versatility: Can handle different types of fluids, making them adaptable.
- Low maintenance needs: Their simpler design typically docket the risk of failure and ongoing maintenance costs.
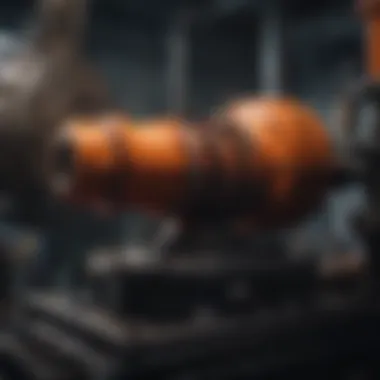
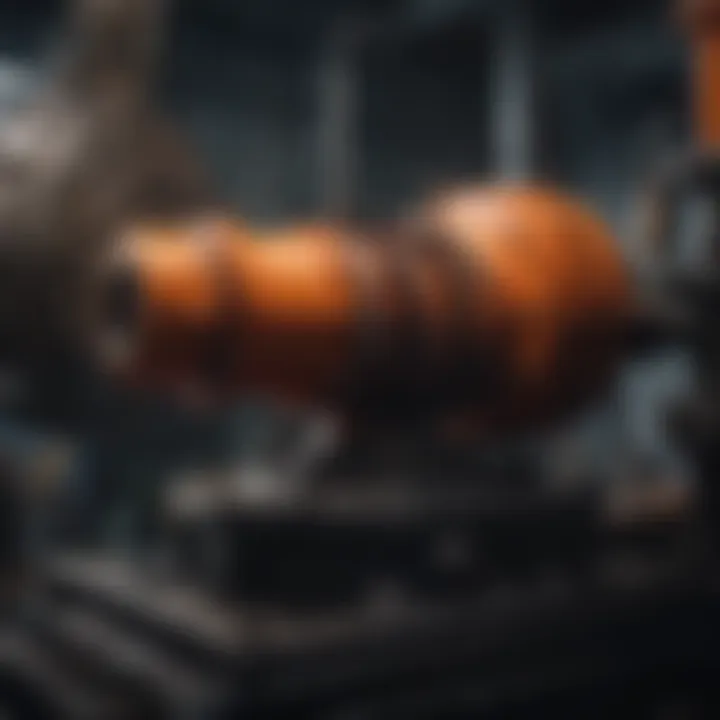
Centrifugal pumps excel in applications where flow consistency is critical. The adjustable impeller provides opportunities for customization based on specific drilling conditions. However, it is crucial to monitor slips or air entrainment as that might impact performance.
Positive Displacement Pumps
Positive displacement pumps function in a fundamentally different manner. They draw fluid into a chamber and then expel it at a predetermined volume, regardless of pressure. This consistency provides some advantages:
- Constant and predictable flow rates: Useful in applications requiring stable pressures, such as those dealing with viscous fluids.
- Cleansing capability: Good at transporting slurries or containing solid pieces, which is an advantage in drilling mud systems.
- Efficiency at higher pressures: Well-suited for environments with demanding conditions.
While positive displacement pumps have many strengths, installers must pay attention to the requirement bits, ensuring proper clearance and compensation allowances in the systems. \Crucial to know the pump index and to monitor configurations consistently depending on the variable fluid inputs.
Submersible Pumps
Submersible pumps standout by operating when fully plunged beneath fluid levels. Due to this integral placement, they are critical for well applications, particularly in adding safety as well as performance. Their merits include:
- Space-saving design: Designed to minimize surface footprint while maximizing utility.
- Efficient cooling: Operating submerged prevents overheating, prolonging the pump life cycle.
- Lower installation costs: Reduces the need for built structures or spaces above ground.
Operationally, submersible pumps can enter into larger boreholes. However, using them involves strict adherence to manufacturer guidelines regarding the depth to which they can be impeded. With both environment considerations and material provenance taken seriously, these pumps can yield significant operational advantages.
Each type of pump has specific proficiencies and especialled usages that cater to distinct drilling needs. Assessing cost-saving maintenance and operational efficiencies plays a pivotal role in pump selection and integration into overall drilling systems.
Operational Principles of Drilling Pumps
Understanding the operational principles of drilling pumps is essential for optimizing performance in drilling activities. By mastering these principles, operators can effectively leverage the functionality of different pumps, ensuring smooth operations and maximizing drilling efficiency. This section explores the significance of hydraulic dynamics and fluid mechanics in drilling systems, which underpin the full functionality of these critical components.
Hydraulic Dynamics
Hydraulic dynamics refers to the behavior of fluids in motion and is paramount in the operation of drilling pumps. When drilling, various factors, such as pressure, fluid properties, and pump design influence hydraulic dynamics. The appropriate understanding allows operators to navigate challenges effectively.
Key Aspects:
- Pressure Management: An accurate balance of pressure ensures that fluids are moved efficiently. This minimizes risks of blowouts or other safety hazards.
- Flow Rate Optimization: Adjusting flow rates can enhance drilling performance. Something similar to how pumps operate in farms influences the dynamics in non-drilling scenarios.
- Energy Efficiency: Ingenious designs in pumps allow the efficient conversion of energy into hydraulic power, minimizing fuel consumption.
Utilizing hydraulic analysis can help predict how changes in pump operations could impact overall performance. The movement of drilling mud's viscosity alters, and any variations can drastically change dynamics in hydraulic systems.
Fluid Mechanics in Drilling
Fluid mechanics studies how fluids behave and interact within systems. Its principles are integral for optimizing drilling operations. With the direct involvement of drilling fluids, proper management of these materials determines efficiency.
Key Considerations:
- Viscosity: This property affects the flow rate and the ability to carry cuttings out of the drill well efficiently. Operators need to choose the right mix.
- Pressure Loss: Understanding average pressure for fluid flow is crucial. It affects the circulation of drilling mud within the borehole.
- Cuttings Transport: Often, issues arise where cuttings accumulate. Knowledge of fluid mechanics helps prevent this through strategic design or adjustments.
“A fundamental understanding of fluid mechanics can lead to significant improvements in drilling performance.”
Incorporating knowledge from hydraulic dynamics and fluid mechanics helps in fine-tuning pump selection within drilling systems. By comprehensively analyzing these principles, drilling teams can improve efficiency and reliability in their operations.
Mounting and Compatibility with Drilling Equipment
The proper integration of pumps into drilling systems is vital for enhanced operational efficiency. When choosing a pump, attention to mounting and compatibility with existing drilling equipment is crucial. Effective mounting ensures that the pumps function at their optimal levels, and compatibility promotes seamless operations. Misalignment or poor fitment can lead to significant issues such as downtime, inefficiency, and increased operational costs.
Attachment Mechanisms
Attachment mechanisms offer a framework to connect pumps securely to drilling systems. An airtight or highly efficient attachment is key to maintaining suction strength and pressure. The main types of attachment methods include:
- Bolting: Utilizing bolts to fasten the pump tightly.
- Clamping: This provides flexibility for adjusting the pump position.
- Sliding: Enables easy repositioning during maintenance procedures.
It's essential to select a method compatible with both the pump and the rig setup. The wrong attachment can put undue strain on the equipment, creating risk for both the pump and drilling rigs.
Sizing and Fit Requirements
Maintaining appropriate fit and size when integrating pumps into a drilling system results in smoother operational flow and minimizes risk of complications. Correct sizing is influenced by:
- Pump Output Specifications: Ensure the pump is capable of handling the desired flow rate and pressure.
- Space Constraints: Evaluate the physical layout of the drilling site and fit the pump accordingly.
- Weight Distribution: Consider the total weight of the pump along with other drilling equipment.
Evaluating these aspects can bolster the efficiency of work processes. Misfits can lead to maintenance complications and compromise the service lifetime.
It is essential for drill operators to invest time in assessing both attachment mechanisms and sizing. This will optimize the operational capacity and increases the useful life of drilled structures.
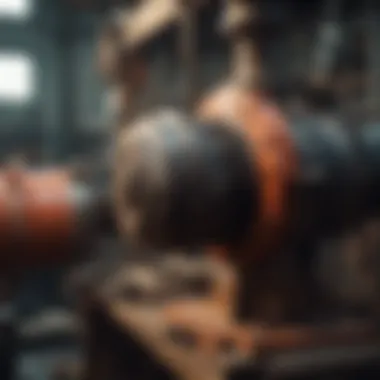
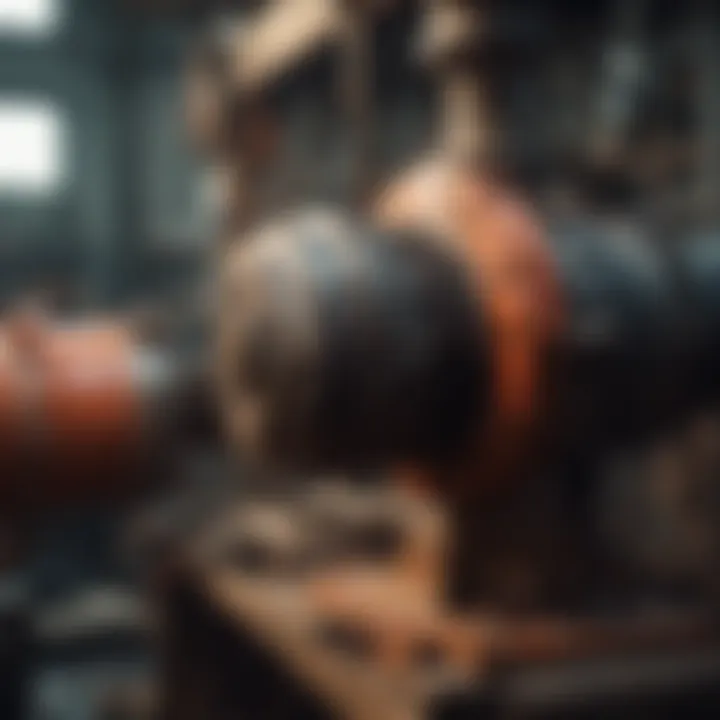
The Role of Pumps in Enhancing Drilling Performance
Pumps are essential components in drilling systems. They significantly improve the efficiency and overall effectiveness of drilling operations. The integration of appropriate pumps can facilitate fluid movement, maintain pressure, and manage flow rates, directly influencing performance metrics. Enhanced drilling performance leads not only to increased profits but also to better resource management.
Efficiency and Speed Improvements
Efficiency in drilling is paramount for success in any project. By employing advanced pump technologies, the speed of drilling operations can be markedly improved. Pumps help manage the drilling fluid properly, ensuring it covers the bit uniformly while removing cuttings swiftly. This accelerates the drilling process and optimizes the useful working time of equipment.
- Higher Flow Rates: A well-chosen pump will provide adequate flow rates to match the needs of the drilling operation, which can lead to faster penetration rates.
- Reduced Downtime: Advanced pumps designed for minimal maintenance can significantly decrease operational downtime. Thus, more drilling can be accomplished over time.
- Consistent Pressure Levels: Maintaining optimal pressure is crucial. Pumps designed specifically for drilling applications assure constant pressure, resulting in uniform performance.
Cost-Benefit Analysis
Undergoing a cost-benefit analysis of pump integration into drilling systems reveals numerous financial advantages. The initial costs must be evaluated against potential savings in time, labor, and materials. Here are several key points of consideration:
- Reduced Operational Costs: Efficient pumps lead to quicker drilling, reducing the labor and machinery costs.
- Lower Energy Consumption: Many modern pumps are designed to use less power, resulting in lower energy costs without sacrificing effectiveness.
- Long-Term Investment: Investing in high-performing pumps may come with a higher upfront cost, but the benefits gained will often outweigh these costs over the long haul.
- Decreased Risk of Failures: Quality pumps have fewer failures which translates to lower repair costs and mitigation of project delays.
Integrating pumps efficiently into drilling applications not only optimizes performance but also enhances the profitability of operations.
Maintenance Considerations for Drill Pumps
Maintaining pumps in drilling systems is fundamental for achieving optimal performance and longevity. Regular maintenance reduces downtime and prevents costly replacements. It is crucial for users—particularly housewives and home owners—to understand maintenance protocols and failure modes to ensure efficient operation. By keeping the pumps in good condition, users avoid frustration and unnecessary stress.
Routine Maintenance Protocols
Proper maintenance can keep a drill pump functioning effectively for an extended period. Among the essential aspects of routine maintenance are:
- Inspection Cycles: Regular checks allow users to spot wear and tear early. Check for any signs of leaks or loose connections when inspecting. This can prevent fluid loss and system failures.
- Cleaning Components: Dirt and other substances can accumulate in the pump and hinder performance. Regular greening ensures smooth operation. This includes cleaning filters and removing accumulated debris from filter screens.
- Lubrication: When required, apply suitable lubricants to moving parts according to the manufacturer's specifications. This helps prevent friction wear, which can compromise pump performance over time.
By following these protocols, users can extend the lifespan of their drilling pumps and save on replacement costs.
Common Failure Modes
Despite taking precautions, failures can still occur. Being aware of possible failure modes can provide significant insights into restoration efforts. Some of the common issues seen in drill pumps include:
- Seal Failures: Damaged or worn seals can lead to fluid leaks. Regular inspections can flag seals needing replacement before they cause losses.
- Bearing Wear: Bearings can experience wear due to consistent usage and friction. Monitor vibrations and sound levels to detect abnormalities.
- Cavitation: This condition occurs when vapor bubbles form in the fluid, leading to reduced performance, noise, and potential stack damage. Maintaining proper suction can reduce instances of cavitation.
It is vital for users to recognize these issues early. Understanding these problems can not only save costs on repairs but also ensure continued efficient operation in their drilling systems.
Innovations in Pump Technology for Drilling
The modern drilling industry continues to face challenges related to efficiency, cost, and environmental impact. Innovations in pump technology have become essential in addressing these issues head-on. As pumps are central components in drilling systems, technological advancements can significantly enhance drilling operations. These innovations not only pave the way for improved efficiencies but also contribute to sustainability and stronger performance metrics. By exploring advancements and integrating smart technologies, drilling operations position themselves better in an ever-evolving market.
Advancements in Pump Design
Recent developments in pump design have focused on creating equipment that is more robust and capable of handling a variety of fluids. Enhanced materials and manufacturing processes lead to pumps that can resist wear and tear upon heavy utilization. Improved hydraulic designs are optimizing flow rates, reducing the energy needed for operation. Achievements in the structural framework ensure that pumps can perform effectively even under extreme conditions. Such developments make installation and operation much more reliable and secure.
Some notable advancements include:
- Compact Designs: Recent models of pumps have become more compact, allowing for an easier fit into existing drilling systems. This is vital for maintaining functionality in tightly packed well sites.
- High-Efficiency Impellers: Latest impeller designs enhance the velocity and flow of fluids, allowing for better drilling performances.
- Corrosion Resistance: With the integration of new coatings and materials, pumps can now withstand harsher environments, extending their lifespan while lowering replacement costs.
Integration with Smart Technologies
The integration of smart technologies into pumping systems marks a transformative phase in drilling processes. Various professionals within the industry recognize the impact of data-driven decision-making facilitated by these technologies. By utilizing sensors, real-time data monitoring, and advanced analytics, pumps can optimize performance and predict maintenance needs.
Key advantages lie in the following areas:
- Real-Time Monitoring: Next-gen drilling pumps can measure flow, pressure, and wear in real-time. This capability minimizes surprises during drilling and reduces wasted resources.
- Predictive Maintenance: Using data analytics, operators can foresee potential failures and conduct maintenance proactively. This stops major issues before they arise, creating less downtime and boosting overall efficiency.
- Enhanced Safety Controls: Advanced telemetry systems help detect anomalies and trigger alerts. Safety improves not only for equipment but also for personnel on-site, as they are more aware of pump conditions.
- Environmental Monitoring: By tracking the fluids being used, operators can gain insights into environmental impacts, pushing them toward more sustainable practices.
The integration of smart technologies leveraging data analytics and sensors allows for real-time adjustments, optimizing the drilling process and maximizing efficiency.
In summary, the innovations in pump technology provide a fresh lens onto traditional operations. Both advancements in pump design and the integration with smart systems demonstrate how the pumping segment of the drilling industry continues to evolve. Consequently, embracing these innovations is no longer optional; it is an imperative to stay competitive, sustainable, and efficient in a dynamic global marketplace.
Environmental Considerations
Environmental considerations are central to the discussion of integration of pumps in drilling systems. It is crucial to assess how these pumps affect the ecological landscape during operation and their overall sustainability. Decisions made related to pump usage can significantly influence the broader environment. Hence, understanding these implications leads to improved practices in engineering and operational developments of drilling systems.
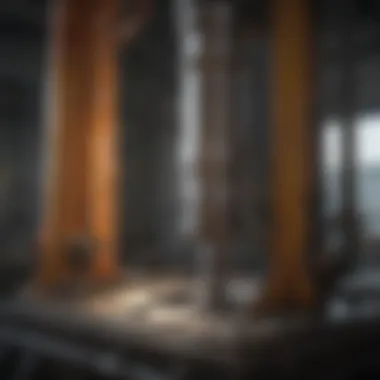

Sustainability Practices in Pump Usage
Sustainability in pump usage is about maximizing efficiency while minimizing environmental impact. This involves several practices:
- Efficient Design: Modern pumps are designed to lose less energy. They operate at optimal levels and meet specific fluid-moving needs without wasting resources.
- Recycling Water: Many industries focus on recycling water used in the drilling process. Technologies are available that can filter and return water after separation of drilling fluids and contaminants.
- Waste Management: It is important to manage the waste generated during drilling operations carefully. Proper disposal and treatment can mitigate harmful effects on soil and groundwater.
Implementing these practices not only helps protect the environment but also often leads to cost savings.
Impact on Natural Resources
The impact of drilling pumps on natural resources cannot be understated. When improperly managed, the extraction of resources can lead to several challenges:
- Water Depletion: Excessive use of water during drilling operations may strain local water supplies. This is especially critical in regions that are arid or have limited resources.
- Soil Contamination: If mishandled, fluids from drilling may seep into the ground, risking soil health. The right techniques and pump design can help prevent this mishap.
- Impact on Biodiversity: Disturbing natural habitats for drilling purposes can seriously impact local ecosystems. Understanding the right deployment and management of pumps can mitigate these factors.
Case Studies
Case studies serve an essential purpose in comprehending the real-world applications and performance of pumps in drilling systems. They illustrate practical instances where various types of pumps have been effectively integrated. Analyzing these real-life examples help in discerning the advantages, challenges, and strategies that are involved in implementing pumping solutions. Through these case studies, stakeholders gain insights that can inform their decisions, enhancing operational efficiency and productivity.
Successful Implementations
Implementing pumps in drilling systems has seen considerable success across different industries. One notable example is the** use of centrifugal pumps** in offshore drilling operations. These pumps efficiently transfer large volumes of fluids, streamlining operations. Companies reported significant reductions in time and labor costs, demonstrating how choosing the right pump can yield measurable benefits.
Another successful implementation involved positive displacement pumps in geothermal drilling. These pumps reliably deliver high pressure, which can be critical when drilling into challenging geological formations. The enhanced flow rates not only expedite drilling processes but also reduce completion times significantly.
Critical factors that contributed to the success of these implementatons include:
- Thorough research and selection of the right pump type.
- Robust integration with existing drilling equipment.
- Comprehensive training for personnel using the systems.
These examples reflect not just the utility of pumps but highlight their importance as core tools in drilling endeavors.
Lessons Learned
The lessons obtained from case studies about pump integration are valuable for future projects. Firstly, it becomes clear that strategic planning is vital. Proper analysis of the drilling environment and demands is required before any pump organzition. Second, issues of maintenance and component compatibility must not be overlooked. Failures often result from a lack of attention to upkeep, causing delays and increased project costs.
Additionally, many cases have shown that technological adaptability can significantly enhance pump functionality. Two major lessons from recent implementations include:
- Using state-of-the-art monitoring tools can yield early warnings of potential failures.
- Regular training for operators enhances their ability to troubleshoot unexpected issues quickly.
In summary, case studies highlight that success often depends on a combination of thorough research, ongoing training, and a focus on both efficiency and adaptability. These insights foster a proactive approach to pump integration, ultimately driving better outcomes in drilling operations.
Future Trends in Pump Technology for Drilling
The exploration of future trends in pump technology for drilling is crucial for understanding how advancements impact incorporate different types of pumps to improve efficiency and reliability in drilling systems. As industries look for more efficient solutions, these changes may influence everything from the design of drilling pumps to their overall integration into existing systems.
Predicted Developments
Recent forecasts highlight key areas where pump technology is headed. Some predicted developments include:
- Increased Automation: The integration of automated systems can enhance operational efficiency and reduce manual intervention.
- Energy Efficiency Improvements: New technologies focus on minimizing power usage without sacrificing performance. This is significant as climbing energy costs affect operation budgets.
- Advanced Materials: Using composite materials can improve durability and reduce weight, leading to better handling during installation.
These predictets make it necessary for industry stakeholders to stay informed about widget technologies, so that equipment and components can be streamlined. Companies will find benefits as they adapt to modern challenges by adopting these innovations.
Opportunities for Research and Development
Continuously evolving, the field offers numerous opportunities for research and development. Highlighted areas are:
- Customization of Systems: More attention is needed on custom solutions that accommodate unique operational needs and silicon variations.
- Smart Sensor Integration: By developing embedded sensors, real-time monitoring systems can provide valuable data. This leads to improved decision-making and predictive maintenance strategies.
- Environmental Sustainability: Research aimed at reducing environmental impacts is vital to modernize the drilling process. It's needed to minimize waste and resource depletion advantages in facilities.
Embracing these advances can notably enhance the functionality of drilling systems. In the long term, being proactive in fuelling research opens up pathways eliminated technologies while ensuring future are aligned with market demands.
In essence, the combination of automation, energy efficiency, and sustainability can distinguish leading pump technologies, positioning stakeholders effectively in a rapidly changing market.
Culmination
Summary of Key Points
In summary, the integration of pumps into equipment relates to several essential elements. Firstly, their ability to maintain the proper flow of fluids enhances drilling performance. Secondly, various pump types offer unique functions catering to specific needs within drilling activities. This diversity allows operators to choose the pump that best fits their operational requirements.
Additionally, understanding pumps involves recognizing maintenance protocols, as a failure in this area can lead to costly downtime. Moreover, technological innovations allow for better integration of pumps with advanced systems that optimize performance. Overall, a comprehensive grasp of these aspects spells the difference between a successful drilling operation and one plagued with inefficiencies.
Final Thoughts on the Role of Pumps in Drilling
As drilling projects advance, keeping pace with innovations in pump technology becomes increasingly important. Continuous learning about designs, operational methodologies, and maintenance habits leads to more informed choices that can mitigate risks and enhance productivity. Positions within this industry can afford to overlook pumps, but those who appreciate their significance ultimately generate greater value.
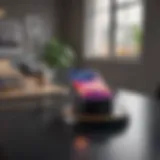
