Unveiling the Complexity of Copper Split Rivets in Various Industries
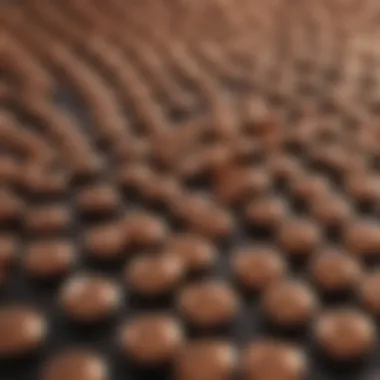
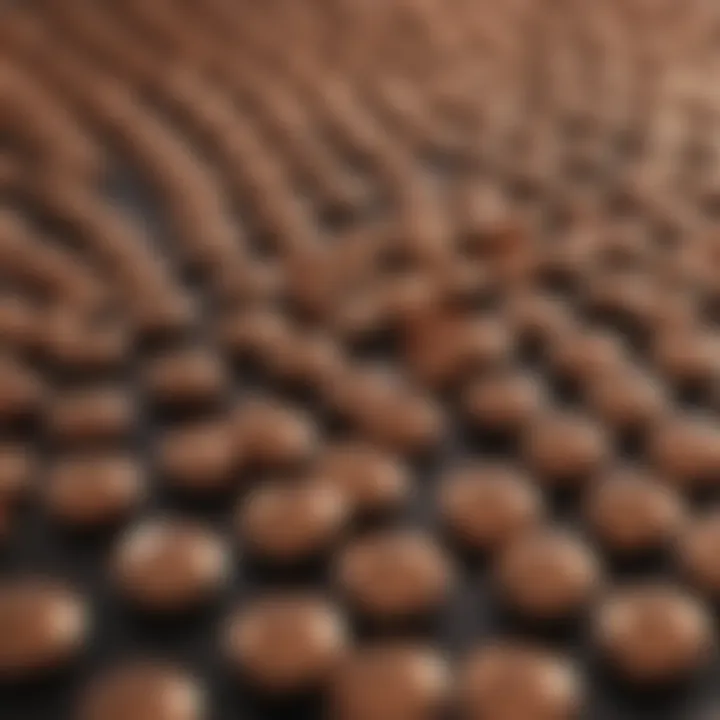
Overview of Copper Split Rivets in the Home Improvement Industry
Copper split rivets serve as a crucial component in the realm of home improvement, offering unmatched durability and fastening capabilities. Homeowners often underestimate the importance of choosing the right rivets for various projects, not realizing the impact they can have on the overall quality and longevity of structures.
Common Challenges and Solutions
Despite their benefits, homeowners commonly face challenges when it comes to selecting and utilizing copper split rivets. Issues such as incorrect sizing or improper installation techniques can lead to structural weaknesses, compromising the integrity of the project. To tackle these hurdles, it is essential for homeowners to educate themselves on the proper selection and installation processes. Seeking guidance from professionals or referring to detailed tutorials can greatly aid in overcoming these challenges.
Product Recommendations
When it comes to choosing the best copper split rivets for home improvement projects, [Industry Brand] offers a range of top-notch products renowned for their quality and reliability. These rivets come in various sizes and designs to cater to different needs, ensuring versatility and efficiency in fastening applications. The benefits of [Industry Brand] rivets include exceptional strength, corrosion resistance, and ease of installation, making them a preferred choice among homeowners and professionals alike.
Step-by-Step Guides
To ensure successful implementation of copper split rivets in home improvement projects, it is crucial to follow precise steps for selecting, preparing, and installing the rivets. Begin by carefully assessing the requirements of the project and selecting the appropriate rivet size and style. Then, prepare the materials and tools needed for installation, ensuring a smooth and efficient process. Finally, follow manufacturer guidelines or seek expert advice to ensure proper installation techniques, guaranteeing the durability and reliability of the fastening solution.
Introduction
In the realm of fastening components, copper split rivets stand out as essential elements that play a pivotal role in various industries. This article embarks on a thorough exploration of the intricacies surrounding copper split rivets, shedding light on their composition, structure, manufacturing process, applications, benefits, challenges, future trends, and more. By dissecting each facet methodically, we aim to provide an in-depth understanding of these versatile rivets.
Definition of Copper Split Rivets
Copper split rivets, also known as bifurcated rivets, are unique fasteners characterized by their two-prong design. These rivets consist of a tubular body with two split tines at one end that are spread apart during installation to secure materials together. The construction of copper split rivets allows for a robust and lasting bond, ensuring reliable fastening solutions across diverse applications.
Brief History
The history of copper split rivets traces back to ancient craftsmanship, where metalworkers utilized rudimentary forms of riveting techniques to join materials. Over time, advancements in metallurgy and manufacturing processes have refined the design and functionality of copper split rivets, making them indispensable components in modern engineering and construction practices. Understanding the historical evolution of these rivets provides valuable insights into their enduring significance and widespread adoption in contemporary industries.
Composition and Structure
The material used in the creation of copper split rivets is paramount to their overall quality and effectiveness. Copper, known for its excellent conductivity and malleability, is often chosen for its unique combination of properties. When combined with other alloys to improve strength and durability, copper split rivets become versatile fastening solutions suitable for a wide range of applications.
The design features of copper split rivets contribute significantly to their functionality and ease of use. From the shape and size of the rivet head to the configuration of the split, every detail is carefully considered in optimizing performance. Additionally, factors such as grip range, shear strength, and resistance to loosening play a crucial role in ensuring the reliability and longevity of the rivets in demanding environments.
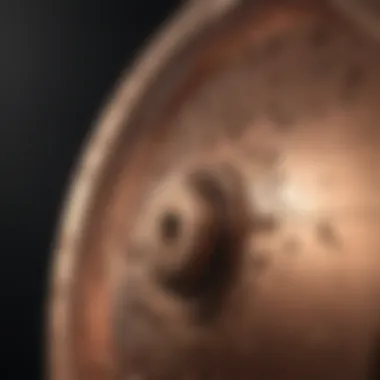
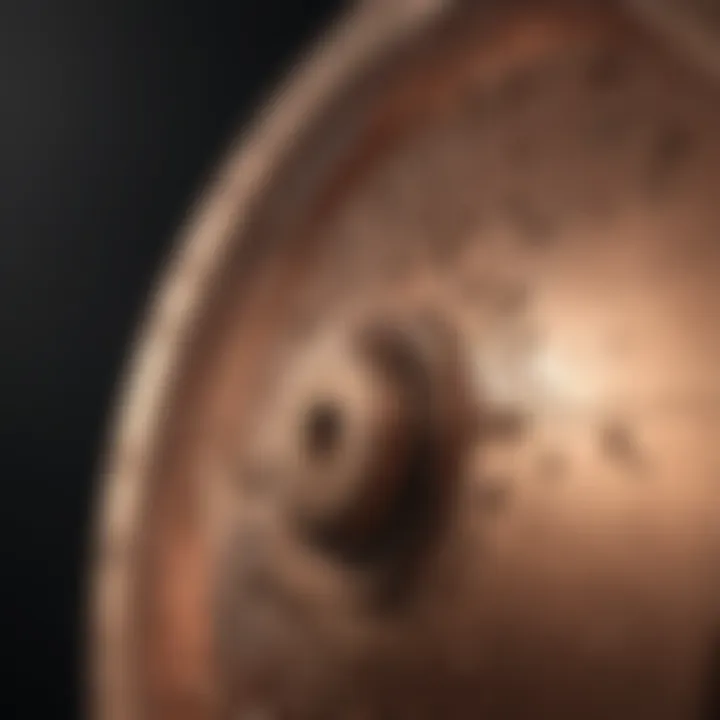
Materials Used
The materials used in manufacturing copper split rivets are carefully selected to meet stringent quality standards and performance requirements. Copper, being the primary material, offers excellent electrical conductivity and thermal efficiency, making it ideal for applications where such properties are crucial. In addition to copper, various alloys may be added to enhance the strength and corrosion resistance of the rivets, ensuring they can withstand harsh environmental conditions.
Aluminum is another material commonly used in conjunction with copper to create hybrid rivets that exhibit a balanced combination of lightweight construction and robust performance. This blend of materials allows for the rivets to be used in aerospace applications where weight-saving is critical without compromising on strength or durability. Stainless steel is also frequently utilized in the manufacturing of copper split rivets to provide exceptional resistance to corrosion, extending the lifespan of the fastening components in challenging industrial settings.
Design Features
The design features incorporated into copper split rivets are integral to their functionality and efficacy. The head of the rivet is often engineered to provide a secure grip and prevent pull-through, ensuring reliable fastening under various loads. The split design of the rivet body allows for quick and easy installation by expanding and securing the material, creating a strong and lasting connection.
Furthermore, specific design elements such as serrations along the shaft of the rivet enhance the grip strength, reducing the risk of loosening or disconnection over time. The choice of rivet size, length, and thickness is tailored to the intended application, ensuring optimal performance and longevity. By paying careful attention to these design features, manufacturers can produce copper split rivets that meet the stringent requirements of industries ranging from automotive and construction to electronics and marine engineering.
Manufacturing Process
In this section, we will delve deep into the crucial aspect of the manufacturing process of copper split rivets. Understanding the manufacturing process is essential as it directly impacts the quality and durability of the final product. The intricate steps involved in creating these rivets play a significant role in their performance across various industries. From the selection of materials to the final formation, each stage requires precision and expertise to ensure top-notch rivets for diverse applications.
The manufacturing process of copper split rivets begins with the meticulous selection of high-quality copper materials. The purity and composition of the copper significantly impact the strength and resilience of the rivets. These materials undergo strict quality checks to ensure they meet industry standards before proceeding to the next phase.
Next, the chosen copper materials are shaped and prepared for the formation of the rivets. Specialized machinery and tools are utilized to create the distinctive shape and structure of the rivets. This step demands precision engineering to achieve uniformity in size and shape, crucial for their performance in various settings.
Once the initial shaping is complete, the rivets undergo a series of heating and cooling processes to enhance their strength and durability. This annealing process is vital in refining the metallurgical properties of the copper, making the rivets resilient to mechanical stress and environmental factors.
Finally, quality control measures are implemented to assess the integrity of the manufactured rivets. Comprehensive testing procedures, including stress tests and dimensional checks, ensure that each rivet meets the required specifications for proper functioning. Any deviations or defects are identified and rectified to maintain the high quality standards of the final product.
The manufacturing process of copper split rivets culminates in the production of reliable and durable fastening components that find widespread applications across sectors like aerospace and automotive industries. By meticulously following each step of the manufacturing process, manufacturers can guarantee the efficiency and strength of these essential rivets.
Formation of Copper Split Rivets
The formation of copper split rivets is a meticulous process that involves precise techniques to create these essential fastening components. The production of copper split rivets begins with the careful shaping of raw copper materials into the desired form. Specialized machinery and tools are employed to shape the copper accurately, maintaining consistency in size and shape.
After the initial shaping, the copper pieces undergo a series of heating processes to enhance their malleability. Heating the copper to a specific temperature allows for easy manipulation and forming of the rivets. This process is crucial in achieving the distinctive split design that gives these rivets their unique functionality.
Once the heated copper reaches its optimum malleable state, it is carefully molded and divided into separate sections that will form the split rivets. Precision tools are used to cut and shape the copper into individual rivet components, ensuring uniformity in size and dimensions.
After the formation of the individual rivet segments, they undergo a final assembly process where the split design is perfected. Skilled technicians meticulously join the split ends of the rivets to create a secure and functional fastening solution. This intricate assembly process is critical in ensuring the effectiveness and reliability of copper split rivets in various applications.
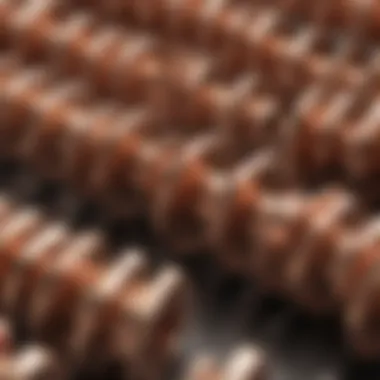
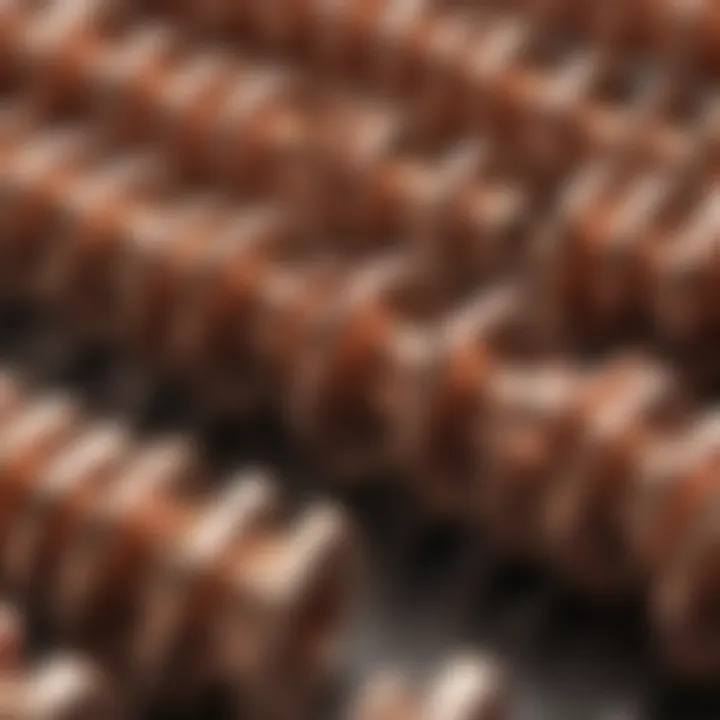
The formation of copper split rivets combines technical expertise and precision craftsmanship to produce high-quality fastening components that offer exceptional performance and durability. Manufacturers adhere to strict standards and meticulous procedures to create rivets that meet the diverse needs of industries like aerospace and automotive, providing reliable solutions for fastening requirements.
Quality Control Measures
Quality control measures play a pivotal role in ensuring the reliability and performance of copper split rivets. Rigorous testing and inspection protocols are implemented throughout the manufacturing process to maintain the high standards of these essential fastening components. By adhering to strict quality control measures, manufacturers can deliver rivets that meet stringent specifications and exceed customer expectations.
One of the primary quality control measures employed in the production of copper split rivets is material testing. Before initiation of the manufacturing process, raw copper materials undergo thorough testing to verify their purity, composition, and mechanical properties. This initial screening helps in selecting high-quality materials that form the foundation of durable and robust rivets.
During the manufacturing process, continuous quality checks are performed at various stages to monitor the forming and shaping of the rivets. Dimensional accuracy, surface finish, and structural integrity are assessed to detect any deviations from the specified standards. Any anomalies are identified and corrected promptly to maintain uniformity and consistency in the rivets.
Furthermore, quality control measures extend to post-production inspections where finished rivets undergo comprehensive testing procedures. Stress tests, corrosion resistance assessments, and load-bearing evaluations are conducted to evaluate the performance capabilities of the rivets under simulated conditions. This meticulous testing ensures that each rivet meets industry requirements for strength, durability, and functionality.
By emphasizing stringent quality control measures, manufacturers uphold the reputation of copper split rivets as dependable and resilient fastening solutions. The commitment to maintaining high quality standards through thorough inspection and testing cements the position of these rivets as indispensable components in critical industries demanding superior performance.
Applications
Copper split rivets play a vital role in various industries due to their unique properties and functionalities. Their applications range from aerospace to automotive sectors, where their use is integral to the efficient functioning of diverse processes. Understanding the specific elements and benefits of these applications is crucial for comprehending the importance of copper split rivets in this article.
Aerospace Industry
In the aerospace industry, precision and reliability are paramount, and copper split rivets offer these qualities in abundance. These rivets find extensive use in aircraft construction, where they are utilized in securing critical components due to their high strength and durability. The aerospace sector values copper split rivets for their ability to withstand harsh environmental conditions and vibrations, ensuring the structural integrity of aircraft throughout their lifespan.
Automotive Sector
The automotive sector relies heavily on copper split rivets for various applications, such as in vehicle assembly and repair. These rivets are preferred for their corrosion resistance and longevity, making them an ideal choice for automotive fastening solutions. Whether in engine components or bodywork, copper split rivets provide secure and long-lasting connections, contributing to the overall safety and reliability of vehicles on the road.
Benefits of Copper Split Rivets
In exploring the significance of copper split rivets, understanding their benefits is crucial. These fasteners offer a myriad of advantages across various industries, making them a preferred choice for engineers and manufacturers. One of the key elements that set copper split rivets apart is their exceptional durability. The ability to withstand extreme conditions and heavy loads makes them a reliable and long-lasting fastening solution. This durability ensures that structures and components secured with copper split rivets maintain their integrity over an extended period, reducing maintenance costs and downtime.
Durability
The durability of copper split rivets is unmatched in the fastening industry. Their resilience under pressure and resistance to mechanical stresses make them ideal for applications where a strong and lasting bond is essential. In high-impact environments such as the aerospace and construction sectors, copper split rivets excel in providing structural stability and peace of mind. The ability to maintain their structural integrity even in harsh conditions or under frequent use positions copper split rivets as a top choice for critical installations.
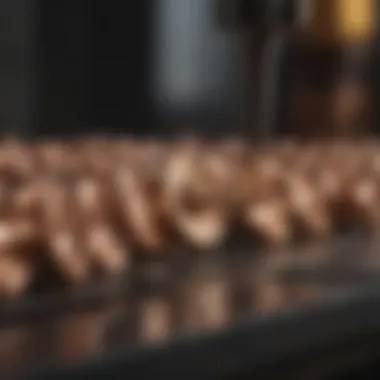
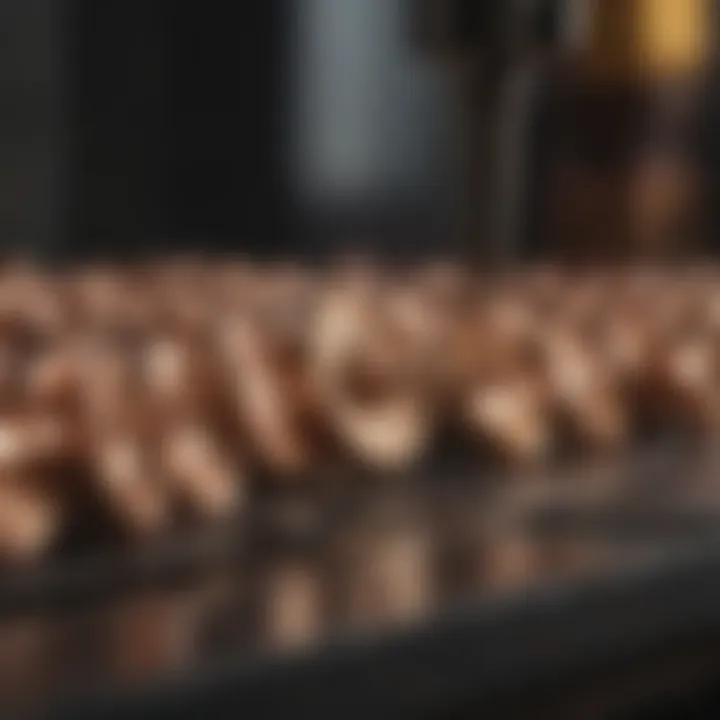
Corrosion Resistance
Another valuable benefit of copper split rivets is their exceptional corrosion resistance. Corrosion can deteriorate traditional fasteners, compromising the structural integrity of a system. However, copper split rivets' inherent corrosion resistance ensures that they can withstand exposure to moisture, chemicals, and environmental factors without succumbing to rust or degradation. This corrosion resistance extends the lifespan of installations using copper split rivets, making them a cost-effective and reliable choice for both indoor and outdoor applications. Housewives and homeowners can trust in the long-lasting performance of copper split rivets even in challenging environments, ensuring the safety and durability of their projects.
Challenges and Limitations
Understanding the challenges and limitations associated with copper split rivets is crucial for a comprehensive examination of this fastening component. Challenges: One significant challenge faced when utilizing copper split rivets is the Cost Factors involved. These rivets may entail higher production costs compared to other fastening options, which can impact the overall budget of a project. Moreover, the Maintenance and Replacement Costs associated with copper split rivets should not be overlooked, as these factors contribute to the long-term expenses of using this fastening solution. Limitations: Installation Complexities present another set of limitations when employing copper split rivets. The intricate design of these rivets may require specialized tools or techniques for proper installation, increasing the complexity of the assembly process. Furthermore, the Structural Integrity of copper split rivets may impose limitations on the maximum load-bearing capacity they can support, affecting their applicability in heavy-duty or high-stress environments.
Cost Factors
Cost Factors play a vital role in determining the feasibility of incorporating copper split rivets into a project. The initial procurement cost of copper split rivets, including materials and manufacturing expenses, contributes to the overall budget allocation. Additionally, Maintenance and Replacement Costs should be factored in, considering the long-term implications of using copper split rivets. Importantly, the Cost-Benefit Analysis of utilizing these rivets should be conducted to evaluate their economic efficiency and long-term viability in comparison to alternative fastening methods.
Installation Complexities
Installation Complexities are a key consideration when implementing copper split rivets in various applications. The Unique Design of copper split rivets may necessitate specialized tools or equipment for efficient and precise installation. Moreover, the Structural Integrity of the assembly must be ensured during the installation process to guarantee the effectiveness of these rivets. Addressing any Compatibility Issues between copper split rivets and the materials being fastened is essential to prevent performance issues or structural failures in the future. Proper training and expertise may be required to handle the installation complexities associated with copper split rivets, emphasizing the importance of skilled labor in utilizing this fastening solution.
Future Trends
To truly grasp the evolution and potential of copper split rivets, it's crucial to delve into the realm of future trends. Understanding where this essential fastening component is headed is not just a matter of curiosity, but a strategic insight for industries relying on its functionality. Future trends in the implementation of copper split rivets encompass a spectrum of advancements that are set to revolutionize the way these rivets are utilized.
The significance of future trends lies in their ability to enhance the durability, efficiency, and capabilities of copper split rivets. By staying abreast of technological advancements and innovative applications, manufacturers can continually improve the quality and performance of these rivets across various sectors. Moreover, exploring future trends enables industries to adapt to changing requirements, environmental considerations, and emerging challenges, ensuring that copper split rivets remain a cornerstone of secure fastening solutions.
Technological Advancements
Technological advancements in the realm of copper split rivets are paving the way for enhanced precision, reliability, and customization. From cutting-edge automated manufacturing processes to advanced coating techniques, innovations are reshaping the landscape of copper split rivet production. These advancements not only streamline manufacturing processes but also bolster the mechanical properties of the rivets, making them more resilient and adaptable to diverse conditions.
The integration of robotics, artificial intelligence, and data analytics in the manufacturing of copper split rivets has opened up new frontiers in quality control, efficiency, and product development. With real-time monitoring capabilities and predictive maintenance systems, manufacturers can ensure optimum performance and consistency in the production of copper split rivets. Additionally, innovations in surface treatments and coatings enhance the corrosion resistance and longevity of these rivets, expanding their applications in hostile environments.
Innovative Applications
Innovative applications of copper split rivets go beyond traditional uses, pushing the boundaries of fastening solutions in various industries. The versatility of copper split rivets allows for creative applications in areas such as renewable energy, electronics, and infrastructure development. Whether in securing solar panels, assembling electronic components, or reinforcing structural elements, copper split rivets offer a reliable and cost-effective fastening solution.
The advent of composite materials and lightweight structures has further spurred the innovative use of copper split rivets, where their high strength-to-weight ratio and ease of installation make them ideal for modern construction projects. By exploring new avenues for application and integration, industries can leverage the unique properties of copper split rivets to optimize performance, efficiency, and sustainability in their projects. As technological advancements continue to drive innovation, the future holds exciting possibilities for the utilization of copper split rivets in ways yet to be imagined.
Conclusion
Copper split rivets play a crucial role in various industries due to their unique properties and versatile applications. As highlighted throughout this article, the significance of copper split rivets lies in their exceptional durability and corrosion resistance, making them a preferred choice for demanding environments. The detailed exploration of their composition, manufacturing process, and benefits underscores the importance of understanding these fastening components. By delving into the challenges and limitations faced in utilizing copper split rivets, one can appreciate the intricacies involved in their installation and the cost factors to consider. Overall, the future trends section provides a glimpse into the advancements and innovative applications that will shape the continued evolution of copper split rivets, paving the way for enhanced performance and efficiency across industries.
Summary of Key Points
- Copper split rivets are valued for their durability and corrosion resistance, making them ideal for various industries.
- Understanding the composition and manufacturing process of copper split rivets is essential for maximizing their benefits and overcoming challenges.
- The cost factors and installation complexities associated with copper split rivets highlight the need for careful consideration in their usage.
- Future trends in technological advancements and innovative applications promise to elevate the capabilities of copper split rivets, ensuring their continued relevance in the industrial landscape.