Unveiling the Efficiency of Mixing Bins in Industrial Operations for Enhanced Productivity

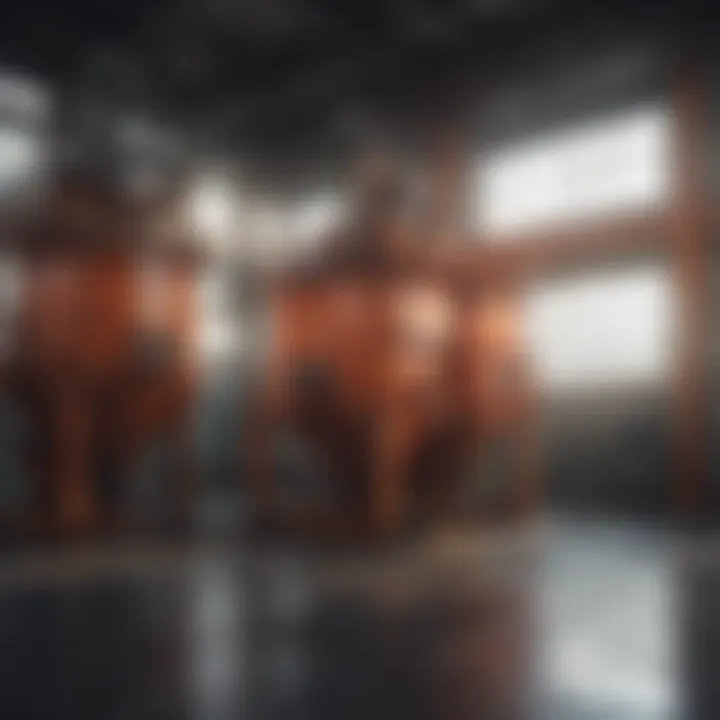
Overview of Topic
In the realm of home improvement industry, the incorporation of mixing bins stands as a pivotal element. These bins hold a significant role in streamlining industrial processes, fostering heightened efficiency, and elevating productivity levels exponentially. Understanding the nuances of mixing bins is imperative for industries seeking to optimize their operations and achieve superior outcomes.
Common Challenges and Solutions
When it comes to homeowners, various challenges may arise in relation to the utilization of mixing bins. Issues such as improper blending of materials, inefficient distribution, and inadequate mixing ratios often plague operations. However, there are practical solutions and essential tips to navigate through these challenges seamlessly. Implementing appropriate mixing techniques, utilizing the right equipment, and adhering to precise ratios can surmount these common hurdles effectively.
Product Recommendations
Delving into the market's top industry brands, notable products have emerged as frontrunners in the realm of mixing bins. These products boast a myriad of benefits and features, offering homeowners reliability, durability, and exceptional functionality. From superior material quality to innovative designs, these recommended products are tailored to enhance operational efficiency and streamline industrial processes seamlessly.
Step-by-Step Guides
For those embarking on the journey of optimizing their industrial processes through mixing bins, a step-by-step guide is essential. Detailing practical steps to enhance blending processes, these guides offer thorough instructions for seamless implementation. From the initial planning stages to the final execution, each step is outlined meticulously to ensure optimal results and maximize productivity levels.
Introduction
In the realm of industrial processes, the efficiency of operations stands as a cornerstone for sustainable success. One crucial element that plays a pivotal role in enhancing this efficiency is the utilization of mixing bins. These specialized containers are not mere receptacles; instead, they serve as crucial facilitators of optimized operations and heightened productivity levels within various industries. By delving into the intricate functionalities and nuances of mixing bins, businesses can unlock a realm of possibilities in streamlining their processes and elevating their output quality.
Understanding the core principles behind mixing bins unveils a world of benefits for industries seeking to stay ahead in a competitive market landscape. From improving mixing efficiency to enhancing product quality and reducing processing time, the impact of incorporating mixing bins within operations goes far beyond mere storage or containment. Each aspect of mixing bin utilization holds the key to unlocking greater operational potential and refining the overall industrial workflow.
However, before delving into the depths of understanding mixing bins, it is essential to underscore the critical considerations that come into play when selecting the ideal mixing bin for specific operational needs. Factors such as material compatibility, capacity requirements, and maintenance considerations shape the decision-making process and directly influence the effectiveness of integrating mixing bins into industrial processes.
As industries navigate the complexities of selecting and implementing mixing bins, optimizing the performance of these systems becomes paramount. Proper installation practices, robust monitoring and control systems, and stringent cleaning and maintenance protocols are essential pillars in maximizing the efficiency and longevity of mixing bins within industrial settings.
Through a lens of continuous improvement and innovation, the future trends in mixing bin technology pave the way for groundbreaking advancements in industrial processes. The integration of automation and robotics, enhanced mixing algorithms, and a firm commitment to sustainability initiatives collectively shape the trajectory of industry practices towards heightened efficiency and environmental stewardship.
Understanding Mixing Bins
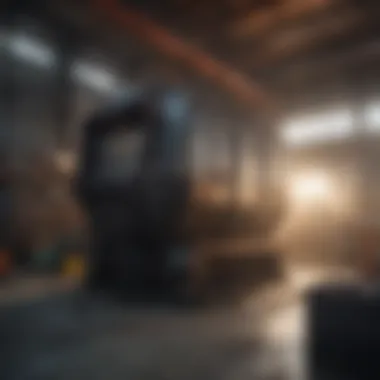
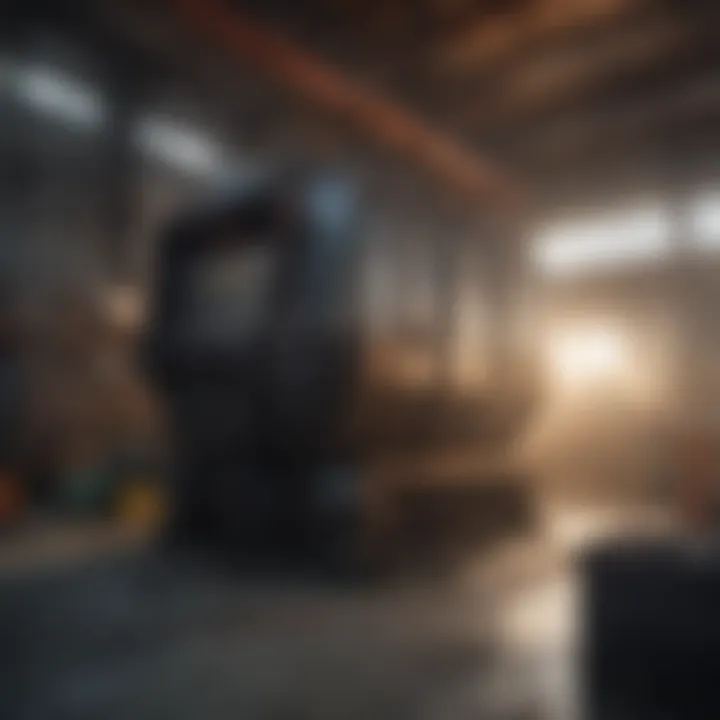
In the domain of industrial processes, understanding mixing bins holds paramount importance. By delving deep into the intricacies of mixing bins, industries can significantly enhance their operational efficiency and bolster productivity levels. This article serves as a comprehensive guide shedding light on the functionalities, benefits, and crucial considerations linked with utilizing mixing bins.
Definition of Mixing Bins
Mixing bins can be elucidated as specialized containers or vessels designed for blending and homogenizing various substances. These bins play a pivotal role in ensuring thorough mixing of components, thereby facilitating the production of consistent and high-quality end products.
Types of Mixing Bins
-#### Batch Mixing Bins Batch mixing bins are characterized by their capability to process a specific quantity of materials within a confined batch cycle. This controlled mechanism allows for precise mixing of components, making batch mixing bins a favored choice in sectors requiring batch-wise production.
-#### Continuous Mixing Bins Continuous mixing bins operate uninterruptedly, ensuring a steady flow of mixing processes. This seamless integration of material blending makes continuous mixing bins ideal for industries necessitating non-stop production cycles to meet demands efficiently.
-#### Fluidized Bed Mixing Bins Fluidized bed mixing bins utilize gas or air to create a fluidized state within the mixing chamber, enhancing mixing efficiency. This fluidization promotes homogenous mixing, making it a suitable option for industries valuing uniformity in product composition.
-#### Gravity Mixing Bins Gravity mixing bins enable mixing through gravitational forces, simplifying the blending process without the need for complex mechanical agitation. This straightforward mechanism reduces energy consumption and maintenance requirements, appealing to industries seeking cost-effective mixing solutions.
Components of Mixing Bins
-#### Agitators Agitators are pivotal components within mixing bins, responsible for stirring and mixing materials to achieve desired consistency. Their role in maintaining uniformity during blending processes makes them indispensable for ensuring product quality and process efficiency.
-#### Feeders Feeders regulate the controlled discharge of materials into the mixing bin, ensuring precise ingredient proportions. This controlled feeding mechanism is crucial for achieving accurate mixtures and preventing inconsistencies in the final product.
-#### Discharge Mechanisms Discharge mechanisms extract the homogenized mixture from the mixing bin once the blending process is complete. These mechanisms play a vital role in streamlining material flow, contributing to efficient processing operations and minimizing production downtime.
Benefits of Utilizing Mixing Bins
In the realm of industrial processes, the utilization of mixing bins holds significant importance, serving as a cornerstone for enhancing operational efficiency and productivity. By incorporating mixing bins into operations, industries can reap a myriad of benefits that lead to streamlined processes and improved output quality. One of the key advantages of utilizing mixing bins is the enhanced mixing efficiency they offer. These bins provide a controlled environment for mixing different components, ensuring thorough blending and homogeneity of materials. This precise mixing ability results in consistent product quality, reducing waste and enhancing overall production output. Furthermore, the use of mixing bins contributes to improved product quality, as the controlled mixing process helps eliminate inconsistencies and irregularities, leading to a more uniform final product. This aspect is particularly crucial in industries where product uniformity and quality standards are paramount. Moreover, mixing bins play a pivotal role in reducing processing time by facilitating efficient mixing processes. The structured design of mixing bins allows for seamless blending of materials, reducing the time required for mixing cycles and expediting overall production timelines. This not only enhances operational efficiency but also enables industries to meet customer demands more effectively by accelerating production schedules. Overall, the benefits of utilizing mixing bins in industrial processes are multifaceted, encompassing enhanced mixing efficiency, improved product quality, and reduced processing time, all of which culminate in heightened productivity levels and operational excellence.
Factors to Consider When Selecting Mixing Bins
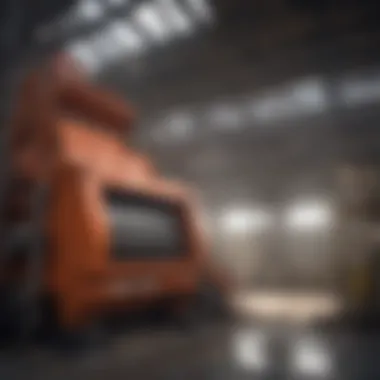
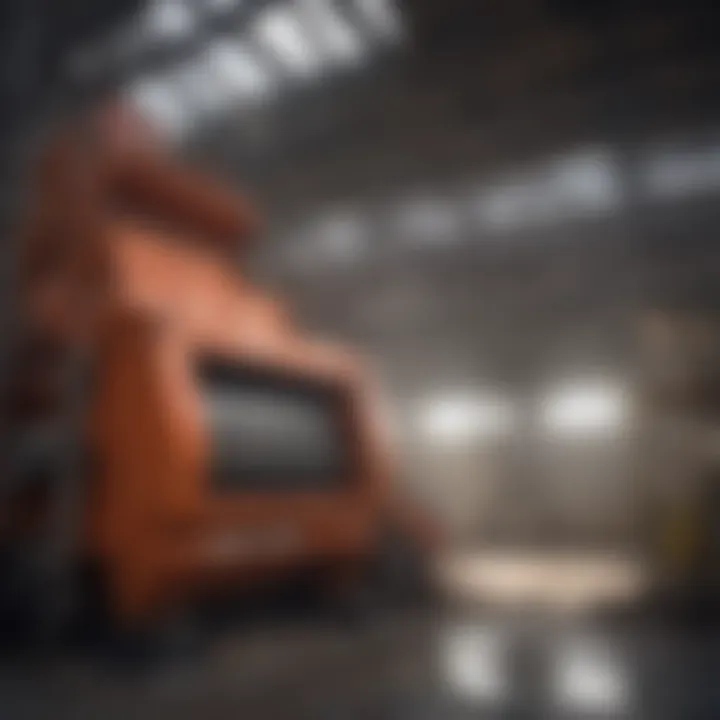
In the realm of industrial processes, the selection of mixing bins holds substantial importance for optimizing operations and achieving efficiency. When delving into the critical aspects of selecting mixing bins, several key factors warrant consideration to ensure seamless integration and functionality within the existing framework. These factors play a pivotal role in determining the success and effectiveness of mixing bin utilization.
Material Compatibility
Material compatibility stands out as a fundamental consideration when selecting mixing bins for industrial applications. The ability of mixing bins to accommodate and effectively blend different types of materials is essential for ensuring the uniformity and quality of the final product. Compatibility issues can lead to issues such as uneven mixing, excessive waste, or even machine failure. Therefore, evaluating the compatibility of materials with the mixing bin construction materials is crucial for long-term efficiency and productivity.
Capacity Requirements
The capacity of mixing bins directly influences the volume of materials that can be processed at any given time. Understanding the specific capacity requirements of the industrial process is vital to prevent bottlenecks and maintain a consistent workflow. Oversized mixing bins may lead to inefficient use of resources, while undersized ones can limit production output. By carefully assessing and aligning the capacity of mixing bins with production demands, industries can enhance productivity and streamline operations effectively.
Maintenance Considerations
Maintenance plays a significant role in ensuring the longevity and optimal performance of mixing bins in industrial settings. Regular maintenance routines encompassing cleaning, inspections, and repairs are essential to prevent downtime and operational disruptions. Additionally, considering factors such as ease of access for maintenance tasks, availability of replacement parts, and preventive maintenance schedules are vital to sustain the efficiency of mixing bins over extended periods.
These meticulous considerations underscore the critical nature of selecting mixing bins thoughtfully and strategically to yield the desired operational efficiency and productivity gains.
Optimizing Mixing Bin Performance
In the realm of industrial processes, optimizing mixing bin performance stands as a critical facet that can significantly elevate operational efficiency and output quality. This section delves into the intricate nuances involved in enhancing the functionality of mixing bins to maximize productivity levels across various sectors. By focusing on the meticulous calibration of components and operational practices, companies can streamline their processes, reduce wastage, and achieve higher levels of uniformity in the mixing process.
When considering the optimization of mixing bin performance, one cannot overlook the importance of proper installation practices. The proper setup of mixing bins lays the foundation for efficient operation and ensures optimal functionality. Elements such as correct positioning, secure anchoring, and alignment of key components like agitators and discharge mechanisms are fundamental in guaranteeing smooth operation and preventing potential malfunctions. Implementing a structured approach to installation is vital in mitigating the risk of downtime and enhancing overall system reliability.
Moreover, the integration of monitoring and control systems plays a pivotal role in fine-tuning mixing bin performance. These systems offer real-time insights into operational parameters, allowing operators to make timely adjustments and optimize mixing conditions. By leveraging advanced monitoring technologies, such as sensors and data analytics, companies can proactively identify performance fluctuations, adjust settings on-the-go, and maintain consistent output quality. The implementation of robust monitoring and control mechanisms is key to achieving precision in the mixing process and meeting stringent quality standards.
Additionally, establishing comprehensive cleaning and maintenance protocols is paramount in sustaining optimal mixing bin performance over time. Regular cleaning routines help prevent contamination, product residue buildup, and equipment wear, ensuring uninterrupted operation and extending the lifespan of mixing bin components. By adhering to stringent maintenance schedules and employing industry best practices, companies can uphold hygiene standards, prolong equipment durability, and sustain peak operational efficiency. Emphasizing the significance of consistent cleaning and maintenance procedures is essential in preserving mixing bin integrity and safeguarding overall process efficiency.
Case Studies of Mixing Bin Implementations
In this section of the article, we delve into the importance and impact of case studies focusing on the implementation of mixing bins in various industrial settings. Case studies serve as valuable real-world examples that highlight the practical benefits and challenges faced when integrating mixing bins into industrial processes. By examining these case studies, industries can gain insights into how different sectors have leveraged mixing bins to optimize efficiency, improve product quality, and streamline operations.
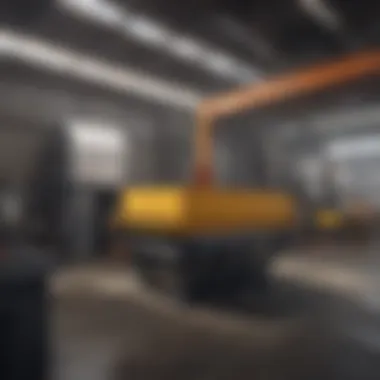
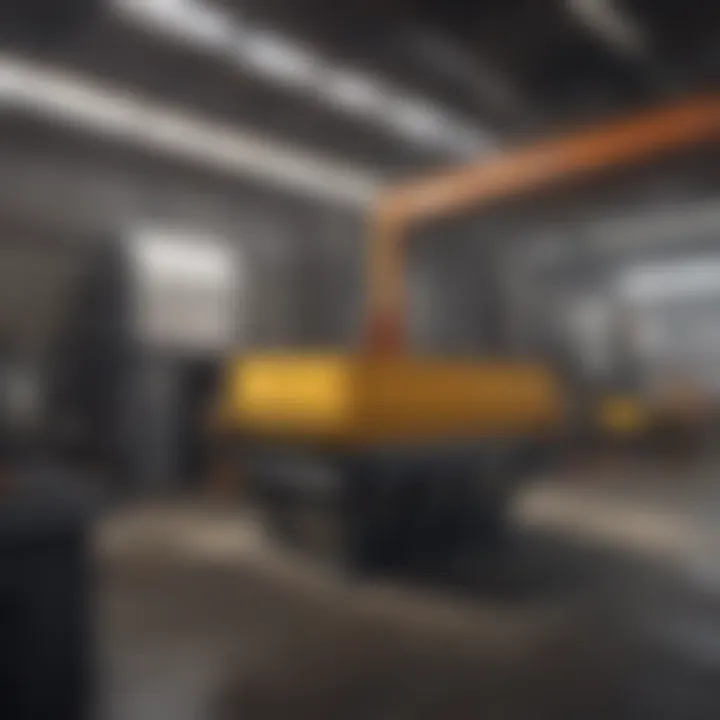
Food Processing Industry
Within the food processing industry, mixing bins play a crucial role in ensuring the uniform blending of ingredients, vital for maintaining product consistency and quality. Case studies in this sector demonstrate how food manufacturers have successfully utilized mixing bins to achieve homogenous mixtures, reduce processing times, and enhance overall operational efficiency. By analyzing these case studies, industry professionals can glean best practices and creative solutions employed by their counterparts to overcome specific challenges unique to food processing.
Chemical Manufacturing Sector
In the realm of chemical manufacturing, the implementation of mixing bins is instrumental in facilitating precise mixing of raw materials for the production of various chemical products. Case studies within this sector shed light on how mixing bins have contributed to improved product quality, increased production output, and reduced wastage. Through detailed examination of these case studies, stakeholders in the chemical manufacturing sector can draw valuable lessons on optimizing mixing processes, mitigating risks associated with chemical handling, and ensuring regulatory compliance.
Pharmaceutical Production
In the pharmaceutical industry, where accuracy and consistency are paramount, mixing bins are employed for the meticulous blending of active ingredients and excipients in drug formulation. Case studies showcasing the integration of mixing bins in pharmaceutical production underscore their role in maintaining strict quality control standards, enhancing batch uniformity, and expediting production cycles. By delving into these case studies, pharmaceutical professionals can gather insights into the application of mixing bins for ensuring product efficacy, adhering to stringent regulatory requirements, and driving innovation in drug development.
Future Trends in Mixing Bin Technology
In the realm of industrial processes, the evolution of mixing bin technology stands at the forefront of innovation, driving significant enhancements in efficiency and productivity. The integration of cutting-edge advancements propels industries towards unparalleled levels of operational optimization. Employing a forward-looking approach in this article, we dissect future trends in mixing bin technology, shedding light on the pivotal role they play in shaping the industrial landscape. By exploring the trajectory of these advancements, businesses can proactively adapt to stay competitive and meet the demands of a rapidly evolving market.
Automation and Robotics Integration
Automation and robotics integration emerge as a game-changer in the domain of mixing bin technology. With the seamless fusion of automation processes and robotic functionalities, industries witness a paradigm shift in operational dynamics. Automated systems streamline workflow processes, minimize human intervention, and maximize precision in material handling and mixing operations. The integration of robotics injects a new level of efficiency, accuracy, and safety in industrial processes, paving the way for augmented production output and reduced operational costs.
Enhanced Mixing Algorithms
Enhanced mixing algorithms signify a revolutionary leap in optimizing mixing bin performance. By harnessing the power of advanced algorithms, industries can achieve unparalleled levels of mixing precision and homogeneity in their products. These sophisticated algorithms analyze multiple variables such as material properties, mixing parameters, and end-product requirements to optimize the mixing process. The application of enhanced mixing algorithms results in superior product quality, reduced processing times, and enhanced overall operational efficiency.
Sustainability Initiatives
In a rapidly evolving industrial landscape, sustainability initiatives take center stage in shaping the future of mixing bin technology. Embracing eco-friendly practices and energy-efficient solutions, industries are aligning their operations with sustainable development goals. From reducing waste to implementing recycling measures, sustainability initiatives surrounding mixing bins aim to minimize environmental impact while maintaining high levels of productivity. By prioritizing sustainability, businesses not only contribute to a greener future but also enhance their brand value and create a positive impact on the ecosystem.
Conclusion
In the realm of industrial processes, the conclusion can serve as a pivotal point where the efficacy and overall success of incorporating mixing bins are evaluated and appreciated. The significance of this section lies in summarizing the pivotal insights surrounding the exploration of mixing bins in industrial operations. As the preceding sections meticulously unfolded the layers of understanding related to mixing bins, the conclusion acts as the compass pointing towards the overarching benefits and considerations for industries.
One of the key emphases in the conclusion is to underscore the transformative impact that effective utilization of mixing bins can have on operational efficiency and productivity. By encapsulating the essence of enhanced mixing efficiency, improved product quality, and reduced processing time discussed in prior sections, the conclusion synthesizes these advantages into a comprehensive narrative. It elucidates how embracing mixing bins can lead to streamlined processes, heightened output quality, and optimized manufacturing timelines, thereby translating into tangible business benefits.
Furthermore, the conclusion sheds light on the critical role of thoughtful consideration when selecting mixing bins for industrial applications. Factors such as material compatibility, capacity requirements, and maintenance considerations significantly influence the performance and longevity of mixing bins within operations. Delving into these aspects in the conclusion provides a well-rounded view on the importance of strategic decision-making in implementing mixing bins effectively.
Overall, the conclusion serves as a beacon of guidance for industries looking to embark on the journey of enhancing their industrial processes through mixing bins. It amalgamates key learnings, best practices, and future considerations, offering a roadmap for organizations to navigate the realm of mixing bin efficiency successfully. By distilling complex information into actionable insights, the conclusion acts as a crucial compass for industries seeking to optimize their manufacturing processes and elevate their competitive edge in today's dynamic industrial landscape.