In-Depth Exploration of Reamer Blades: Design and Usage
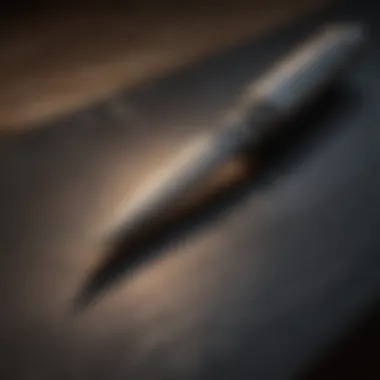
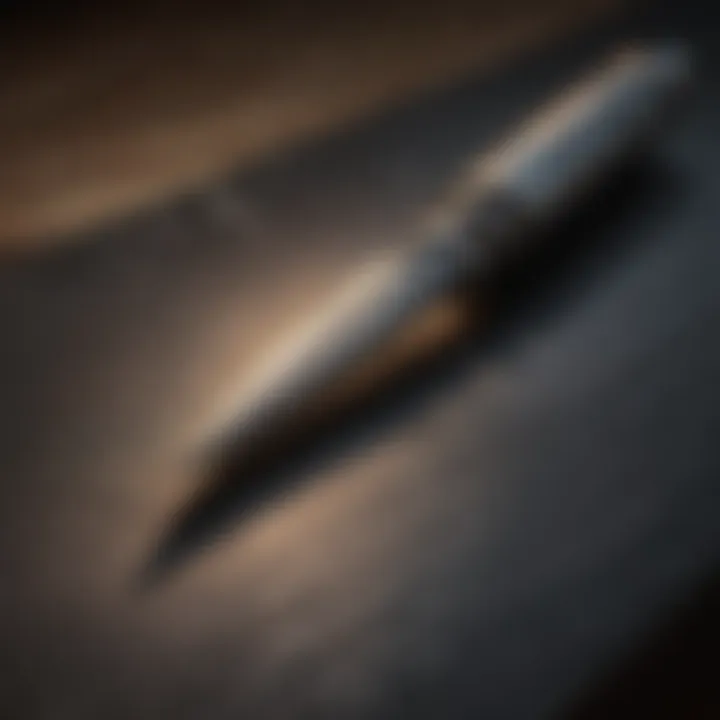
Intro
Reamer blades are essential tools in the manufacturing and engineering landscapes, particularly when precision is paramount. These blades are designed to enlarge holes in materials or achieve a specific dimensional tolerance. Their usage spans multiple industries, from aerospace to construction, where the quality of work heavily relies on the efficacy of the tools involved.
Understanding reamer blades entails examining their design, functionality, and the materials utilized in their production. Additionally, as technology evolves, so do the advancements related to these tools. Manufacturing processes have improved significantly, leading to higher performance and longer-lasting tools that meet the rigorous demands of diverse applications.
The importance of reamer blades cannot be overstated in the context of home improvement projects as well. Homeowners aiming to enhance their living spaces often find themselves confronted with precise drilling tasks. Having a firm grasp on how to utilize reamer blades effectively can lead to superior results and satisfaction in various projects.
Prolusion to Reamer Blades
Reamer blades play a crucial role in the realm of machining and engineering. Their design and functionality ensure that precision is maintained in the manufacturing process. Understanding what reamer blades are, and their applications is not only beneficial for professionals but also for house owners and enthusiasts engaged in home improvement projects.
Definition and Purpose
Reamer blades are specialized cutting tools used to enlarge and finish holes with high accuracy. Unlike drill bits which create holes, reamers refine existing holes to achieve a specific diameter or smoothness. The practical purpose of using a reamer is to enhance the dimensional accuracy and surface quality of a hole, making it ready for fitting components or facilitating assembly in diverse applications. In summary, reamer blades serve to create a perfect fit, which is essential in critical operations.
Importance in Engineering
In engineering, precision is non-negotiable. Reamer blades are indispensable tools in ensuring that this precision is achieved. Manufacturing components for machinery or construction requires strict adherence to specific measurements. Reaming allows engineers to correct discrepancies that may arise during the drilling process, thus minimizing waste and ensuring that parts align correctly. Moreover, when using modern reamer blades made from high-performance materials, engineers can achieve finer tolerances.
"Precision in engineering is paramount, and reamer blades hold the key to achieving that standard."
Additionally, reamer blades contribute to efficiency. Using a reamer after drilling saves time and resources by reducing the need for multiple tool changes. Furthermore, they can accommodate various materials, from metals to composites, making them versatile tools in the industry.
Historical Development of Reamer Blades
The historical development of reamer blades offers a vital understanding of their evolution and increasing significance in engineering. This section emphasizes how advancements in design, materials, and technology have shaped the present capabilities of reamer blades. Knowing this history allows users to appreciate the complexity and sophistication involved in modern manufacturing processes.
Evolution Over Time
Reamer blades have a long history that dates back centuries. The earliest versions were simple hand tools used for enlarging holes and achieving more precise dimensions. Artisans and metalworkers relied on rudimentary designs, primarily crafted from iron or bronze. These initial models focused on the basic function without deep consideration for efficiency or precision.
As industrialization progressed during the 19th century, the demand for precision increased. This prompted the development of more complex designs, incorporating improved materials and production techniques. For instance, the introduction of high-speed steel in the early 20th century revolutionized the manufacturing of reamer blades. This material not only offered greater hardness but also resilience against wear and heat. The blades became not just tools but essential instruments in precision engineering.
In the late 20th century, the advent of Computer Numerical Control (CNC) technology brought forth a new era for reamer blades. The ability to program machines allowed for more intricate designs that enhanced performance while maintaining higher levels of accuracy. This technological leap ensured that reamer blades could meet the rigorous demands of contemporary manufacturing environments.
Key Innovations
Throughout the history of reamer blades, several innovations stand out due to their profound impact on performance and application:
- Material Advancements: Transitioning from basic metals to high-speed steel and then to carbide and cobalt alloys has significantly elevated the durability and precision of reamer blades.
- Flute Design: The evolution of flute geometry is crucial. Optimized flute designs enhance chip removal, thus minimizing clogging and ensuring cleaner cuts.
- Coating Technologies: The introduction of coatings such as titanium nitride has decreased friction and improved wear resistance. These coatings enhance the lifespan and effectiveness of reamer blades during machining operations.
- Smart Tools: Incorporating sensors and IoT technology into reamer designs allows for better performance monitoring and predictive maintenance. This innovation leads to more efficient machining processes and reduces downtime.
This historical perspective illustrates that reamer blades are not static tools; they are continuously improving. As industries evolve, so do the methods used to produce and implement them effectively.
Understanding the progression of reamer blades provides insight into how they are perceived and utilized today. It also highlights the importance of ongoing research and development in producing tools that meet the rigorous demands of modern engineering applications.
Types of Reamer Blades
Understanding the various types of reamer blades is integral to appreciating their roles and applications in precision machining. Each design serves specific purposes and influences the performance of the machining tasks. When selecting a reamer blade, the type affects not just effectiveness but also the quality of finishes, operational efficiency, and compatibility with different materials. Choosing the right type can significantly enhance outcomes in projects, making it vital for users to comprehend the distinctions.
Straight Reamers
Straight reamers are among the most common types of reamer blades used in various applications. These tools have parallel cutting edges, making them ideal for creating precise, cylindrical holes in materials. Often employed in metalworking, they provide a consistent diameter and smooth finish without altering the existing geometry of the hole.
One primary benefit of straight reamers is their ease of use. They are straightforward to set up, which can save time in production settings. Furthermore, these reamers can be utilized in manual machines, CNC lathes, and milling machines. This versatility allows them to work efficiently across a range of machining environments.
Key considerations when using straight reamers include maintaining proper feed rates and aligning them accurately with the workpiece. Improper use can lead to dulling of the cutting edges or even damage to the tool itself.
Tapered Reamers
Tapered reamers serve a unique purpose by creating conical holes. With a gradual reduction in diameter from top to bottom, they are especially useful in applications requiring an angle or a specific taper. This makes them popular in areas like automotive or aerospace manufacturing, where precise fitment is crucial.
The design of tapered reamers allows for smooth transitions between different parts, reducing stress on components. This fluidity is essential to ensure that assemblies fit together snugly without gaps.
Advantages of using tapered reamers include their ability to align parts more effectively. They also help in managing tolerances in complex assemblies. However, care must be taken during operation, as incorrect handling can lead to non-uniform tapers or an inconsistent hole profile.
Spiral Reamers
Spiral reamers, characterized by their helical cutting edges, present a distinct alternative for specific machining needs. These tools excel in removing material quickly, offering efficient chip removal and improved performance in deeper holes. Their design allows for greater flexibility, which is beneficial for operations requiring high precision.
The efficiency gained from using spiral reamers stems from their ability to create a smoother finish and better hole geometry. Consequently, this type of reamer is ideal in high-speed drilling applications and is frequently seen in industries like aerospace and heavy machinery.
However, selection of a spiral reamer necessitates careful consideration of the material and thickness of the workpiece. As they can exert considerable force, ensuring compatibility with the workpiece material is essential to prevent tool damage or workpiece failure.
Important Note: The decision on which type of reamer blade to use should align with the specific requirements of the task at hand, considering factors such as material type, desired finish, and operational conditions.
Materials Utilized in Reamer Blade Construction
In the realm of manufacturing and engineering, the selection of materials for reamer blades is pivotal. This aspect directly influences their functionality, durability, and performance in various applications. Understanding the materials utilized in reamer blade construction not only aids in optimizing their use but also highlights the distinct advantages each material brings to the table.
High-Speed Steel
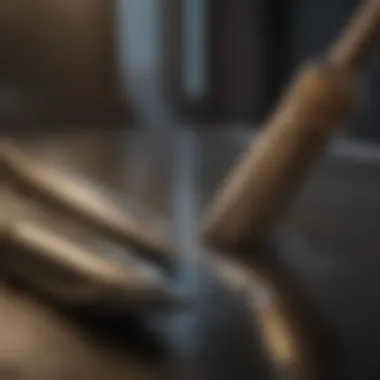
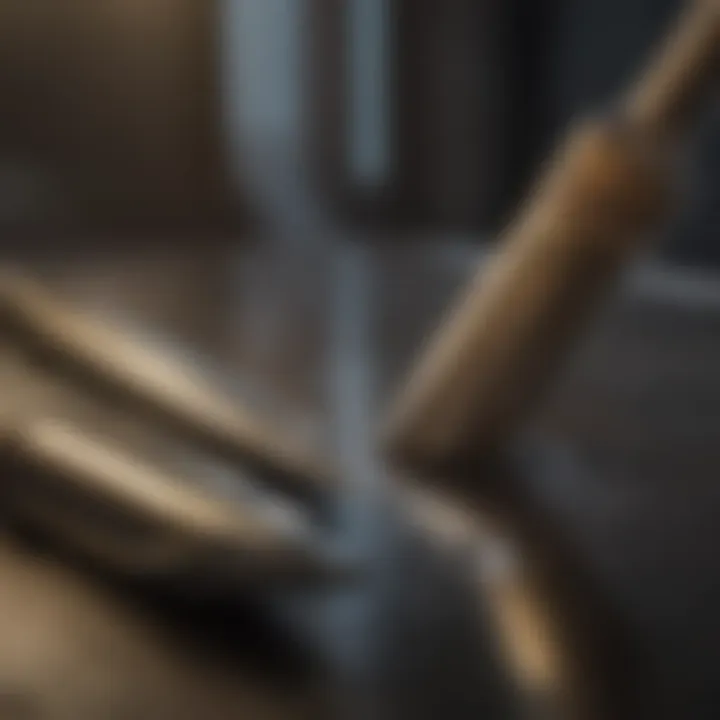
High-speed steel (HSS) has been a favored choice for reamer blades for many years. It is well-known for its ability to withstand high temperatures without losing hardness. This property is crucial when working at high speeds in machining processes. HSS reamers are versatile and can effectively process a wide range of materials, making them an excellent choice for general applications.
Some benefits of high-speed steel blades include:
- Affordability: Generally, HSS is more cost-effective than other materials like carbide.
- Ease of Resharpening: HSS can be sharpened relatively easily, ensuring a longer lifespan and sustained performance.
- Toughness: It's less brittle than carbide, offering resilience when faced with varying machining conditions.
Carbide
Carbide reamer blades offer a significant upgrade in durability and cutting performance compared to their HSS counterparts. Carbide, specifically tungsten carbide, is extremely hard, allowing it to maintain cutting edges longer and withstand higher cutting speeds. This makes carbide blades ideal for precision machining in hard materials.
Key attributes of carbide blades include:
- High Hardness: Carbide rates much higher on the Mohs scale of hardness, which helps it resist wear.
- Temperature Resistance: Carbide can perform under higher temperature conditions, prolonging tool life.
- Precision: These blades offer exceptional accuracy in machining tasks, enhancing the overall quality of the finished product.
Cobalt Alloys
Cobalt alloys are another alternative that combines the hardness of carbide with the toughness of high-speed steel. This balance creates reamer blades that can endure rigorous machining processes, particularly in applications where heat generation is significant.
The merits of cobalt alloy blades include:
- Enhanced Wear Resistance: They exhibit superior resistance to wear compared to HSS, extending operational lifespan.
- Stability Under Pressure: Cobalt alloys maintain structural integrity even under heavy loads and extreme conditions.
- Versatility: Suitable for both soft and hard materials, these blades can adapt to a wide range of applications.
"Material selection is essential for the efficiency and efficacy of reamer blades. It affects both the machining process and the quality of the final output."
Reamer Blade Design Principles
Reamer blades play a crucial role in precision machining and other applications. Understanding the design principles behind these tools is key to selecting the right reamer for specific tasks. In this section, we will cover important aspects such as geometric considerations, cutting edge configurations, and flute design. These elements not only influence the performance of reamer blades but also affect their durability and efficiency.
Geometric Considerations
Geometric considerations in reamer blade design refer to the shape and structure of the tool. The design must optimize cutting performance and ensure longevity.
- Tapered edges: These contribute to smoother cutting by reducing friction.
- Rake angles: The angle at which the cutting edge is positioned affects how the blade engages with material. Higher angles lead to more aggressive cutting. Lower angles are better for finer finishes.
- Diameter variation: Selecting the appropriate diameter ensures that the reamer can achieve the intended level of precision.
Proper geometric design is essential for minimizing wear and maximizing efficiency. It helps in preventing issues like binding or excessive heat generation during operation.
Cutting Edge Configurations
The cutting edge configuration is another vital aspect in the design of reamer blades. This involves the arrangement and shape of the blade edges that do the actual cutting.
Different configurations include:
- Straight edges: Common for basic reaming tasks, offering stability and ease of control.
- Compound angles: They improve chip removal, crucial for maintaining cleanliness during machining.
- Angular edges: These are meant for specific applications, providing a sharper cut suited for hard materials.
Choosing an appropriate cutting edge configuration can significantly improve the outcomes of machining processes. It can lead to better surface finishes and precision.
Flute Design
Flute design contributes significantly to the operational efficiency of reamer blades. The flutes facilitate chip removal and help in cooling the tool during operation.
Key elements in flute design include:
- Number of flutes: More flutes can lead to enhanced chip removal but may also increase friction.
- Flute depth & width: These dimensions affect the volume of chips that can be evacuated, impacting performance.
- Flute shape: Spiral flutes, for instance, are effective for faster chip evacuation and smoother cutting.
Good flute design is of utmost importance to ensure that the reamer operates at peak efficiency. It minimizes clogging and heat buildup, ultimately prolonging the tool's life.
"The principles of design directly correlate with the performance of reamer blades in various contexts."
Functions and Applications of Reamer Blades
The functions of reamer blades play a crucial role in various machining processes. These tools are essential for achieving the desired precision and surface finish in holes made by other cutting tools. The applications of reamer blades extend across many industries, making them invaluable for both large-scale manufacturing and smaller, specialized jobs. Understanding these functions and applications enhances one's appreciation of reamer blades, as they are tailored for specific needs.
Precision Machining
Reamer blades are pivotal in precision machining. They refine the dimensions of holes to meet strict tolerances. Unlike regular drills, which create holes with a rougher interior finish, reamers provide a smoother finish. This is important in assemblies where parts must fit tightly, such as in automotive and aerospace components.
Using a reamer, operators can achieve hole diameters that are exact. It minimizes the risk of misalignment in subsequent operations. Therefore, in industries demanding high precision, reamers become an integral tool. They can adapt to various materials, improving efficiency and reducing production time.
Boring Operations
Boring operations often require precision beyond what a basic drill can provide. Reamer blades excel in this area due to their design. Boring typically results in larger diameter holes from smaller ones. Here, reamers ensure that the enlarged hole meets the specifications necessary for fitting other components.
During the boring process, a reamer can remove just a small amount of material, allowing it to correct any imperfections left from drilling. This not only enhances the overall quality of the hole but also contributes to the longevity of the parts being machined. The use of reamer blades in boring operations increases productivity while decreasing the likelihood of costly errors.
Repair and Maintenance Work
In repair and maintenance work, reamer blades serve a significant purpose. As machinery ages, parts may wear out and require refurbishing. Reaming can restore these components back to their original specifications.
The precision that reamers provide is beneficial when addressing issues like worn holes. They can clean out and restore holes to accommodate new parts or hardware. This not only extends the life of the equipment but also saves costs on replacing entire units. Thus, knowing how to properly implement reamer blades is important for maintenance personnel.
In summary, reamer blades are critical tools in precision machining, boring operations, and repair work. Their ability to produce accurate holes with excellent surface finishes makes them essential in various industrial applications.
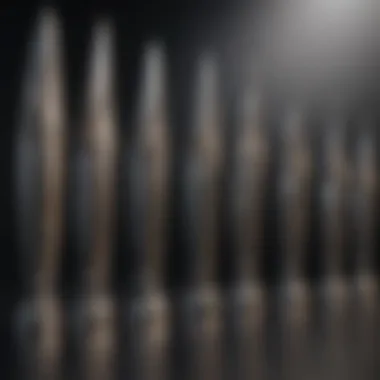
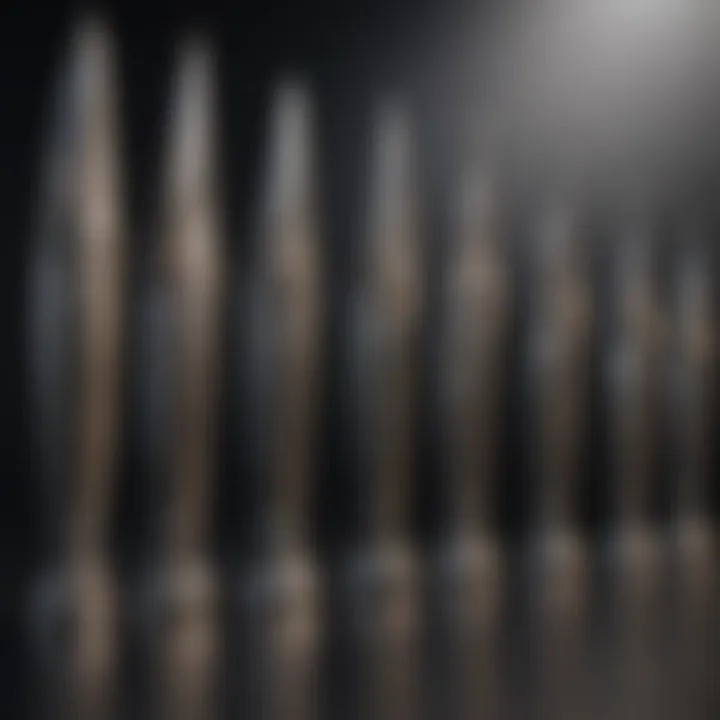
The understanding of these functions will inform the selection and use of reamer blades, ensuring optimal performance in any task.
Selection Criteria for Reamer Blades
Choosing the right reamer blade is crucial for achieving desired outcomes in various machining processes. It involves considering multiple factors that influence not only the performance of the reamer but also the quality of the final product. Understanding these selection criteria can lead to improved efficiency, enhanced precision, and longer tool life.
Material Compatibility
Material compatibility is one of the primary considerations when selecting reamer blades. Different materials interact uniquely with the cutting edges of the reamers. For instance, high-speed steel is often used for softer metals, while carbide may be better suited for harder materials. Choosing the correct material ensures optimal performance and minimizes wear.
When looking at compatibility, one must consider several elements:
- Type of Workpiece Material: Assessing whether the reamer will be used on materials like aluminum, steel, or titanium is essential, as each requires different blade properties.
- Cutting Environment: The presence of different chemicals or heat during operation can affect the choice of blade material.
Using the correct material reduces the risk of tool failure in critical applications.
Desired Finish Quality
Another significant factor is the desired finish quality of the machined hole. The smoother and more precise the finish required, the more attention needs to be paid to the selection of the reamer. Reamers with sharper and more accurately formed cutting edges provide better surface finishes, essential in components where tight tolerances are necessary.
Some points to consider regarding finish quality include:
- Surface Roughness Requirements: Specifications for how smooth the surface should be often dictate the reamer design.
- Application Needs: Industries like aerospace or medical may require extremely fine finishes, necessitating specific reamer types.
Selecting a reamer that matches the finish quality requirements can save time and costs associated with additional finishing processes.
Tolerance Requirements
Tolerance indicates the allowable variation in a dimension and is vital in ensuring that parts fit and function properly. Different applications will have varying tolerance requirements, influencing the choice of reamer blade.
Factors affecting tolerance requirements include:
- Precision Engineering Standards: Some sectors have stringent standards that must be met, making it essential to select a reamer capable of achieving those tolerances.
- Tool Wear Factors: As reamers wear, their ability to maintain tight tolerances diminishes. It is critical to consider how often reamers will be replaced or sharpened to preserve accuracy.
Inaccurate tolerances can affect the integrity of the final product, making the selection of the proper blade critical in manufacturing applications.
Inadequate consideration of these selection criteria can lead to increased costs, unnecessary rework, and potential project delays. Understanding the intricacies involved ensures better choices are made, yielding superior results.
Technological Advancements in Reamer Blades
The rapid evolution of technology has significantly transformed the production and utilization of reamer blades. Understanding these advancements is vital for manufacturers and end-users alike. The integration of modern techniques enhances performance, improves accuracy, and reduces operational costs. Key advancements can be categorized into innovations in automation and material treatments, which play significant roles in expanding the capabilities of reamer blades.
Computer Numerical Control (CNC) Technology
Computer Numerical Control (CNC) technology represents a major leap in the machining world. CNC machines automate the movement of cutting tools, including reamer blades, by executing pre-programmed sequences of machine control commands. This precision enables high-volume production of complex shapes with exceptional repeatability.
- Precision and Accuracy: With CNC technology, reamer blades can be crafted and manipulated with minuscule tolerances. This results in remarkably precise finished products that meet rigorous specifications.
- Customization: CNC allows for tailored designs based on specific project requirements. Manufacturers can create unique blade configurations, which can enhance performance for particular applications, thus catering to a diverse array of industries.
- Reduced Waste: Enhanced accuracy leads to less material wastage, which is both cost-effective and environmentally friendly. This aligns with broader sustainability goals within manufacturing sectors.
- Efficiency: The automation of processes streamlines production. This efficiency means shorter lead times and the ability to quickly respond to market demands, giving firms a competitive edge.
The importance of CNC technology cannot be overstated. It not only contributes to higher quality outcomes but also impacts the overall productivity of operations involving reamer blades.
Coating Technologies
The introduction of advanced coating technologies has drastically improved the performance of reamer blades. These innovations enhance durability, reduce friction, and improve resistance to wear. Several notable coating technologies are essential to consider:
- Titanium Nitride (TiN): This is a widely used coating that has excellent hardness and wears resistance. Reamer blades coated with TiN show improved life span, which leads to lower replacement costs.
- Diamond Coatings: Implementation of diamond-like carbon coatings enhances the hardness of reamer blades further. These coatings significantly decrease friction during cutting operations and increase the efficiency of the reaming process.
- Aluminum Oxide Coatings: This type is beneficial for reamer blades used in softer materials. It provides a smoother surface, which helps in producing higher quality finishes on workpieces.
Maintenance of Reamer Blades
Maintenance of reamer blades is vital for achieving consistent performance and prolonging the lifespan of these tools. Regular upkeep not only ensures that the blades function effectively but also enhances precision in machining tasks. Understanding how to properly maintain these tools can save resources and improve overall project outcomes.
Sharpening Techniques
Sharpening reamer blades is essential for maintaining their cutting efficiency. Various techniques can be employed depending on the type of reamer blade. For instance, manual sharpening involves using a sharpening stone or diamond file to revive the cutting edges. Ensure that the angle of sharpening matches the original bevel to retain the blade's geometry.
Another popular method is using a specialized grinding machine designed for reamers. This equipment can provide a more precise sharpening angle, improving the bladeβs performance.
It's important to regularly inspect the cutting edges, as dull blades can lead to unnecessary wear and tear, potentially damaging both the reamer and the workpiece.
Cleaning Practices
Keeping reamer blades clean is critical. After each use, they should be thoroughly cleaned to remove any residue or chips. A simple solution is to utilize a cleaning solvent suitable for metal tools. Soaking the blades in the solution for a few minutes helps dissolve oils and contaminants.
After cleaning, use a soft brush to scrub off stubborn residues. Wipe the blades dry with a clean cloth to prevent rust formation. Proper cleaning methods not only help keep the blades effective but also enhance safety during usage.
Storage Recommendations
Proper storage of reamer blades can significantly impact their lifespan. Blades should be stored in a dry, clean environment to prevent corrosion. Consider using blade holders or cases specifically designed for reamers. These holders will protect the tool edges from inadvertent damage and contamination.
Moreover, when storing blades, avoid stacking them haphazardly, which can cause nicks or scratches. Ensure you are placing them in an organized manner where each blade is easy to access and inspect. By following these storage best practices, one can maintain the integrity and performance of reamer blades for extended periods.
"Regular maintenance not only improves safety but enhances efficiency in your projects."
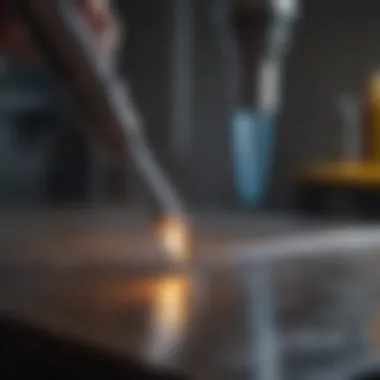
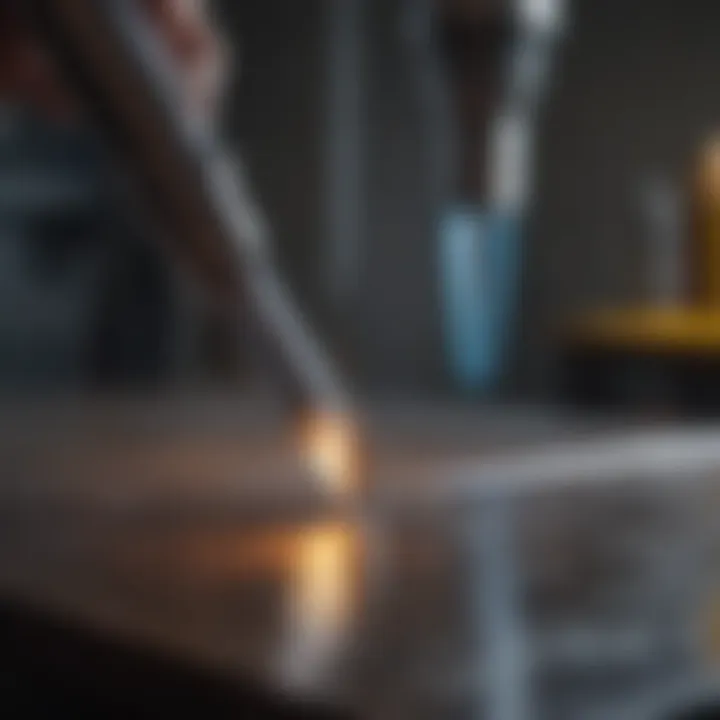
In summary, consistent maintenance of reamer blades encompasses sharpening, cleaning, and proper storage. By adhering to these guidelines, users can maximize their tool investment, ensuring precision and effectiveness in their work.
Safety Considerations
Safety considerations are pivotal in the context of reamer blades. These tools, while effective in enhancing precision, can also pose significant risks if not handled properly. Understanding the safety measures involved is essential to protect users from injuries and accidents during operation. Elements such as proper handling procedures and reliance on personal protective equipment (PPE) are crucial aspects of ensuring a safe working environment.
"Safety first, because injuries can last a lifetime."
Reamer blades, if mishandled, can lead to unintended consequences, including cuts, lacerations, and even severe accidents. Therefore, familiarizing oneself with safe handling practices can greatly reduce the risk of such incidents. Additionally, certain protocols should be followed in accordance with safety standards relevant to the tool's application. The importance of these considerations cannot be overstated, as the secure operation of these blades ultimately promotes increased productivity and ensures that tasks can be completed efficiently without harm.
Proper Handling Procedures
Proper handling of reamer blades is essential to minimizing risks during their use. Care must be taken throughout the entire process, from transport to operation and finally to storage. When moving reamer blades, always hold them by their non-working edge. This prevents accidental contact with cutting edges. It is also advisable to keep blades sheathed or stored in protective casings when not in use.
When operating the tool, ensure that all safety guards are in place. It is important to regularly inspect blades for wear and damage before use. Dull or broken blades not only compromise the quality of work but also increase the likelihood of accidents. Establishing a routine check for integrity helps maintain both safety and effectiveness. Furthermore, operators must be trained in the correct usage of reamer blades to avoid improper techniques that could lead to injuries.
Personal Protective Equipment (PPE)
The use of personal protective equipment (PPE) is another essential aspect of ensuring safety when working with reamer blades. Appropriate PPE can help shield the user from potential injuries or hazards present during blade operation. Key items of PPE include:
- Safety goggles: Protects the eyes from metal shavings or debris.
- Cut-resistant gloves: Offers protection against cuts while handling blades, ensuring a firm grip.
- Hearing protection: Necessary in environments with high noise levels associated with machining.
- Steel-toed boots: Provides foot protection against heavy objects that may accidentally fall.
Incorporating these protective measures into daily practice significantly reduces the risk of injury. It is crucial for those working with reamer blades to not only understand their significance but also to routinely wear this equipment while handling and operating the tools. By prioritizing safety and proper handling practices, operators can create a more secure workplace, ultimately benefiting productivity and efficiency.
Environmental Impact of Reamer Blade Production
The importance of examining the environmental impact of reamer blade production cannot be overstated. As industries grow, their need for efficient tools increases. However, this growth often comes at a cost to the environment. Understanding how reamer blades are produced, and the materials used in their manufacture, is critical. We must consider how this production affects our ecosystem and what sustainable practices can be implemented.
Sustainable Materials
Using sustainable materials in reamer blade production is crucial for reducing environmental footprints. Metals like high-speed steel and carbide dominate this sector. However, choosing recycled materials can lessen the demand for virgin resources.
Here are some key points regarding sustainable materials:
- Recycled Steel: Integrating recycled steel into production minimizes resource extraction and energy usage. This reduces greenhouse gas emissions.
- Biodegradable Coatings: Innovative coatings that decompose safely can replace traditional, more harmful options. Such materials are essential for minimizing long-term environmental damage.
- Reduced Toxicity: Selecting low-toxicity substances in manufacturing processes helps protect workers and surrounding communities.
By utilizing sustainable materials, manufacturers can meet the demand for reamer blades while protecting the planet.
Reducing Waste in Manufacturing
Waste reduction during the manufacturing phase of reamer blades is critical. Inefficient processes often lead to excess scrap and pollutants. Here are strategies to minimize waste and enhance sustainability:
- Lean Manufacturing: Adopting lean principles focuses on minimizing waste throughout production. This philosophy encourages efficiency in resource use while maintaining quality.
- Recycling Scrap Metal: Implementing systems to recycle scrap metal generated during the manufacturing of reamer blades ensures that materials are reused. This significantly cuts down on waste.
- Process Optimization: Evaluating and refining processes can lead to less energy consumption and reduced waste generation. Continuous improvement initiatives can impact the production line positively.
"Every industry should rethink its practices to ensure a sustainable future. The production of tools like reamer blades must evolve alongside environmental considerations."
Future Trends in Reamer Blade Technology
The development of reamer blades is not standing still. New trends in technology are emerging, creating potential for efficiencies and performance improvements. The focus on innovation is crucial for maintaining competitive advantages in industries reliant on precision tools. Understanding these trends enhances potential in engineering applications and fosters sustainable production processes.
Smart Tools and IoT Integration
One significant trend is the integration of smart technology within reamer blades. Tools now are being designed with embedded sensors that provide real-time data about their performance. This technology allows for better monitoring of wear and tear, helping users to optimize their operations.
Benefits of this innovation are notable:
- Preventative Maintenance: By monitoring conditions, manufacturers can anticipate failures and perform maintenance before issues arise.
- Increased Efficiency: Real-time data can lead to adjustments in tooling patterns, reducing machining time and improving outcomes.
- Cost Savings: Efficient management of resources and time contributes to reduced operational costs.
This integration exemplifies how modern technology can enhance traditional tools, leading to smarter work environments.
Advancements in Material Science
Material science continues to evolve, significantly impacting reamer blade technology. New composites and coatings are emerging, which improve durability and performance under extreme conditions. For example, the use of graphene-infused materials is becoming more prevalent, offering lights weight but high strength.
Factors contributing to these advancements include:
- Improved Wear Resistance: Higher resistance means longer tool life and less frequent replacements.
- Enhanced Precision: Advanced materials enhance the cutting process, allowing for finer tolerances.
- Adaptability to Various Environments: New materials can perform well in different settings, from plastics to metals, broadening usability.
These advancements pave the way for future applications in diverse industries, reflecting the importance of research and development in maintaining tool performance in changing landscapes.
"The evolution of reamer blade technology reflects a broader trend towards efficiency in manufacturing, integrating both smart features and advanced materials."
As reamer blade technology progresses, it is evident that both smart technologies and advancements in material science play crucial roles in shaping the future of these tools. Keeping a close eye on these trends will allow professionals in the field to adapt and innovate, ensuring best practices and operational efficiencies.
Ending
In any comprehensive examination of reamer blades, the conclusion serves as a vital component. It encapsulates the previously discussed elements, reinforcing their significance in the broader context of engineering and manufacturing. The importance of reamer blades in precision machining cannot be overstated. They play a crucial role in achieving desired tolerances, enhancing overall workflow efficiency, and ensuring that finished products meet stringent quality standards.
Summary of Key Points
This article has provided a detailed analysis of several key aspects related to reamer blades. Significant points include:
- Types of Reamer Blades: Various types such as straight, tapered, and spiral offer specific advantages depending on the application.
- Materials Used: High-speed steel, carbide, and cobalt alloys are common materials chosen for their durability and performance.
- Design Principles: Geometric considerations and edge configurations directly affect cutting efficiency and precision.
- Functions and Applications: Reamer blades find utility in precision machining, boring operations, and maintenance work, making them versatile tools in many industries.
- Selection Criteria: Factors like material compatibility, finish quality, and tolerance requirements must be considered when choosing the right reamer blade.
- Maintenance and Safety: Regular sharpening, cleaning, and appropriate handling practices ensure longevity and safe usage.
- Environmental Impact: Sustainable practices in production and waste reduction are increasingly important in today's manufacturing environment.
- Future Trends: The advent of smart tools and advancements in material science will likely drive future developments.
Importance of Continued Innovation
The realm of reamer blades is dynamic, where continued innovation remains a necessity. As industries evolve, the demand for more precise and efficient tools increases. Advancements such as Computer Numerical Control (CNC) technology and innovative coating methods not only enhance performance but also extend the usability of these tools under various conditions.
Moreover, the environmental impacts of production methods must be regularly assessed. The integration of sustainable materials and practices is becoming a defining characteristic of responsible manufacturing.