Unveiling the Fascinating Realm of Aluminum Terminal Lugs: A Comprehensive Guide
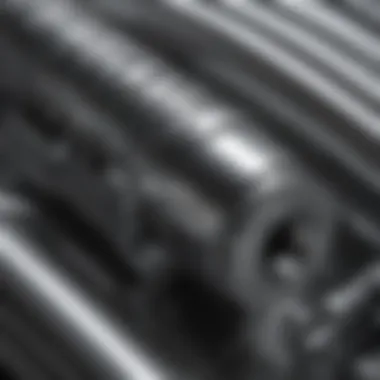
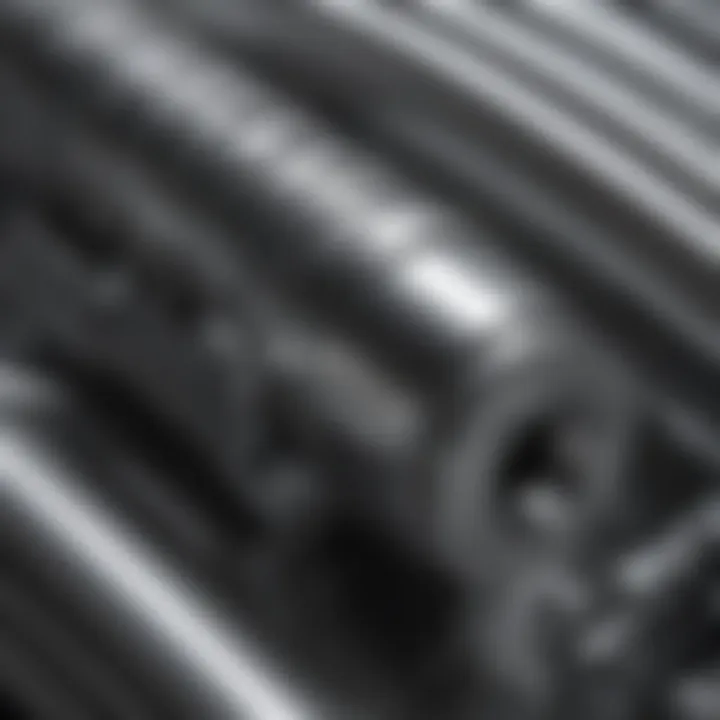
Overview of Aluminum Terminal Lugs
In the realm of the home improvement industry, aluminum terminal lugs play a critical role in ensuring efficient electrical connections. These essential components serve as connectors between electrical wires and other components, facilitating the safe and reliable transfer of electrical current within residential systems. The importance of aluminum terminal lugs cannot be overstated, as they provide stability and durability to electrical connections, promoting the overall safety and functionality of household electrical systems.
Common Challenges and Solutions
Homeowners often encounter common challenges pertaining to aluminum terminal lugs, such as corrosion, improper installation, and compatibility issues. To address these concerns effectively, homeowners can implement solutions like using anti-corrosion coatings, ensuring proper installation techniques following manufacturer guidelines, and verifying compatibility with existing electrical components. By proactively addressing these challenges, homeowners can maintain optimal performance and safety in their electrical systems.
Product Recommendations
When considering top-notch aluminum terminal lugs in the market, [Industry Brand] offers a range of high-quality products known for their durability and reliability. These aluminum terminal lugs boast features such as high conductivity, corrosion resistance, and easy installation, making them ideal choices for residential electrical applications. By opting for [Industry Brand] products, homeowners can enjoy peace of mind knowing that their electrical connections are secure and efficient.
Step-by-Step Guides
To implement improvements or solutions related to aluminum terminal lugs, homeowners can follow these practical steps:
- Assessment: Begin by assessing the current state of aluminum terminal lugs in the electrical system, checking for any signs of wear or damage.
- Selection: Choose the appropriate aluminum terminal lugs based on wire size, current rating, and environmental factors for optimal performance.
- Preparation: Ensure a clean and proper installation environment, free of dust or debris that may affect the connection quality.
- Installation: Follow manufacturer guidelines for installation, including proper crimping techniques, torque specifications, and inspection protocols.
- Testing: After installation, conduct thorough testing to verify the integrity and functionality of the electrical connections, addressing any issues promptly for a reliable electrical system.
By adhering to these step-by-step guides, homeowners can enhance the performance and longevity of their electrical systems featuring aluminum terminal lugs.
Introduction
In the realm of electrical systems, the utilization of aluminum terminal lugs plays a pivotal role in ensuring efficient and reliable connections. This article embarks on an exploratory journey into the nuanced world of aluminum terminal lugs, shedding light on their fundamental aspects, applications, and implications. Understanding the significance of these components is essential for anyone involved in electrical installations and maintenance.
Understanding Aluminum Terminal Lugs
Definition and Function
Aluminum terminal lugs serve as essential connectors that facilitate the transfer of electrical current between conductors. Their primary function is to establish secure and durable connections within an electrical system. The key characteristic that distinguishes aluminum terminal lugs is their ability to conduct electricity effectively while withstanding varying environmental conditions. This feature makes them a popular choice in numerous applications where reliability and conductivity are paramount. Despite their advantageous conductivity properties, aluminum terminal lugs may be susceptible to corrosion over time, necessitating proper maintenance to ensure long-term functionality.
Types of Aluminum Terminal Lugs
There are various types of aluminum terminal lugs available in the market, each designed to cater to specific connectivity needs. From copper-plated to pure aluminum options, these lugs offer a range of features to suit diverse applications. The key characteristic of different aluminum terminal lug types lies in their compatibility with various wire sizes and insulation types. Selecting the right type of lug is crucial to ensuring optimal electrical connections. While aluminum terminal lugs provide many benefits such as cost-effectiveness and easy installation, it is essential to consider factors like thermal expansion and hardware compatibility when choosing the appropriate type for a given application.
Significance in Electrical Systems
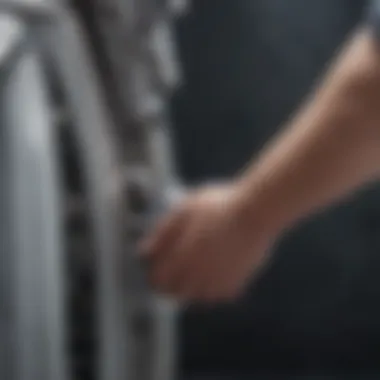
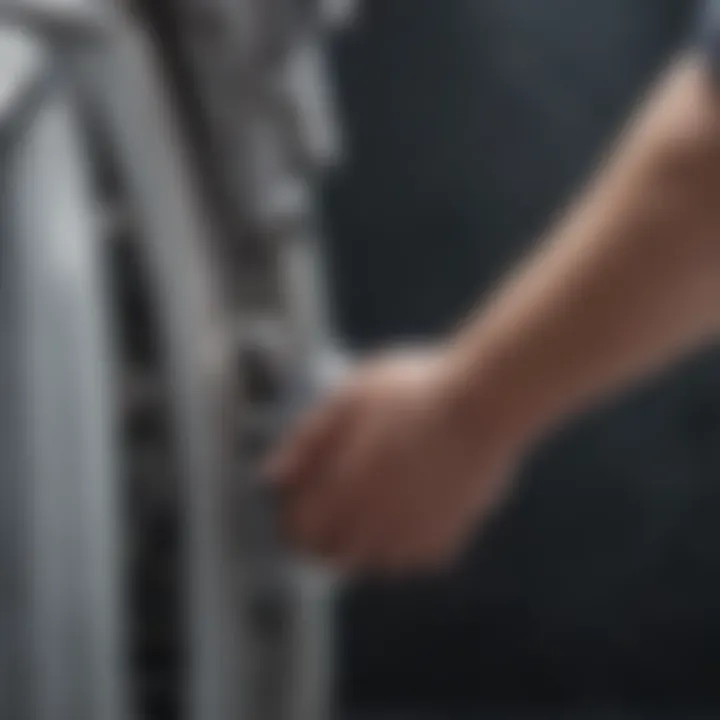
Conductivity and Corrosion Resistance
The conductivity and corrosion resistance of aluminum terminal lugs are crucial considerations in electrical systems. These properties determine the efficiency and longevity of electrical connections. Aluminum's high conductivity allows for the seamless flow of electricity, minimizing power loss and ensuring stable performance. Additionally, the corrosion resistance of aluminum terminal lugs protects them from environmental factors that could degrade their functionality over time. By maintaining high conductivity levels and resisting corrosion, aluminum terminal lugs contribute significantly to the reliability and safety of electrical systems.
Durability and Longevity
The durability and longevity of aluminum terminal lugs make them indispensable components in electrical installations. These lugs are engineered to endure various operational conditions without compromising performance. Their exceptional durability ensures that electrical connections remain secure even under intense loads or environmental stressors. Moreover, the longevity of aluminum terminal lugs minimizes the need for frequent replacements, reducing maintenance costs and downtime. By combining superior durability and extended lifespan, these lugs enhance the overall effectiveness and efficiency of electrical systems.
Common Applications
Industrial Settings
In industrial settings, aluminum terminal lugs find extensive use due to their robust nature and adaptable design. Their key characteristic of withstanding high temperatures and chemical exposure makes them ideal for industrial applications where harsh conditions are prevalent. Additionally, aluminum terminal lugs offer cost-effective solutions for large-scale electrical projects, contributing to operational efficiency and reliability. While their reliability and conductivity make them popular in industrial settings, it’s essential to consider factors like proper installation and maintenance to maximize their performance and longevity.
Residential Installations
Within residential installations, aluminum terminal lugs serve as crucial components in ensuring safe and efficient electrical connections. Their key characteristic of ease of installation and versatility makes them a preferred choice for residential electrical work. From household wiring to appliance connections, aluminum terminal lugs offer practical solutions for homeowners looking to enhance their electrical systems. Despite their advantages, it’s vital for homeowners to follow recommended installation guidelines and periodic maintenance checks to ensure the longevity and safety of aluminum terminal lugs within residential settings.
Composition and Properties
Material Composition
Aluminum terminal lugs are essential components in electrical systems, with their composition playing a crucial role in their performance and longevity. When examining material composition, two key aspects stand out: aluminum alloys and additives for strength.
Aluminum Alloys
Aluminum alloys are fundamental to the design and function of terminal lugs due to their unique properties. These alloys are crafted to optimize conductivity while maintaining durability and corrosion resistance. The key characteristic of aluminum alloys lies in their ability to strike a balance between strength and weight, making them a popular choice for various electrical applications. The versatility of aluminum alloys enables them to adapt to different operating conditions, ensuring the longevity and reliability of terminal lugs. However, one potential disadvantage of aluminum alloys is their susceptibility to certain types of corrosion, which can be mitigated through proper maintenance and protective measures.
Additives for Strength
Additives play a crucial role in enhancing the strength and resilience of aluminum terminal lugs. By incorporating specific additives into the composition, manufacturers can tailor the properties of the terminal lugs to meet specific requirements. The key characteristic of additives for strength is their ability to augment the mechanical properties of the lug, such as tensile strength and resistance to deformation. This enhancement improves the overall performance of the lug and extends its operational lifespan. While additives for strength bring significant benefits to aluminum terminal lugs, careful consideration must be given to the type and proportion of additives used to avoid compromising other essential properties.
Physical and Mechanical Properties
The physical and mechanical properties of aluminum terminal lugs are critical factors that determine their efficacy in electrical systems. Specifically, conductivity levels and strength-to-weight ratio play a pivotal role in the overall functionality of these components.
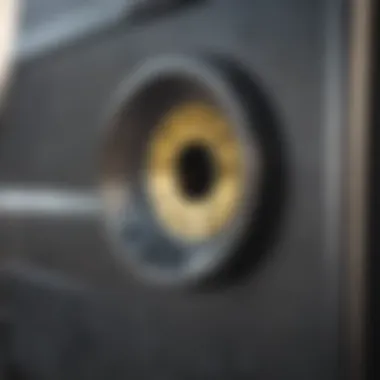
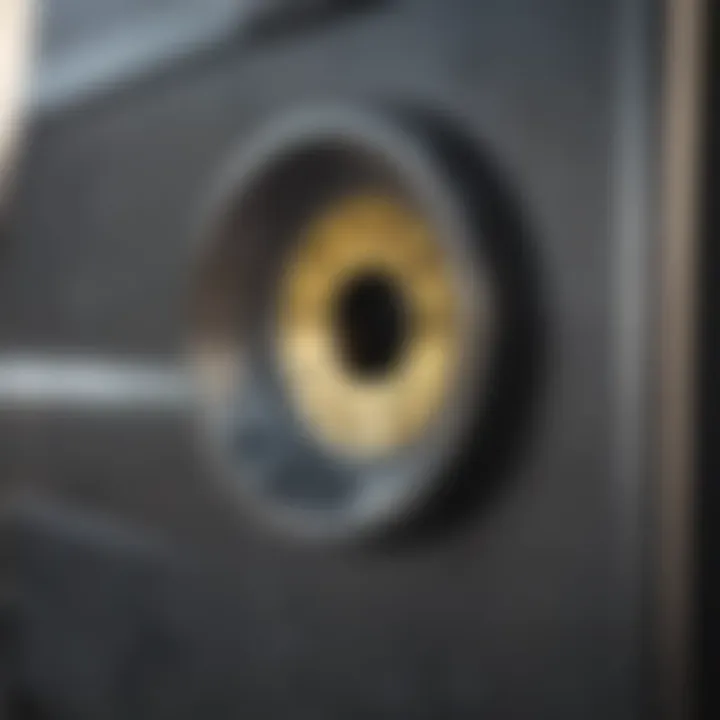
Conductivity Levels
Conductivity levels refer to the ability of the terminal lug to efficiently transmit electrical current without incurring significant losses. High conductivity is a desirable trait in terminal lugs, as it ensures minimal resistance during electrical flow. The key characteristic of conductivity levels lies in maximizing the flow of electricity while minimizing heat generation. This feature is particularly advantageous in high-demand applications where efficient energy transmission is paramount. However, excessive conductivity can also lead to overheating and potential safety hazards if not properly managed.
Strength-to-Weight Ratio
The strength-to-weight ratio of aluminum terminal lugs signifies the balance between structural integrity and lightweight construction. A favorable strength-to-weight ratio indicates that the lug can withstand substantial mechanical stress while remaining lightweight and easy to handle. This characteristic is vital in applications where weight constraints or portability are significant considerations. The unique feature of a high strength-to-weight ratio ensures that the terminal lug can endure mechanical loads without adding unnecessary bulk or complexity. However, achieving an optimal strength-to-weight ratio may involve trade-offs between material thickness, alloy selection, and manufacturing techniques to strike the ideal balance between strength and weight.
Installation Techniques
In the realm of aluminum terminal lugs, the efficient and proper installation techniques play a vital role in ensuring the effectiveness and longevity of electrical systems. This section delves into the significance of mastering the installation techniques, emphasizing specific elements that contribute to seamless connections within various applications. Understanding the nuances of installation techniques is crucial for preventing potential hazards and optimizing the performance of electrical setups.
Preparation Steps
Surface Cleaning:
Surface cleaning is a fundamental step in the preparation process for installing aluminum terminal lugs. By meticulously removing any contaminants or residues from the surface, such as dirt, grease, or oxidation, the efficacy of the electrical connection is greatly enhanced. The key characteristic of surface cleaning lies in its ability to promote optimal conductivity and reduce the risk of corrosion, ensuring long-term reliability. This meticulous cleaning process is a popular choice in this article due to its proven track record in maintaining electrical integrity. While surface cleaning offers substantial advantages in improving the overall performance of aluminum terminal lugs, it necessitates thoroughness and attention to detail to eliminate any potential drawbacks that may arise.
Wire Stripping:
Wire stripping is another essential aspect of preparation when working with aluminum terminal lugs. This process involves carefully removing the insulation from the wires to expose the conductor, facilitating a secure connection. The key characteristic of wire stripping is its role in maximizing contact between the conductor and the lug, thereby optimizing electrical conductivity. Wire stripping is a beneficial choice for this article as it ensures proper signal transmission and minimizes resistance within the system. The unique feature of wire stripping lies in its ability to tailor the wire length and stripping depth to specific requirements, offering precision and customization. While wire stripping presents clear advantages in enhancing connectivity, attention must be paid to potential disadvantages, such as fraying or damage to the wire during the process.
Connection Methods
Crimping:
Crimping is a versatile and reliable connection method widely used in the installation of aluminum terminal lugs. By mechanically securing the lug to the conductor using a crimping tool, a robust and durable joint is achieved, capable of withstanding varying environmental conditions. The key characteristic of crimping is its ability to create a gas-tight connection, ensuring efficient current flow and reducing the risk of thermal issues. Crimping stands out as a popular choice in this article due to its efficiency and cost-effectiveness in establishing secure electrical connections. The unique feature of crimping lies in its adaptability to different wire sizes and lug types, providing flexibility and consistency in installations. While crimping offers numerous advantages in ensuring reliable connections, it is essential to be mindful of potential drawbacks, such as improper crimping techniques leading to connectivity issues.
Soldering:
Soldering is a precise and intricate connection method that involves melting solder to fuse the conductor to the lug, creating a strong and stable joint. The key characteristic of soldering is its ability to form a permanent bond between the components, enhancing conductivity and mechanical strength. Soldering is a beneficial choice for this article as it provides a secure and low-resistance connection suitable for diverse electrical applications. The unique feature of soldering lies in its capability to join dissimilar materials effectively, offering versatility and adaptability in complex setups. While soldering presents notable advantages in ensuring robust connections, it requires skill and caution to avoid potential disadvantages such as joint weakening due to excessive heat or insufficient solder.
Maintenance and Troubleshooting
In the dynamic realm of electrical systems, the prowess and longevity of components like aluminum terminal lugs heavily rely on proper maintenance and effective troubleshooting protocols. This section serves as a pivotal guide towards ensuring the uninterrupted functionality of these crucial elements. Emphasizing a strategic approach to maintenance and troubleshooting can avert potential malfunctions, safeguarding both the system and its users.
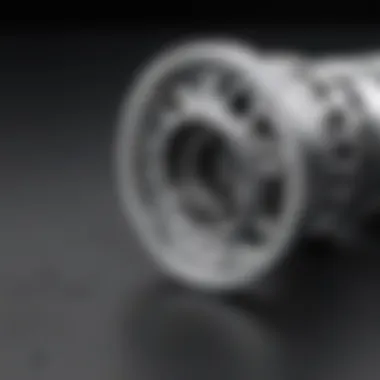
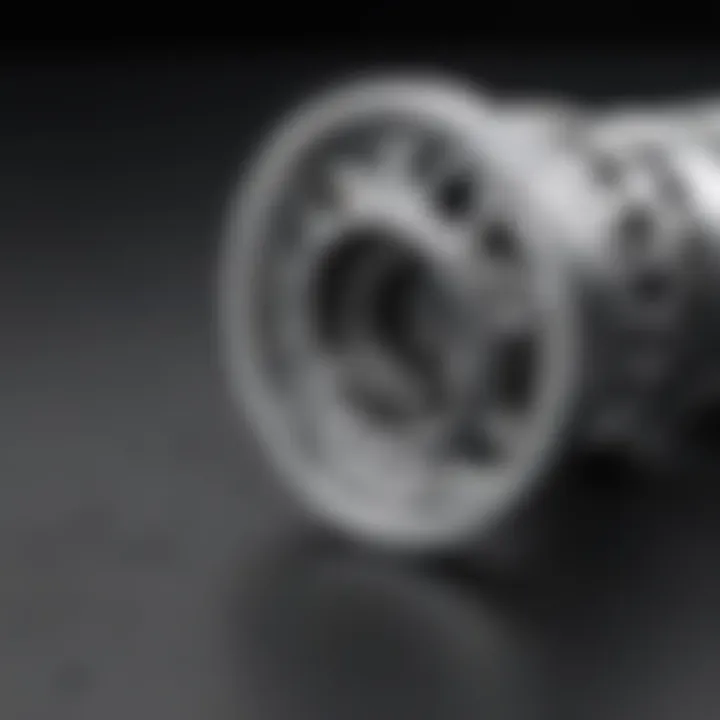
Inspection Guidelines
Visual Checks
Visual checks play a fundamental role in the comprehensive maintenance of aluminum terminal lugs. By visually inspecting key components, such as surface conditions and connection points, anomalies or issues can be swiftly identified before escalating into larger concerns. This proactive approach enhances the overall reliability of the electrical system, promoting a safer operational environment. The simplicity and efficiency of visual checks make them a popular choice for ensuring the immediate condition assessment of aluminum terminal lugs within the context of this article.
Testing Procedures
Testing procedures offer a more in-depth assessment of the functionality and integrity of aluminum terminal lugs. By utilizing specialized equipment and testing methodologies, the performance of these components can be rigorously evaluated. This detailed scrutiny not only validates the quality of installations but also pinpoints any underlying issues that standard visual checks may overlook. While testing procedures require more time and resources compared to visual checks, their analytical depth and accuracy provide invaluable insights, making them an essential component of the maintenance and troubleshooting process within the scope of this article.
Common Issues and Solutions
Corrosion
Corrosion stands out as a primary challenge in the realm of aluminum terminal lugs, posing threats to conductivity and structural integrity. Understanding the corrosive processes involved and implementing proactive measures are pivotal in mitigating its impact. By highlighting the key characteristics and risk factors associated with corrosion, this section aims to equip readers with a proactive stance towards combating this pervasive issue. While corrosion presents a formidable challenge, timely interventions and preventative strategies can significantly prolong the lifespan and efficiency of aluminum terminal lugs, underscoring its relevance within the narrative of this article.
Loose Connections
Loose connections emerge as a common source of electrical malfunctions, jeopardizing the operational reliability of systems. Identifying the root causes and consequences of loose connections is imperative for maintaining electrical safety standards. The distinct characteristics of loose connections, such as intermittent faults and thermal stress, necessitate specialized solutions tailored to address these challenges effectively. By offering a nuanced exploration of the causes and implications of loose connections, this section aims to empower readers with the knowledge and strategies required to resolve such issues efficiently within the context of this article.
Future Trends and Innovations
In the world of aluminum terminal lugs, staying ahead of trends and embracing innovation is paramount for enhancing functionalities and ensuring sustainability. Future trends and innovations in the field of aluminum terminal lugs hold significant importance in shaping the direction of electrical systems and applications. By focusing on developments in materials and manufacturing processes, these advancements pave the way for more efficient and durable terminal lug solutions.
Advancements in Aluminum Technology
Nanostructuring
Nanostructuring in aluminum technology represents a groundbreaking approach to enhancing the performance and longevity of terminal lugs. This method involves manipulating the nanoscale structure of aluminum to improve its mechanical and conductive properties significantly. The key characteristic of nanostructured aluminum lies in its increased surface area-to-volume ratio, resulting in enhanced conductivity and strength. Nanostructuring offers a unique feature of improved corrosion resistance and fatigue durability in aluminum terminal lugs, making it a preferred choice for applications requiring high reliability and performance.
Smart Alloys
Within the realm of aluminum terminal lugs, the emergence of smart alloys revolutionizes the landscape of electrical connectivity. Smart alloys are designed to adapt their properties in response to changing conditions, offering tailored conductivity and durability based on the electrical environment. The key characteristic of smart alloys is their self-regulating behavior, optimizing performance under varying loads and temperatures. These alloys provide a unique feature of self-healing capabilities, ensuring reliability in challenging operating conditions. While smart alloys offer exceptional benefits in enhancing the efficiency and resilience of aluminum terminal lugs, potential disadvantages may include higher manufacturing costs and specialized processing requirements.
Environmental Impact and Sustainability
Recycling Initiatives
Recognizing the importance of sustainability, recycling initiatives play a crucial role in the aluminum terminal lug industry. These initiatives focus on reclaiming and reusing aluminum materials through efficient recycling processes, reducing the demand for virgin resources and minimizing waste. The key characteristic of recycling initiatives lies in their ability to promote a circular economy by closing the loop on material usage. This sustainable practice not only conserves natural resources but also reduces energy consumption and greenhouse gas emissions, aligning with global environmental goals. However, challenges such as sorting complexities and contaminant removal can present disadvantages in certain recycling initiatives.
Green Manufacturing Practices
Green manufacturing practices encompass environmentally conscious strategies applied in the production of aluminum terminal lugs. These practices prioritize eco-friendly processes, materials, and energy sources to minimize environmental impact throughout the manufacturing lifecycle. The key characteristic of green manufacturing practices is their focus on resource efficiency and pollution prevention, fostering sustainability in the industry. These practices offer a unique feature of reducing carbon footprint and waste generation, contributing to a greener and healthier environment. While the advantages of green manufacturing practices are clear in promoting sustainability and corporate social responsibility, potential disadvantages may include initial investment costs and operational adjustments required for implementing these practices.