Unlocking Connectivity: A Comprehensive Guide to Submersible Wire Splice Kits
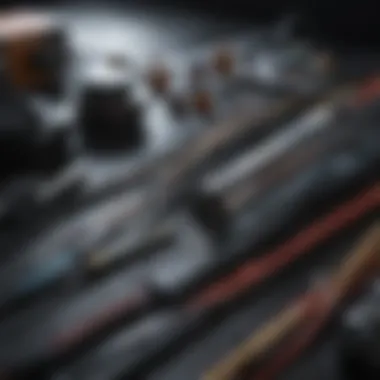
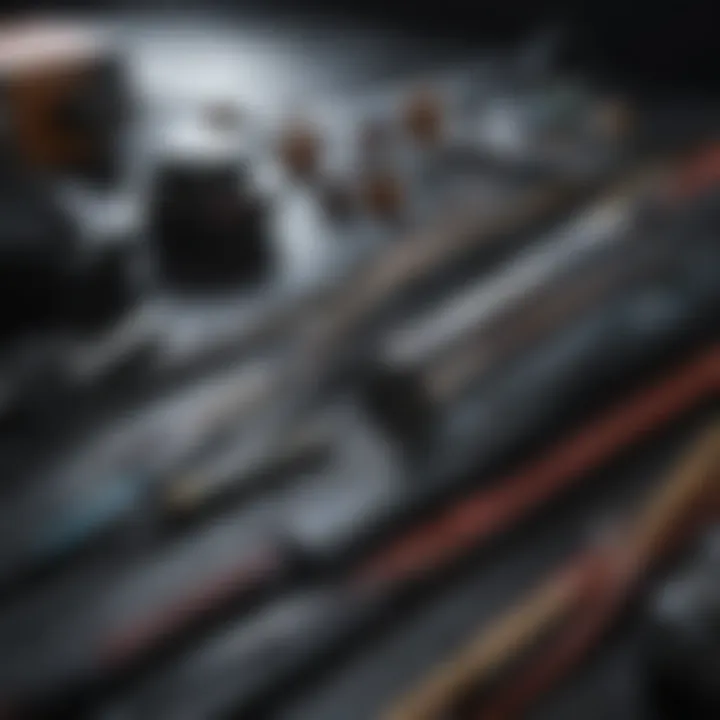
Overview of Topic
Submersible wire splice kits play a crucial role in the home improvement industry, particularly in scenarios where electrical connections need to withstand challenging environments such as underwater installations or harsh outdoor conditions. These kits ensure seamless connectivity and durability for electrical systems, making them indispensable tools for homeowners seeking reliable electrical solutions.
Common Challenges and Solutions
Homeowners often face issues with traditional wire connections becoming damaged or malfunctioning due to exposure to water or extreme weather conditions. Submersible wire splice kits offer a practical solution by providing watertight seals and robust insulation, protecting connections from moisture and environmental factors. Utilizing these kits helps homeowners overcome the challenges of maintaining secure and long-lasting electrical connections in adverse settings.
Product Recommendations
When considering submersible wire splice kits for home improvement projects, leading industry brands like [Industry Brand] offer a range of high-quality products tailored for different applications. These kits come with features such as durable waterproof casing, corrosion-resistant materials, and ease of installation, ensuring reliable performance in demanding environments. Homeowners can benefit from the superior quality and longevity provided by these recommended products.
Step-by-Step Guides
To effectively implement submersible wire splice kits in home improvement projects, follow these step-by-step instructions:
- Assess the Application: Determine the specific requirements and environmental conditions where the wire splice kits will be deployed.
- Select the Right Kit: Choose a submersible wire splice kit that matches the voltage rating and wire size of the electrical connections.
- Prepare the Cables: Strip the insulation from the cable ends and clean the wires to ensure proper contact and secure connections.
- Install the Kit: Follow the manufacturer's instructions to assemble the splice kit components and seal the connections securely.
- Test and Verify: Conduct thorough testing to ensure the connections are waterproof and functioning correctly.
By following these detailed steps, homeowners can effectively enhance their electrical systems using submersible wire splice kits, guaranteeing reliable performance and longevity
Introduction
Submersible wire splice kits are a critical component in ensuring seamless connectivity and durability in challenging environments, from underwater installations to electrical repairs. This comprehensive guide aims to delve into the intricate world of these kits, exploring their functionality, application, and significance across various industries. By analyzing the components, installation methods, and best practices associated with submersible wire splice kits, readers will gain a thorough understanding of how these kits can be effectively utilized to meet diverse needs.
Understanding Submersible Wire Splice Kits
Definition and Purpose
The definition and purpose of submersible wire splice kits play a fundamental role in the overall connectivity and reliability of electrical systems. These kits are specifically designed to provide waterproof and insulated connections, safeguarding them from moisture and other environmental factors. Their key characteristic lies in their ability to maintain connectivity in harsh conditions, making them a popular choice for applications requiring water resistance. The unique feature of these kits is their capability to protect electrical connections from corrosion and degradation, ensuring long-term performance. While they offer excellent waterproofing properties, their main disadvantage often lies in the complexity of installation in comparison to traditional splicing methods.
Key Components Overview
The key components of submersible wire splice kits encompass protective enclosures, insulating materials, connectors, and terminals. Protective enclosures come in various types and materials, each offering different levels of protection against water ingress. Insulating materials such as heat shrink tubing and waterproof sealants serve to insulate and seal the spliced connections, preventing water damage. Connectors and terminals such as soldering connectors and crimp terminals ensure secure and reliable connections. Each component plays a vital role in enhancing the durability and effectiveness of submersible wire splice kits, making them essential for dependable electrical installations.
Importance of Waterproof Splicing
Challenges Faced Without Proper Splicing
Without proper waterproof splicing, electrical connections are susceptible to corrosion, short circuits, and failure in moist or wet conditions. The key challenge lies in maintaining connection integrity and performance in environments where exposure to water is inevitable. This underscores the importance of utilizing waterproof splicing methods to mitigate these risks effectively. Failure to do so can result in system malfunctions, safety hazards, and costly repairs.
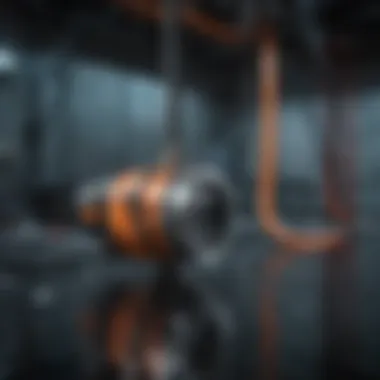
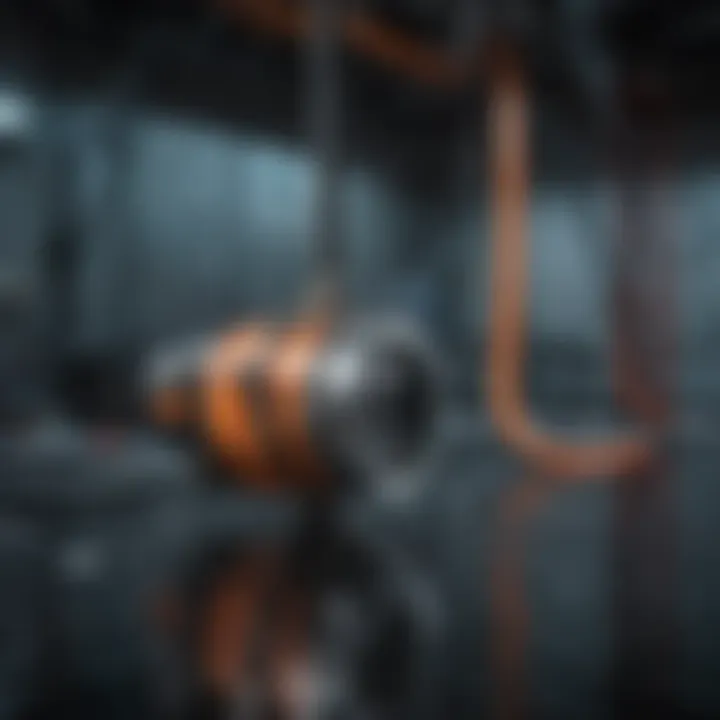
Benefits of Waterproof Splicing
Waterproof splicing offers a range of benefits, including enhanced reliability, durability, and safety of electrical connections. By creating a moisture-resistant barrier around spliced wires, waterproof splicing ensures long-term functionality and performance, even in challenging environments. Its unique feature lies in its ability to protect against moisture intrusion, thereby prolonging the lifespan of electrical systems. While the advantages are significant, it is essential to adhere to proper waterproof splicing techniques to maximize these benefits.
Scope of Application
Marine Industry
In the marine industry, submersible wire splice kits are indispensable for maintaining electrical connections on boats, ships, and offshore structures. They are specially designed to withstand constant exposure to water, salt, and marine conditions. Their key characteristic lies in their ability to prevent corrosion and ensure reliable electrical connections in marine environments. The unique feature of these kits is their resistance to saltwater intrusion, making them a preferred choice for marine applications. However, thorough installation and regular maintenance are crucial to offset the challenges posed by harsh marine conditions.
Outdoor Lighting Systems
For outdoor lighting systems, submersible wire splice kits provide vital protection against the elements, ensuring consistent illumination in garden lights, landscape lighting, and outdoor fixtures. They offer a key advantage in safeguarding electrical connections from moisture, UV exposure, and temperature fluctuations, enhancing the longevity of outdoor lighting setups. The unique feature of these kits is their weatherproof sealing, which prevents water ingress and maintains connectivity in various outdoor environments. Utilizing submersible wire splice kits is essential for optimizing the performance and safety of outdoor lighting systems.
Underground Electrical Connections
In underground electrical installations, submersible wire splice kits are essential for preserving the integrity of buried cables, conduits, or junction boxes. Their key characteristic lies in providing waterproof protection against soil moisture and groundwater infiltration, ensuring continuous electrical connectivity underground. The unique feature of these kits is their ability to withstand environmental pressures and prevent water damage, making them a reliable solution for underground electrical connections. Proper installation and regular inspections are crucial to prevent potential issues and maintain the efficiency of underground electrical networks.
Components of Submersible Wire Splice Kits
In the realm of electrical connectivity, the components of submersible wire splice kits reign supreme as the unsung heroes, ensuring seamless integration even in the most challenging environments. These kits play a pivotal role in maintaining the integrity of electrical connections, especially in marine environments, outdoor lighting systems, and underground electrical connections. By delving into the various elements that comprise these kits, we gain a profound understanding of their significance in ensuring uninterrupted functionality and longevity.
Protective Enclosures
Types of Enclosures
One of the cornerstone elements of submersible wire splice kits is the protective enclosures. These enclosures serve as shields against moisture, corrosion, and external elements that could compromise the electrical connections. There are various types of enclosures available, ranging from plastic to metal variants, each with its unique set of characteristics and benefits. Plastic enclosures, for instance, offer lightweight and corrosion-resistant properties, making them ideal for applications where weight and environmental factors are crucial considerations. On the other hand, metal enclosures provide robust physical protection and enhanced durability, ensuring the longevity of the spliced wires in demanding conditions.
Material Considerations
When it comes to choosing the right material for protective enclosures, factors such as strength, conductivity, and resistance to environmental factors come into play. The material of the enclosure directly impacts its performance and suitability for specific applications. For instance, high-quality plastics offer excellent insulation properties and can withstand a wide range of temperatures, making them versatile and reliable in varied settings. Conversely, metals provide superior mechanical protection and electromagnetic shielding, ideal for environments where robustness is paramount. By carefully considering the material of the enclosures, users can tailor their splice kits to meet the demands of their particular use cases effectively.
Insulating Materials
Heat Shrink Tubing
In the realm of insulating materials, heat shrink tubing stands out as a versatile and effective solution for protecting spliced wires. This specialized tubing contracts when heat is applied, forming a tight seal around the connection point to prevent moisture ingress and ensure electrical insulation. The key characteristic of heat shrink tubing lies in its ability to conform to irregular shapes and sizes, providing a snug fit that enhances the longevity and performance of the spliced wires. Its heat-activated feature simplifies the insulating process, offering a convenient and secure solution for a wide range of applications.
Waterproof Sealants
Waterproof sealants play a crucial role in enhancing the resilience of submersible wire splice kits against water intrusion and environmental contaminants. These sealants create a protective barrier around the splice joint, effectively sealing out moisture and preventing corrosion or short circuits. The primary advantage of waterproof sealants is their ability to maintain the integrity of the electrical connection even in submerged or moist conditions, ensuring reliable performance over an extended period. While waterproof sealants offer robust protection, users need to consider the compatibility of the sealant with the materials used in the splice kit to ensure optimal performance and durability.
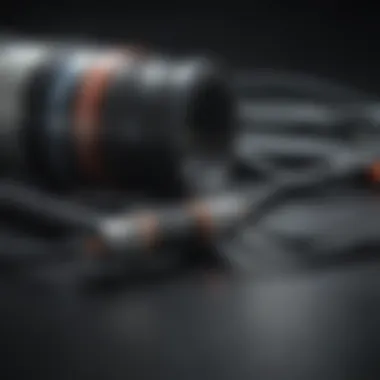

Connectors and Terminals
Soldering Connectors
When it comes to establishing secure and reliable electrical connections, soldering connectors play a key role in forming strong bonds between wires. These connectors utilize solder to create a permanent joint that enhances conductivity and prevents accidental disconnection. The key characteristic of soldering connectors lies in their ability to withstand high temperatures and voltage levels, making them ideal for applications where stability and durability are paramount. Additionally, soldering connectors provide mechanical strength to the splice point, reducing the risk of wire fatigue or breakage over time.
Crimp Terminals
On the other hand, crimp terminals offer a versatile and user-friendly solution for joining wires securely without the need for soldering. These terminals utilize a crimping tool to compress the terminal onto the wire, creating a tight and reliable connection. The key advantage of crimp terminals lies in their ease of installation and adaptability to various wire gauges, making them suitable for a broad range of applications. While crimp terminals provide quick and efficient wire connectivity, proper crimping techniques and tools are essential to ensure a strong and enduring joint that can withstand environmental stressors and vibrations.
Installation Procedures
In the expansive realm of submersible wire splice kits, emphasizing the Installation Procedures stands as a crucial component in ensuring the efficient and effective use of these essential tools. Installation Procedures play a pivotal role in guaranteeing the longevity and reliability of electrical connections in challenging environments. By meticulously following the correct installation steps, individuals can significantly reduce the risk of malfunctions, water infiltration, and corrosion, thus securing a seamless and durable connection. This section aims to delve deep into the intricacies of Installation Procedures, shedding light on the specific elements, benefits, and considerations critical for successful utilization.
Preparation Steps
Surface Cleaning
Surface Cleaning holds paramount importance within the context of Installation Procedures, serving as the foundational step that sets the stage for a successful splice. The meticulous removal of debris, contaminants, and moisture from the surfaces to be spliced ensures optimal adhesion and conductivity, ultimately enhancing the overall performance and durability of the connection. Moreover, the thorough cleaning process contributes to the prevention of oxidation and corrosion, extending the lifespan of the splice. Despite the seemingly simple nature of Surface Cleaning, its significance cannot be overstated, making it a popular choice for experts seeking to achieve flawless connections in submersible environments. The unique feature of Surface Cleaning lies in its ability to remove microscopic impurities, which, although invisible to the naked eye, can severely impair the efficacy of the splice. This comprehensive cleaning method, when executed meticulously, leads to enhanced connectivity, reduced resistance, and superior electrical performance in the context of submersible wire splicing.
Component Inspection
Component Inspection plays a fundamental role in the overarching goal of successful splice installations as it ensures the integrity and quality of the components involved. By scrutinizing each element for defects, damage, or discrepancies, individuals can preemptively identify issues that might compromise the functionality and reliability of the splice. Through rigorous inspection, one can guarantee that only top-notch components are used, thereby elevating the overall quality and performance of the splice. This proactive approach not only enhances the safety and efficiency of the connection but also minimizes the likelihood of costly repairs or replacements down the line. The unique feature of Component Inspection lies in its ability to pinpoint potential weak points or faulty components before they escalate into larger problems, thus saving time, resources, and ensuring a seamless splicing process.
Splicing Techniques
Heat Shrinking Method
The Heat Shrinking Method epitomizes a cutting-edge technique employed in the installation of submersible wire splices, offering a reliable and durable bonding mechanism. As heat is applied to the heat shrink tubing enclosing the splice, it contracts, forming a snug and watertight seal around the connection, effectively insulating and protecting it from external elements such as water, moisture, and corrosion. This method is renowned for its simplicity, efficiency, and efficacy in creating robust electrical joints that can withstand harsh environmental conditions. The unique feature of the Heat Shrinking Method lies in its ability to provide a seamless, airtight seal that not only insulates the connection but also ensures longevity and reliability, making it an indispensable technique in submersible wire splicing. Amidst its benefits, one of the standout advantages of the Heat Shrinking Method is its adaptability to various wire sizes and configurations, accommodating diverse splicing requirements with precision and ease.
Crimping Method
Contrasting the Heat Shrinking Method, the Crimping Method showcases an alternative yet equally effective technique for creating secure and strong connections in submersible environments. By employing specialized crimp terminals and tools, individuals can compress the conductor and terminal together, forging a reliable and resilient bond devoid of solder or heat. This cold-welding process not only simplifies the splicing procedure but also eliminates the need for a heat source, making it a safer option for individuals working in potentially hazardous conditions. The unique feature of the Crimping Method lies in its capacity to produce durable connections that maintain their integrity even under external stresses and environmental challenges, thus ensuring a solid and enduring splice. Additionally, this method offers quick and convenient execution, ideal for situations where time is of the essence or where access to heat sources may be limited.
Sealing and Protection
Sealing and Protection represent the final but critical stage in the process of submersible wire splicing, serving as the ultimate safeguard against environmental factors and potential damage. Through the implementation of robust sealing techniques and protective measures, individuals can fortify the splice against moisture ingress, mechanical stress, and corrosion, thereby extending its operational lifespan and reliability. Waterproofing Strategies, such as specialized sealants and encapsulation materials, offer a watertight barrier that shields the connection from water-related degradation and ensures sustained functionality in wet or submerged conditions. The unique feature of Waterproofing Strategies resides in their ability to form a resilient seal that not only keeps water at bay but also maintains electrical integrity and connectivity over time, making them a go-to choice for submersible applications.
Mechanical Protection, on the other hand, focuses on safeguarding the splice against physical harm, abrasion, and impact that could compromise its functionality. By incorporating robust protective casings, cable management systems, or sheathing materials, individuals can shield the splice from external factors, thereby prolonging its lifespan and durability. The key characteristic of Mechanical Protection lies in its ability to reinforce the connection, enhancing its resistance to wear and tear, environmental pressures, and external disturbances. While offering enhanced physical resilience, Mechanical Protection also contributes to the overall structural stability of the splice, making it a valuable addition to any submersible wire splicing project.
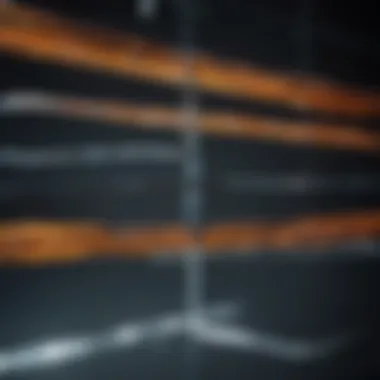
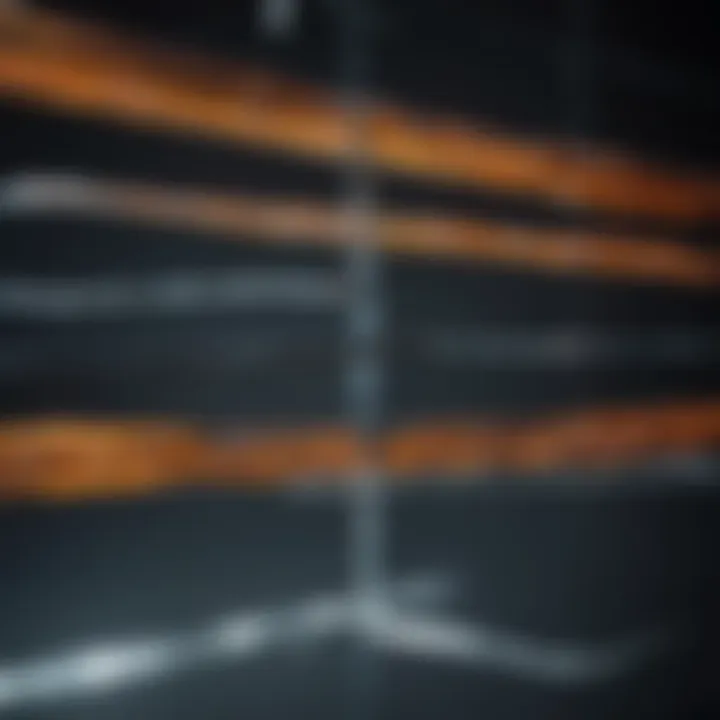
Best Practices and Maintenance
In this comprehensive guide on submersible wire splice kits, the section on 'Best Practices and Maintenance' is of paramount importance to ensure the longevity and reliability of electrical connections. Emphasizing meticulous adherence to industry best practices and regular maintenance schedules is crucial in sustaining the efficiency and safety of submersible wire splice installations.
Quality Assurance
Testing Procedures
Testing procedures are a cornerstone of quality assurance in submersible wire splice kits. These procedures involve rigorous testing protocols to validate the integrity and functionality of the spliced connections. By subjecting the splices to a series of tests under varying conditions, manufacturers and installers can ascertain the robustness and waterproofing capabilities of the splices. This proactive approach not only ensures compliance with industry standards but also instills confidence in the durability and reliability of the connections. However, while testing procedures are essential for identifying potential weaknesses in the splicing process, they can prolong installation timelines and add to the overall project costs.
Durability Standards
Durability standards play a vital role in setting benchmarks for the expected quality and longevity of submersible wire splice connections. By adhering to stringent durability standards, manufacturers can produce splice kits that withstand harsh environmental conditions and maintain peak performance over extended periods. The incorporation of durable materials and designs in accordance with predefined standards ensures that the splices deliver consistent results under varying loads and operational scenarios. While adhering to durability standards enhances the reliability of the connections, it may also entail higher material costs and more complex installation procedures.
Regular Inspections
Visual Checks
Visual checks form an integral part of routine maintenance and inspection protocols for submersible wire splice installations. Conducting visual checks allows operators and maintenance personnel to visually assess the condition of the splices, looking for signs of wear, corrosion, or damage. By identifying and addressing issues at an early stage, visual checks play a crucial role in preventing potential failures and ensuring uninterrupted operation. Moreover, visual inspections provide valuable insights into the overall health of the electrical system, enabling stakeholders to make informed decisions regarding necessary repairs or replacements.
Functionality Testing
Functionality testing is a critical aspect of maintenance procedures for submersible wire splice kits. By subjecting the spliced connections to functional tests, operators can verify that the electrical circuits remain intact and operational under normal operating conditions. This proactive approach not only validates the efficacy of the splices but also helps in detecting any underlying performance issues that may compromise system functionality. However, despite its effectiveness in ensuring system reliability, functionality testing can be time-consuming and may require specialized equipment or expertise.
Troubleshooting Guidelines
Common Issues
Identifying common issues associated with submersible wire splice installations is essential for implementing effective troubleshooting strategies. Issues such as water ingress, insulation failure, or poor connection integrity can impact the performance and safety of the electrical system. By recognizing these common issues early on, maintenance personnel can address root causes and implement corrective measures to restore optimal functionality. However, resolving common issues may necessitate specialized knowledge or training, increasing the complexity of maintenance activities.
Resolution Techniques
Resolution techniques encompass a range of strategies employed to address issues encountered during the troubleshooting process. From resealing splices to replacing faulty components, resolution techniques aim to rectify identified issues and restore the intended functionality of the electrical system. By leveraging proven resolution techniques, maintenance teams can expedite the troubleshooting process and minimize downtime associated with system malfunctions. While effective in achieving quick resolutions, these techniques may involve additional costs or parts replacement, impacting the overall maintenance budget.
Conclusion
In the realm of submersible wire splice kits, the conclusion serves as a pivotal element in ensuring seamless connectivity and durability. As we wrap up this comprehensive guide to innovative solutions for submersible wire splice kits, it becomes evidently clear that the significance of proper splicing techniques cannot be overstated. By harnessing the power of these kits, individuals can navigate challenging environments and facilitate uninterrupted electrical connectivity. The overarching goal of the conclusion is to emphasize the transformative impact that submersible wire splice kits can have on various industries and applications, ranging from marine installations to outdoor lighting systems and underground electrical connections. Through meticulous attention to detail and adherence to best practices, users can enhance the reliability and longevity of their electrical systems, safeguarding against potential downtime and inefficiencies.
Harnessing the Power of Submersible Wire Splice Kits
Ensuring Longevity
When delving into the aspect of ensuring longevity with submersible wire splice kits, what truly stands out is the robustness and resilience they offer in demanding conditions. The key characteristic of longevity within these kits lies in their ability to withstand harsh environmental factors such as moisture, corrosion, and temperature variations. This longevity is a beneficial choice for this article as it underscores the durability and longevity that users can expect when implementing these splice kits. One unique feature of ensuring longevity is the utilization of high-quality insulating materials and connectors, which contribute to the overall longevity of the spliced connections. While longevity ensures prolonged service life and minimal maintenance requirements, it's essential to note that improper installation techniques or using subpar components can compromise this aspect.
Enhancing Reliability
Within the context of enhancing reliability, submersible wire splice kits excel at providing consistent and secure electrical connections. The key characteristic that sets these kits apart is their ability to minimize the risk of electrical failures and signal disruptions, thus enhancing the overall reliability of the electrical system. This enhanced reliability is a popular choice for this article due to its critical role in ensuring uninterrupted power transmission in critical applications. A unique feature of enhancing reliability is the comprehensive sealing and protection measures incorporated during the splicing process, safeguarding against moisture ingress and mechanical stresses. While enhancing reliability guarantees stable and reliable electrical connections, adherence to proper installation procedures and regular maintenance inspections are imperative to sustain this level of reliability over time.