Mastering Buffing Discs for Drills: A Comprehensive Guide
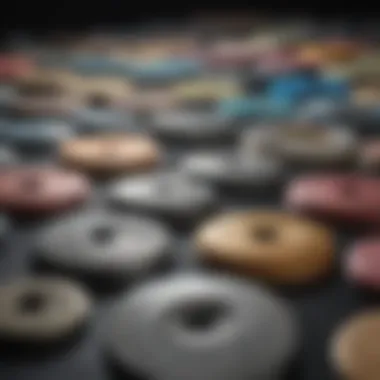
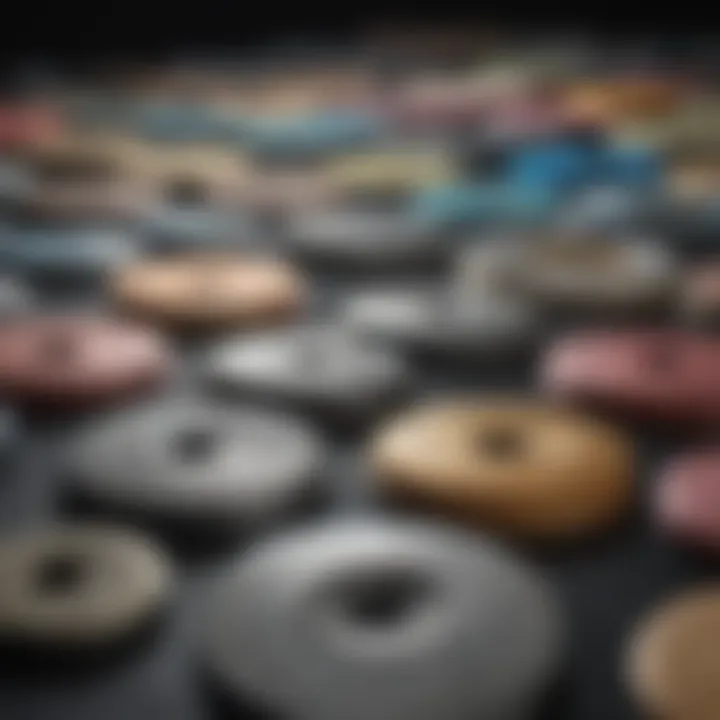
Overview of Topic
In the home improvement industry, buffing discs for drills play a pivotal role in achieving a flawless finish on various surfaces. These discs are essential for tasks like polishing, buffing, and restoring the shine of different materials. Their versatility and effectiveness make them a must-have tool for homeowners looking to elevate the appearance of their spaces.
Understanding the importance of buffing discs is crucial for homeowners who want to maintain their belongings in top condition. Whether it's reviving an old piece of furniture or giving a new shine to metal fixtures, buffing discs offer a cost-effective and convenient solution to enhance the aesthetic appeal of home decor.
Common Challenges and Solutions
Homeowners often face challenges when using buffing discs for drills, such as uneven finishes, swirl marks, or material damage. These issues can detract from the desired outcome and lead to frustration. To overcome these obstacles, it is essential to follow proper techniques and use the right products.
One common challenge is achieving a uniform shine without streaks or imperfections. By adjusting the speed and pressure while buffing, homeowners can maintain a consistent finish. Additionally, selecting the correct buffing pad and compound for the specific material being polished can significantly improve results and prevent damage.
Product Recommendations
When it comes to buffing discs, [Industry Brand] offers a range of high-quality products that cater to different needs and preferences. For heavy-duty tasks, the [Product A] disc provides exceptional cutting power and durability, making it ideal for removing deep scratches and restoring surfaces to their original condition.
For more delicate polishing jobs, the [Product B] disc is perfect for achieving a mirror-like shine without leaving swirl marks. Its advanced composition ensures a smooth finish and can be used on a variety of surfaces, including metals, wood, and plastics.
Step-by-Step Guides
To effectively utilize buffing discs for drills, homeowners should follow a systematic approach to ensure optimal results. Begin by thoroughly cleaning the surface to be polished and removing any dirt or debris that could cause scratches. Next, apply a small amount of buffing compound onto the disc to lubricate the surface and enhance the polishing process.
When buffing, remember to work in small sections to maintain control and avoid overbuffing. Move the drill in smooth, overlapping motions to evenly distribute the compound and achieve a consistent shine. Once the desired finish is achieved, wipe off any excess compound and admire the refreshed appearance of the surface.
By following these step-by-step instructions and incorporating the recommended products, homeowners can unlock the full potential of buffing discs for drills and transform their living spaces with professional-quality results.
Introduction
In the realm of DIY projects and home maintenance, the significance of buffing discs for drills cannot be overstated. This introductory section sets the stage for a comprehensive exploration of this crucial tool in the toolkit of any housewife or homeowner looking to achieve professional-level results in their various projects.
Buffing discs play a vital role in achieving a smooth, polished finish on a wide range of surfaces, from wood to metal, making them indispensable for tasks such as refinishing furniture, polishing automotive paint, or restoring the shine to household fixtures. Understanding how to wield these discs effectively can elevate the quality of one's work and deliver results that not only look impressive but also stand the test of time.
Throughout this guide, we will delve into the nitty-gritty details of buffing discs for drills, covering everything from the fundamental concepts behind their operation to the nuanced techniques required for optimal performance. By the time you reach the end of this article, you will be equipped with a comprehensive understanding of buffing discs, enabling you to tackle your next project with confidence and finesse.
Understanding Buffing Discs
In this article, a key section is understanding buffing discs for drills. This is crucial as it lays the foundation for effective usage and optimization of outcomes. Understanding buffing discs encompasses grasping the different types available, knowing their specific uses, and comprehending the importance of selecting the right disc for various projects. By delving into this topic, readers can enhance their knowledge and make informed decisions when utilizing buffing discs.
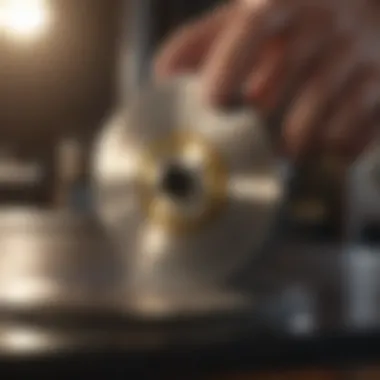
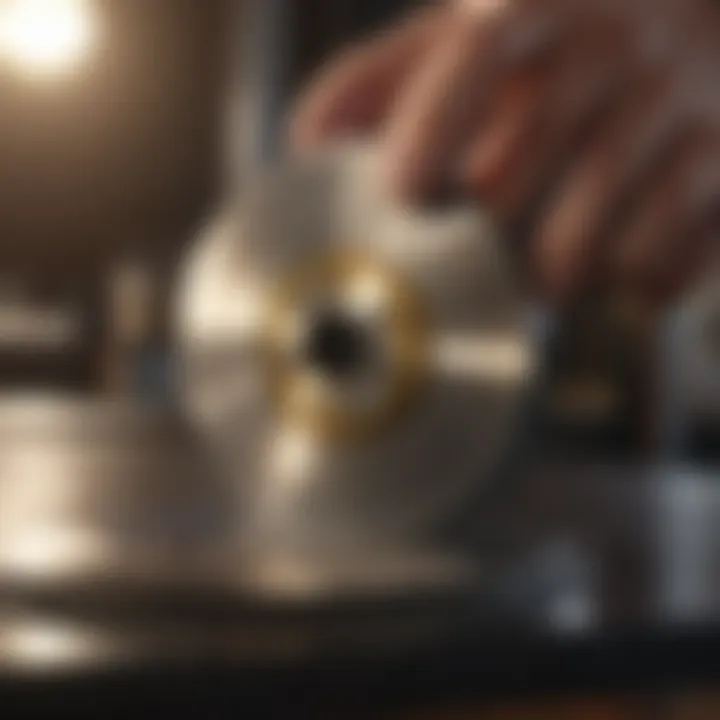
What are Buffing Discs?
Buffing discs are essential tools used in conjunction with drills to smoothen, polish, or grind surfaces. They come in various materials, sizes, and grit levels to suit different applications. The primary function of buffing discs is to enhance the appearance and texture of materials through abrasion and polishing. By utilizing different buffing discs, users can achieve varying levels of smoothness and shine on surfaces.
Types of Buffing Discs
Fiber Discs
Fiber discs are known for their durability and versatility in abrasive applications. Their key characteristic lies in the use of reinforced fibers bonded with abrasive materials, allowing for efficient material removal and surface refinement. These discs are particularly useful for heavy-duty tasks and are favored for their long-lasting performance. While they may be more abrasive compared to other discs, their ability to tackle challenging surfaces makes them a popular choice for tasks requiring intense polishing or grinding.
Sanding Discs
Sanding discs are designed for smoothing rough surfaces, removing paint, and preparing materials for finishing. Their key feature is the abrasive sandpaper used on the disc's surface, which is effective in removing imperfections and creating a smooth finish. Sanding discs are available in various grit levels, allowing users to achieve different levels of smoothness based on the project requirements. While sanding discs excel in surface preparation, they may be less suitable for polishing tasks that require a finer finish.
Velcro Discs
Velcro discs, also known as hook and loop discs, offer convenience and versatility in attachment and removal from sanders or drills. Their key characteristic is the Velcro backing on the disc, which ensures quick and easy changes between discs during projects. Velcro discs are popular for their ease of use and efficiency in switching between different grits or types of discs without the need for additional tools. However, the reliance on Velcro for attachment may be a limitation in high-intensity applications where a more secure fastening method is required.
Polishing Discs
Polishing discs are specifically designed for achieving a high-gloss finish on surfaces through the use of polishing compounds or fine abrasives. Their key feature lies in the softness and smoothness of the disc surface, which helps in buffing out scratches and imperfections to create a mirror-like shine. Polishing discs are essential for adding a final touch of brilliance to materials such as metal, wood, or even automotive surfaces. While they excel in providing a polished look, polishing discs may require different techniques and compounds for optimal results compared to other types of buffing discs.
Choosing the Right Buffing Disc
The section on Choosing the Right Buffing Disc holds pivotal importance in this comprehensive guide to Buffing Discs for Drill as it is the cornerstone of achieving optimal results in any buffing task. Selecting the appropriate buffing disc is essential for ensuring efficiency, quality outcomes, and safety. When considering the various factors involved in choosing the right buffing disc, several key elements come into play:
Factors to Consider
Material
Material is a crucial aspect to contemplate when selecting a buffing disc for your drill. Different materials offer distinct characteristics that impact the performance and durability of the disc. For instance, abrasive materials like aluminum oxide or silicon carbide are popular choices due to their effectiveness in removing imperfections and achieving smooth finishes. These materials can withstand high temperatures and heavy use, making them suitable for various applications.
Grit
Grit refers to the coarseness or fineness of the abrasive particles on the buffing disc. The grit rating determines the level of abrasiveness and the type of surface finish it can achieve. Finer grits are ideal for polishing and finishing tasks, while coarser grits are more effective for removing layers of material or smoothing rough surfaces. Understanding the appropriate grit for each project is essential to achieve the desired results efficiently.
Size
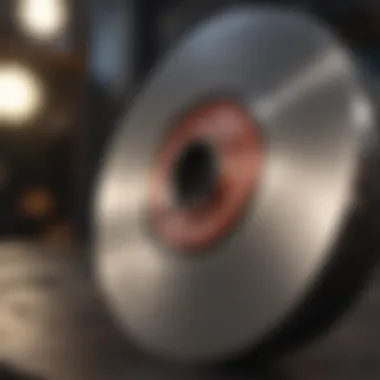
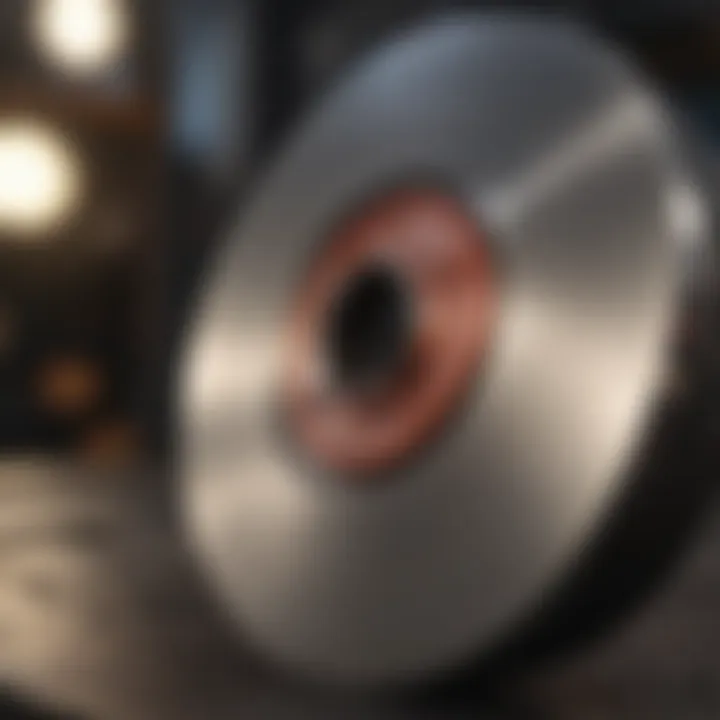
The size of the buffing disc plays a significant role in its versatility and usability. Larger discs cover more surface area, making them suitable for extensive projects that require rapid material removal or polishing. On the other hand, smaller discs offer greater precision and maneuverability, facilitating intricate detailing and reaching tight spaces. Selecting the right size depending on the task at hand is crucial for optimizing productivity and achieving consistent results.
Compatibility
Compatibility between the buffing disc and the drill is essential to ensure seamless operation and safety. It is imperative to match the disc's design, mounting style, and specifications with the drill's capabilities to prevent accidents, damage, or inefficiencies. Understanding the compatibility requirements can streamline the buffing process, enhance user experience, and prolong the lifespan of both the disc and the drill.
Using Buffing Discs Effectively
Using buffing discs effectively is a crucial aspect of achieving optimal results when utilizing them with a drill. This section delves into specific elements, benefits, and considerations related to using buffing discs effectively.
Preparation and Safety Measures
Surface Cleaning
Surface cleaning plays a vital role in the buffing process. It ensures that the surface is free from dirt, oils, or any contaminants that may interfere with the buffing action. By meticulously cleaning the surface, you create an ideal canvas for the buffing disc to work its magic. The key characteristic of surface cleaning is its ability to enhance the adhesion of the buffing compounds and improve overall surface finish. This meticulous process guarantees a smooth and flawless buffing outcome, making it a popular choice among professionals and DIY enthusiasts alike.
Protective Gear
Investing in proper protective gear is non-negotiable when using buffing discs with a drill. Protective gear such as safety goggles, gloves, and a respirator shields you from potential hazards like flying debris, chemical splashes, and harmful fumes. The key characteristic of protective gear is the ability to safeguard your well-being while operating power tools. Ensuring that you have the right protective gear minimizes the risk of injuries and promotes a safe working environment. While it may add an extra step to your routine, the advantages of wearing protective gear far outweigh any inconveniences.
Equipment Inspection
Regular equipment inspection is paramount for ensuring safe and efficient buffing operations. By inspecting your drill and buffing disc before each use, you can identify any wear and tear, loose components, or malfunctions that could compromise your safety or the quality of the finish. The key characteristic of equipment inspection is its preventive nature, helping you catch potential issues before they escalate. This proactive approach saves you time, money, and minimizes the risk of accidents, making it an indispensable practice in the buffing process.
Application Techniques
Proper Speed Settings
Setting the correct speed on your drill is essential for achieving the desired buffing results. Proper speed settings depend on factors such as the material being buffed and the type of buffing disc used. The key characteristic of proper speed settings is their influence on the aggressiveness and finesse of the buffing process. By calibrating the speed correctly, you can optimize material removal, reduce overheating, and enhance overall surface finish. This precise control over speed settings distinguishes professionals from amateurs, making it a vital aspect of using buffing discs effectively.
Correct Pressure
Applying the correct pressure when using a buffing disc is a skill that requires finesse and attention to detail. The key characteristic of applying correct pressure is its impact on material removal and surface contact. Too much pressure can result in excessive abrasion, heat buildup, and potential damage to the surface, while too little pressure may yield ineffective buffing results. Finding the right balance ensures consistent and efficient buffing, prolonging the life of the buffing disc and preserving the integrity of the workpiece. Correct pressure application is a fine art that contributes significantly to the overall success of the buffing process.
Even Application
Maintaining an even application of pressure and movement is essential for uniform buffing results. The key characteristic of even application is its ability to distribute abrasive particles evenly across the surface, preventing swirl marks or uneven finishes. By mastering the art of even application, you can achieve a smooth and flawless surface that showcases your attention to detail and professionalism. Consistency in pressure and motion is key to attaining a mirror-like finish that enhances the aesthetic appeal of your workpiece. Embracing the practice of even application elevates your buffing expertise and sets you apart as a skilled artisan in the world of buffing discs.
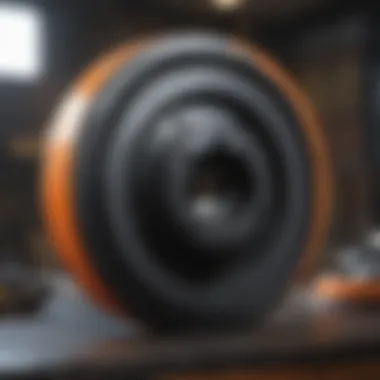
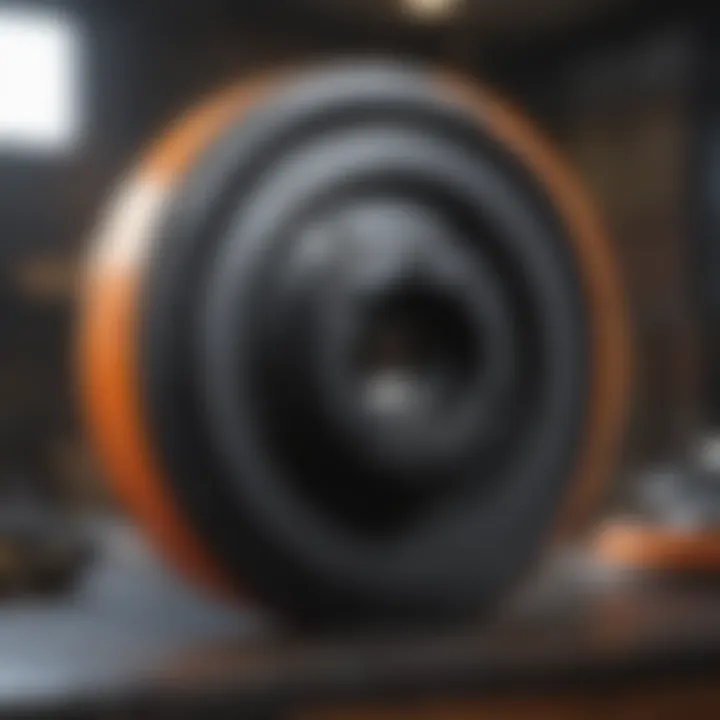
Maintaining and Storing Buffing Discs
Maintaining and storing buffing discs are crucial aspects to ensure their longevity and performance. Proper care and storage practices can significantly impact the effectiveness of the discs and the quality of the results achieved. Regular inspection and appropriate storage techniques are essential components to consider in this process.
Cleaning
Regular Inspection
Regular inspection is a fundamental step in maintaining buffing discs. By regularly examining the condition of the discs, users can identify any signs of wear, damage, or dirt accumulation. This proactive approach helps in preventing potential issues during usage, such as uneven buffing or machine damage. Regular inspection not only extends the lifespan of the discs but also ensures consistent performance.
Proper Storage
Proper storage plays a key role in preserving the integrity of buffing discs. Storing the discs in a clean, dry environment helps prevent contamination and protects them from external elements that may affect their abrasive properties. Organizing discs based on type and size can further facilitate easy access and prevent damage caused by improper stacking. Effective storage practices enhance the longevity of the discs and contribute to maintaining their original quality.
Common Mistakes to Avoid
In the realm of buffing discs for drills, understanding and avoiding common mistakes are paramount to achieving excellent results. This section delves deep into the critical aspects that one should steer clear of when using buffing discs, ensuring a smooth and efficient buffing process. By focusing on the following elements, housewives and homeowners can elevate their buffing game and maintain a safe working environment.
Overlooked Safety Precautions
Lack of Eye Protection:
Eye protection is a cornerstone of safety when using buffing discs. Failing to safeguard your eyes can lead to serious injuries due to splinters, debris, or abrasive particles flying off while buffing. The core characteristic of eye protection lies in its ability to shield the eyes from potential harm, making it an essential choice for any individual engaging in buffing activities. Utilizing specialized safety goggles or glasses provides a safeguard against flying particles, ensuring a secure working environment. While eye protection may seem like a small detail, its inclusion in the buffing process can prevent major mishaps and guarantee a smooth operation.
Incorrect Disc Selection:
Selecting the appropriate disc for the task at hand is crucial for achieving optimal results. Choosing the wrong type of buffing disc can result in ineffective buffing, surface damage, or even accidents. The key characteristic of proper disc selection is matching the disc's material, grit, and size to the specific surface and task requirements. This ensures efficient buffing and prolongs the lifespan of both the disc and the workpiece. By carefully considering the disc's compatibility with the material being worked on, users can prevent unnecessary mishaps and attain a desirable finish.
Improper Technique
Excessive Pressure:
Applying excessive pressure while buffing can lead to a range of issues, including surface scratches, material distortion, and premature wear of the disc. The primary benefit of avoiding excessive pressure lies in preserving the integrity of the workpiece and achieving a consistent finish. By maintaining a balanced pressure level, users can enhance the longevity of both the disc and the material being buffed, resulting in a professional outcome. This technique allows for better control over the buffing process and ensures a uniform appearance across the surface without causing damage.
Inconsistent Speed:
Inconsistent speed during buffing can produce uneven results and compromise the final finish of the surface. Maintaining a steady speed throughout the buffing process is essential for achieving a uniform appearance and preventing swirl marks or other imperfections. The advantageous characteristic of consistent speed lies in its ability to promote precision and control, leading to a flawless finish. By adhering to a consistent speed setting based on the material and buffing disc type, users can significantly improve the overall quality of the buffed surface.
Conclusion
In wrapping up this comprehensive guide to buffing discs for drills, it becomes evident that mastering the art of buffing is a nuanced skill that requires attention to detail and proper technique. Through delving into the various types of buffing discs, selecting the right one based on material, grit, size, and compatibility, as well as understanding the importance of preparation and safety measures, readers have gained valuable insights into optimizing their buffing practices. Additionally, learning about the application techniques focusing on speed settings, pressure application, and ensuring even distribution has equipped readers with the tools necessary for achieving impeccable results.
Furthermore, the significance of maintaining and storing buffing discs through regular inspection, proper cleaning, and storage practices cannot be overstated. By avoiding common mistakes such as neglecting safety precautions and using improper techniques, readers are poised to elevate their buffing experience and enhance the longevity of their discs.