Choosing the Perfect Industrial Equipment Paint: A Comprehensive Guide
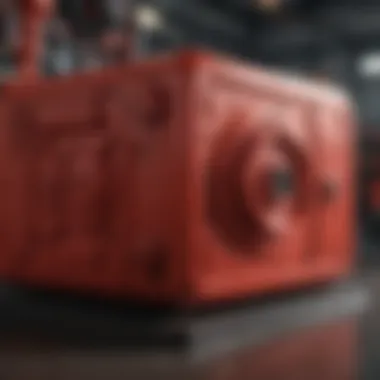
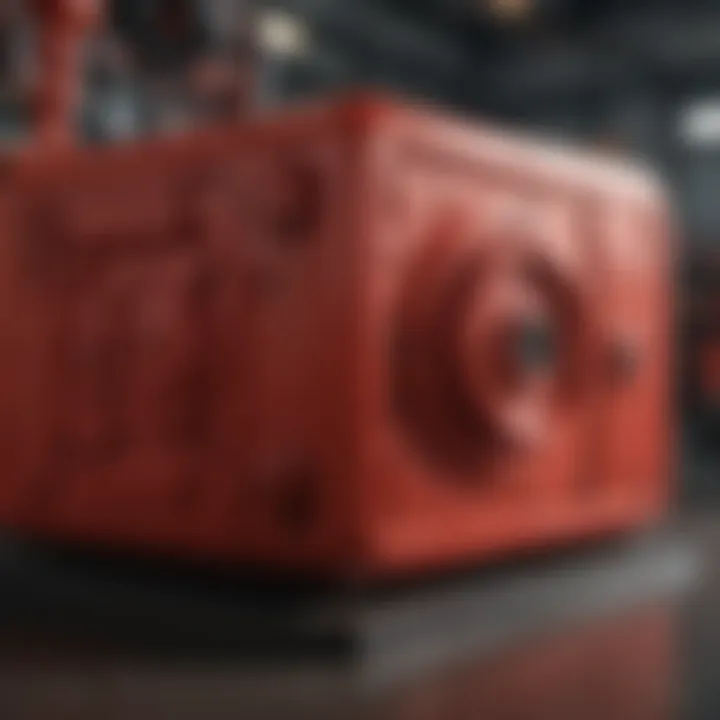
Overview of Topic
When it comes to the home improvement industry, selecting the best paint for industrial equipment is a crucial decision. Industrial equipment is subject to harsh conditions and requires a durable and long-lasting finish to maintain functionality and aesthetics. Choosing the right paint not only enhances the appearance of industrial equipment but also provides protection against corrosion, chemical exposure, and other damaging factors.
Common Challenges and Solutions
Homeowners often face common challenges when painting industrial equipment, such as selecting the appropriate paint type for specific machinery, achieving a smooth and even finish, and ensuring the paint adheres properly to metal surfaces. To overcome these challenges, it is essential to thoroughly prepare the equipment surface by cleaning, sanding, and priming before applying the paint. Additionally, choosing high-quality industrial paints designed for specific substrates and environments can help prevent issues such as chipping, peeling, and fading over time.
Product Recommendations
In the market today, [Industry Brand] offers a range of top-quality industrial equipment paints that cater to different needs and preferences. These products are known for their exceptional adhesion, durability, and resistance to chemicals, abrasion, and UV exposure. Some recommended products from [Industry Brand] include:
- [Product A]: A high-performance enamel paint suitable for metal surfaces, providing excellent corrosion protection and a glossy finish.
- [Product B]: A two-part epoxy coating ideal for machinery exposed to harsh chemicals and extreme temperatures, offering superior durability and impact resistance.
Step-by-Step Guides
To achieve a professional finish when painting industrial equipment, follow these step-by-step guidelines:
- Preparation: Clean the equipment surface thoroughly, remove rust and old paint, and apply a suitable primer.
- Paint Selection: Choose the right type of industrial paint based on the equipment material and environmental factors.
- Application: Use a high-quality brush, roller, or sprayer to apply the paint evenly in thin coats, allowing sufficient drying time between each coat.
- Finishing Touches: Inspect the painted surface for any imperfections, touch up as needed, and apply a clear coat or protective finish for added durability.
- Maintenance: Regularly inspect the painted equipment for signs of wear or damage, and perform touch-ups or recoating as necessary to preserve the finish.
With these guidelines and recommendations in mind, homeowners can confidently choose the best paint for their industrial equipment, ensuring longevity, performance, and aesthetic appeal.
Introduction
When it comes to industrial equipment, selecting the right paint is crucial for ensuring longevity, protection, and visual appeal. The choice of paint can significantly impact the durability and performance of the equipment, making it imperative to make informed decisions. This article serves as a comprehensive guide to help housewives and house owners navigate through the different factors to consider, types of paints available, application techniques, and maintenance practices. By delving into the intricacies of industrial paints, readers will gain an understanding of how to best preserve and enhance the appearance and functionality of their equipment.
Understanding the Importance of Choosing the Right Paint
Enhancing Durability
Enhancing durability is a fundamental aspect when selecting a paint for industrial equipment. The ability of the paint to withstand constant use, varying environmental conditions, and potential abrasions is paramount in ensuring the longevity of the equipment. Industrial paints designed for enhancing durability are formulated with specialized additives and resins that create a robust protective layer on the surface, safeguarding it against wear and tear. This characteristic is essential for industrial equipment subjected to high-impact activities, harsh weather conditions, and chemical exposure. While enhancing durability provides a significant advantage in prolonging the lifespan of the equipment, it is crucial to consider maintenance requirements to maintain its protective properties.
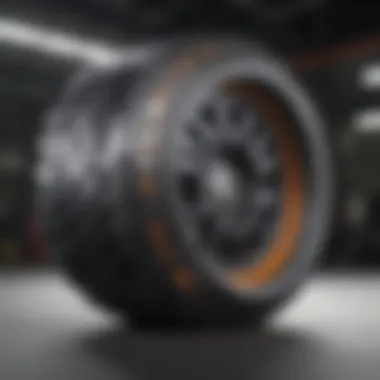
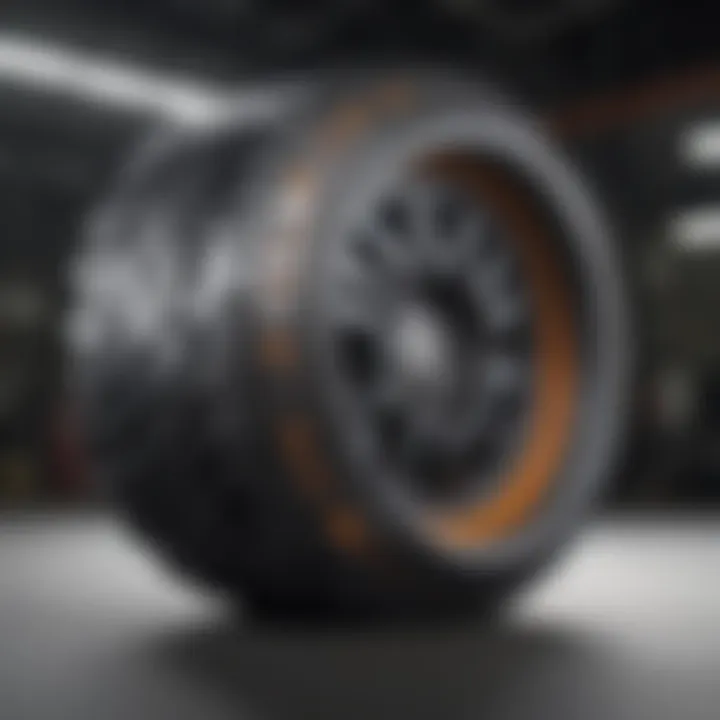
Protection Against Corrosion
Protection against corrosion is a key consideration in industrial settings where equipment is exposed to moisture, chemicals, and other corrosive agents. Industrial paints that offer superior corrosion protection form a barrier that prevents metal surfaces from rusting and deteriorating over time. By inhibiting the process of oxidation, these paints contribute significantly to the structural integrity and operational efficiency of the equipment. The unique feature of corrosion-resistant paints lies in their ability to ward off environmental threats that could compromise the functionality of industrial machinery. While these paints are highly effective in preventing corrosion, proper surface preparation and application techniques are essential for maximizing their protective attributes.
Aesthetics and Brand Image
Apart from functionality, aesthetics and brand image play a crucial role in the selection of paint for industrial equipment. The visual appearance of equipment reflects on the professionalism and brand identity of a business, making it essential to choose paints that not only protect but also enhance the overall aesthetic appeal. Industrial paints formulated to provide a visually appealing finish contribute to a positive brand image and create a lasting impression on clients and stakeholders. Additionally, these paints can be customized to match brand colors, logos, and corporate themes, further reinforcing brand recognition. While aesthetics may not directly impact the performance of equipment, they contribute significantly to creating a cohesive and professional environment in industrial spaces.
Key Factors to Consider
Surface Material
The surface material of industrial equipment plays a critical role in determining the type of paint that is most suitable. Different surfaces require specific paints that adhere effectively and provide long-lasting protection. Whether it is metal, concrete, or plastic, selecting the right paint for the surface material is essential for achieving optimal adhesion and durability. Industrial paints tailored for different surface materials offer unique properties such as adhesion promoters, anti-corrosive agents, and UV resistance, ensuring that the protective coating adheres securely and performs effectively over time. Considering the surface material before choosing a paint is essential for ensuring compatibility and maximizing the longevity of the coating.
Exposure Conditions
Exposure conditions significantly impact the performance and durability of industrial equipment paints. Equipment that is exposed to extreme temperatures, UV radiation, humidity, or chemical fumes requires specialized paints that can withstand these environmental stressors. Understanding the specific exposure conditions of the equipment is crucial for selecting paints with the right protective properties. Industrial paints formulated for high-temperature resistance, UV stability, chemical resistance, or anti-abrasion characteristics offer enhanced protection against the elements, prolonging the lifespan of the equipment. By considering exposure conditions during the paint selection process, housewives and house owners can ensure that their industrial equipment remains suitably protected in challenging environments.
Budget Constraints
Budget constraints play a significant role in determining the type and quality of paint that can be used for industrial equipment. While high-performance paints may offer superior durability and protection, they often come at a higher cost. Balancing budget constraints with the need for quality and longevity is essential for making cost-effective decisions when choosing industrial paints. Opting for paints that provide a good balance between performance and affordability is key to maximizing the value of the investment. Understanding the long-term benefits of higher-quality paints in terms of reduced maintenance and reapplication costs can help housewives and house owners make informed choices that align with their budget constraints.
Types of Industrial Paints
In the realm of selecting the best paint for industrial equipment, understanding the nuances of different types of industrial paints plays a pivotal role. Industrial paints are not one-size-fits-all; each type comes with its unique characteristics that cater to specific needs and environments. Therefore, delving into the realm of industrial paints opens up a world of possibilities where the right choice can make a significant difference in the longevity and performance of your equipment.
Epoxy Paints
Benefits and Applications
Epoxy paints stand out for their exceptional durability and resistance to abrasion and chemicals. They form a tough, protective coating that enhances the lifespan of industrial equipment exposed to harsh conditions. Epoxy paints are coveted for their ability to withstand impacts and rough usage, making them a popular choice for industries requiring heavy-duty protection. Their seamless finish not only safeguards against corrosion but also provides a smooth surface that is easy to clean and maintain.
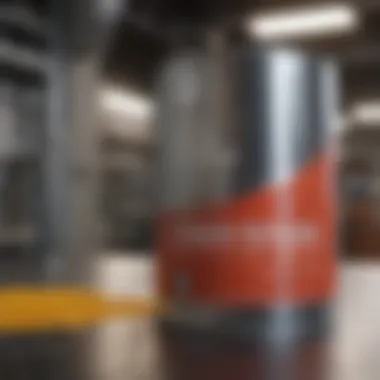
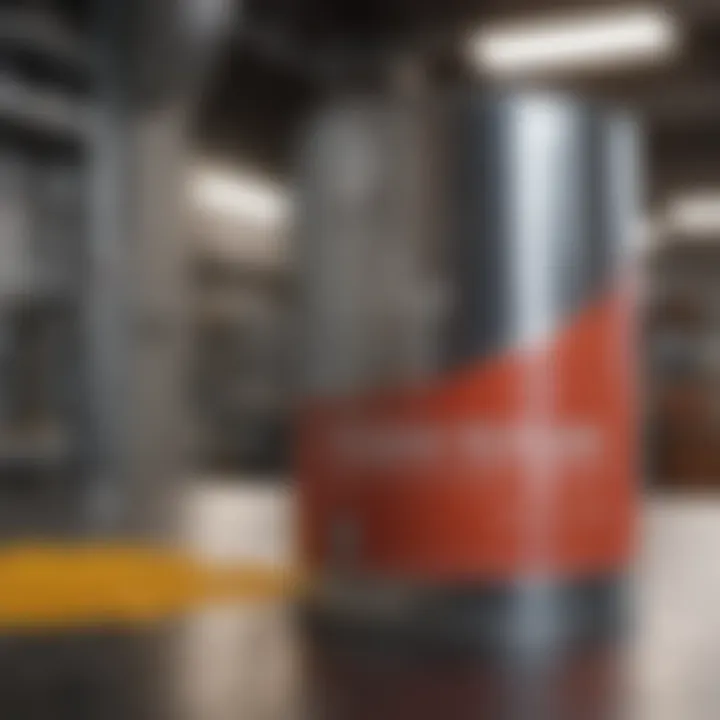
Considerations Before Use
Before opting for epoxy paints, it is crucial to consider factors such as surface preparation and application conditions. The effectiveness of epoxy paints relies heavily on proper surface priming and the absence of moisture or contaminants that can jeopardize adhesion. Additionally, the curing time and temperature requirements must align with the operational environment to ensure the paint sets correctly and endures environmental stresses. While epoxy paints offer superior protection, proper application and adherence to manufacturer guidelines are vital for achieving optimal results.
Polyurethane Paints
Durable Finishes
Polyurethane paints are renowned for their exceptional durability, making them ideal for industrial equipment exposed to extreme weather conditions or corrosive agents. Their resilient finish provides long-lasting protection against UV rays, chemicals, and abrasions, ensuring that equipment maintains its aesthetic appeal and structural integrity over time. Polyurethane paints offer a high-gloss finish that not only enhances the visual appeal but also adds a layer of defense against wear and tear, making them a preferred choice for outdoor applications.
Resistance to Harsh Environments
One of the key strengths of polyurethane paints lies in their ability to resist harsh environmental factors, including temperature fluctuations, moisture, and chemicals. Their chemical-resistant properties make them a suitable option for equipment operating in challenging industrial settings where exposure to corrosive substances is a concern. By forming a robust barrier that shields the surface from degradation, polyurethane paints ensure that industrial equipment maintains its structural integrity and appearance, even in the most aggressive conditions.
Acrylic Paints
Versatility in Applications
Acrylic paints are prized for their versatility in applications, offering a wide range of colors and finishes to suit diverse industrial requirements. They exhibit excellent adhesion to various surfaces, including metal, concrete, and plastics, making them an adaptable choice for different types of equipment. Acrylic paints can be customized to meet specific color preferences and aesthetic needs, providing ample flexibility in design and style options for industrial settings.
Color Retention Properties
The color retention properties of acrylic paints ensure that industrial equipment maintains its vibrancy and appearance for an extended period. Acrylic paints are resistant to fading and discoloration caused by UV exposure or environmental elements, ensuring that the equipment retains its original look and appeal over time. This longevity in color retention reduces the need for frequent repainting or touch-ups, resulting in cost savings and enhanced visual consistency across industrial facilities.
Application Methods
In the realm of industrial equipment paint selection, the application methods play a crucial role in ensuring a successful and long-lasting finish. The effectiveness of chosen paints can be heavily influenced by the method of application, making it a significant aspect to be considered. Selecting the right method for application can enhance the durability of the paint, improve resistance against corrosion, and contribute to a high-quality aesthetic appearance which reflects positively on the brand image.
Spray Painting
Advantages and Best Practices
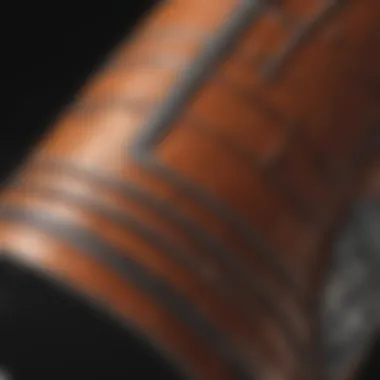
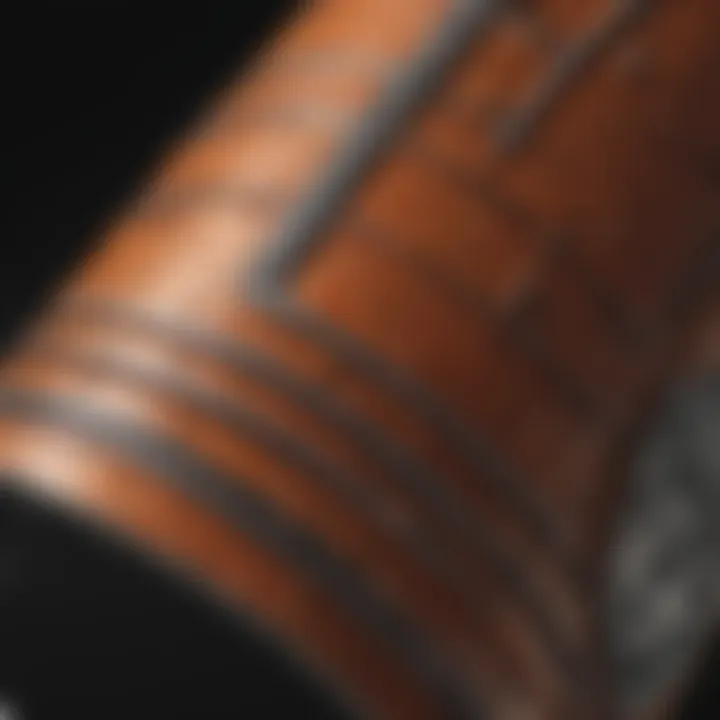
Spray painting stands out for its efficiency and uniform coverage, making it a preferred choice in industrial settings for its ability to provide a smooth, even finish. The key characteristic of spray painting lies in its ability to deliver a professional-grade appearance while saving time and effort. Its precise application ensures a uniform coat, reducing the chances of imperfections appearing on the equipment surface. This method's unique feature of quick application and seamless coverage makes it advantageous for achieving a flawless finish on industrial equipment. However, despite its benefits, care must be taken to avoid overspray and ensure proper ventilation to prevent health hazards linked with the process.
Common Mistakes to Avoid
One common mistake to avoid when undertaking spray painting is neglecting adequate surface preparation. Failure to thoroughly clean and prime the surface can lead to poor adhesion and premature paint failure. Additionally, overlooking environmental factors such as temperature and humidity levels can impact the outcome of the paint job. It is crucial to be mindful of overspray, which can result in wastage and environmental pollution if not controlled effectively. By following best practices and adhering to safety measures, these common mistakes can be mitigated, leading to a successful spray painting application.
Roller Application
Suitable Conditions
Roller application is ideal for large, flat surfaces where a consistent finish is desired. This method thrives in conditions where gravity does not interfere with the coating process, allowing for even distribution of paint. The key characteristic of roller application lies in its versatility and ease of use, particularly on surfaces where spray application may not be suitable. Its unique feature of providing a uniform coat makes it a popular choice for surfaces that require a smooth and even finish. However, roller application may be cumbersome for intricate designs or hard-to-reach areas, necessitating the use of alternative methods for such surfaces.
Techniques for Even Coating
To achieve an even coating using a roller, it is essential to apply consistent pressure and maintain a steady pace while rolling the paint onto the surface. Rolling in overlapping strokes helps to prevent unevenness and ensures a seamless finish. Additionally, proper load management of the roller with paint is crucial to avoid excess drips or thin coverage. Mastering the techniques for even coating with a roller involves practicing consistent pressure and direction, resulting in a professionally finished surface free of streaks and inconsistencies.
Maintenance Tips
In the realm of industrial equipment maintenance, proper care and attention to detail are crucial for ensuring longevity and optimal performance. Maintenance tips serve as the cornerstone of preserving the integrity and functionality of your machinery. By adhering to a well-structured maintenance plan, you can detect early signs of wear, prevent costly breakdowns, and uphold safety standards within your industrial setting.
Regular Inspections
Detecting Early Signs of Wear
Detecting early signs of wear is a critical aspect of equipment maintenance, as it allows you to identify potential issues before they escalate into major problems. By conducting regular inspections and being vigilant for subtle indicators of wear and tear, such as corrosion, rusting, or structural weaknesses, you can proactively address maintenance needs and avoid sudden equipment failures. This proactive approach not only saves time and money but also promotes a safe working environment by reducing the risk of accidents or malfunctions.
Preventive Maintenance Strategies
Preventive maintenance strategies involve implementing proactive measures to preemptively address potential issues and uphold the operational efficiency of industrial equipment. By following a set schedule of inspections, cleaning, lubrication, and parts replacement, you can extend the lifespan of your machinery and mitigate the likelihood of unexpected breakdowns. These strategies not only enhance equipment durability but also optimize performance, reduce downtime, and contribute to overall cost savings in the long run.
Cleaning and Touch-ups
Recommended Cleaning Agents
Selecting the appropriate cleaning agents is essential for maintaining the cleanliness and functionality of industrial equipment surfaces. The right cleaning agents can effectively remove dirt, grease, and contaminants without causing damage to the underlying materials. By using industry-approved cleaning solutions and techniques, you can ensure that your equipment remains in pristine condition, prolonging its lifespan and minimizing the risk of performance issues.
Proper Touch-up Techniques
Proper touch-up techniques are indispensable for addressing minor imperfections, scratches, or areas of damage on industrial equipment surfaces. By employing precise touch-up methods, such as sanding, priming, and painting, you can restore the appearance and protective properties of the affected areas. These techniques not only improve the aesthetic appeal of the equipment but also prevent further deterioration, ensuring its longevity and reliability.
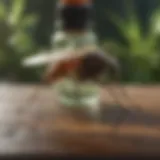
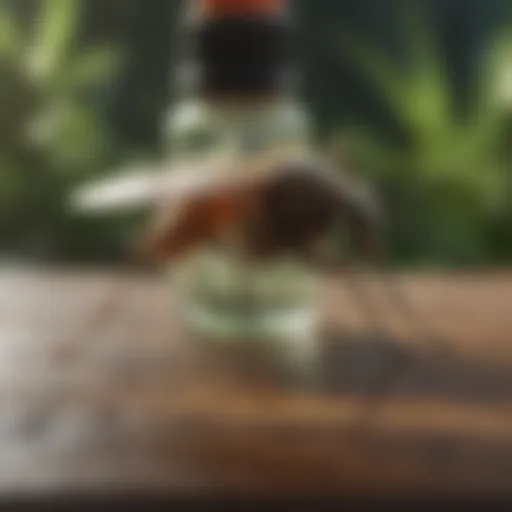