Expert Guide: How to Choose the Best Glue for Plastic to Plastic Car Parts
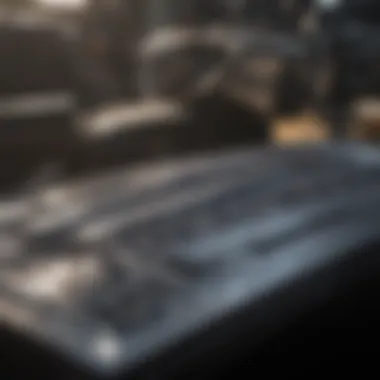

In the realm of home improvement, the selection of an appropriate adhesive for plastic to plastic car parts stands as a crucial and oft-overlooked aspect. Ensuring the right glue choice not only impacts the repair's efficacy but also influences its longevity and resilience. Understanding the subtle nuances between various adhesives becomes paramount to achieving an effective repair solution.
Common Challenges and Solutions
House owners frequently encounter challenges when choosing the best glue for plastic to plastic car parts. Issues like adhesive compatibility, bonding strength, and weather resistance often prove daunting. To conquer these obstacles, one must consider meticulous surface preparation, adhesive selection based on substrate material, and application precision. By addressing these challenges head-on, homeowners can enhance the durability and effectiveness of their car repair endeavors.
Product Recommendations
In the vast landscape of adhesive products, discerning the top industry brands becomes imperative. Brands renowned for their quality and reliability, such as [Industry Brand], offer a myriad of options tailored to plastic to plastic car part repairs. These products boast features like superior bonding strength, weatherproof properties, and ease of application. Embracing recommended products from trusted brands ensures a seamless repair process and long-lasting results.
Step-by-Step Guides
Transitioning from theory to practice, implementing glue solutions for plastic to plastic car parts mandates a systematic approach. Step one involves meticulous surface cleaning to facilitate optimal adhesion. Next, selecting the appropriate adhesive based on material compatibility plays a pivotal role in the repair's success. Application techniques, such as uniform spreading and pressure application, further enhance bonding strength. By following these detailed instructions with precision, homeowners can enjoy durable and reliable results that surpass expectations.
Understanding Different Types of Adhesives
This section delves into the critical aspects of various adhesive options available for plastic to plastic car parts. By comprehending the nuances of different adhesives, individuals can make informed decisions regarding their choice of glue. Understanding the distinct characteristics, benefits, and considerations of each adhesive type is paramount in ensuring successful bonding between plastic car parts.
Epoxy Adhesives
Epoxy adhesives are renowned for their exceptional strength and durability, making them a preferred choice in automotive applications. The Features and Benefits section highlights the high bonding strength, resistance to chemicals and heat, and versatility of epoxy adhesives. Also, the Application Techniques subsection focuses on the importance of precise mixing ratios, proper surface preparation, and effective bonding methods to maximize the adhesive's performance.
Polyurethane Adhesives
Polyurethane adhesives offer a blend of flexibility and strength, catering to the dynamic stress requirements of plastic car parts. The Advantages and Limitations segment emphasizes the adhesive's ability to absorb vibrations, withstand varying temperatures, and resist impacts. In contrast, the Factors to Consider section educates readers on factors such as curing time, adhesive consistency, and bonding surface compatibility when using polyurethane adhesives.
Cyanoacrylate (Super Glue)
Cyanoacrylate adhesives, commonly known as
Factors to Consider Before Choosing the Glue
When embarking on the journey of selecting the ideal adhesive for plastic to plastic car parts, several crucial factors demand consideration. These pivotal aspects pave the path towards a successful bonding outcome, ensuring durability and efficacy in the repair process. Understanding these key elements is quintessential to inform and empower individuals engaged in automotive restoration projects.
Material Compatibility
- Checking Plastic Types:
Exploring the nuances of plastic types is a fundamental step in the adhesive selection process. Different plastics have varying chemical compositions, leading to distinct adhesion characteristics. By identifying the specific plastic materials involved, such as polyethylene or polypropylene, one can ascertain the most compatible adhesive for a robust bond. Considering the diverse range of plastic polymers utilized in automotive applications, meticulous scrutiny of plastic types becomes imperative for achieving optimal bonding strength and longevity.
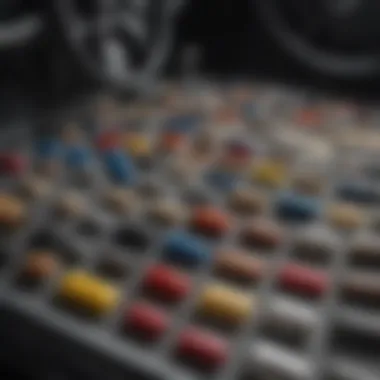

In the realm of plastic repairs, understanding the interaction between adhesives and the specific plastic substrates is pivotal. Various adhesives exhibit differing affinities towards certain plastic compositions, impacting the effectiveness of the bonding process. Consequently, comprehending the plastic types aids in selecting the most suitable adhesive tailored to the repair requirements.
Important Tip: Prioritize identifying the plastic types of car parts to ensure precise adhesive selection for durable repairs.
- Chemical Reactions:
Investigating the chemical reactions between adhesives and plastic substrates illuminates the complexities underlying the bonding process. Each adhesive formulation interacts uniquely with plastics, triggering specific chemical reactions vital for adhesion. By delving into these chemical dynamics, individuals can anticipate the bond strength, curing mechanisms, and overall performance of the adhesive under varying environmental conditions.
The interplay of chemical reactions dictates the adhesive's affinity towards specific plastic surfaces, influencing the bond's resilience to external stressors. Recognizing these intricate chemical processes empowers individuals to make informed decisions regarding adhesive compatibility, ensuring robust and enduring bonds in plastic repair endeavors.
In essence, assessing the chemical reactions between adhesives and plastic substrates furnishes invaluable insights into the adhesive behavior, guiding the selection of suitable adhesives for optimal bonding outcomes.
Factors to Consider Before Choosing the Glue
When engaging with the task of choosing the perfect glue for plastic to plastic car components, it is imperative to ponder on a multitude of critical factors. These elements stand as the bedrock for ensuring a successful adhesion between the plastic parts, propelling the repair process towards efficiency and longevity. Grasping the essence of these factors lays the groundwork for making educated decisions in the realm of vehicle mending.
Strength Requirements
- Assessing Load-Bearing Needs:
In the realm of adhesive selection for plastic to plastic car parts, evaluating the load-bearing requirements holds paramount significance. Understanding the mechanical stresses and strains that the bonded components will endure is essential for determining the adhesive's capacity to withstand these challenges. By assessing the load-bearing needs, individuals can opt for adhesive solutions that align with the specific mechanical demands of the repair, fostering resilience and structural integrity.
The evaluation of load-bearing requirements facilitates the identification of adhesives capable of withstanding the intended stresses, safeguarding the longevity and operational efficiency of the repaired car parts. By delving into the load-bearing aspects, individuals can make informed choices regarding adhesive selection, fortifying the integrity of the plastic-to-plastic bonds.
- Longevity Expectations:
Contemplating the longevity expectations in adhesive selection underscores the pivotal role of durability in automotive reparative endeavors. Anticipating the anticipated lifespan of the adhesive bond aids in selecting formulations that exhibit longevity and endurance under diverse operational conditions. By setting realistic longevity expectations, individuals can choose adhesives that offer sustained performance and reliability throughout the vehicle's lifespan.
The consideration of longevity expectations steers individuals towards adhesive solutions best suited for prolonged usage, mitigating the risk of premature bond failure. Embracing a forward-looking approach towards durability enhances the reliability and functionality of the repaired plastic components, showcasing the importance of longevity assessments in adhesive selection processes.
Factors to Consider Before Choosing the Glue
When delving into the realm of adhesive selection for plastic to plastic car parts, environmental considerations play a pivotal role in determining the adhesive's performance and longevity. Evaluating the impact of environmental factors on adhesive bonds elucidates the significance of creating resilient adhesion capable of withstanding harsh conditions. By incorporating environmental considerations into the adhesive selection process, individuals can ensure sustained bond integrity and operational reliability.
Environmental Considerations
- Exposure to Temperature:
Assessing the adhesive's response to temperature variations is essential in securing robust plastic-to-plastic bonds that withstand fluctuating thermal conditions. Understanding how adhesives behave under different temperature ranges aids in selecting formulations that exhibit stability and effectiveness across diverse environmental scenarios. By delving into the impact of temperature on adhesive performance, individuals can choose formulations resilient to thermal fluctuations, ensuring bond integrity and longevity.
The consideration of temperature exposure directs individuals towards adhesive solutions capable of maintaining bond strength and structural integrity under varying temperature conditions. By factoring in temperature resilience, individuals can optimize the durability and reliability of plastic-to-plastic bonds, underscoring the critical role of environmental considerations in adhesive selection.


- Resistance to Moisture:
Contemplating the adhesive's resistance to moisture infiltration is pivotal in safeguarding plastic-to-plastic bonds from degradation and weakening. Evaluating the adhesive's ability to repel moisture intrusion and maintain adhesion strength in humid environments is essential for creating durable bonds resilient to water exposure. By prioritizing resistance to moisture, individuals can select adhesives that mitigate the risk of bond failure due to environmental moisture, ensuring the longevity and efficacy of plastic repairs.
The focus on moisture resistance underscores the importance of selecting adhesives capable of preserving bond integrity and performance levels in moisture-laden conditions. By addressing moisture resistance in adhesive selection, individuals can fortify plastic-to-plastic bonds against environmental degradation, emphasizing the significance of environmental considerations in achieving durable and reliable adhesive bonds.
Application Techniques for Optimal Bonding
In this article, the Application Techniques for Optimal Bonding play a vital role in ensuring a strong and durable bond between plastic car parts. These techniques significantly impact the overall performance and longevity of the adhesive connection. By focusing on specific elements such as surface preparation, dispensing, and curing, the application techniques elevate the bond's quality and reliability.
Surface Preparation
Cleaning and Sanding
Cleaning and sanding are imperative steps in preparing the surfaces of plastic car parts for bonding. Cleaning removes dirt, dust, and oils that can hinder adhesion, while sanding creates a rough texture on the surface, enhancing the grip of the adhesive. The key characteristic of cleaning and sanding is their ability to promote adhesion by ensuring a clean and properly roughened surface. This crucial preparation step enhances the bond's strength and durability, making it a popular choice for achieving reliable adhesive connections.
Priming if Necessary
Priming, if deemed necessary, is a supplemental step in surface preparation that involves applying a primer to enhance adhesion. The unique feature of priming is its ability to create a strong bond between the adhesive and the plastic surface, especially in challenging conditions. While priming can improve adhesion performance, it may add complexity to the bonding process. Therefore, understanding the advantages and disadvantages of priming in this context is essential for effective application.
Correct Dispensing and Mixing
Applying the Right Amount
Applying the right amount of adhesive is critical for achieving a successful bond between plastic car parts. The key characteristic of applying the right amount lies in achieving a balance between excess and insufficient adhesive. This balance ensures optimal coverage and penetration, leading to a robust bond. Properly applying the right amount of adhesive is a beneficial choice as it minimizes waste and promotes cost-effectiveness in the bonding process.
Ensuring Uniformity
Ensuring uniformity in dispensing and mixing the adhesive is essential for a homogenous bond. The key characteristic of uniformity is its ability to distribute the adhesive evenly across the bonding surfaces, preventing weak spots and ensuring consistent strength. The unique feature of ensuring uniformity is its contribution to the overall reliability and durability of the bond. While maintaining uniformity may require precision and attention to detail, the benefits of a consistently strong bond make it a worthwhile practice.
Clamping and Curing Process
Proper Alignment
Proper alignment of plastic car parts during the bonding process is crucial for establishing a correct fit and maximizing bond strength. The key characteristic of proper alignment is its role in preventing misalignment, which can compromise the integrity of the bond. Proper alignment is a beneficial choice as it promotes structural integrity and enhances the overall performance of the adhesive connection.
Allowing Sufficient Drying Time
Allowing sufficient drying time is essential to ensure that the adhesive cures properly and reaches its full strength. The key characteristic of sufficient drying time is its contribution to bond durability and long-term performance. By allowing the adhesive to cure completely, the bond achieves maximum strength and resilience. While waiting for sufficient drying time demands patience, the advantages of a fully cured bond justify the wait.
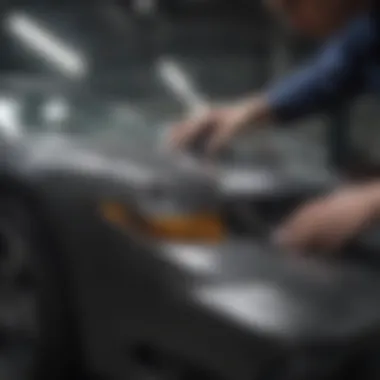

Key Tips for Ensuring Durability
In this segment of the comprehensive guide for selecting the best glue for plastic to plastic car parts, the focus shifts to ensuring the longevity and sturdiness of the bond created. Enhancing durability is crucial to avoid frequent reapplications and maintain the structural integrity of the repaired car parts. By following these key tips, you can significantly improve the effectiveness of the adhesive solution.
- Regular Inspection: One essential tip to ensure durability is to routinely inspect the bonded areas for any signs of wear or weakening. By catching potential issues early, you can prevent any major breakdowns and address them promptly.
- Proper Application: Ensuring that the glue is applied correctly and according to the manufacturer's instructions is vital for long-lasting results. Proper application techniques contribute significantly to the bond's strength and endurance over time.
- Selecting the Right Adhesive: Choosing the most suitable adhesive based on the specific requirements of the plastic materials and the environmental conditions the car will be exposed to is paramount. Selecting an adhesive with the appropriate properties for the intended use enhances the bond's durability.
It is imperative to prioritize durability when selecting and applying glue for plastic to plastic car parts, as this directly impacts the repair's longevity and effectiveness.
Avoiding Common Pitfalls
Avoiding Overapplication
When it comes to adhesive application, overapplication can lead to several issues that compromise the bond's quality. Overapplying adhesive can result in excess material seeping out, creating a mess, and potentially weakening the bond. It is essential to apply the right amount of glue to avoid these pitfalls.
- Benefits of Avoiding Overapplication:
- Cleaner Finish: By avoiding overapplication, you can achieve a neater and more professional-looking repair job.
- Improved Bond Strength: The correct amount of adhesive ensures optimal bonding strength without the risk of excess glue interfering with the connection.
Protecting Bonded Area
To maintain the integrity of the bonded area, it is crucial to protect it from external factors that could compromise the adhesive bond. Proper precautions and protective measures can significantly extend the lifespan of the repaired parts.
- Importance of Protecting Bonded Area:
- Preventing Contaminants: Shielding the bonded area from dust, dirt, and other contaminants preserves the bond's quality and prevents degradation over time.
- Enhancing Longevity: By protecting the bonded area, you ensure that the adhesive bond remains secure and stable, contributing to the overall durability of the repair.
Safeguarding the bonded area is essential to maintain the adhesive bond's strength and integrity, prolonging the effectiveness of the repair.
Regular Maintenance Practices
Checking for Degradation
Regularly checking for any signs of degradation in the adhesive bond is critical for ensuring the long-term effectiveness of the repair. Detecting degradation early allows for timely interventions to maintain the bond's strength and prevent potential failures.
- Benefits of Checking for Degradation:
- Timely Interventions: Early detection of degradation enables prompt repairs or reinforcements to prevent further damage.
- Extended Lifespan: By addressing degradation early, you can prolong the life of the adhesive bond and maintain the repaired parts in optimal condition.
Reinforcement Strategies
Incorporating reinforcement strategies, such as additional support or protective coatings, can further enhance the durability and stability of the adhesive bond. These strategies strengthen weak areas, mitigate potential risks, and ensure the longevity of the repair.
- Advantages of Reinforcement Strategies:
- Enhanced Structural Integrity: Reinforcements provide additional support to critical areas, improving the overall strength of the bond.
- Improved Resistance: By reinforcing weak spots, you increase the bond's resistance to external forces and stressors, enhancing its durability.
Utilizing reinforcement strategies plays a vital role in fortifying the adhesive bond and maintaining the structural integrity of plastic to plastic car parts.