Mastering Angle Grinder Sanding Pads: A Complete Guide for Efficiency
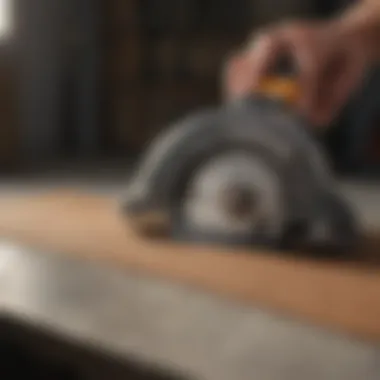
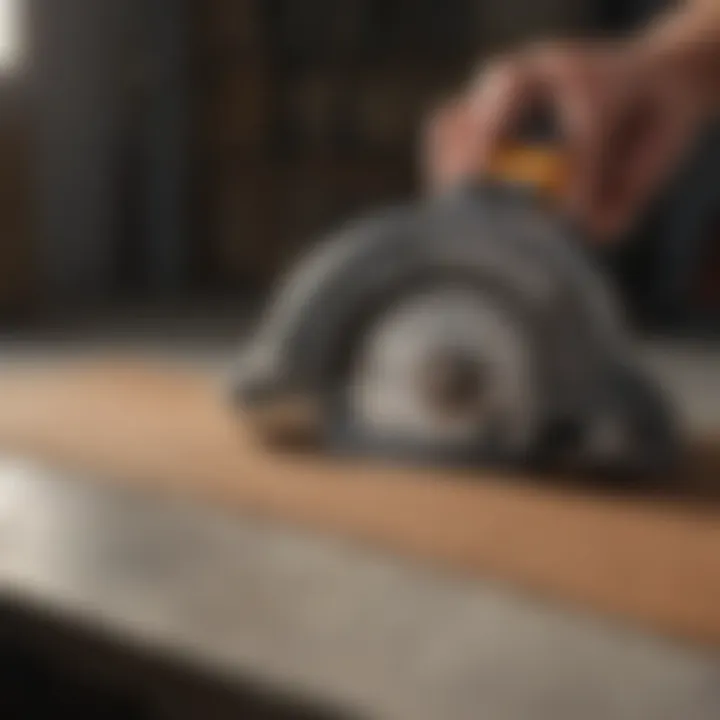
Overview of Angle Grinder Sanding Pads
In the realm of home improvement, angle grinder sanding pads play a pivotal role in achieving smooth and polished surfaces. These small but mighty tools are essential for tasks such as paint removal, rust removal, and surface preparation. The importance of selecting the right sanding pad cannot be overstated, as it directly impacts the quality of the finish and the efficiency of the job at hand.
Common Challenges and Solutions
House owners often face challenges when using angle grinder sanding pads, such as uneven sanding, swirl marks, and material clogging. To address these issues, it is essential to choose the correct grit size for the task at hand, ensure even pressure during sanding, and regularly clean the sanding pad to prevent clogging. Additionally, using a sanding pad with a dust extraction system can help minimize dust and debris buildup, improving overall performance.
Product Recommendations
When it comes to angle grinder sanding pads, [Industry Brand] offers a range of top-quality products that stand out in the market. The [Product A] boasts superior durability and a versatile range of grit sizes, making it suitable for a variety of sanding applications. On the other hand, the [Product B] prides itself on its innovative design, featuring a quick-change mechanism for effortless pad swaps and excellent sanding precision.
Step-by-Step Guides
To maximize the efficiency of angle grinder sanding pads, follow these step-by-step instructions:
- Select the Right Pad: Choose a sanding pad with the appropriate grit size for the material you are working on. Lower grits are ideal for rough sanding, while higher grits are suited for finer finishes.
- Prepare the Surface: Ensure the surface is clean and free of debris before starting the sanding process. This helps prevent scratches and ensures a smooth finish.
- Secure the Pad: Attach the sanding pad securely to the angle grinder following the manufacturer's instructions to prevent slippage during operation.
- Start Sanding: Turn on the angle grinder and begin sanding the surface with even and consistent movements. Avoid applying excessive pressure, as it can lead to uneven sanding and premature pad wear.
- Inspect and Maintain: Regularly inspect the sanding pad for signs of wear and tear, replacing it when necessary. Clean the pad after each use to prolong its lifespan and maintain optimal performance.
By following these guidelines, house owners can effectively harness the power of angle grinder sanding pads for a wide range of home improvement projects, achieving professional results with ease.
Introduction
Angle grinder sanding pads are a crucial tool for achieving precise and smooth finishes on various surfaces. In this article, we will delve deep into the intricacies of these sanding pads, providing a comprehensive guide tailored for housewives and homeowners. By understanding the different types, applications, and best practices associated with angle grinder sanding pads, readers will be equipped with the knowledge to enhance their sanding projects effectively and efficiently.
Understanding Angle Grinder Sanding Pads
Types of Sanding Pads
When it comes to types of sanding pads, the market offers a wide array of options to choose from, each suited for particular sanding tasks. From flap discs to fiber discs and abrasive wheels, the variation in sanding pads allows for versatility in handling different materials and achieving varying levels of finish. The key characteristic of these pads lies in their abrasive material composition, which determines their effectiveness in material removal and surface refinement. Selecting the right type of sanding pad depends on the specific project requirements, considering factors such as material hardness, surface texture, and desired finish. While some pads excel in aggressive material removal, others focus on precision and fine finishing, providing users with a customizable approach to sanding tasks.
Materials Used
The materials used in manufacturing sanding pads significantly impact their performance and durability. Common materials include aluminum oxide, zirconia alumina, ceramic alumina, and silicon carbide, each offering unique properties that cater to different sanding needs. Aluminum oxide pads are known for their versatility and cost-effectiveness, making them a popular choice for general-purpose sanding. On the other hand, zirconia alumina pads are lauded for their enhanced durability and heat resistance, ideal for heavy-duty applications. Understanding the properties of different materials is essential in selecting the most suitable sanding pad for the task at hand, ensuring optimal results with minimal wear and tear.
Benefits of Using Sanding Pads
The benefits of using sanding pads extend beyond surface finishing, encompassing efficiency, precision, and overall project quality. Sanding pads facilitate smoother material removal compared to traditional abrasives, allowing for faster and more consistent results. Moreover, their ergonomic design enables comfortable handling and reduces user fatigue during extended use. By utilizing sanding pads, users can achieve greater control over the sanding process, leading to enhanced precision and a higher degree of finish refinement. Additionally, the reusable nature of sanding pads makes them a cost-effective solution in the long run, providing sustained performance across multiple projects without sacrificing quality.
Applications of Angle Grinder Sanding Pads
Woodworking
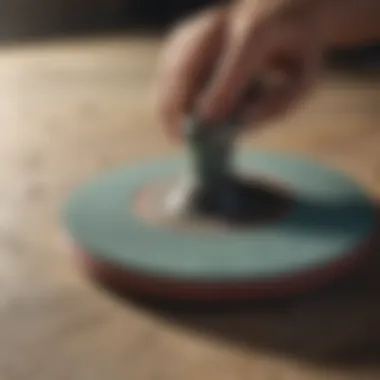
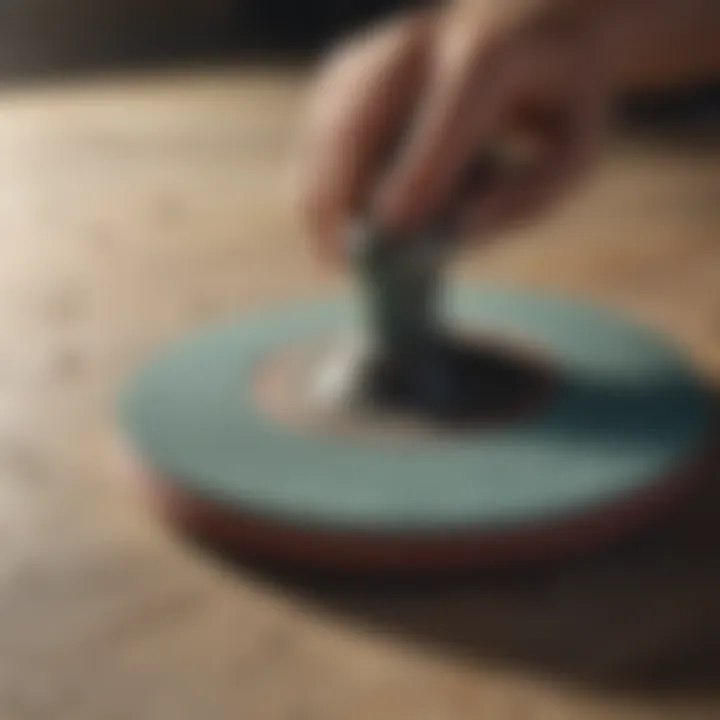
In woodworking applications, angle grinder sanding pads play a crucial role in shaping and refining wooden surfaces. Whether smoothing rough edges, sanding intricate patterns, or preparing wood for staining, these sanding pads offer versatility and precision. Woodworkers can choose from a variety of grit sizes and pad strengths to cater to different wood types and finishing requirements, ensuring a flawless end result that highlights the natural beauty of the wood.
Metal Fabrication
Metal fabrication projects benefit greatly from the use of angle grinder sanding pads, which are designed to handle the rigors of metal surfaces. From removing rust and corrosion to polishing welds and preparing surfaces for painting, these sanding pads provide the necessary abrasiveness and durability to tackle tough metalwork tasks. With the right selection of pads and proper technique, metal fabricators can achieve smooth, blemish-free metal surfaces that meet the highest quality standards.
Concrete Polishing
Concrete polishing requires precision and finesse, which can be achieved effectively with angle grinder sanding pads. Whether honing concrete countertops, smoothing floors, or polishing decorative concrete elements, these pads offer the abrasion power needed to transform rough concrete surfaces into sleek, professional finishes. With varying pad sizes and grit options tailored for concrete polishing, users can achieve desired gloss levels and surface smoothness, enhancing the aesthetic appeal and durability of concrete structures.
Choosing the Right Sanding Pad
Grit Size
The grit size of a sanding pad is a critical factor in determining the level of surface abrasion and finish refinement. Lower grit sizes, such as 40-80, are suitable for heavy material removal and leveling uneven surfaces, while higher grit sizes, typically above 120, focus on fine sanding and polishing. Choosing the right grit size depends on the initial surface condition, material hardness, and desired finish level, empowering users to customize their sanding approach for optimal results. By matching the grit size to the project requirements, users can achieve smooth, professional finishes with efficiency and precision.
Backing Material
Backing materials in sanding pads provide the necessary support and structure for abrasive materials to work effectively. Common backing materials include cloth, fiber, paper, and film, each offering unique levels of flexibility, durability, and heat resistance. Cloth backing, known for its tear resistance, is suitable for heavy-duty sanding tasks, while paper backing provides flexibility for contour sanding. Understanding the strengths and limitations of different backing materials is crucial in selecting the most appropriate pad for specific applications, ensuring optimal performance and longevity.
Pad Size
The size of a sanding pad directly influences its coverage area and abrasion capacity, affecting the speed and efficiency of the sanding process. Smaller pad sizes are favored for detailed or intricate work, offering enhanced maneuverability and access to tight spaces. On the other hand, larger pad sizes excel in covering extensive surface areas quickly, ideal for bulk material removal and rough sanding. By considering the project scale, surface dimensions, and intricacy of detailing, users can determine the optimal pad size that aligns with their sanding goals, enabling efficient and effective completion of tasks.
Usage Techniques
In the realm of angle grinder sanding pads, usage techniques play a pivotal role in achieving optimal results. Understanding how to effectively handle these tools not only ensures safety but also significantly impacts the quality of the sanding outcomes. By delving into usage techniques, individuals can fine-tune their skills and elevate their sanding capabilities to new heights. Proper handling of angle grinder sanding pads involves a series of essential steps that users must adhere to for successful usage.
Proper Handling of Angle Grinder Sanding Pads
Safety Precautions
When it comes to using angle grinder sanding pads, safety precautions stand as a critical aspect that cannot be overlooked. Ensuring the implementation of proper safety measures minimizes the risk of accidents and injuries during the sanding process. Proper eye protection, suitable clothing, and a secure grip on the angle grinder are among the key components of safety precautions. By emphasizing safety, users can create a secure working environment and focus on the task at hand without compromising their well-being.
Optimal Pressure Application
Optimal pressure application is another fundamental element of using angle grinder sanding pads effectively. Applying the right amount of pressure is crucial for achieving desired sanding results without causing damage to the workpiece. Understanding the appropriate pressure levels based on the material being sanded can prevent uneven surfaces and prolong the lifespan of the sanding pads. By mastering optimal pressure application, users can enhance the efficiency and precision of their sanding projects.
Avoiding Common Mistakes
Avoiding common mistakes is imperative when utilizing angle grinder sanding pads to ensure seamless operations. Mistakes such as excessive pressure, incorrect pad attachment, or failure to secure the workpiece adequately can lead to subpar sanding outcomes. By recognizing and avoiding these common pitfalls, users can maintain consistency in their sanding work and produce high-quality results. Through vigilance and attention to detail, individuals can overcome challenges and achieve optimal performance while using angle grinder sanding pads.
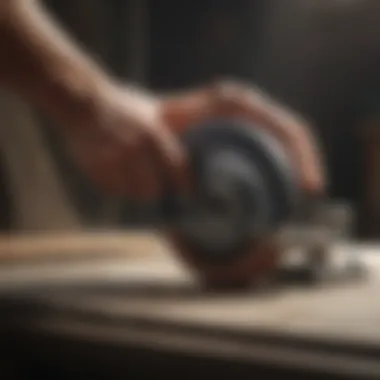
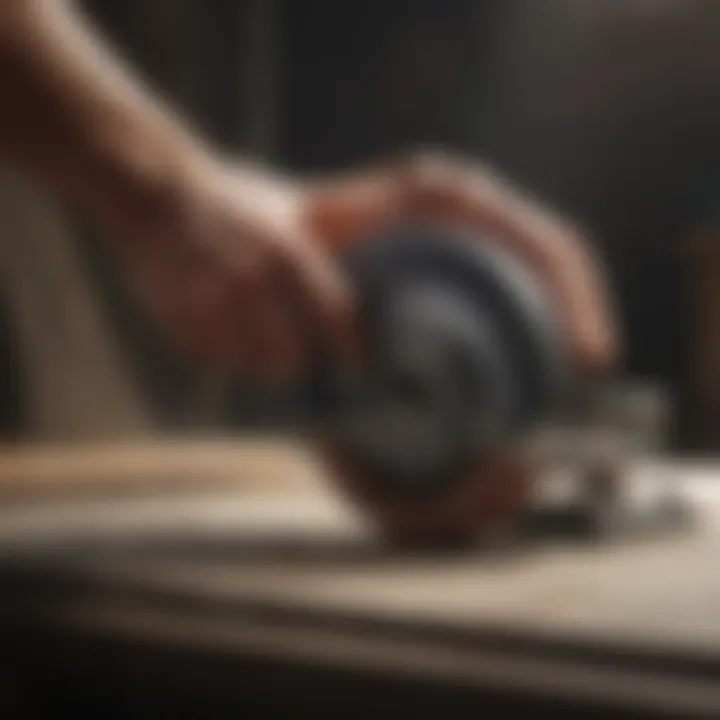
Grinding vs. Sanding
In the context of angle grinder sanding pads, understanding the distinction between grinding and sanding is essential for selecting the appropriate technique for specific applications. While both processes involve material removal, their techniques, purposes, and outcomes vary significantly. By dissecting the key differences between grinding and sanding, users can make informed decisions on the best approach for their projects.
Key Differences
The key differences between grinding and sanding lie in their abrasive methods and intended results. Grinding typically involves using abrasive wheels to remove excess material or shape workpieces with precision. On the other hand, sanding utilizes abrasive pads to smooth surfaces, eliminate imperfections, and prepare them for finishing touches. By discerning these disparities, individuals can tailor their techniques to suit the desired outcomes and optimize their sanding efforts.
When to Choose Sanding
Knowing when to choose sanding over grinding can significantly influence the overall effectiveness of a project. Sanding is often preferred for tasks that require surface refinement, texture enhancement, or paint preparation. By recognizing the specific needs of a project, users can decide whether sanding is the most suitable method for achieving the desired result. Selecting the right technique ensures efficient material removal, consistent results, and a professional finish, making sanding a valuable tool in any woodworking, metal fabrication, or renovation project.
Effective Sanding Techniques
Mastering effective sanding techniques is key to achieving flawless finishes and professional results in various applications. Whether working with wood, metal, or concrete, understanding grain orientation, cross-grain sanding, and finishing touches can elevate the quality of sanding outcomes and improve overall efficiency.
Grain Orientation
Grain orientation refers to the direction of the material's natural fibers, which directly affects the sanding process's efficiency. By sanding with the grain, users can prevent splintering, achieve smoother surfaces, and maintain the material's structural integrity. Understanding grain orientation allows individuals to work with the material's natural properties and produce superior results with minimal effort. By aligning sanding techniques with grain direction, users can unlock the full potential of angle grinder sanding pads and enhance their craftsmanship.
Cross-Grain Sanding
Cross-grain sanding involves sanding perpendicular to the material's natural grain direction, offering a unique approach to smoothing surfaces and removing imperfections. This technique is particularly effective for leveling uneven surfaces, removing stubborn marks, and preparing materials for subsequent finishing treatments. While cross-grain sanding may result in slightly rougher surfaces, it provides a quicker and more aggressive material removal method compared to traditional grain-aligned sanding. By incorporating cross-grain sanding into their repertoire, users can address challenging sanding tasks with precision and efficiency.
Finishing Touches
Adding finishing touches to sanding projects is the final step in achieving professional results and enhancing the aesthetic appeal of the finished workpiece. Finishing touches involve refining the surface, eliminating micro-scratches, and preparing the material for painting, staining, or sealing. By paying attention to detail and incorporating meticulous finishing techniques, users can elevate the overall quality of their sanding projects and create stunning outcomes. From smoothing edges to polishing surfaces, mastering finishing touches ensures that every project is completed with finesse and precision.
Maintenance and Care
In the realm of angle grinder sanding pads, maintenance and care play a crucial role in ensuring their longevity and optimal performance. By incorporating a solid maintenance routine, users can extend the lifespan of their sanding pads while also maximizing their efficiency during various applications. This section will delve into the specific elements, benefits, and considerations regarding maintenance and care, providing insights that are valuable for both novice users and seasoned professionals.
Cleaning and Storage
Removing Residue
Removing residue from angle grinder sanding pads is a pivotal task to maintain their effectiveness. The careful removal of accumulated debris, such as wood or metal shavings, old adhesives, or dust particles, ensures that the pad's abrasive surface remains clean and ready for the next sanding task. This process aids in preventing clogging, which can diminish the sanding pad's ability to perform optimally. Properly removing residue also helps in preserving the material being worked on by avoiding scratches or marks caused by debris buildup.
Proper Drying
Properly drying angle grinder sanding pads post-cleaning is essential to prevent the growth of mold or mildew, which can compromise their abrasive qualities. By allowing the pads to fully dry before storage, users can maintain their structural integrity and prevent any degradation of the abrasive material. Additionally, ensuring that the pads are completely dry before reuse helps in avoiding any potential safety hazards that may arise from moisture retention.
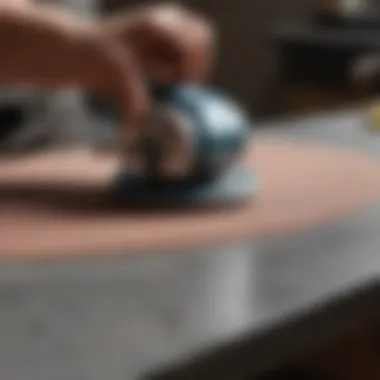
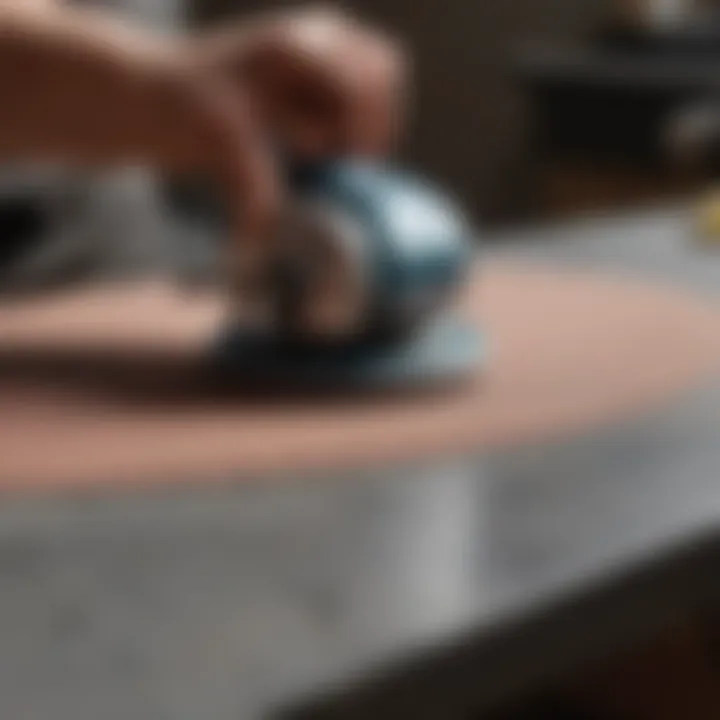
Storage Tips
Effective storage is key to prolonging the lifespan of angle grinder sanding pads. Storing the pads in a clean, dry environment away from direct sunlight and extreme temperatures helps in preserving their quality over time. Proper organization of pads based on size and grit type can further prevent damage and facilitate easy access during projects. Implementing storage solutions such as designated containers or racks can aid in extending the longevity of the pads by safeguarding them from impacts, dust, and other potential harms.
Replacing Worn Sanding Pads
Signs of Wear
Recognizing the signs of wear on angle grinder sanding pads is essential for maintaining a high level of efficiency during sanding tasks. Signs such as reduced abrasive effectiveness, uneven wear patterns, or visible damage indicate the need for replacement. Failing to replace worn pads can lead to subpar results, increased sanding time, and potential damage to the material being worked on. By staying vigilant and identifying these signs promptly, users can ensure consistent and quality outcomes in their sanding endeavors.
Installation Steps
Proper installation of sanding pads is critical for optimal performance and safety. Following correct installation steps, which may vary based on the pad type and grinder model, ensures a secure attachment that minimizes the risk of slippage or detachment during use. Thoroughly cleaning the pad mounting surface, aligning the pad correctly with the grinder's attachment mechanism, and securely fastening the pad according to manufacturer guidelines are key steps for successful installation. By adhering to proper installation techniques, users can enhance the efficiency and longevity of their angle grinder sanding pads.
Extending Lifespan
Regular Inspection
Conducting regular inspections of angle grinder sanding pads is a proactive measure to identify potential issues early and maintain their peak performance. Inspecting for signs of wear, damage, or uneven wear patterns allows users to address any concerns promptly and take corrective actions, such as replacements or maintenance, as needed. Regular inspections also enable users to assess the overall condition of their pads, ensuring they are always ready for optimal performance during various sanding tasks.
Correct Storage
Proper storage practices significantly impact the lifespan of angle grinder sanding pads. Storing the pads in a designated area, free from contaminants and humidity, can prevent premature wear and degradation. Additionally, correctly storing pads based on size and grit type facilitates easy access and helps users keep track of their inventory. Implementing correct storage techniques, such as hanging pads vertically or storing them in padded containers, safeguards the pads from physical damage and prolongs their usability over time.
Conclusion
In the realm of angle grinder sanding pads, the conclusion serves as a pivotal point that consolidates key insights garnered throughout this detailed guide. As readers journey through the nuances of sanding pad types, applications, selection criteria, and maintenance practices, the conclusion ties together the relevance and significance of each aspect. It encapsulates the essence of maximizing efficiency and effectiveness in sanding tasks.
Summary of Key Points
Key Takeaways
Exploring the nuances of key takeaways in the context of this comprehensive guide astutely reveals the critical elements that elevate the utility of angle grinder sanding pads. Whether it's understanding the intricate balance between grit size, backing material, and pad size, or delving into the finesse of grain orientation and finishing touches, key takeaways empower readers to make informed decisions and execute sanding tasks with precision and finesse. The inherent utility and practical applicability of these key takeaways underscore their essential role in enhancing sanding outcomes.
Future Applications
Delving into the realm of future applications unveils a landscape of possibilities and advancements that can further augment the utility of angle grinder sanding pads. From innovating grit technologies to advancing backing materials and pad designs, future applications hold the promise of enhancing efficiency, durability, and precision in sanding tasks. Embracing these forward-looking advancements ensures that users can stay at the forefront of sanding innovations, unlocking new possibilities and efficiencies in their projects.
Final Thoughts
Importance of Quality Pads
The significance of quality pads reverberates throughout the narrative of this ultimate guide, emphasizing the critical role they play in ensuring optimal sanding outcomes. Quality pads not only contribute to smoother sanding processes but also enhance precision, durability, and overall user experience. By underscoring the importance of investing in top-notch sanding pads, readers are encouraged to prioritize quality as a cornerstone of their sanding endeavors.
Continuous Learning
The ethos of continuous learning emerges as a guiding principle that propels users towards mastery and excellence in their sanding pursuits. Embracing a mindset of continuous improvement, experimentation, and exploration nurtures growth, innovation, and efficiency in sanding practices. By championing continuous learning, users foster a culture of adaptation and resilience, ensuring that they remain adept at tackling diverse sanding challenges and harnessing the full potential of angle grinder sanding pads.