Unveiling the Secrets of Sandpaper Grinding Discs: A Comprehensive Guide
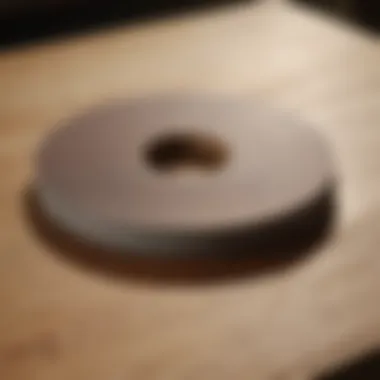
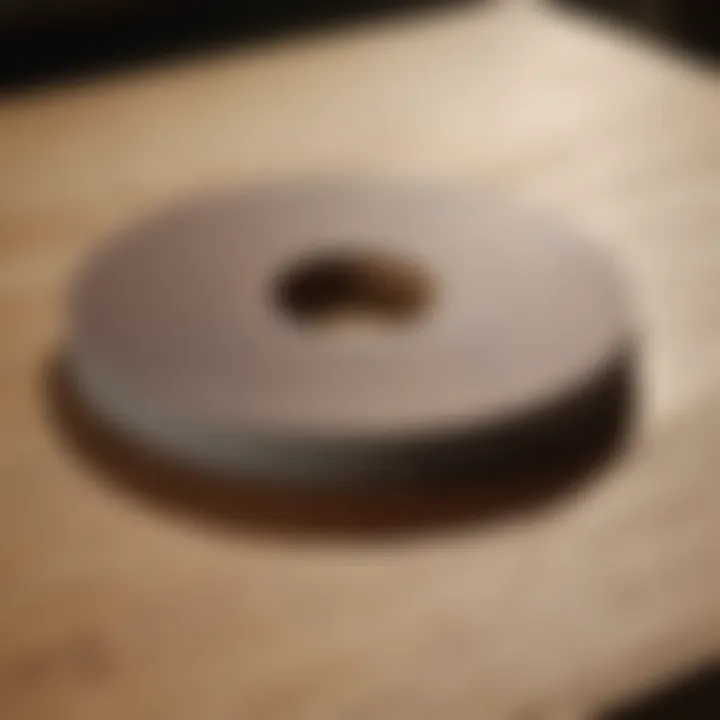
Overview of Sandpaper Grinding Discs
Sandpaper grinding discs are indispensable tools in the home improvement industry. They play a crucial role in achieving smooth and polished surfaces across various materials. Whether you are a DIY enthusiast or a professional contractor, understanding the nuances of these discs can significantly impact the quality of your projects.
Importance of Sandpaper Grinding Discs
The significance of sandpaper grinding discs lies in their ability to efficiently remove material, smooth rough surfaces, and prepare surfaces for painting or finishing. These discs come in a range of grit sizes, each serving a specific purpose in the surface preparation process. By choosing the right disc and using it appropriately, you can elevate the outcome of your projects to a professional level.
Common Challenges in Sandpaper Grinding
Homeowners often encounter challenges when using sandpaper grinding discs, such as uneven sanding, clogging, and premature wear of the disc. To address these issues effectively, it is essential to follow best practices and utilize proper techniques. By understanding these common pitfalls and implementing suitable solutions, you can achieve optimal results in your sanding endeavors.
Solutions for Common Challenges
To combat uneven sanding, it is crucial to maintain consistent pressure and use a rhythmic motion while sanding. Clogging can be prevented by periodically cleaning the disc during use. Additionally, choosing high-quality discs with superior durability can reduce premature wear and ensure longer usage.
Product Recommendations for Sandpaper Grinding Discs
When it comes to sandpaper grinding discs, [Industry Brand] offers a diverse range of products known for their quality and performance. The [Brand X] series, for instance, stands out for its exceptional durability and versatility across different surfaces. These discs are designed to deliver consistent results, making them a preferred choice among professionals in the industry.
Benefits of [Brand ] Discs
- Superior durability for extended usage
- Optimal performance on various materials
- Reduced risk of clogging for uninterrupted sanding
- Enhanced efficiency in surface preparation
Step-by-Step Guide for Using Sandpaper Grinding Discs
- Select the Right Grit Size: Begin by choosing the appropriate grit size based on the material and the level of sanding required.
- Prepare the Surface: Ensure the surface is clean and free of any debris before starting the sanding process.
- Secure the Disc: Attach the sandpaper grinding disc securely to the grinder or sander, following the manufacturer's instructions.
- Start Sanding: Begin sanding in smooth, overlapping motions, applying consistent pressure for even results.
- Keep the Disc Clean: Regularly clean the disc during sanding to prevent clogging and maintain optimal performance.
- Inspect the Surface: Check the sanded surface periodically to evaluate progress and make any necessary adjustments.
- Finish and Enjoy the Result: Once the desired finish is achieved, finish off the surface as required for a polished outcome.
By following these step-by-step instructions and incorporating high-quality sandpaper grinding discs into your projects, you can elevate your home improvement endeavors with professional results.
Introduction
Sandpaper grinding discs play a pivotal role in various projects, offering immense utility for tasks ranging from minor touch-ups to major renovations. Understanding the nuances of these discs is crucial for achieving impeccable results with finesse. This guide will delve deep into the intricacies of sandpaper grinding discs, enlightening readers on their composition, usability, and advantages.
What are Sandpaper Grinding Discs?
Composition and Materials
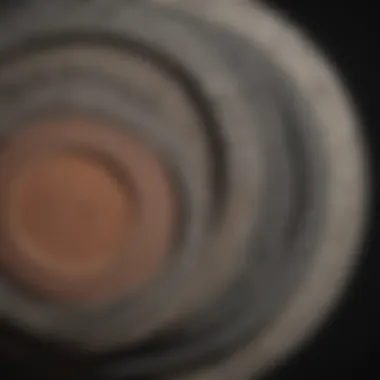
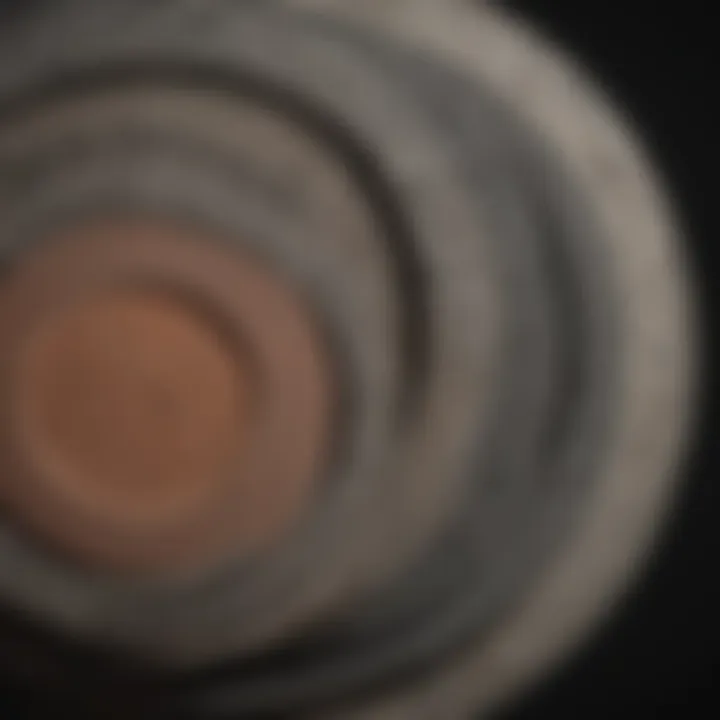
Sandpaper grinding discs are meticulously crafted tools designed with precision and attention to detail. They typically consist of abrasive particles embedded in a bonding agent, ensuring optimal abrasion during surface preparation. The materials used vary but commonly include aluminum oxide, silicon carbide, or zirconia alumina. Each component contributes uniquely to the disc's performance, ensuring durability and efficiency in smoothing surfaces with exceptional results. The versatility and strength derived from these materials make sandpaper grinding discs a preferred choice among professionals and enthusiasts seeking unparalleled finishing.
Functionality and Purpose
The primary function of sandpaper grinding discs is to abrade surfaces efficiently, smoothing rough areas and preparing them for finishing touches. Their abrasive nature allows for precise material removal while maintaining uniformity in surface texture. These discs excel in tackling a myriad of materials, from wood to metal, showcasing their adaptability across diverse applications. Their purpose extends beyond mere surface smoothing, as they assist in shaping, refining, and polishing, delivering impeccable results with minimal effort. The unique feature of sandpaper grinding discs lies in their ability to offer consistent performance and longevity, contributing to enhanced productivity and superior outcomes.
Importance of Sandpaper Grinding Discs
Efficiency in Surface Preparation
Efficiency in surface preparation is a hallmark feature of sandpaper grinding discs. These discs facilitate swift removal of imperfections, fl
Grit Sizes
Grit sizes play a crucial role in the realm of sandpaper grinding discs. Understanding the intricacies of grit sizes is essential for achieving optimal results in various projects. The granularity of the abrasive material determines the level of roughness or smoothness that can be achieved on the surface being worked on. Different applications require specific grit sizes to ensure efficient and effective material removal and finishing.
Understanding Grit Sizes
Coarse Grits
Coarse grits serve as the initial step in the sanding process, known for their aggressive material removal capabilities. The primary characteristic of coarse grits is their larger particle size, which aids in quickly leveling uneven surfaces and removing tough coatings or paint layers. Despite their effectiveness in rapid material removal, using coarse grits on delicate materials may result in surface damage due to their abrasive nature. However, for tasks demanding heavy-duty sanding and shaping, coarse grits stand out as a popular choice due to their efficiency.
Medium Grits
Medium grits bridge the transition between coarse and fine abrasives, offering a balanced approach to surface preparation. Their moderate particle size enables them to smoothen rough surfaces left by coarse grits while still being capable of removing minor imperfections effectively. One key characteristic of medium grits is their versatility, making them suitable for a wide range of applications across different materials. They strike a balance between material removal and surface refinement, making them a valuable option for various projects.
Fine Grits
Fine grits excel in providing a smooth and polished surface finish, ideal for preparing surfaces for final treatments such as painting or staining. These finer abrasives have a smaller particle size, allowing them to refine surfaces with precision and minimal risk of damage. The main advantage of fine grits lies in their ability to achieve a high level of surface smoothness, crucial for achieving professional-quality results. However, fine grits may require more time and patience during the sanding process to achieve the desired finish.
Extra Fine Grits
Extra fine grits represent the pinnacle of surface refinement, suited for achieving a mirror-like finish on materials. These ultra-fine abrasives possess the smallest particle size among grit types, capable of removing minute imperfections and providing an exceptionally smooth surface texture. Despite their ability to deliver unparalleled smoothness, extra fine grits demand careful handling to prevent over-sanding and surface damage. Their advantages lie in the impeccable finishing they offer, making them indispensable for tasks requiring unparalleled surface quality.
Types of Sandpaper Grinding Discs
In delving deep into the realm of sandpaper grinding discs, one cannot overlook the significance of understanding the types available. The diversity in sanding discs plays a crucial role in achieving various finishes and effects, making it imperative to comprehend the distinctions between them. Each type brings its own set of advantages, considerations, and applications, catering to different needs and preferences of users.
Resin Fiber Discs
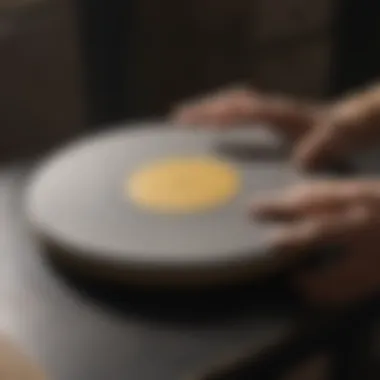
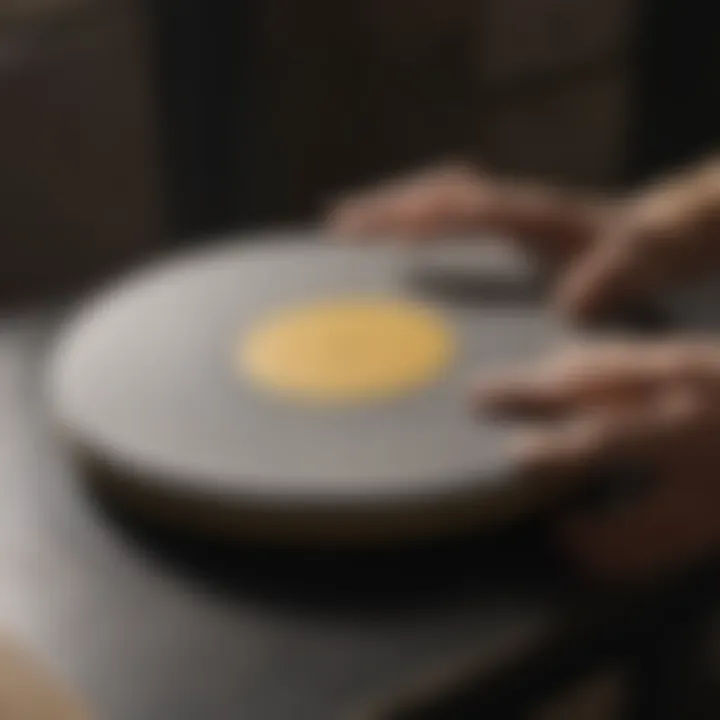
Composition and Advantages
When discussing resin fiber discs, one cannot dismiss their unique composition and the advantages it offers. Comprising a blend of resin and abrasive materials, resin fiber discs are known for their exceptional durability and cutting capabilities. The resin bonding enhances the disc's strength and heat resistance, making it suitable for tough grinding tasks requiring longevity and reliability. By understanding the composition of resin fiber discs, users can appreciate their effectiveness in achieving smooth finishes and precise results, especially on metals and hardwoods.
Ideal Applications
Moreover, exploring the ideal applications of resin fiber discs sheds light on their versatile nature. These discs excel in heavy-duty grinding and stock removal applications, where efficiency and consistent performance are paramount. Their ability to maintain sharpness and withstand high pressure makes them a preferred choice in industrial settings and workshops. Whether for shaping, deburring, or blending, resin fiber discs prove their worth in various metal and woodworking projects, elevating the quality of workmanship and productivity.
Flap Discs
Flexibility and Durability
Moving on to flap discs, their key attributes of flexibility and durability stand out as defining features. The angled flaps of abrasive cloth on a sturdy backing enable flap discs to conform to contoured surfaces with ease, ensuring uniform material removal across the workspace. This flexibility not only simplifies intricate grinding tasks but also reduces the risk of surface gouging or overgrinding. Additionally, the durable construction of flap discs extends their lifespan, offering cost-effective solutions for long-term projects that demand consistent results.
Suitable Uses
The versatility of flap discs extends to their suitability for various applications, from light grinding to blending and finishing operations. Their gentle yet effective abrasive action makes them ideal for surface preparation, rust removal, and weld blending tasks across different materials. From stainless steel to aluminum, flap discs deliver smooth finishes and optimal results, making them a versatile choice for both DIY enthusiasts and professionals in need of a reliable grinding tool.
Sanding Belts
Structure and Function
Lastly, sanding belts present a different approach to material removal with their linear action and robust structure. The continuous loop of coated abrasives offers extended coverage and consistent results when working on large surface areas or uneven contours. Their stable backing and efficient abrasive material enhance the cutting power and precision of sanding belts, providing a steady performance for heavy-duty sanding tasks that require meticulous attention to detail.
Applications in Detail
The detailed applications of sanding belts emphasize their role in aggressive material removal and surface leveling. From stripping paint to shaping wood, sanding belts offer thorough and uniform results, ensuring a smooth surface ready for finishing touches. Their efficient stock removal capabilities make them essential in woodworking, metalworking, and various fabrication processes, where precision and speed are essential for achieving desired outcomes.
Choosing the Right Disc
In the realm of sandpaper grinding discs, the decision-making process of selecting the appropriate disc holds immense significance. Being able to pinpoint the right disc for a specific project can dictate the outcome's quality, efficiency, and overall success. Understanding the nuances and intricacies of different discs is crucial for achieving optimal results.
Factors to Consider
Material Being Worked On
When contemplating the material being worked on, one must delve into its composition, density, and hardness. These factors play a pivotal role in determining the type of disc needed for the task at hand. For instance, working on hardwoods versus softwoods requires distinct disc characteristics to ensure smooth and precise abrasion without causing damage. Each material poses a unique challenge that the suitable disc must address effectively. It is imperative to match the disc's abrasiveness and durability with the material's properties to achieve the desired outcome efficiently.
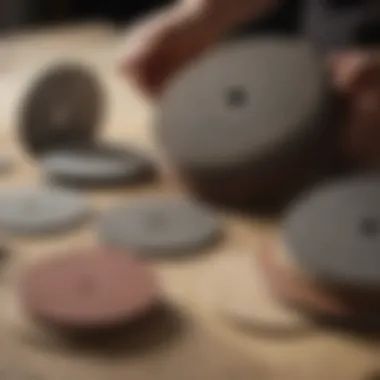
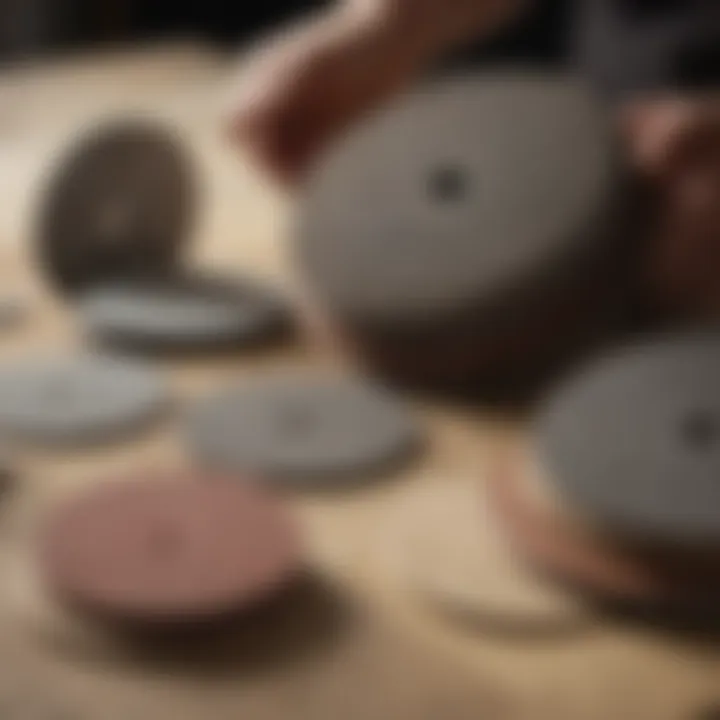
Desired Finish
The desired finish serves as a guiding principle in the disc selection process. Whether aiming for a smooth, polished surface or a coarser texture, the choice of disc impacts the final appearance of the workpiece. Different discs offer varying levels of abrasion intensity and precision, catering to specific finish requirements. Considering the finish early in the decision-making process enables the craftsman to align the disc's characteristics with the envisioned end result, thereby streamlining the grinding process and achieving the desired finish with finesse.
Duration of Use
The duration of use is a critical aspect to factor in when choosing the right disc. Some projects demand prolonged grinding sessions, necessitating discs that can withstand continuous usage without compromise. Durability, longevity, and heat resistance become paramount considerations for tasks that extend over extended periods. Selecting a disc capable of maintaining performance integrity throughout extended usage guarantees efficiency, cost-effectiveness, and consistent results over time.
Practical Tips
Testing on Scrap Material
Before embarking on the main project, it is advisable to conduct a test run on a similar piece of scrap material. Testing the chosen disc on a small sample allows for adjustments and fine-tuning before commencing the actual work. This preliminary trial offers insights into the disc's compatibility with the material, its abrasiveness, and the resulting finish, enabling the worker to refine their approach and optimize the grinding process.
Consulting with Experts
Seeking guidance from seasoned experts in the field can provide invaluable insights for selecting the right disc. Professionals with extensive experience can offer recommendations based on the project's requirements, material specifics, and desired outcomes. Their expertise can help navigate the vast array of disc options available, ensuring a well-informed decision that aligns with the project goals. Consulting with experts enhances the decision-making process, fostering confidence and precision in disc selection for optimal results.
Maintenance and Storage
Maintenance and storage play a crucial role in the effectiveness and longevity of sandpaper grinding discs. Proper care ensures these tools remain in optimal condition, offering consistent performance over time. By focusing on maintenance and storage, users can maximize the lifespan of their discs, saving time and resources in the long run.
Ensuring Longevity
Cleaning After Use
One essential aspect of maintenance is cleaning the sandpaper grinding discs after each use. This step removes any debris or residue, preventing build-up that could affect the disc's performance. Proper cleaning not only enhances the disc's efficiency but also prolongs its lifespan. Users should gently wipe the disc with a soft cloth or brush to ensure all particles are removed without damaging the abrasive surface. Regular cleaning is a practical habit that promotes consistent results and prevents premature wear.
Proper Storage
Proper storage is equally important in maintaining the quality of sandpaper grinding discs. Storing discs in a dry and humidity-controlled environment protects them from moisture damage and retains their abrasive properties. By keeping discs organized and away from potential contaminants, users safeguard their investment and extend the usability of each disc. Storing discs in a dedicated container or rack also prevents accidental damage and minimizes the risk of misplacement, ensuring easy access when needed. Adhering to recommended storage practices is key to preserving the discs' effectiveness and performance.
Conclusion
In wrapping up the exhaustive exploration of sandpaper grinding discs, it becomes strikingly evident that these tools are quintessential in various industrial and artisanal applications. The meticulous assessment of grit sizes, types of discs, factors in selection, and maintenance underscores their crucial role in achieving meticulous finishes and optimal surface preparations. Importantly, when analyzing the significance of the conclusion within this article, it is imperative to acknowledge the myriad benefits that accrue from a profound understanding of sandpaper grinding discs. The insightful tips, detailed guidance, and emphasis on continual learning equip both novices and seasoned craftsmen with the confidence and competence to navigate the diverse landscape of sanding techniques and disc selection efficiently.
Final Thoughts
Summary of Benefits
Delving into the nuances of the summary of benefits unveils a treasure trove of advantages that elevate the efficacy and precision of utilizing sandpaper grinding discs. The pivotal characteristic of the summary of benefits lies in its ability to swiftly expedite surface preparation and refinishing tasks with impeccable finesse. This feature seamlessly aligns with the core objectives outlined in our guide, emphasizing the paramount importance of achieving impeccable finishes and streamlined workflows. The unique selling point of the summary of benefits lies in its adaptability and versatility across an array of projects and materials, making it an unparalleled choice for individuals seeking optimal performance and reliability in their grinding disc endeavors.
Continual Learning
Within the realm of sanding methodologies and tool applications, continual learning stands out as a cornerstone of proficiency and innovation. The key characteristic of continual learning lies in its inherent ability to foster adaptability and skill refinement among craftsmen and enthusiasts alike. This facet resonates deeply with the overarching goals of our article, which prioritize not merely a static understanding of sanding techniques but a dynamic engagement with evolving best practices and emerging tool technologies. The distinctive feature of continual learning lies in its capacity to transcend conventional boundaries and propel users towards mastery and expertise in leveraging sandpaper grinding discs effectively. Embracing the ethos of continual learning ensures a constant evolution in technique, efficiency, and outcomes, cementing its pivotal role in maximizing the utility and impact of sanding endeavors.