Unlocking the Full Potential of Masonry Wheels for Angle Grinders
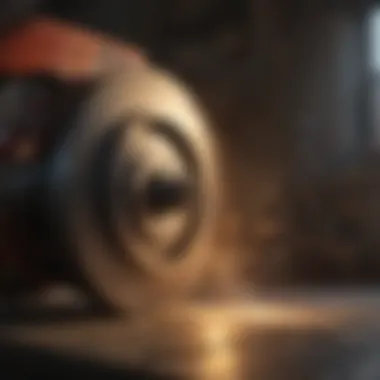
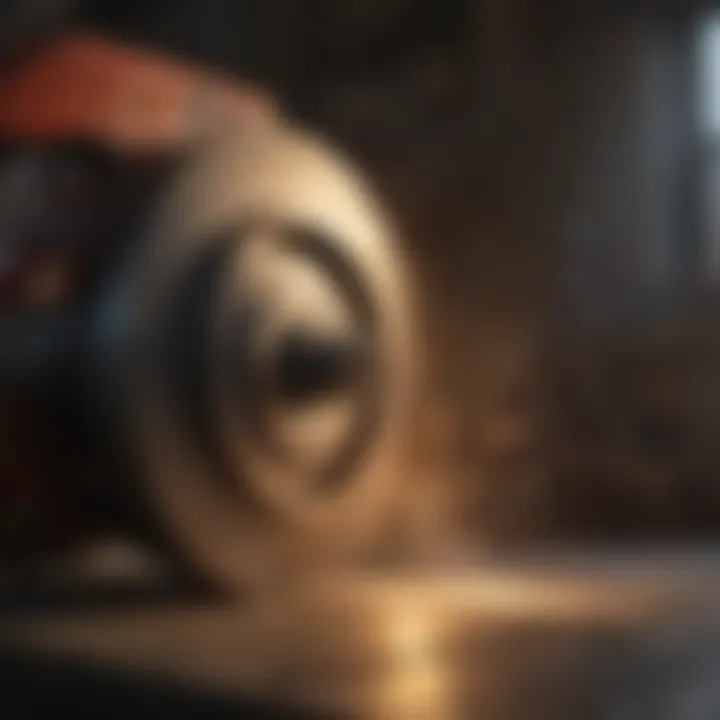
In the realm of the home improvement industry, the utilization of a masonry wheel for an angle grinder plays a pivotal role in various tasks, from cutting concrete blocks to shaping stones. This tool offers precision and efficiency, making it a valuable asset for DIY enthusiasts and professionals alike. The importance of understanding and maximizing the potential of a masonry wheel cannot be overstated, as it can significantly enhance the quality and speed of your projects.
Common Challenges and Solutions
Homeowners often encounter challenges when it comes to using a masonry wheel effectively. Some common issues include insufficient precision in cutting, uneven edges, and excessive wear and tear on the wheel. To tackle these challenges, it is crucial to ensure proper alignment of the wheel, use the appropriate pressure, and regularly inspect and maintain the wheel for optimal performance. Additionally, investing in high-quality masonry wheels can also eliminate many common issues faced by homeowners, providing smoother cutting and extended durability.
Product Recommendations
When it comes to choosing a masonry wheel for your angle grinder, [Industry Brand] offers a range of top-tier products known for their durability and precision. The [Product A] from [Industry Brand] is renowned for its superior cutting ability and long lifespan, making it a popular choice among professionals. Another notable product is [Product B], which excels in providing smooth and clean cuts on various materials. These recommended products not only enhance the performance of your angle grinder but also ensure safety and efficiency in your projects.
Step-by-Step Guides
To maximize the potential of your masonry wheel for an angle grinder, follow these practical steps:
- Planning: Assess your project requirements and select the appropriate masonry wheel for the task at hand.
- Preparation: Ensure your angle grinder is properly set up, with the masonry wheel securely attached.
- Execution: Cut or shape the material with steady, controlled movements, applying consistent pressure on the wheel.
- Maintenance: After use, clean the masonry wheel and store it in a dry, secure location to prevent damage.
These step-by-step instructions, combined with the right techniques and products, will empower you to harness the full potential of your masonry wheel for angle grinder, delivering precise results with ease.
Understanding Masonry Wheels
In this extensive guide on maximizing the potential of a masonry wheel for an angle grinder, understanding the intricacies of masonry wheels stands as a crucial foundation. By comprehending the composition and functionality of these wheels, users can optimize their performance and ensure safety measures are met.
Composition and Functionality
Materials Used in Masonry Wheels
Materials used in masonry wheels play a pivotal role in their overall performance. The type of material used, such as bonded abrasives, determines the wheelβs cutting or grinding capabilities. For example, silicon carbide and aluminum oxide are commonly utilized materials known for their durability and versatility in various applications. Understanding the specific characteristics of these materials aids users in selecting the most suitable wheel for their cutting or grinding tasks. However, these materials also come with their considerations, such as heat generation during prolonged use or potential brittleness under excessive pressure.
Role of Masonry Wheels in Cutting and Grinding
The role that masonry wheels play in cutting and grinding processes is indispensable. These wheels enable precise and efficient material removal, making them essential tools in construction and renovation projects. Their capacity to cut through hard materials like concrete or stone showcases their efficacy. Moreover, the abrasive nature of these wheels allows for fast and accurate grinding, contributing to the overall quality of the finished work. However, users must be cautious of potential kickback and vibrations that may occur, necessitating proper handling techniques for safety.
Types of Masonry Wheels
Diamond Blades
Diamond blades represent a premium choice for cutting tasks with exceptional precision and longevity. The synthetic diamonds embedded in the blade's edge provide unmatched hardness, allowing for smooth and clean cuts even on the hardest materials like granite or porcelain. Their ability to operate at high speeds without overheating makes them ideal for prolonged use, enhancing efficiency and productivity. However, the costlier nature of diamond blades may be a deterrent for some users.
Abrasive Blades
Abrasive blades offer versatility in grinding applications, catering to a broad range of materials with varying hardness. Their abrasive nature allows for rapid material removal, making them suitable for tasks that require smoothing or shaping surfaces. Additionally, the affordability of abrasive blades makes them a cost-effective choice for users seeking performance at a reasonable price point. Despite their efficiency, users should be mindful of wear and tear over time, as these blades may require more frequent replacements compared to diamond blades.
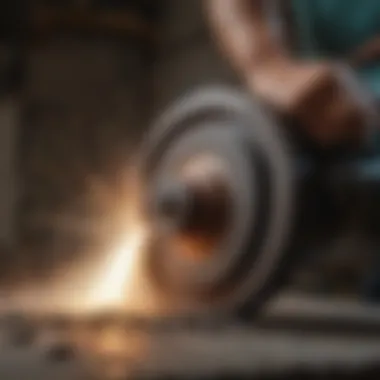
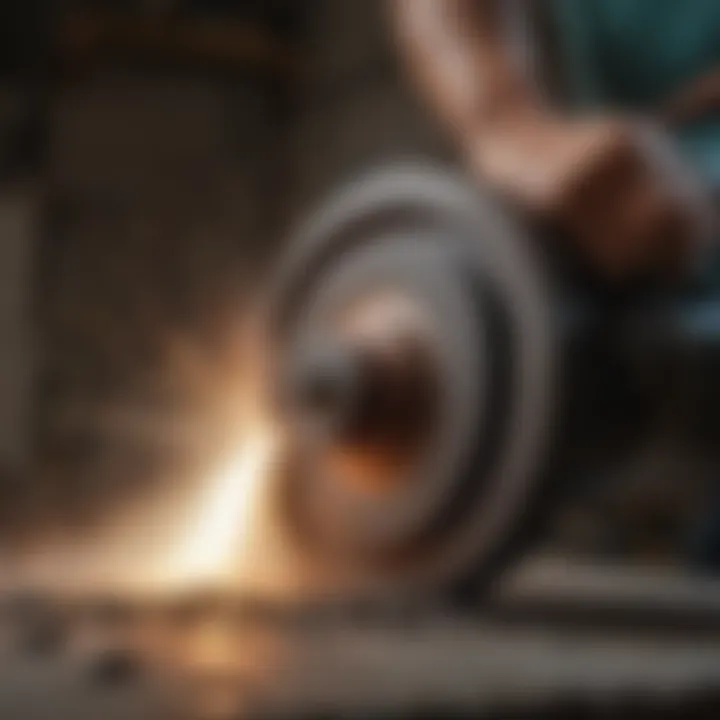
Choosing the Right Masonry Wheel
Considering Material to be Cut or Ground
When selecting a masonry wheel, it is imperative to consider the material to be cut or ground. Different materials may require specific wheel types to achieve optimal results. For instance, cutting through a dense material like brick may necessitate a diamond blade for precise and effortless cutting. Understanding the material's composition ensures that the chosen wheel can handle the task effectively, preventing damage to the wheel or compromising the quality of the cut.
Compatibility with Angle Grinder
Ensuring compatibility between the masonry wheel and the angle grinder is crucial for seamless operation. The wheel's size and mounting mechanism must align with the grinder to guarantee a secure fit and stable performance. Incompatibility between the wheel and grinder can lead to vibrations, slippage, or even accidents during use. Therefore, verifying compatibility before initiating any cutting or grinding tasks is essential for user safety and efficient operation.
Safety Features
Emphasizing safety features in masonry wheels is paramount to protect users from potential hazards. Wheels equipped with reinforced cores or enhanced bond systems offer increased durability and stability during operation, reducing the risk of breakage or machine malfunctions. Additionally, safety indicators or markings on the wheel provide visual cues for users to identify potential risks or damages, prompting necessary action. Prioritizing masonry wheels with adequate safety features enhances user confidence and overall work safety.
Proper Usage Techniques
Proper usage techniques are integral to maximizing the potential of a masonry wheel when using an angle grinder effectively. Attention to detail in how you operate the angle grinder can significantly impact both performance and safety. By thoroughly understanding and implementing proper techniques, users can ensure precise cuts, smoother grinding, and prolonged masonry wheel lifespan. In this section, we will delve into essential aspects such as safe operational practices, optimal speed, pressure settings, and correct cutting and grinding methods.
Safety Precautions
Wearing Personal Protective Equipment
Wearing personal protective equipment (PPE) is a crucial aspect of safety when using a masonry wheel with an angle grinder. Items such as safety glasses, gloves, and ear protection safeguard against potential hazards like flying debris and noise exposure. PPE not only reduces the risk of injuries but also promotes a secure working environment, instilling confidence in the user to operate the equipment efficiently and securely.
Securing Workpiece
Securing the workpiece firmly before initiating the cutting or grinding process is paramount for stability and precision. Using clamps or vices to hold the material in place prevents unexpected movement that can lead to accidents. A securely fixed workpiece ensures accurate cuts and reduces the likelihood of errors, enhancing overall operational efficiency.
Avoiding Kickback
Avoiding kickback is vital in maintaining control over the angle grinder and masonry wheel during operation. Kickback occurs when the wheel binds or stalls, causing it to kick back towards the user. By maintaining a firm grip on the grinder, using proper wheel rotational direction, and avoiding abrupt movements, users can minimize the risk of kickback incidents, ensuring smooth and safe operation.
Angle Grinder Settings
When it comes to angle grinder settings, understanding the optimal speed and pressure is key to achieving precise results with a masonry wheel. By fine-tuning these settings based on the material being worked on, users can optimize cutting and grinding efficiency while prolonging the life of the wheel.
Optimal Speed and Pressure
The optimal speed and pressure settings vary depending on the material and wheel type. Finding the right balance between speed and pressure is essential for achieving clean cuts and uniform grinding finishes. Adjusting the grinder to the ideal parameters not only enhances performance but also prevents overheating and premature wear of the wheel.
Proper Angle of Approach
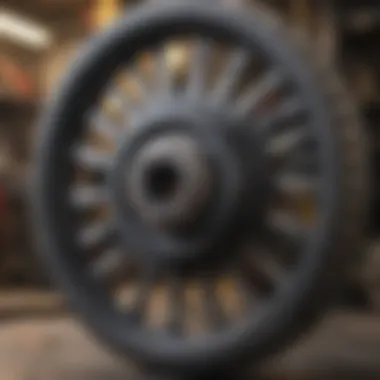
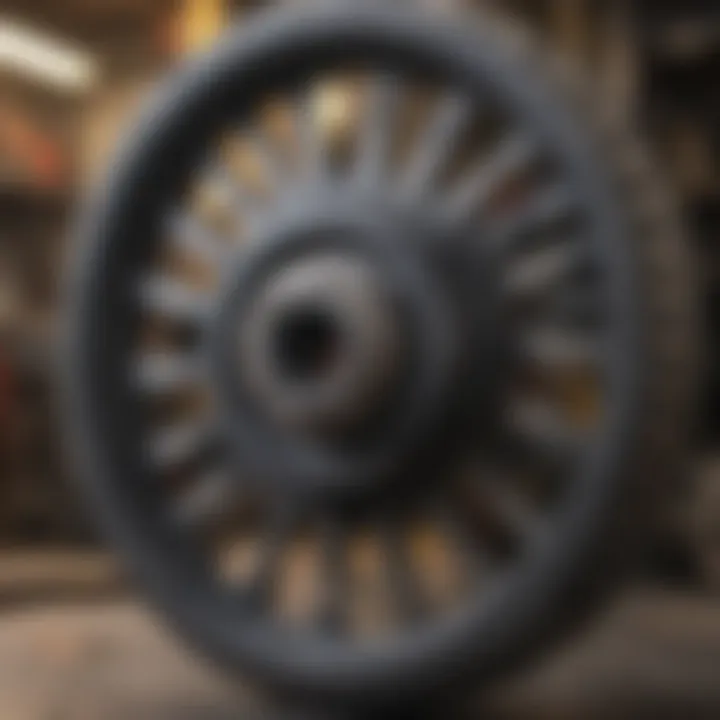
Maintaining the proper angle of approach while cutting or grinding plays a critical role in the quality of the end result. Whether making straight cuts or bevel cuts, positioning the grinder at the correct angle ensures precise and consistent outcomes. By following recommended angle guidelines, users can avoid errors, improve accuracy, and reduce material wastage.
Cutting and Grinding Techniques
Mastering cutting and grinding techniques is fundamental to maximizing the efficiency of a masonry wheel on an angle grinder. Different applications require specific approaches to achieve desired results, from straight cuts for basic shaping to intricate bevel cuts and various grinding applications.
Straight Cuts
Straight cuts are fundamental in various projects, demanding accuracy and control. Following a straight line with the grinder while exerting even pressure guarantees clean, uninterrupted cuts. This technique is indispensable for tasks requiring precise edges or divisions in the material.
Bevel Cuts
Bevel cuts involve creating angled edges on materials for purposes like joining corners or creating chamfers. Grinders equipped with masonry wheels can execute bevel cuts smoothly by adjusting the angle of the tool relative to the workpiece. Proper positioning and steady movement are key to achieving consistent and aesthetically pleasing bevels.
Grinding Applications
Grinding applications cover a broad spectrum of tasks, including smoothing surfaces, removing excess material, or sharpening edges. By selecting the appropriate grinding technique based on the material and desired finish, users can effectively reshape, refine, or polish various surfaces with precision and efficiency.
Maintenance and Care
When it comes to maximizing the potential of your masonry wheel for an angle grinder, the aspect of maintenance and care plays a crucial role in ensuring its longevity and performance. Proper maintenance not only extends the life of your masonry wheel but also enhances safety during operation. This section will delve into key elements of maintenance and care, providing comprehensive insights into keeping your tools sharp and efficient.
Cleaning After Use
Removing Debris and Residue:
In the realm of ensuring the longevity and optimal performance of your masonry wheel, the meticulous task of removing debris and residue after each use is paramount. By effectively eliminating these accumulations, you prevent potential damage to the wheel and maintain its cutting or grinding effectiveness. The key characteristic of this practice lies in its ability to preserve the integrity of the wheel's surface, thereby prolonging its usability. When conducting this task, be sure to utilize appropriate tools such as a cleaning brush to dislodge particles effectively. While this process may seem time-consuming, its advantages far outweigh the brief inconvenience, offering a clean slate for future tasks.
Ensuring Blade Sharpness:
Another vital aspect of maintenance involves ensuring the sharpness of your masonry wheel's blade. A sharp blade results in precise cuts or grinds, reducing the effort needed for tasks and enhancing overall output quality. The key characteristic of maintaining blade sharpness is the consistent honing and sharpening of the blade to prevent dullness, which can lead to inefficient performance and potential safety hazards. By prioritizing blade sharpness, you guarantee smoother operations and minimize the risk of accidents, making it a popular choice among professionals and DIY enthusiasts alike.
Storage Tips
In addition to post-use cleaning and maintenance, proper storage of your masonry wheel is imperative for its longevity and performance consistency. This section will explore optimal storage practices and precautions to safeguard your tool investment.
Proper Handling and Storing:
Efficient storage starts with proper handling and storing techniques for your masonry wheel. The key characteristic of this practice lies in providing a designated storage space that is clean, dry, and away from direct sunlight or excessive heat exposure. By implementing proper handling methods, such as lifting the wheel without stress on the blade or ensuring it remains flat during storage, you preserve its structural integrity and prevent potential warping or damage. This conscientious approach to storage ensures that your masonry wheel remains ready for action whenever the need arises.
Avoiding Moisture Exposure:
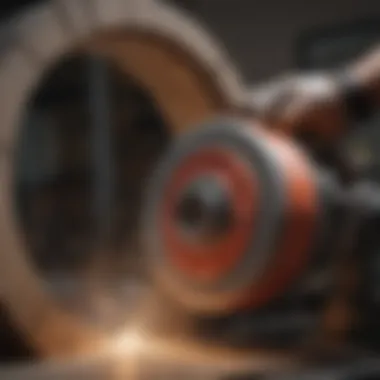
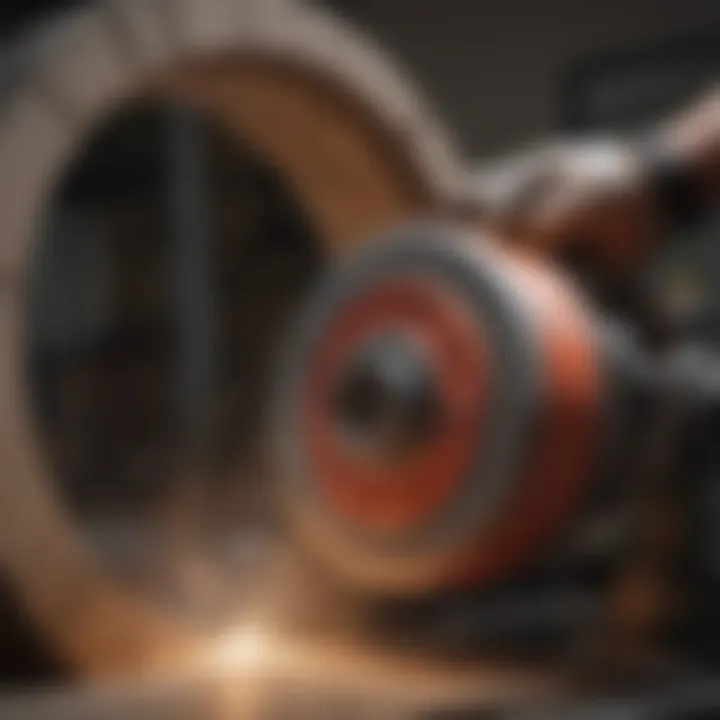
Moisture exposure stands as a common threat to the longevity of masonry wheels, causing rust and deterioration. By actively avoiding moisture exposure through storage in a dry environment and using protective coverings when not in use, you shield your wheel from corrosive elements that could compromise its performance. The key characteristic of this practice lies in the prevention of oxidation and the preservation of the wheel's surface qualities, ensuring that when it's time to use the wheel again, it functions at its best.
Replacing Masonry Wheels
As masonry wheels undergo wear and tear over time, knowing when and how to replace them becomes crucial for maintaining efficient operation and safety. This segment will provide detailed insights into recognizing signs for replacement and executing the removal and installation process meticulously.
Signs of Wear and Tear:
Identifying signs of wear and tear on your masonry wheel is essential for preemptive replacement, preventing potential accidents or diminished performance. The key characteristic of this practice lies in inspecting the wheel for cracks, chips, or uneven wear patterns, all of which indicate the need for a new wheel. By promptly recognizing these signs, you avoid compromised cutting and grinding quality, steering clear of potential hazards and ensuring uninterrupted workflow. Stay vigilant for any deviations in the wheel surface to maintain optimal operational standards.
Safe Removal and Installation:
When it comes time to replace your masonry wheel, executing the removal and installation process safely is paramount for both your equipment and personal well-being. The key characteristic of this practice involves carefully disassembling the grinder, following manufacturer guidelines for secure wheel removal, and replacing it with a new wheel with precision. By adopting safe removal and installation measures, you mitigate the risk of accidents or damage to your angle grinder, prolonging its usability and performance. This meticulous approach guarantees a seamless transition between wheels, allowing you to resume your projects with efficiency and reliability.
Advanced Tips for Efficiency
When delving into the world of masonry wheels for angle grinders, understanding advanced tips for efficiency becomes paramount. These tips elevate your craftsmanship and ensure precision in every cut or grind. From customizing masonry wheels to seeking professional guidance, efficiency tips offer a competitive edge in your projects. By focusing on maximizing the potential of each tool and technique, you can streamline your workflow and achieve superior results.
Customizing Masonry Wheels
Segmentation for Specific Applications
Segmentation for specific applications is a critical consideration in enhancing the functionality of masonry wheels. This process involves dividing the wheel into segments optimized for particular materials or tasks, such as concrete cutting or brick grinding. The key characteristic of segmentation lies in its adaptability, allowing users to tailor their masonry wheels for precise and efficient performance. By opting for segmented masonry wheels, individuals can boost cutting accuracy and minimize waste, making it a popular choice among professionals seeking precision and versatility in their projects.
Modifying Grit Levels
Modifying grit levels on masonry wheels contributes significantly to efficiency and effectiveness in cutting and grinding tasks. This customization empowers users to adjust the coarseness of the wheel surface based on the material being worked on, whether it's coarse concrete or delicate tile. The unique feature of modifying grit levels lies in its flexibility, allowing for seamless transitions between different materials without compromising performance. While advantages include enhanced control and smoother finishes, potential disadvantages may involve increased tool wear depending on the grit level chosen, highlighting the importance of selecting the right grit for the specific project at hand.
Professional Guidance
Consulting Experts for Complex Projects
Consulting experts for complex projects can provide invaluable insight and advice on utilizing masonry wheels to their full potential. Experts can offer specialized knowledge on selecting the right wheel for intricate tasks, maximising efficiency, and ensuring safety in challenging scenarios. The key characteristic of expert consultation lies in their experience and proficiency, guiding users towards optimal solutions for their project requirements. By leveraging expert advice, individuals can overcome obstacles, troubleshoot issues efficiently, and elevate the quality of their work.
Training on Advanced Techniques
Training on advanced techniques offers a structured approach to enhancing mastery in using masonry wheels with angle grinders. This training equips individuals with in-depth knowledge on cutting-edge procedures, safety protocols, and efficiency strategies. The key characteristic of advanced technique training is its focus on honing skills and expanding capabilities, empowering users to tackle complex projects with confidence and precision. While advantages include improved efficiency and enhanced competence, potential disadvantages may involve initial time investment and adjustment to new methodologies, underscoring the importance of continuous learning and development.
Innovative Applications
Exploring New Materials for Cutting
Exploring new materials for cutting with masonry wheels opens up possibilities for creative and functional applications. By experimenting with unconventional materials like composites or alloys, individuals can push the boundaries of traditional cutting and create unique designs. The key characteristic of exploring new materials lies in its innovation potential, sparking creativity and inspiring novel solutions in various projects. While advantages include diversification of skills and exposure to emerging trends, potential disadvantages may involve initial experimentation challenges and material adaptation complexities, emphasizing the need for thorough research and testing.
Artistic Uses of Angle Grinders with Masonry Wheels
Artistic uses of angle grinders with masonry wheels showcase the artistic flair and decorative capabilities of these tools. From sculpting intricate patterns in stone to crafting bespoke metalwork, the marriage of angle grinders and masonry wheels unlocks a realm of artistic expressions. The unique feature of artistic applications lies in blending utility with aesthetics, transforming mundane materials into works of art. While advantages include creative fulfillment and personalized creations, potential disadvantages may involve technical precision requirements and fine detail work challenges, highlighting the importance of patience and skill refinement.