Unlocking the Art of Optimal Grinding Wheel Selection for Plastic Materials
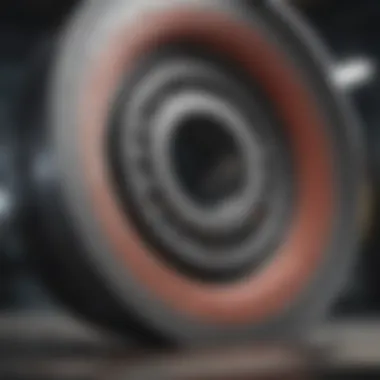
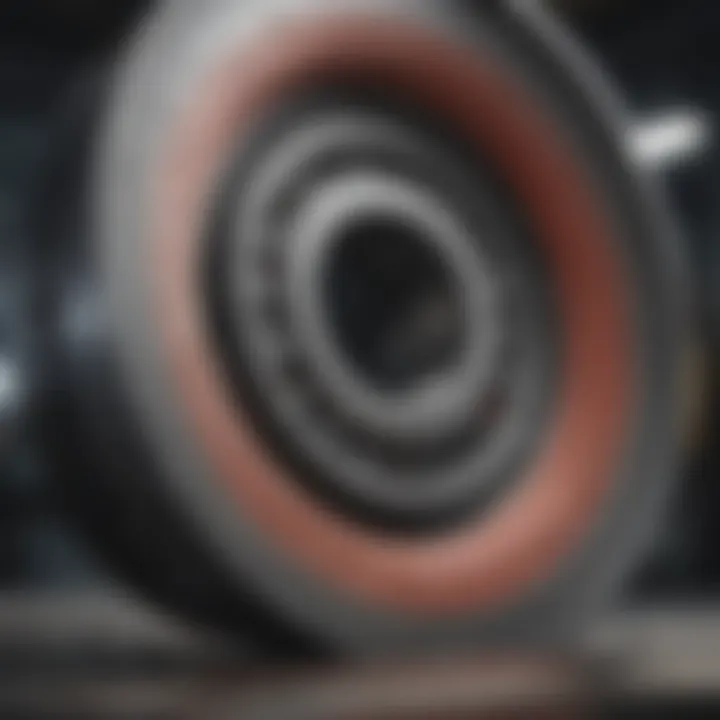
Overview of Topic
In the realm of home improvement, the selection of grinding wheels tailored for plastic materials is a critical aspect that impacts the efficiency and quality of the grinding process. The choice of grinding wheel can significantly influence the outcome of the task, making it essential for homeowners to grasp the nuances of this selection process.
Common Challenges and Solutions
Homeowners often face common challenges when selecting grinding wheels for plastic materials. Issues such as compatibility with specific materials, durability, and achieving the desired finish can pose obstacles in the grinding process. To overcome these challenges, it is crucial for homeowners to conduct thorough research, seek expert advice, and test various grinding wheels to find the most suitable option for their unique requirements.
Solutions lie in exploring a diverse range of grinding wheel options, considering factors like abrasiveness, wheel bond, and grit size to achieve optimal results. Additionally, regular maintenance and proper storage of grinding wheels can extend their lifespan and performance, contributing to a smoother grinding experience.
Product Recommendations
Delving into the market of grinding wheels for plastic materials, top industry brands offer a myriad of products designed to cater to specific needs. Brands like [Industry Brand] provide a range of grinding wheels known for their durability, precision, and versatility.
Recommended products from [Industry Brand] often feature innovative designs, superior abrasives, and efficient cooling mechanisms to enhance performance and deliver consistent results. Homeowners can benefit from these products by selecting the most suitable option based on their project requirements and desired outcomes.
Step-by-Step Guides
To optimize the selection of grinding wheels for plastic materials, homeowners can follow a structured approach that includes various steps to streamline the process. Beginning with researching the specific properties of the plastic material being worked on, homeowners can then proceed to assess their grinding requirements and select a compatible grinding wheel.
Detailed instructions such as proper mounting of the grinding wheel, adjusting speed settings, and monitoring the grinding process are essential to ensure efficiency and safety. By adhering to these step-by-step guides, homeowners can maximize the effectiveness of their grinding tasks and enjoy superior outcomes with precision and finesse.
Introduction
The significance of this topic lies in its ability to bridge the gap between mediocre outcomes and exceptional results in plastic machining. By delving into the selection process of grinding wheels, we unravel the inner workings of enhancing productivity, precision, and surface finish. Each facet of the grinding wheel spectrum plays a crucial role in shaping the final output, making it imperative to grasp the nuances of selection.
As we traverse through this article, key considerations, properties, and practical tips come together harmoniously to form a comprehensive roadmap for optimizing your grinding wheel selection journey. Whether you're a seasoned veteran in plastic processing or a novice looking to delve into the intricacies of grinding, this article promises to enlighten and empower your decision-making process. So, buckle up as we embark on a knowledge-rich expedition, unearthing the treasures of selecting the perfect grinding wheel for plastic materials.
Understanding Plastic Grinding
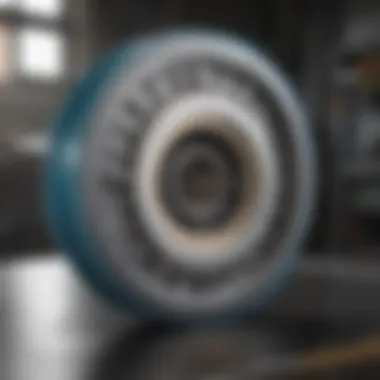
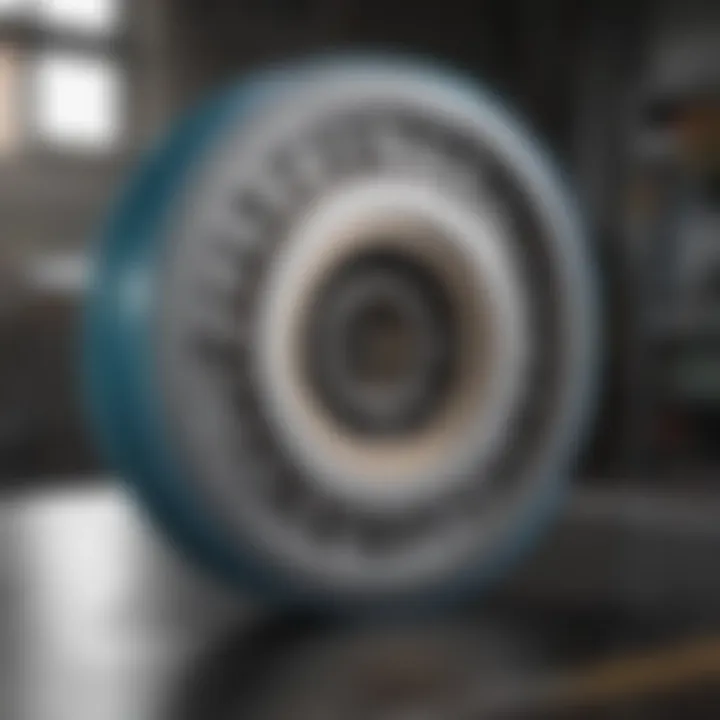
Understanding the nuances of plastic grinding is paramount when aiming for optimal results in processing plastic materials. Plastics possess distinct characteristics that set them apart from traditional materials, necessitating a specialized approach to grinding. By delving into the specifics of plastic grinding, manufacturers can enhance productivity and precision in their operations. This section will elucidate the various elements that make understanding plastic grinding essential for successful material processing.
Characteristics of Plastic Materials
Thermal Sensitivity
Plastic materials exhibit varying degrees of thermal sensitivity, which impacts their suitability for different manufacturing processes. Thermal sensitivity refers to how reactive a material is to changes in temperature during grinding. This property is crucial as it influences the choice of grinding wheel and the overall efficiency of the grinding process. Selecting the appropriate wheel that complements the thermal sensitivity of the plastic material is key to achieving precise and consistent results.
Abrasion Resistance
Another critical aspect of plastic materials is their abrasion resistance, which determines their durability and wear characteristics during grinding. Abrasion resistance measures the ability of a material to withstand friction and contact during the grinding process without deteriorating. Understanding the abrasion resistance of the plastic material allows operators to choose the right grinding wheel that can withstand the required level of abrasion, ensuring longevity and high-quality results.
Importance of Grinding in Plastic Processing
Dimensional Accuracy
Achieving dimensional accuracy is crucial in plastic processing as it directly impacts the final product's quality and functionality. Dimensional accuracy refers to the precision with which parts are manufactured, influencing their fit and performance. By selecting the appropriate grinding wheel that aligns with the dimensional accuracy requirements of the plastic material, manufacturers can ensure consistent results and meet stringent production standards.
Surface Finish
The surface finish of plastic components plays a significant role in their aesthetics and functionality. A smooth and high-quality surface finish is desirable in plastic processing as it enhances the overall appearance and performance of the end product. Grinding wheels with specific attributes tailored to achieving the desired surface finish can help manufacturers elevate the quality of their plastic components, making them more visually appealing and functional.
Choosing the Right Grinding Wheel
Abrasive Material Selection
Diamond Wheel
When delving into the realm of abrasive material selection, the Diamond Wheel emerges as a standout choice for effectively grinding plastic materials in this context. The key characteristic that sets the Diamond Wheel apart is its exceptional hardness and durability, making it an invaluable asset for achieving precision and accuracy in the grinding process. The Diamond Wheel's unique feature lies in its ability to maintain sharpness over prolonged usage, resulting in consistent and reliable performance. While the Diamond Wheel boasts remarkable advantages in terms of efficiency and longevity, it is crucial to be mindful of potential drawbacks such as higher initial costs compared to other options.
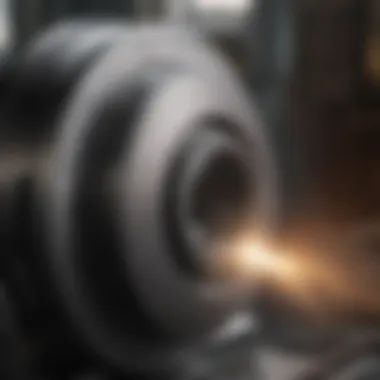
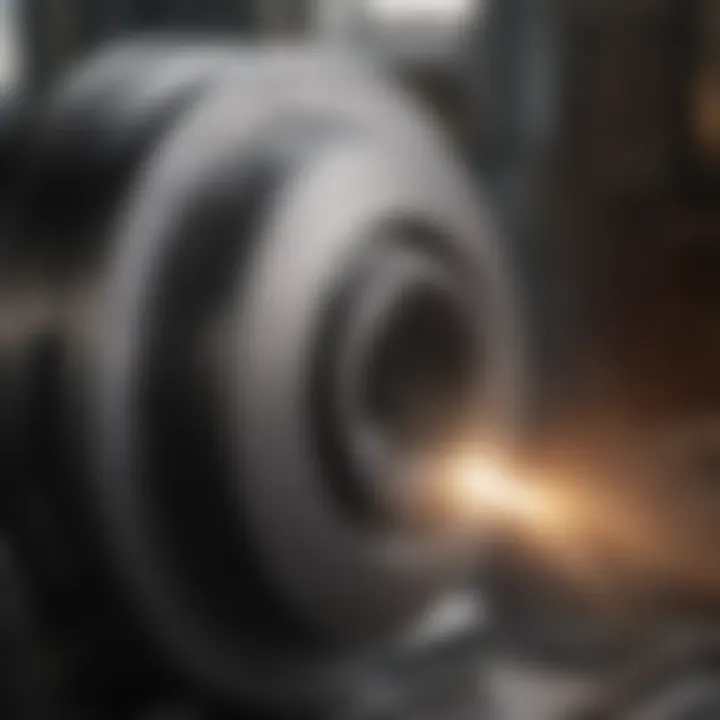
Silicon Carbide Wheel
Another prominent player in the realm of abrasive material selection is the Silicon Carbide Wheel. Renowned for its versatility and strength, the Silicon Carbide Wheel brings a different set of advantages to the table. With a focus on efficient material removal and sturdy abrasive properties, this type of wheel is well-suited for tackling a variety of plastic materials with varying hardness levels. The key characteristic that makes the Silicon Carbide Wheel a popular choice in this scenario is its ability to maintain sharpness even under high heat conditions, ensuring consistent grinding performance. While the Silicon Carbide Wheel offers various benefits, it is essential to also consider certain limitations such as potential brittleness under extreme pressure.
Determining Grit Size
Coarse Grits
Fine Grits
Conversely, Fine Grits present themselves as indispensable components in the spectrum of grit size determination. Known for their fine abrasive qualities and ability to deliver smooth surface finishes, Fine Grits are ideal for refining and polishing workpieces with precision and detail. The key characteristic that distinguishes Fine Grits is their capacity to achieve intricate surface textures and superior dimensional accuracy during the grinding process. Although Fine Grits excel in providing immaculate finishes and fine detail work, it is essential to note their slower material removal rate compared to Coarse Grits, necessitating careful consideration for optimal grinding outcomes.
Managing Heat Generation
Coolant Usage
Benefits of Coolant
When it comes to the benefits of coolant in the grinding process, its ability to dissipate heat effectively is paramount. Coolant plays a crucial role in reducing the temperature of the workpiece and grinding wheel, preventing overheating and potential damage to the plastic material. Additionally, coolant helps in improving lubrication, reducing friction, and enhancing chip evacuation, thereby prolonging the lifespan of the grinding wheel and ensuring consistent performance throughout the grinding operation.
Types of Coolants
Exploring the types of coolants available for plastic grinding reveals a range of choices tailored to specific requirements. Water-based coolants are popular for their cost-effectiveness and environmental friendliness. Synthetic coolants offer excellent cooling properties and oxidation resistance, ideal for high-speed grinding applications. Oil-based coolants provide superior lubrication and cooling for heavy-duty grinding tasks. Each type of coolant has its unique features and advantages, catering to diverse grinding needs and ensuring the optimal management of heat during the grinding process.
Avoiding Overheating
As overheating can detrimentally impact the grinding process, employing strategies to avoid this issue is vital for achieving desirable results in plastic material grinding operations.
Monitoring Temperature
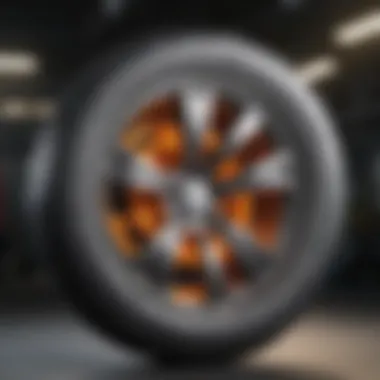
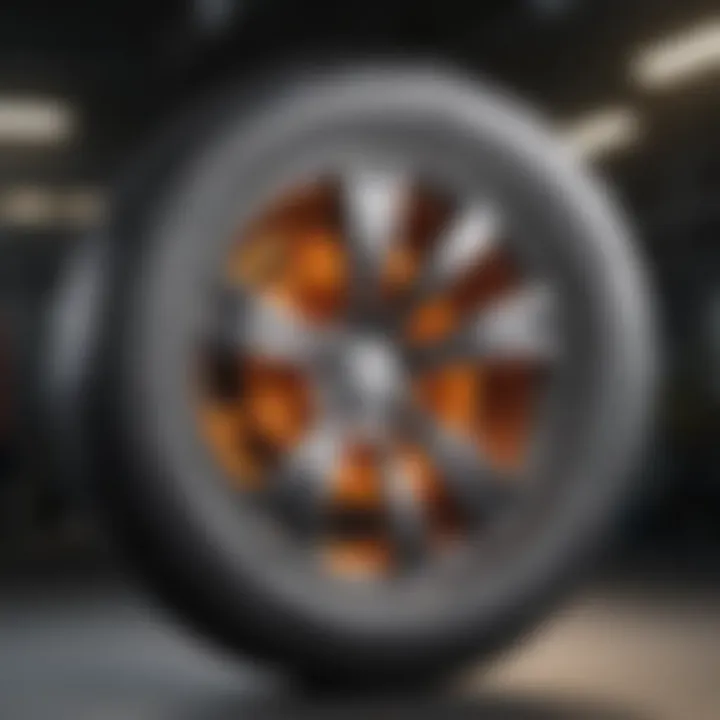
The implementation of temperature monitoring systems facilitates real-time tracking of the heat generated during grinding. By closely monitoring temperature fluctuations, operators can adjust grinding parameters to maintain an optimal heat level, preventing thermal damage to the workpiece. This proactive approach not only enhances the quality of the ground material but also prolongs the lifespan of the grinding wheel, contributing to overall process efficiency.
Workpiece Cooling
Integrating workpiece cooling mechanisms is essential for dissipating heat and maintaining stable operating temperatures during grinding. Workpiece cooling techniques, such as air blast cooling or coolant flood systems, help regulate the temperature of the workpiece, preventing thermal deformation and ensuring dimensional accuracy. Effective workpiece cooling not only improves the grinding process but also preserves the integrity of the plastic material, resulting in superior surface finish and enhanced productivity.
Practical Grinding Tips
Workpiece Preparation
Cleaning Surface
The first crucial aspect of Workpiece Preparation is Cleaning Surface. The cleanliness of the workpiece surface plays a pivotal role in the grinding process. A clean surface ensures better contact between the workpiece and the grinding wheel, leading to improved grinding accuracy and surface finish. The key characteristic of Cleaning Surface lies in its ability to remove impurities, contaminants, and residues that may hinder the grinding operation. This meticulous cleaning process is a popular choice in the context of this article as it guarantees optimal grinding outcomes. The unique feature of Cleaning Surface is its capability to eliminate debris and ensure a smooth, uniform contact surface, ultimately resulting in enhanced precision and quality in the grinding operation.
Securing Workpiece
Another vital aspect of Workpiece Preparation is Securing Workpiece. Properly securing the workpiece is essential to prevent vibrations, displacement, or distortion during the grinding process. Securing Workpiece ensures stability and precision, enabling consistent and accurate grinding results. The key characteristic of Securing Workpiece lies in its ability to hold the workpiece firmly in place, minimizing the risk of errors or defects in the grinding process. This method is a beneficial choice for this article as it guarantees reliability and repeatability in the grinding operation. The unique feature of Securing Workpiece is its capacity to provide a stable workpiece foundation, contributing to improved control and efficiency while grinding.
Optimizing Feed Rates
Uniform Cutting Pressure
Delving deeper into the optimization of feed rates, Uniform Cutting Pressure emerges as a critical factor in the grinding process. Maintaining uniform cutting pressure across the workpiece surface is essential for achieving consistent material removal and surface finish. The key characteristic of Uniform Cutting Pressure is its ability to distribute the grinding forces evenly, preventing uneven wearing of the grinding wheel and ensuring precise material removal. This feature is a popular choice in this article as it guarantees uniform grinding results and prolongs the lifespan of the grinding wheel. The unique aspect of Uniform Cutting Pressure lies in its capacity to control the cutting intensity, leading to improved efficiency and quality in the grinding operation.
Consistent Feed Rate
Equally important in the realm of optimizing feed rates is Consistent Feed Rate. Maintaining a steady and consistent feed rate during the grinding process is crucial for achieving uniform material removal and surface quality. The key characteristic of Consistent Feed Rate is its ability to regulate the speed at which the workpiece advances towards the grinding wheel, ensuring a uniform material removal rate. This approach is a beneficial choice for this article as it guarantees stable and predictable grinding outcomes. The unique feature of Consistent Feed Rate is its capability to prevent material overloading or underutilization, leading to optimized grinding efficiency and quality.
Conclusion
The significance of the [Conclusion] section lies in its ability to distill the key takeaways for the readers, emphasizing the critical factors to consider when selecting a grinding wheel for plastic materials. It serves as a compass that guides us towards making informed decisions that directly impact the efficiency and quality of the grinding operation.
One of the primary benefits of delving into the [Conclusion] section is gaining a holistic perspective on the interplay between abrasive material selection, grit size determination, bonding agent consideration, heat management strategies, and practical grinding tips. By encapsulating these elements into a coherent summary, the [Conclusion] ensures that readers leave with a comprehensive understanding of how to optimize grinding wheel selection for plastic materials.
Moreover, the [Conclusion] section underscores the importance of meticulous planning and execution in the grinding process to achieve optimal results. It highlights the need for careful consideration of each step, from initial planning to enjoying the final outcome, illustrating that success in plastic grinding is a result of thoughtful deliberation and precise implementation.
In essence, the [Conclusion] section serves as the ultimate guidepost that illuminates the path towards effective grinding wheel selection for plastic materials, empowering readers with the knowledge and insights necessary to enhance their plastic processing operations with efficiency and precision.