Unveiling the Mastery of Forney Grinding Wheels: An In-Depth Analysis
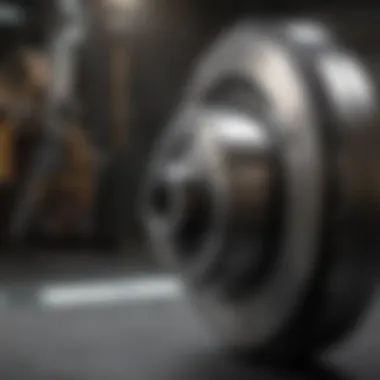
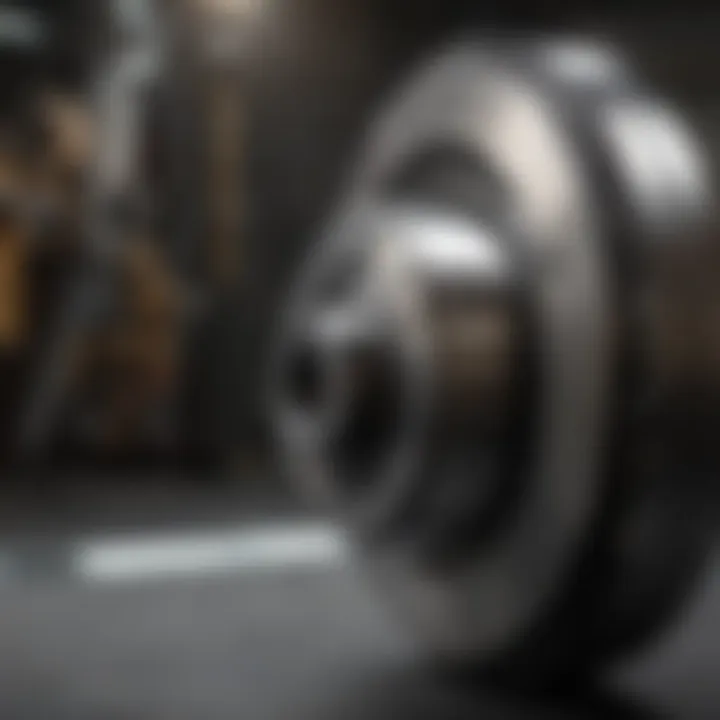
Overview of Forney Grinding Wheels
In the realm of home improvement, Forney grinding wheels stand out as indispensable tools for various tasks. These wheels, meticulously designed for efficiency and precision, play a pivotal role in enhancing the quality of work in different industries. Understanding the nuances of Forney grinding wheels is crucial for professionals and enthusiasts who seek unmatched performance.
Importance of Forney Grinding Wheels
The significance of Forney grinding wheels cannot be overstated. These tools enable users to achieve smooth and accurate finishes on different surfaces, ranging from metals to concrete. Their versatility and durability make them a preferred choice for tasks requiring meticulous attention to detail and superior results.
Common Challenges and Solutions
Challenges Faced by Homeowners
Homeowners often encounter challenges when using Forney grinding wheels, such as selecting the right wheel for specific applications, maintaining optimal performance, and ensuring safety during operation. These challenges can hamper project progress and quality if not addressed effectively.
Solutions for Overcoming Challenges
To overcome these challenges, homeowners should conduct thorough research to understand the various types of Forney grinding wheels available and their respective applications. Proper maintenance practices, including regular inspection for wear and tear, are essential to optimize performance and longevity. Additionally, following safety guidelines and using protective gear can prevent accidents and injuries, ensuring a smooth workflow.
Product Recommendations
Top Forney Grinding Wheel Products
When exploring the market for Forney grinding wheels, consider top products from renowned brands like Forney Industries. These products are crafted with precision engineering to deliver exceptional results and durability, meeting the diverse needs of users across industries.
Benefits and Features
The recommended Forney grinding wheels boast superior abrasion resistance, ensuring longevity and consistent performance. Their ergonomic designs allow for comfortable handling, reducing user fatigue during prolonged use. Additionally, advanced features like reinforced bonds and innovative grit compositions enhance cutting efficiency and deliver pristine finishes.
Step-by-Step Guides
Implementing Improvements with Forney Grinding Wheels
For homeowners looking to enhance their projects with Forney grinding wheels, follow these practical steps for optimal results. Begin by selecting the appropriate wheel for the task at hand, considering factors like material type and desired finish. Ensure proper installation and alignment of the wheel on the grinding machine, following manufacturer guidelines for secure attachment.
Maintain the wheel's condition by regularly cleaning and inspecting for any damage or wear. Utilize recommended accessories, such as wheel dressers or balancing tools, to enhance performance and extend the wheel's lifespan. Finally, adhere to safety protocols at all times, wearing protective equipment and operating the grinder with care to prevent accidents. By following these steps diligently, homeowners can elevate their projects with precision and efficiency using Forney grinding wheels.
Introduction
Grinding wheels play a critical role in various industries, serving as essential tools for shaping, finishing, and polishing materials with precision and efficiency. In this detailed exploration of Forney grinding wheels, we unravel the intricate components and diverse functionalities of these indispensable tools. Understanding the composition, types, applications, and maintenance of Forney grinding wheels is pivotal for professionals and enthusiasts seeking to enhance their machining processes and achieve superior results. By delving into the inner workings of Forney grinding wheels, we aim to equip readers with comprehensive insights into the intricate world of abrasive tools. Let's embark on this enlightening journey to uncover the nuances and practicalities of Forney grinding wheels, shedding light on their significance in modern industrial applications.
Grinding wheels, commonly known as abrasive wheels, present a versatile solution for tasks ranging from precision grinding to deburring and from metal fabrication to woodworking. Whether utilized in the automotive industry for polishing or woodworking to sharpen tools, Forney grinding wheels exhibit a diverse range of capabilities tailored to meet specific requirements. The inherent properties and characteristics of Forney grinding wheels, including hardness, grit size, and structure, significantly impact their performance in various applications, making them indispensable assets for professionals committed to achieving exceptional results. As we navigate through the intricacies of Forney grinding wheels, we uncover the fundamental aspects that underpin their functionality and discern the nuanced considerations that inform their selection and maintenance.
Understanding Grinding Wheels
Grinding wheels play a crucial role in various industries due to their ability to shape, polish, and cut materials. Understanding the composition, types, and properties of grinding wheels is essential for professionals and enthusiasts alike, as it directly impacts the efficiency and quality of grinding operations.
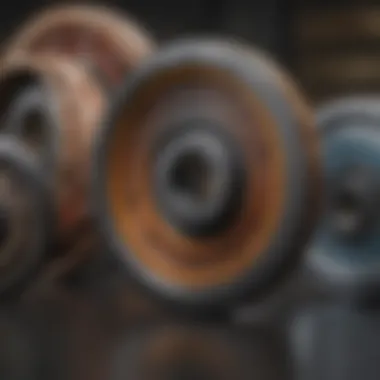
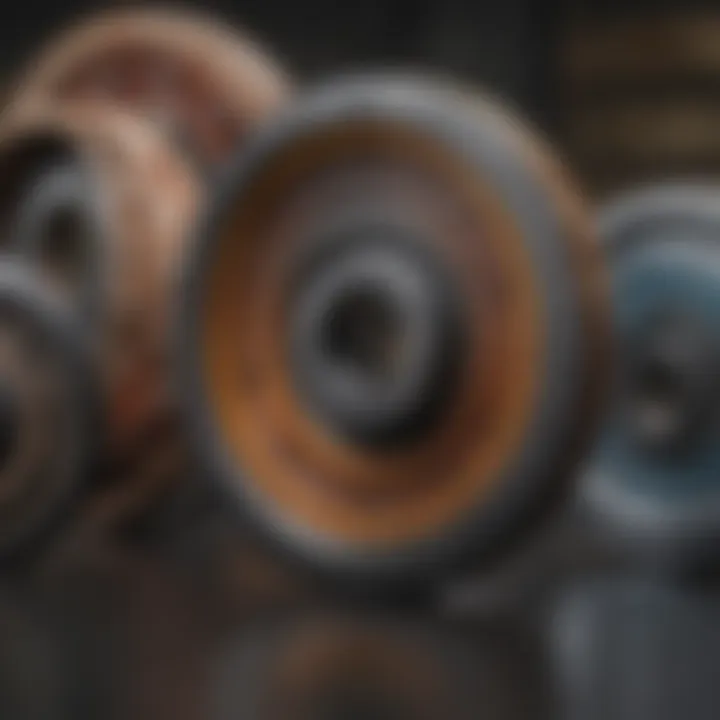
Composition of Forney Grinding Wheels
Abrasive Materials
Abrasive materials are the key components of Forney grinding wheels, responsible for the cutting and grinding action. These materials, such as aluminum oxide or silicon carbide, exhibit high hardness and toughness, making them ideal for shaping hard materials like metal or stone. The choice of abrasive material depends on the application and desired finish, with each type offering unique advantages in terms of durability and precision.
Bonding Agents
Bonding agents hold abrasive particles together and secure them to the wheel structure. The bonding agent's role is crucial in determining the wheel's hardness, porosity, and strength. Resin, vitrified, or metal bonds are commonly used, each offering specific advantages like heat resistance, wear resistance, or ease of dressing. Selecting the right bonding agent is essential to ensure optimal performance and longevity of Forney grinding wheels.
Reinforcement
Reinforcements, such as fiberglass or cloth, provide additional strength and stability to Forney grinding wheels, reducing the risk of breakage during operation. These reinforcements help in maintaining the wheel's shape and integrity under high-speed grinding conditions, enhancing safety and performance. Proper reinforcement ensures consistent and precise grinding results, making Forney grinding wheels reliable tools for various applications.
Types of Forney Grinding Wheels
Straight Wheels
Straight wheels are among the most common grinding wheel types, featuring a flat surface for surface grinding and cylindrical grinding tasks. Their straightforward design allows for precise and efficient material removal, making them suitable for a wide range of applications. Straight wheels are popular for their versatility and ease of use in shaping and sharpening tasks.
Cylinder Wheels
Cylinder wheels have a large diameter with a flat surface, ideal for grinding flat stock or cylindrical materials. These wheels excel in heavy-duty grinding operations, providing aggressive material removal and efficient surface finishing. Cylinder wheels are favored for their durability and effectiveness in stock removal tasks.
Tapered Wheels
Tapered wheels feature a conical shape, allowing for intricate grinding and profiling tasks. The tapered design offers enhanced accessibility to tight spaces and intricate shapes, making them ideal for precision grinding applications. Tapered wheels offer superior control and finesse in shaping and smoothing tasks, making them a valuable tool for detailed work.
Saucer Wheels
Saucer wheels have a slightly concave design, providing a wide grinding surface for contoured or curved materials. These wheels are well-suited for grinding curved components or creating precise bevels and angles. The saucer wheel's unique shape facilitates smooth material removal and precise shaping, making it a versatile and efficient choice for various grinding tasks.
Properties and Characteristics
Hardness
The hardness of a grinding wheel determines its resilience and ability to maintain shape under pressure. Harder wheels are ideal for heavy-duty applications requiring aggressive material removal, while softer wheels are suitable for finer finishing or profiling tasks. Understanding the hardness of Forney grinding wheels is essential for selecting the right wheel for specific grinding requirements.
Grit Size
Grit size refers to the abrasive particle size on the wheel surface, influencing the cutting performance and surface finish. Coarser grit sizes are effective for rapid material removal, while finer grit sizes offer smoother finishes with higher precision. Choosing the appropriate grit size based on the material and application is crucial for achieving desired grinding results.
Structure
The structure of a grinding wheel relates to the spacing and arrangement of abrasive particles within the wheel matrix. Open structures allow for cooler grinding and reduced loading, while dense structures provide aggressive cutting action. Understanding the structure of Forney grinding wheels helps in selecting the most suitable wheel for specific tasks, ensuring efficient and effective grinding operations.
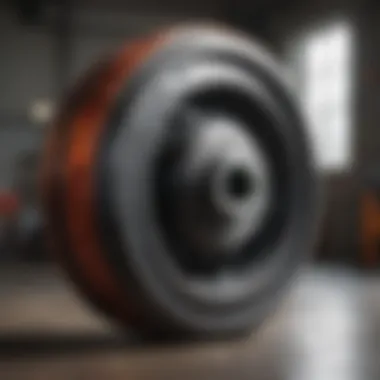
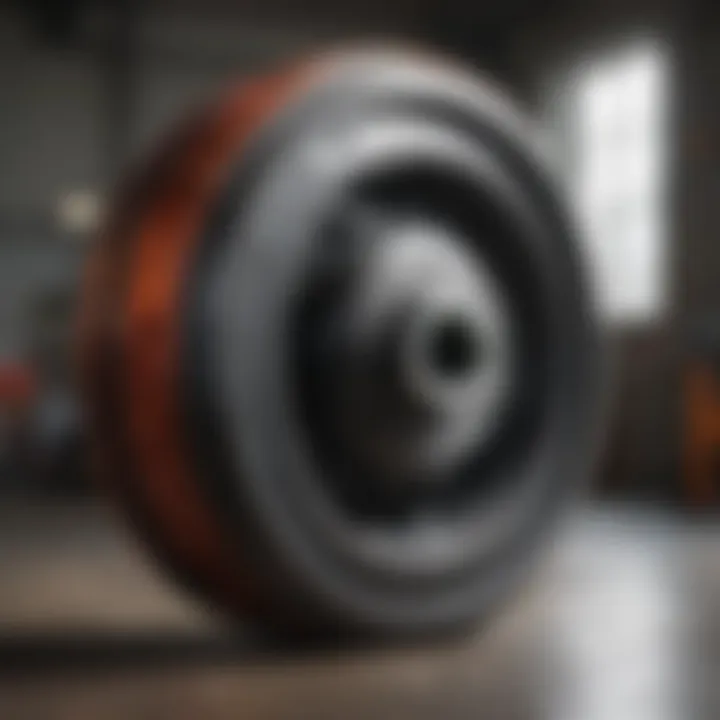
Applications of Forney Grinding Wheels
In delving into the applications of Forney grinding wheels, we uncover the pivotal role they play in various industries. These grinding wheels are essential tools in metal fabrication, woodworking, and the automotive industry, offering precise solutions for a multitude of tasks. The versatility of Forney grinding wheels allows professionals and enthusiasts to achieve precision grinding, deburring tasks, and surface grinding with ease and efficiency. By understanding the applications of Forney grinding wheels, individuals can optimize their work processes and enhance the quality of their outputs.
Metal Fabrication
Precision Grinding
Delving into the realm of precision grinding unveils its critical role in achieving fine and accurate results in metal fabrication. Precision grinding involves the meticulous removal of material from workpieces to attain the desired dimensions and surface finish. This method stands out for its ability to produce intricate shapes and precise measurements, making it a preferred choice for applications requiring high levels of accuracy. The unique feature of precision grinding lies in its ability to deliver exceptional surface quality and tight tolerances, contributing significantly to the overall success of metal fabrication processes.
Deburring
Considering the aspect of deburring sheds light on the importance of removing sharp edges and burrs from workpieces in metal fabrication. Deburring plays a crucial role in enhancing the safety and functionality of metal components by creating smooth and polished surfaces. Its key characteristic lies in its ability to refine edges and eliminate imperfections, making it a popular choice for achieving clean and flaw-free workpieces. While deburring offers the advantage of promoting a safer working environment and improving the aesthetics of finished products, it may require additional time and attention to detail in metal fabrication settings.
Surface Grinding
Exploring the realm of surface grinding reveals its significance in creating flat and smooth surfaces on metallic workpieces. Surface grinding involves the use of abrasive wheels to remove material and refine the surface texture of components, resulting in precise and uniform finishes. The key characteristic of surface grinding is its ability to improve the flatness and parallelism of workpieces, making it an efficient choice for achieving tight dimensional tolerances. The unique feature of surface grinding lies in its versatility and capability to produce high-quality surfaces with excellent accuracy, enhancing the overall quality of metal fabrication outputs.
Woodworking
Sharpening Tools
Analyzing the aspect of sharpening tools unveils its pivotal role in maintaining the sharpness and precision of woodworking instruments. Sharpening tools involve the use of abrasive materials to hone the edges of cutting implements, ensuring optimal performance and longevity. The key characteristic of sharpening tools is their ability to restore the sharp edge of woodworking tools, making them a popular choice for woodworkers seeking to enhance cutting precision. While sharpening tools offer the advantage of prolonging the lifespan of woodworking equipment and improving cutting efficiency, they may require expertise and attention to detail to achieve optimal results.
Finishing
Evaluating the concept of finishing unveils its importance in enhancing the visual appeal and surface quality of woodworking projects. Finishing involves the application of protective coatings or polishing materials to wood surfaces to improve their aesthetics and durability. The key characteristic of finishing lies in its ability to create smooth and lustrous surfaces, making it a beneficial choice for achieving professional-quality woodworking outputs. The unique feature of finishing is its versatility in adding depth and richness to wood surfaces, elevating the overall appearance of woodworking creations.
Automotive Industry
Polishing
Exploring the realm of polishing reveals its critical role in achieving glossy and reflective surfaces on automotive components. Polishing involves the use of abrasive materials and compounds to remove imperfections and create a smooth finish on vehicle parts. The key characteristic of polishing is its ability to enhance the visual appeal and shine of automotive surfaces, making it a popular choice for achieving showroom-quality finishes. The unique feature of polishing lies in its capability to rejuvenate old and worn-out parts, providing a cost-effective solution for enhancing the appearance of vehicles while extending their lifespan.
Grinding Welds
Delving into the aspect of grinding welds sheds light on the essential process of smoothening and blending welded joints in automotive applications. Grinding welds involve the removal of excess material and weld spatter to create seamless transitions between joined metal pieces. Its key characteristic lies in its ability to improve the aesthetic quality and structural integrity of welded components, making it a preferred choice for achieving professional welding finishes. While grinding welds offer the advantage of producing clean and well-integrated welds, it may require precision and finesse to maintain the integrity of the welded joints and overall structural stability.
Choosing the Right Forney Grinding Wheel
In the realm of Forney grinding wheels, selecting the appropriate wheel is a critical decision that can significantly impact the outcome of various grinding tasks. The choice of the grinding wheel plays a pivotal role in ensuring efficiency, precision, and quality in the grinding process. Being cognizant of specific elements such as material compatibility, operational speed, and desired finishing results is imperative for achieving optimal results. In this segment, we will delve into the intricacies of selecting the right Forney grinding wheel to meet specific needs and optimize performance.
Factors to Consider
Material Being Ground
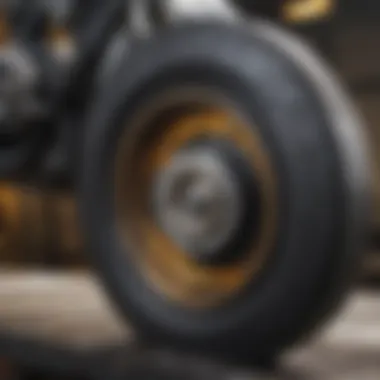
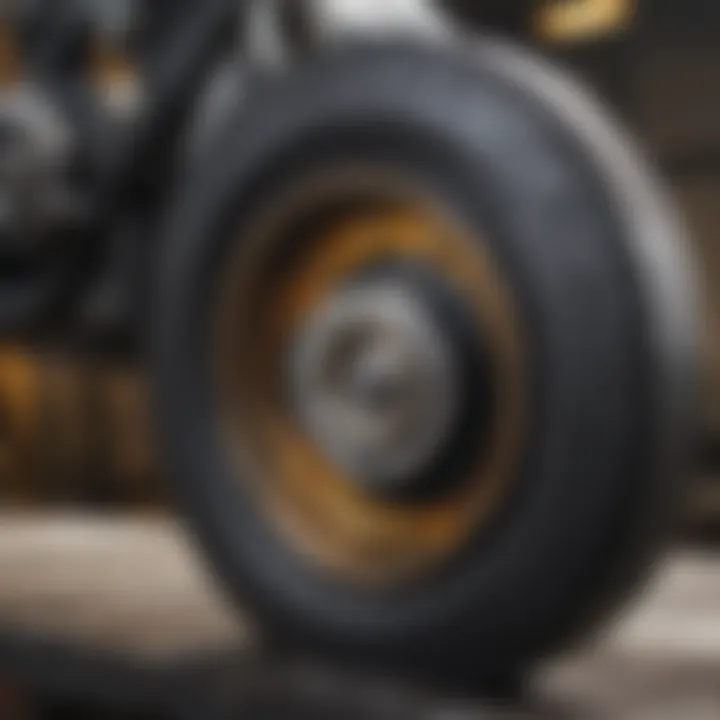
When it comes to the material being ground, understanding its composition and properties is fundamental in determining the suitable grinding wheel for the task at hand. Different materials exhibit varying hardness, abrasiveness, and thermal conductivity, influencing the choice of the grinding wheel. For instance, grinding softer materials like aluminum necessitates a different wheel composition compared to grinding hardened steel. The selection of the grinding wheel based on the material being ground ensures enhanced efficiency, minimal wear, and superior surface quality in grinding operations.
Speed of Operation
The speed of operation is another crucial factor that directly impacts the grinding process's efficiency and effectiveness. Matching the grinding wheel's rotational speed with the operational requirements is essential for achieving optimal performance. Operating at the correct speed minimizes heat generation, reduces wear on the wheel, and enhances material removal rates. Finding the right balance between speed and material compatibility is key to achieving precise and consistent grinding results.
Desired Finish
The desired finish plays a significant role in determining the appropriate grinding wheel characteristics. Whether aiming for a smooth surface finish or a specific surface roughness profile, selecting the right wheel composition and grit size is essential. Different wheel structures and abrasive materials cater to distinct finishing requirements, ensuring the desired surface texture and quality post-grinding. Understanding the nuances of desired finishes enables professionals to select the most suitable grinding wheel for achieving desired outcomes effectively.
Matching the Wheel to the Task
Grain and Bond Combination
The grain and bond combination of a grinding wheel directly influences its cutting efficiency, wear resistance, and material removal capabilities. The abrasive grains' shape, size, and distribution, coupled with the bonding agents' properties, determine the wheel's aggressiveness and performance. Optimal grain and bond combinations ensure effective chip clearance, minimal wheel loading, and prolonged wheel life during grinding operations. Selecting the right grain and bond combination aligns the wheel properties with the specific task requirements, enhancing productivity and quality in grinding processes.
Wheel Shape
The wheel shape is a critical consideration when choosing a grinding wheel tailored to a particular task. Different wheel shapes, such as flat, cylindrical, tapered, and saucer wheels, serve varying grinding applications and geometries. Each wheel shape offers distinct advantages in terms of access, precision, and surface coverage during grinding. Selecting the appropriate wheel shape based on the workpiece geometry and grinding requirements ensures optimal contact between the wheel and the material, facilitating efficient material removal and precise shaping. Matching the wheel shape to the task at hand optimizes grinding performance and enhances overall productivity.
Maintaining Forney Grinding Wheels
Maintaining Forney Grinding Wheels holds paramount importance within the realm of grinding tasks due to its profound impact on the longevity and efficiency of the equipment. Regular maintenance ensures optimal performance and longevity of the grinding wheels, thereby maximizing productivity and cost-effectiveness. This section will delve into the critical aspects of proper storage, inspection, and cleaning, elucidating the significance of each in ensuring the durability and effectiveness of Forney grinding wheels.
Proper Storage
Proper storage of Forney Grinding Wheels is crucial in preserving their integrity and performance. It involves safeguarding the wheels from detrimental factors such as moisture, which can lead to corrosion and degradation of abrasive materials. By storing the wheels in dry and well-ventilated areas, users can mitigate the risks of moisture-induced damage, thereby prolonging the lifespan and functionality of the wheels.
-#### Avoiding Moisture
Avoiding Moisture stands as a fundamental tenet in preserving Forney Grinding Wheels. Moisture can initiate chemical reactions that compromise the abrasive properties of the wheels, diminishing their grinding efficacy. By keeping the wheels in moisture-free environments and utilizing moisture-absorbing agents, users can shield the wheels from corrosive effects, ensuring consistent performance and durability in grinding tasks.
-#### Preventing Damage
Preventing Damage is pivotal in maintaining the structural integrity of Forney Grinding Wheels. Damage, whether from mishandling or environmental factors, can impair the balance and effectiveness of the wheels. Employing protective measures such as cushioned storage containers and careful handling practices minimizes the risk of damage, sustaining the sharpness and efficiency of the wheels for prolonged operational use.
Regular Inspection and Cleaning
Regular inspection and cleaning practices are essential for identifying potential issues and maintaining the performance of Forney Grinding Wheels. Through meticulous examination and consistent cleaning regimens, users can ensure that the wheels are free from damage and residue buildup, enabling smooth and precise grinding operations.
-#### Checking for Damage
The process of Checking for Damage involves thorough visual assessment and tactile inspection of the grinding wheels. By scrutinizing the surface for cracks, chips, or irregularities, users can pinpoint areas of concern and take corrective measures promptly. Early detection of damage prevents further deterioration, preserving the quality and functionality of the wheels for extended usage.
-#### Removing Residue
Removing Residue is a critical step in enhancing the longevity and performance of Forney Grinding Wheels. Residue accumulation, such as metal shavings or debris, can impede the grinding process and diminish the abrasive effectiveness of the wheels. By utilizing appropriate cleaning tools and methods, users can eliminate residue build-up, maintaining the sharpness and efficiency of the wheels for consistent and reliable grinding outcomes.
Conclusion
In the realm of Forney Grinding Wheels, the conclusion serves as the quintessential essence encapsulating the nuanced intricacies and pivotal applications of this tool. Understanding the critical significance of proper maintenance and diligent selection is paramount in leveraging the full potential of these grinding wheels. As professionals, hobbyists, or artisans engage in metal fabrication, woodworking, or automotive tasks, the conclusion acts as a guiding light towards ensuring efficiency, precision, and longevity. By emphasizing the decisive impact of factors such as material compatibility, operational speed, and desired finishes, the conclusion bridges theoretical knowledge with practical applicability. Furthermore, in a world inundated with a myriad of grinding wheel options, the conclusion synthesizes essential considerations and tips, enabling users to navigate this indispensable tool's landscape with informed acuity.
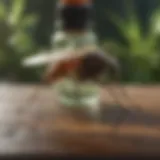
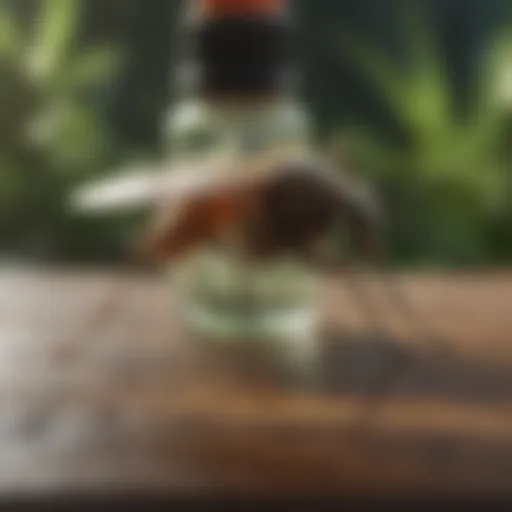